Multi-material additive manufacturing of metals: A review of structures and mechanical characteristics
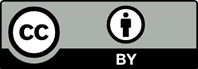
The ability to manufacture complex designs from multiple materials has long been a key objective for applications operating in extreme environments. Multi-material (MM) additive manufacturing (MMAM) has significantly enhanced the functionality of additive manufacturing (AM) by enabling the integration of dissimilar alloys while leveraging the inherent advantages of AM, including design flexibility, reduced material waste, and rapid production, with the ability to tailor mechanical properties through spatial material distribution and local processing conditions. This process unlocks unprecedented opportunities across industries such as aerospace, automotive, biomedical, energy, and nuclear sectors. This article provides a comprehensive review of the state-of-the-art in MMAM, focusing on the manufacturing processes, molten pool formation, alloy compatibility, and bimetallic interface characteristics—including microstructural and mechanical properties—as well as modeling and simulation approaches for performance prediction and optimization, with developments tracked from 2013 to 2024. This review article predominantly focuses on: (i) MM-laser powder bed fusion, (ii) MM-directed energy deposition, and (iii) MM-wire-arc AM by detailing the mechanisms of molten pool formation at the interface and dissimilar alloy material compatibilities. Subsequently, the article provides an in-depth analysis of the meso- and micro-structural characteristics at the interface in bimetallic structures across widely employed MMAM alloys. The mechanics of MMs under various mechanical properties are presented, including microhardness/micro-indentation, tensile, flexural, compression, and fatigue strength, which are critical for MMAM applications in extreme conditions. In addition, current modeling and simulation approaches for MMAM are discussed with respect to the challenges and opportunities to increase MMAM adoption. The article concludes with a future roadmap for advancing MMAM by overcoming feedstock and build material cross-contamination, monitoring the in situ process, standardizing MM testing, and further developing thermo-mechanical modeling, specifically, for MMAM.

- Bakewell J. Customising Production. Berlin: Springer; 2019.
- Csere C. How Automakers are 3D-Printing Parts for Production Cars (and Classics); 2018.
- Gandy D, Albert M. Small Modular Reactor Pressure Vessel Manufacturing & Fabrication Technology Development; 2020.
- Ellis JK. 3D-printed nuclear reactor promises faster, more economical path to nuclear energy; 2020.
- Zhong Y, Rännar LE, Liu L, et al. Additive manufacturing of 316L stainless steel by electron beam melting for nuclear fusion applications. J Nucl Mater. 2017;486:234-245.
- McMahon M. Metal AM in the aerospace sector: From early successes to the transformation of an industry, 2023.
- Russell R, Wells D, Waller J, et al. Qualification and certification of metal additive manufactured hardware for aerospace applications. In: Additive Manufacturing for the Aerospace Industry. Netherlands: Elsevier; 2019. p. 33-66.
- González-Barrio H, Calleja-Ochoa A, Lamikiz A, López De Lacalle LN. Manufacturing processes of integral blade rotors for turbomachinery, processes and new approaches. Appl Sci. 2020;10(9):3063.
- Radhika C, Shanmugam R, Ramoni M, Gnanavel BK. A review on additive manufacturing for aerospace application. Mater Res Exp. 2024;11(2):022001.
- Jalui S, Xuan Y, Manogharan G, O’Connor J. Development of a method for shape optimization for a gas turbine fuel injector design using metal-additive manufacturing. J Eng Gas Turb Power. 2025;147(1):011023.
- He P, Sun C, Wang Y. Material distortion in laser-based additive manufacturing of fuel cell component: Three-dimensional numerical analysis. Addit Manuf. 2021;46:102188.
- Hossain A, Pellicotte JT, Stewart M. A calibration approach for accelerated creep testing for electron beam melted (EBM) Ti-6Al-4V using the WCS model. In: Industrial and Cogeneration; Manufacturing Materials and Metallurgy. Vol. 8. Boston, Massachusetts, USA: American Society of Mechanical Engineers; 2023. p. V008T17A023.
- Metal AM. Nexxt Spine develops additively manufactured spinal implants using MTS test systems; 2019.
- Harrysson OLA, Marcellin-Little DJ, Horn TJ. Applications of metal additive manufacturing in veterinary orthopedic surgery. JOM. 2015;67(3):647-654.
- Vilardell AM, Takezawa A, Du Plessis A, et al. Topology optimization and characterization of Ti6Al4V ELI cellular lattice structures by laser powder bed fusion for biomedical applications. Mater Sci Eng A. 2019;766:138330.
- Tilton M, Lewis GS, Hast MW, Fox E, Manogharan G. Additively manufactured patient-specific prosthesis for tumor reconstruction: Design, process, and properties. PLoS One. 2021;16(7):e0253786.
- Tilton M, Borjali A, Griffis JC, Varadarajan KM, Manogharan GP. Fatigue properties of Ti-6Al-4V TPMS scaffolds fabricated via laser powder bed fusion. Manuf Lett. 2023;37:32-38.
- Shuai C, Li D, Yao X, Li X, Gao C. Additive manufacturing of promising heterostructure for biomedical applications. Int J Extreme Manuf. 2023;5(3):032012.
- F42 Committee. Terminology for Additive Manufacturing - General Principles - Terminology.
- Sun Z, Chueh YH, Li L. Multiphase mesoscopic simulation of multiple and functionally gradient materials laser powder bed fusion additive manufacturing processes. Addit Manuf. 2020;35:101448.
- He C, Ramani KS, Okwudire CE. An intelligent scanning strategy (SmartScan) for improved part quality in multi-laser PBF additive manufacturing. Addit Manuf. 2023;64:103427.
- Aerosint Company. Aerosint.
- Gu H, Wei C, Li L, et al. Multi-physics modelling of molten pool development and track formation in multi-track, multi-layer and multi-material selective laser melting. Int J Heat Mass Transfer. 2020;151:119458.
- Toursangsaraki M. A Review of Multi-material and Composite Parts Production by Modified Additive Manufacturing Methods. Version Number: 1. 2018.
- Li Y, Feng Z, Hao L, et al. A review on functionally graded materials and structures via additive manufacturing: From multi-scale design to versatile functional properties. Adv Mater Technol. 2020;5(6):1900981.
- Mirzaali MJ, Nava AH, Gunashekar D, Nouri-Goushki M, Doubrovski EL, Zadpoor AA. Fracture behavior of bio-inspired functionally graded soft-hard composites made by multi-material 3D printing: The case of colinear cracks. Materials (Basel). 2019;12(17):2735.
- Guessasma S, Nouri H, Roger F. Microstructural and mechanical implications of microscaled assembly in droplet-based multi-material additive manufacturing. Polymers (Basel). 2017;9(12):372. doi: 10.3390/polym9080372
- Vaezi M, Chianrabutra S, Mellor B, Yang S. Multiple material additive manufacturing Part 1: A review: This review paper covers a decade of research on multiple material additive manufacturing technologies which can produce complex geometry parts with different materials. Virt Phys Prototyp. 2013;8(1):19-50.
- Sheydaeian E. Systems, Materials, and Methodologies for Multi-material Hybrid Additive Manufacturing Functionally Graded Structures. PhD thesis, University of Waterloo, Ontario, Canada; 2017.
- Putra NE, Mirzaali MJ, Apachitei I, Zhou J, Zadpoor AA. Multi-material additive manufacturing tech- nologies for Ti-, Mg-, and Fe-based biomaterials for bone substitution. Acta Biomater. 2020;109:1-20. doi: 10.1016/j.actbio.2020.03.037
- Doubrovski EL, Tsai EY, Dikovsky D, Geraedts JMP, Herr H, Oxman N. Voxel-based fabrication through material property mapping: A design method for bitmap printing. Comput Aided Design. 2015;60:3-13.
- Skylar-Scott MA, Mueller J, Visser CW, Lewis JA. Voxelated soft matter via multima- terial multinozzle 3D printing. Nature. 2019;575(7782):330-335.
- Griffis JC, Shahed K, Meinert K, Yilmaz B, Lear M, Manogharan G. Multi-material laser powder bed fusion: Effects of build orientation on defects, material structure and mechanical properties. NPJ Adv Manuf. 2025;2(1):5.
- Nazir A, Gokcekaya O, Billah KM, et al. Multi-material additive manufacturing: A systematic review of design, properties, applications, challenges, and 3D printing of materials and cellular metamaterials. Mater Design. 2023;226:111661.
- Singh AW, Kapil S, Das M. A comprehensive review of the methods and mechanisms for powder feedstock handling in directed energy deposition. Addit Manuf. 2020;35:101388.
- Luo X, Chang W, Zhong W, Wardle F. Hybrid machine tool design. In: Hybrid Machining. Netherlands: Elsevier; 2018. p. 197-214.
- Gibson I, Rosen D, Stucker B. Directed energy deposition processes. In: Additive Manufacturing Technologies. New York: Springer New York; 2015. p. 245-268.
- Tanwar RS, Jhavar S. A review on additive manufacturing of SS-Ni multi-material fabrication. In: Materials Today: Proceedings; 2023. p. S2214785323010866.
- Wang D, Liu L, Deng G, et al. Recent progress on additive manufacturing of multi-material structures with laser powder bed fusion. Virt Phys Prototyp. 2022;17(2):329-365.
- Wei C, Li L. Recent progress and scientific challenges in multi-material additive manufacturing via laser- based powder bed fusion. Virt Phys Prototyp. 2021;16(3):347-371.
- Wu Z, Wilson-Heid AE, Joey Griffiths R, Elton ES. A review on experimentally observed mechanical and microstructural characteristics of interfaces in multi-material laser powder bed fusion. Front Mech Eng. 2023;9:1087021.
- Sun Z, Ion JC. Laser welding of dissimilar metal combinations. J Mater Sci. 1995;30(17):4205-4214.
- Mai TA, Spowage AC. Characterisation of dissimilar joints in laser welding of steel-kovar, copper-steel and copper-aluminium. Mater Sci Eng A. 2004;374(1-2):224-233.
- Estrin Y, Beygelzimer Y, Kulagin R, et al. Architecturing materials at mesoscale: Some current trends. Mater Res Lett. 2021;9(10):399-421.
- Gradl PR, Protz C, Fikes J, et al. Lightweight thrust chamber assemblies using multi-alloy additive manufacturing and composite overwrap. In: AIAA Propulsion and Energy 2020 Forum, VIRTUAL EVENT. USA: American Institute of Aeronautics and Astronautics; 2020.
- Gradl PR, Protz CS, Ellis DL, Greene SE. Progress in Additively Manufactured Copper-Alloy GRCop-84, GRCop-42, and bimetallic combustion chambers for liquid rocket engines. In: International Astronautical Congress.
- Marques A, Cunha A, Gasik M, Carvalho O, Silva FS, Bartolomeu F. Inconel 718–copper parts fabricated by 3D multi-material laser powder bed fusion: A novel technological and designing approach for rocket engine. Int J Adv Manuf Technol. 2022;122(3):2113-2123.
- Bhaduri D, Penchev P, Essa K, et al. Evaluation of surface/ interface quality, microstructure and mechanical properties of hybrid additive- subtractive aluminium parts. CIRP Ann. 2019;68(1):237-240.
- Wits WW, Amsterdam E. Graded structures by multi-material mixing in laser powder bed fusion. CIRP Ann. 2021;70(1):159-162.
- Nguyen DS, Park HS, Lee CM. Applying selective laser melting to join Al and Fe: An investigation of dissimilar materials. Appl Sci. 2019;9(15):3031.
- Andreiev A, Hoyer KP, Dula D, et al. Laser beam melting of functionally graded materials with application-adapted tailoring of magnetic and mechanical performance. Mater Sci Eng A. 2021;822:141662.
- Bartolomeu F, Costa MM, Alves N, Miranda G, Silva FS. Additive manufacturing of NiTi-Ti6Al4V multi- material cellular structures targeting orthopedic implants. Optics Lasers Eng. 2020;134:106208.
- Tan C, Zhou K, Kuang T. Selective laser melting of tungsten-copper functionally graded material. Mater Lett. 2019;237:328-331.
- Wei C, Liu L, Gu Y, et al. Multi-material additive- manufacturing of tungsten - copper alloy bimetallic structure with a stainless-steel interlayer and associated bonding mechanisms. Addit Manuf. 2022;50:102574.
- Wei C, Sun Z, Huang Y, Li L. Embedding anti-counterfeiting features in metallic components via multiple material additive manufacturing. Addit Manuf. 2018;24:1-12.
- Liu L, Wang D, Deng G, et al. Interfacial characteristics and formation mechanisms of copper-steel multimaterial structures fabricated via laser powder bed fusion using different building strategies. Chin J Mech Eng Addit Manuf Front. 2022;1(3):100045.
- Wei C, Liu L, Cao H, et al. Cu10Sn to Ti6Al4V bonding mechanisms in laser-based powder bed fusion multiple material additive manufacturing with different build strategies. Addit Manuf. 2022;51:102588.
- Chen J, Yang Y, Song C, Zhang M, Wu S, Wang D. Interfacial microstructure and mechanical properties of 316L/CuSn10 multi-material bimetallic structure fabricated by selective laser melting. Mater Sci Eng A. 2019;752:75-85.
- Schneck M, Horn M, Schmitt M, Seidel C, Schlick G, Reinhart G. Review on additive hybrid-and multi-material-manufacturing of metals by powder bed fusion: State of technology and development potential. Prog Addit Manuf. 2021;6(4):881-894.
- Ansari M, Jabari E, Toyserkani E. Opportunities and challenges in additive manufacturing of functionally graded metallic materials via powder-fed laser directed energy deposition: A review. J Mater Process Technol. 2021;294:117117.
- Bhavar V, Kattire P, Thakare S, Patil S, Singh R. A review on functionally gradient materials (FGMs) and their applications. IOP Conf Ser Mater Sci Eng. 2017;229:012021.
- Mahmoud D, Elbestawi M. Lattice structures and functionally graded materials applications in additive manufacturing of orthopedic implants: A review. J Manuf Mater Process. 2017;1(2):13.
- Ren L, Wang Z, Ren L, Han Z, Liu Q, Song Z. Graded biological materials and additive manufacturing technologies for producing bioinspired graded materials: An overview. Compos Part B Eng. 2022;242:110086.
- Saleh B, Jiang J, Fathi R, et al. 30 Years of functionally graded materials: An overview of manufacturing methods, Applications and Future Challenges. Compos Part B Eng. 2020;201:108376.
- Xu F, Zhang X, Zhang H. A review on functionally graded structures and materials for energy absorption. Eng Struct. 2018;171:309-325.
- Wei C, Zhang Z, Cheng D, Sun Z, Zhu M, Li L. An overview of laser-based multiple metallic material additive manufacturing: From macro- to micro-scales. Int J Extreme Manuf. 2021;3(1):012003.
- Ostolaza M, Arrizubieta JI, Lamikiz A, Plaza S, Ortega N. Latest developments to manufacture metal matrix composites and functionally graded materials through AM: A state-of-the-art review. Materials (Basel). 2023;16(4):1746. doi: 10.3390/ma16041746
- Ma Z, Liu W, Li W, et al. Additive manufacturing of functional gradient materials: A review of research progress and challenges. J Alloys Compd. 2024;971:172642.
- Ju Y, Li C, Yang X, Ba L, Wang Y, Di X. Recent progress on additive manufacturing of steel-based functionally graded materials. Mater Today Commun. 2024;40:109953.
- Sanjeeviprakash K, Rajesh Kannan A, Siva Shanmugam N. Additive manufacturing of metal-based functionally graded materials: Overview, recent advancements and challenges. J Braz Soc Mech Sci Eng. 2023;45(5):241.
- Srivastava M, Rathee S, Tiwari A, Dongre M. Wire arc additive manufacturing of metals: A review on processes, materials and their behaviour. Mater Chem Phys. 2023;294:126988.
- Yan L, Chen Y, Liou F. Additive manufacturing of functionally graded metallic materials using laser metal deposition. Addit Manuf. 2020;31:100901.
- Dev Singh D, Arjula S, Raji Reddy A. Functionally graded materials manufactured by direct energy deposition: A review. Mater Today Proc. 2021;47:2450-2456.
- Tyagi SA, Manjaiah M. Laser additive manufacturing of titanium-based functionally graded materials: A review. J Mater Eng Perform. 2022;31(8):6131-6148.
- Zhang R, Jiang F, Xue L, Yu J. Review of additive manufacturing techniques for large-scale metal functionally graded materials. Crystals. 2022;12(6):858.
- Ghanavati R, Naffakh-Moosavy H. Additive manufacturing of functionally graded metallic materials: A review of experimental and numerical studies. J Mater Res Technol. 2021;13:1628-1664.
- Karimzadeh M, Basvoju D, Vakanski A, Charit I, Xu F, Zhang X. Machine learning for additive manufacturing of functionally graded materials. Materials. 2024;17(15):3673.
- Yang L, Miyanaji H, Ram DJ, Zandinejad A, Zhang S. Functionally graded ceramic based materials using additive manufacturing: Review and progress. In: Shimamura K, Kirihara S, Akedo J, Ohji T, Naito M, editors. Ceramic Transactions Series. 1st ed., Vol. CCLVIII. United States: Wiley; 2016. p. 43-55.
- Delacroix T, Lomello F, Schuster F, et al. Influence of build characteristics and chamber oxygen concentration on powder degradation in laser powder bed fusion. Powder Technol. 2023;416:11823.
- Lu SP, Fujii H, Nogi K, Sato T. Effect of oxygen content in He–O2 shielding gas on weld shape in ultra-deep penetration TIG. Sci Technol Weld Join. 2007;12(8):689-695.
- Li R, Liu J, Shi Y, Wang L, Jiang W. Balling behavior of stainless steel and nickel powder during selective laser melting process. Int J Adv Manuf Technol. 2012;59(9- 12):1025-1035.
- Wang D, Wu S, Fu F, et al. Mechanisms and characteristics of spatter generation in SLM processing and its effect on the properties. Mater Design. 2017;117:121-130.
- Leung CLA, Marussi S, Towrie M, Atwood RC, Withers PJ, Lee PD. The effect of powder oxidation on defect formation in laser additive manufacturing. Acta Mater. 2019;166:294-305.
- Mertens R, Dadbakhsh S, Van Humbeeck J, Kruth JP. Application of base plate preheating during selective laser melting. Proc CIRP. 2018;74:5-11.
- Guan J, Wang Q. Laser powder bed fusion of dissimilar metal materials: A review. Materials. 2023;16(7):2757.
- Dzogbewu TC, Du Preez WB. Additive manufacturing of Ti-based intermetallic alloys: A review and conceptualization of a next-generation machine. Materials. 2021;14(15):4317.
- International Organization for Standardization. Additive Manufacturing-General Principles-Terminology. United Kingdom: ISO/ASTM 52900; 2018.
- Hasanov S, Alkunte S, Rajeshirke M, et al. Review on additive manufacturing of multi-material parts: Progress and challenges. J Manuf Mater Process. 2021;6(1):4.
- Verma A, Kapil A, Klobčar D, Sharma A. A review on multiplicity in multi-material additive manufacturing: Process, capability, scale, and structure. Materials. 2023;16(15):5246.
- Thompson SM, Bian L, Shamsaei N, Yadollahi A. An overview of Direct Laser Deposition for additive manufacturing; Part I: Transport phenomena, modeling and diagnostics. Addit Manuf. 2015;8:36-62.
- Ning J, Zhu L, Wang S, et al. Printability disparities in heterogeneous material combinations via laser directed energy deposition: A comparative study. Int J Extreme Manuf. 2024;6(2):025001.
- Feenstra DR, Banerjee R, Fraser HL, Huang A, Molotnikov A, Birbilis N. Critical review of the state of the art in multi-material fabrication via directed energy deposition. Curr Opin Solid State Mater Sci. 2021;25(4):100924.
- Svetlizky D, Zheng B, Vyatskikh A, et al. Laser-based directed energy deposition (DED-LB) of advanced materials. Mater Sci Eng A. 2022;840:142967.
- Frank Medina. Fundamental of additive manufacturing for prodction.
- Svetlizky D, Das M, Zheng B, et al. Directed energy deposition (DED) additive manufacturing: Physical characteristics, defects, challenges and applications. Mater Today. 2021;49:271-295.
- Xie J, Huang Z, Lu H, Zheng B, Xu X, Lei J. Additive manufacturing of tantalum-zirconium alloy coating for corrosion and wear application by laser directed energy deposition on Ti6Al4V. Surf Coat Technol. 2021;411:127006.
- Rai AK, Srinivasulu B, Paul CB, et al. Development of thick SiC coating on thin wall tube of zircaloy-4 using laser based directed energy deposition technique. Surf Coat Technol. 2020;398:126088.
- Michael Wilson J, Piya C, Shin YC, Zhao F, Ramani K. Remanufacturing of turbine blades by laser direct deposition with its energy and environmental impact analysis. J Clean Prod. 2014;80:170-178.
- Saboori A, Aversa A, Marchese G, Biamino S, Lombardi M, Fino P. Application of directed energy deposition-based additive manufacturing in repair. Appl Sci. 2019;9(16):3316.
- DebRoy HL, Wei JS, Zuback T, et al. Additive manufacturing of metallic components-Process, structure and properties. Prog Mater Sci. 2018;92:112-224.
- Dhanola A, Prasad DS. A comprehensive review of wire arc additive manufacturing for metallic functionally graded materials. Eng Res Express. 2024;6(4):042501.
- Bandyopadhyay A, Heer B. Additive manufacturing of multi-material structures. Mater Sci Eng R Rep. 2018;129:1-16.
- Vimal KEK, Naveen Srinivas M, Rajak S. Wire arc additive manufacturing of aluminium alloys: A review. Mater Today Proc. 2021;41:1139-1145.
- Ding D, Pan Z, Cuiuri D, Li H. Wire-feed additive manufacturing of metal components: Technologies, developments and future interests. Int J Adv Manuf Technol. 2015;81(1-4):465-481.
- Chen Z, Yuan L, Pan Z, et al. A comprehensive review and future perspectives of simulation approaches in wire arc additive manufacturing (WAAM). Int J Extreme Manuf. 2025;7(2):022016.
- Reichardt A, Shapiro AA, Otis R, et al. Advances in additive manufacturing of metal-based functionally graded materials. Int Mater Rev. 2021;66(1):1-29.
- Akinlabi ET, Akinlabi SA. Friction stir welding of dissimilar metals. In: Advances in Friction-Stir Welding and Processing. Netherlands: Elsevier; 2014. p. 241-293.
- Sun Z, Karppi R. The application of electron beam welding for the joining of dissimilar metals: An overview. J Mater Process Technol. 1996;59(3):257-267.
- Kah P, Shrestha M, Martikainen J. Trends in joining dissimilar metals by welding. Appl Mechan Mater. 2013;440:269-276.
- Powell D, Rennie AEW, Geekie L, Burns N. Understanding powder degradation in metal additive manufacturing to allow the upcycling of recycled powders. J Clean Prod. 2020;268:122077.
- Renderos M, Girot F, Lamikiz A, Torregaray A, Saintier N. Ni based powder reconditioning and reuse for LMD process. Phys Proc. 2016;83:769-777.
- Wang P, Nai MLS, Ng FL, et al. Revealing mechanisms underlying powder reusability of Ti-48Al-2Cr-2Nb intermetallic in electron beam powder bed fusion process. Addit Manuf. 2022;59:103155.
- Tang Y, Zhou Y, Hoff T, Garon M, Zhao YF. Elastic modulus of 316 stainless steel lattice structure fabricated via binder jetting process. Mater Sci Technol. 2016;32(7):648-656.
- McGeehan O, Oldfield S, Wilks J, Mawby J, Linaker L. Testing and Analysis of Additive Manufactured Parts from Partially Recycled Powder. MEng Thesi, Liverpool John Moores University, Liverpool; 2018.
- Del Re F, Contaldi V, Astarita A, et al. Statistical approach for assessing the effect of powder reuse on the final quality of AlSi10Mg parts produced by laser powder bed fusion additive manufacturing. Int J Adv Manuf Technol. 2018;97(5-8):2231-2240.
- Seyda V, Kaufmann N, Emmelmann C. Investigation of aging processes of Ti-6Al-4 V powder material in laser melting. Phys Proc. 2012;39:425-431.
- Carroll PA, Pinkerton A, Allen J, et al. The effect of powder recycling in direct metal laser deposition on powder and manufactured part characteristics. In: Proceedings of the AVT-139 Specialists Meeting on Cost Effective Manufacture via Net Shape Processing; 2006. p. 1-8.
- Lanzutti A, Marin E. The challenges and advances in recycling/re-using powder for metal 3D printing: A comprehensive review. Metals. 2024;14(8):886.
- Mostafaei A, Zhao C, He Y, et al. Defects and anomalies in powder bed fusion metal additive manufacturing. Curr Opin Solid State Mater Sci. 2022;26(2):100974.
- Everton SK, Hirsch M, Stravroulakis P, Leach RK, Clare AT. Review of in-situ process monitoring and in-situ metrology for metal additive manufacturing. Mater Design. 2016;95:431-445.
- Grasso M, Colosimo BM. Process defects and in situ monitoring methods in metal powder bed fusion: A review. Meas Sci Technol. 2017;28(4):044005. doi: 10.1088/1361-6501/aa5c4f
- Sahasrabudhe H, Harrison R, Carpenter C, Bandyopadhyay A. Stainless steel to titanium bimetallic structure using LENS™. Addit Manuf. 2015;5:1-8. doi: 10.1016/j.addma.2014.10.002
- Tey CF, Tan X, Sing SL, Yeong WY. Additive manufacturing of multiple materials by selective laser melting: Ti-alloy to stainless steel via a Cu-alloy interlayer. Addit Manufact. 2020;31:100970. doi: 10.1016/j.addma.2019.100970
- Watanabe I, Sun Z, Kitano H, Goto K. Multiscale analysis of mechanical behavior of multilayer steel structures fabricated by wire and arc additive manufacturing. Sci Technol Adv Mater. 2020;21(1):461-470. doi: 10.1080/14686996.2020.1788908
- McDonnell B, Errico V, Posa P, et al. Bi-metallic lattice structures manufactured via an intralayer multi-material powder bed fusion method. Addit Manufact. 2024;89:104301. doi: 10.1016/j.addma.2024.104301
- Bettencourt CJ, Kouraytem N. Microstructural characterization of the transition in SS316L and IN625 bimetallic fabricated using hybrid additive manufacturing. JOM. 2023;75(12):5079-5087. doi: 10.1007/s11837-023-06119-4
- Ghanavati R, Naffakh-Moosavy H, Moradi M, Eshraghi M. Printability and microstructure of directed energy deposited SS316l-IN718 multi-material: Numerical modeling and experimental analysis. Sci Rep. 2022;12(1):16600. doi: 10.1038/s41598-022-21077-8
- Wei C, Li L, Zhang X, Chueh YH. 3D printing of multiple metallic materials via modified selective laser melting. CIRP Ann. 2018;67(1):245-248. doi: 10.1016/j.cirp.2018.04.096
- Bodner SC, Van De Vorst LT, Zalesak J, et al. Inconel-steel multilayers by liquid dispersed metal powder bed fusion: Microstructure, residual stress and property gradients. Addit Manufact. 2020;32:101027. doi: 10.1016/j.addma.2019.101027
- Yusuf SM, Zhao X, Yang S, Gao N. Interfacial characterisation of multi-material 316L stainless steel/Inconel 718 fabricated by laser powder bed fusion. Mater Lett. 2021;284:128928. doi: 10.1016/j.matlet.2020.128928
- Mei X, Wang X, Peng Y, et al. Interfacial characterization and mechanical properties of 316L stainless steel/inconel 718 manufactured by selective laser melting. Mater Sci Eng A. 2019;758:185-191. doi: 10.1016/j.msea.2019.05.011
- Chen N, Khan HA, Wan Z, et al. Microstructural characteristics and crack formation in additively manufactured bimetal material of 316L stainless steel and Inconel 625. Addit Manufact. 2020;32:101037. doi: 10.1016/j.addma.2020.101037
- Ahsan MRU, Fan X, Seo GJ, et al. Microstructures and mechanical behavior of the bimetallic additively-manufactured structure (BAMS) of austenitic stainless steel and Inconel 625. J Mater Sci Technol. 2021;74:176-188. doi: 10.1016/j.jmst.2020.10.001
- Dharmendra C, Shakerin S, Janaki Ram GD, Mohammadi M. Wire-arc additive manufacturing of nickel aluminum bronze/stainless steel hybrid parts - interfacial characterization, prospects, and problems. Materialia. 2020;13:100834. doi: 10.1016/j.mtla.2020.100834
- Ghanavati R, Naffakh-Moosavy H, Moradi M, et al. Design optimization for defect-free AISI 316 L/IN718 functionally graded materials produced by laser additive manufacturing. Mater Characterization. 2025;220:114697. doi: 10.1016/j.matchar.2024.114697
- Stair J, Webler BA, Beuth JL, De Boer MP. Demonstration and analysis of conditions to obtain a high strength inconel 625 to stainless steel 304l interface by directed energy deposition. Metall Mater Trans A. 2024;55(7):2186-2199. doi: 10.1007/s11661-024-07413-9
- Li L, Shi Q, Yang S. In-situ bonding of horizontal bimetallic interface by laser offset during laser powder bed fusion of copper/nickel multi-material structures and underlying thermodynamic mechanisms. J Mater Process Technol. 2025;339:118831. doi: 10.1016/j.jmatprotec.2025.118831
- Chen WY, Zhang X, Li M, Xu R, Zhao C, Sun T. Laser powder bed fusion of inconel 718 on 316 stainless steel. Addit Manuf. 2020;36:101500. doi: 10.1016/j.addma.2020.101500
- Meyer I, Oel M, Ehlers T, Lachmayer R. Additive manufacturing of multi-material parts - design guidelines for manufacturing of 316L/CuCrZr in laser powder bed fusion. Heliyon. 2023;9(8):e18301. doi: 10.1016/j.heliyon.2023.e18301
- Bai Y, Zhang J, Zhao C, Li C, Wang H. Dual interfacial characterization and property in multi-material selective laser melting of 316L stainless steel and C52400 copper alloy. Mater Characterization. 2020;167:110489. doi: 10.1016/j.matchar.2020.110489
- Liu ZH, Zhang DQ, Sing SL, Chua CK, Loh LE. Interfacial characterization of SLM parts in multi-material processing: Metallurgical diffusion between 316L stainless steel and C18400 copper alloy. Mater Characterization. 2014;94:116-125.
- Chen K, Wang C, Hong Q, Wen S, Zhou Y, Yan C, Shi Y. Selective laser melting 316L/CuSn10 multi-materials: Processing optimization, interfacial characterization and mechanical property. J Mater Process Technol. 2020;283:116701.
- Meyer I, Messmann CO, Ehlers T, Lachmayer R. Additive manufacturing of multi- material parts - effect of heat treatment on thermal, electrical, and mechanical part properties of 316L/CuCrZr. Mater Design. 2025;252:113783. doi: 10.1016/j.matdes.2025.113783
- Bulloch A, Harris A, Groom A, Cruchley A, Tuck CJ, Simonelli M. Funda- mental investigation of the interface formation of multi-material additive manufactured 316L-CuSn10 structures. Metallurgical Mater Trans A. 2025.
- Chen J, Zhang M, Zhao D, Bi G, Bai Y, Xiao Y, Wang D. The impact of interfacial characteristics on the interfacial properties of 316 L/CuSn10 multi-material manufactured by laser powder bed fusion. Mater Characterization. 2024;211:113862. doi: 10.1016/j.matchar.2024.113862
- Sun Z, Tang C, Soh V, et al. Laser powder bed fusion of 316L stainless steel and K220 copper multi-material. Virtual Phys Prototyp. 2024;19(1):e2356078. doi: 10.1080/17452759.2024.2356078
- Dash A, Bandyopadhyay A. 17-4 PH and SS316L bimetallic structures via additive manufacturing. Virtual Phys Prototyp. 2024;19(1):e2292695. doi: 10.1080/17452759.2023.2292695
- Zhou Y, Duan L, Li F, Chen K, Wen S. Effect of heat treatment on the microstructure and mechanical property of W/316L multi-material fabricated by selective laser melting. J Alloys Compd. 2022;890:161841. doi: 10.1016/j.jallcom.2021.161841
- Wei C, Gu H, Gu Y, et al. Abnormal interfacial bonding mechanisms of multi-material additive-manufactured tungsten-stainless steel sandwich structure. Int J Extrem Manuf. 2022;4(2):025002.
- Obielodan J, Stucker B. Characterization of LENS-fabricated Ti6Al4V and Ti6Al4V/TiC dual-material transition joints. Int J Adv Manuf Technol. 2013;66(9-12):2053-2061. doi: 10.1007/s00170-012-4481-9
- Wei K, Zeng X, Li F, Liu M, Deng J. Microstructure and mechanical property of Ti-5Al-2.5Sn/Ti-6Al-4V dissimilar titanium alloys integrally fabricated by selective laser melting. JOM. 2020;72(3):1031-1038. doi: 10.1007/s11837-019-03988-6
- Zhai W, Wang P, Ng FL, et al. Hybrid manufacturing of γ-TiAl and Ti-6Al-4V bimetal component with enhanced strength using electron beam melting. Compos Part B Eng. 2021;207:108587. doi: 10.1016/j.compositesb.2020.108587
- Wang P, Nai MLS, Lu S, Bai J, Zhang B, Wei J. Study of direct fabrication of a Ti-6Al-4V impeller on a wrought Ti-6Al-4V plate by electron beam melting. JOM. 2017;69(12):2738-2744. doi: 10.1007/s11837-017-2610-5
- Onuike B, Bandyopadhyay A. Functional bimetallic joints of Ti6Al4V to SS410. Addit Manuf. 2020;31:100931. doi: 10.1016/j.addma.2019.100931
- Scaramuccia MG, Demir AG, Caprio L, Tassa O, Previtali B. Development of processing strategies for multigraded selective laser melting of Ti6Al4V and IN718. Powder Technol. 2020;367:376-389. doi: 10.1016/j.powtec.2020.04.010
- Onuike B, Bandyopadhyay A. Additive manufacturing of Inconel 718 - Ti6Al4V bimetallic structures. Addit Manuf. 2018;22:844-851.
- Feenstra DR, Molotnikov A, Birbilis N. Effect of energy density on the interface evolution of stainless steel 316L deposited upon INC 625 via directed energy deposition. J Mater Sci. 2020;55(27):13314-13328. doi: 10.1007/s10853-020-04913-y
- Gorunov AI. Investigation microstructure of carbon fibers reinforced composite on Fe and Ni-based obtained by laser metal deposition. Surf Coat Technol. 2019;364:279-288. doi: 10.1016/j.surfcoat.2019.03.006
- Duval-Chaneac MS, Gao N, Khan RHU, et al. Fatigue crack growth in IN718/316L multi-materials layered structures fabricated by laser powder bed fusion. Int J Fatigue. 2021;152:106454. doi: 10.1016/j.ijfatigue.2021.106454
- Hinojos A, Mireles J, Reichardt A, et al. Joining of inconel 718 and 316 stainless steel using electron beam melting additive manufacturing technology. Mater Design. 2016;94:17-27. doi: 10.1016/j.matdes.2016.01.041
- Li Y, Liu Z, Wei Z, et al. Inhibition of interfacial cracks in 304L-Inconel718 bimetal fabricated via laser powder bed fusion. Addit Manuf. 2024;94:104463. doi: 10.1016/j.addma.2024.104463
- Chang T, Fang X, Zhou Y, et al. Heterogeneous interfaces of aluminum bronze/Inconel 718 dissimilar alloys under different wire arc directed energy deposition sequences. Int J Extrem Manuf. 2025;7(1):015003. doi: 10.1088/2631-7990/ad870f
- Zhang L, Dong P, Zeng Y, Yao H, Chen J. Additive manufacturing of inconel 718/CuCrZr multi-metallic materials fabricated by laser powder bed fusion. Addit Manuf. 2024;92:104377. doi: 10.1016/j.addma.2024.104377
- Prestes IB, Jägle EA. Influence of the laser strategy on bi-metallic interfaces printed via multi-material laser-based powder bed fusion. Addit Manuf Lett. 2025;13:100274. doi: 10.1016/j.addlet.2025.100274
- Wei C, Zhao Z, Wang C, et al. Integrated laser additive manufacturing of high-strength steel and Ti6Al4V: Experimental investigations and thermodynamic calculations. J Alloys Compd. 2024;983:173902. doi: 10.1016/j.jallcom.2024.173902
- Kim DK, Woo W, Kim EY, Choi SH. Microstructure and mechanical characteristics of multi-layered materials composed of 316L stainless steel and ferritic steel produced by direct energy deposition. J Alloys Compd. 2019;774:896-907. doi: 10.1016/j.jallcom.2018.09.390
- Zhang X, Sun C, Pan T, et al. Additive manufacturing of copper - H13 tool steel bi-metallic structures via Ni-based multi-interlayer. Addit Manuf. 2020;36:101474. doi: 10.1016/j.addma.2020.101474
- Shi Q, Hu Y, Fan H, Yang S. Fundamental role of vertical building sequence and its thermodynamic mechanisms during multi-material additive manufacturing of 18Ni300- CuSn10 structures with IN718 interlayer. J Manuf Processes. 2025;144:243-260. doi: 10.1016/j.jmapro.2025.04.048
- Bai Y, Zhao C, Zhang Y, Wang H. Microstructure and mechanical properties of additively manufactured multi-material component with maraging steel on CrMn steel. Mater Sci Eng A. 2021;802:140630. doi: 10.1016/j.msea.2020.140630
- Tan C, Wang D, Ma W, Zhou K. Ultra-strong bond interface in additively manufactured iron-based multi-materials. Mater Sci Eng A. 2021;802:140642. doi: 10.1016/j.msea.2020.140642
- Khodabakhshi F, Farshidianfar MH, Bakhshivash S, Gerlich AP, Khajepour A. Dissimilar metals deposition by directed energy based on powder-fed laser additive manufacturing. J Manuf Processes. 2019;43:83-97. doi: 10.1016/j.jmapro.2019.05.018
- Wang P, Lao CS, Chen ZW, et al. Microstructure and mechanical properties of Al-12Si and Al-3.5Cu-1.5Mg-1Si bimetal fabricated by selective laser melting. J Mater Sci Technol. 2020;36:18-26. doi: 10.1016/j.jmst.2019.03.047
- Hauser T, Reisch RT, Seebauer S, et al. Multi-material wire arc additive manufacturing of low and high alloyed aluminium alloys with in-situ material analysis. J Manuf Processes. 2021;69:378-390. doi: 10.1016/j.jmapro.2021.08.005
- Ismail L, Mohamed OF, Farrah T, George P, Schiffer A. Influence of process parameters on microstructure and interfacial mechanical properties of Al6061/AlSi10Mg multi-material components fabricated via laser powder bed fusion. Mater Sci Eng A. 2025;928:148061. doi: 10.1016/j.msea.2025.148061
- Sing SL, Lam LP, Zhang DQ, Liu ZH, Chua CK. Interfacial characterization of SLM parts in multi-material processing: Intermetallic phase formation between AlSi10Mg and C18400 copper alloy. Mater Characterization. 2015;107:220-227. doi: 10.1016/j.matchar.2015.07.007
- Zhang M, Yang Y, Wang D, Song C, Chen J. Microstructure and mechanical properties of CuSn/18Ni300 bimetallic porous structures manufactured by selective laser melting. Mater Design. 2019;165:107583. doi: 10.1016/j.matdes.2019.107583
- Ramakrishnan A, Dinda GP. Microstructural control of an Al-W aluminum matrix composite during direct laser metal deposition. J Alloys Compod. 2020;813:152208.
- Zhang W, Liao H, Hu Z, et al. Interfacial characteristics and mechanical properties of additive manufacturing martensite stainless steel on the Cu-Cr alloy substrate by directed energy deposition. J Mater Sci Technol. 2021;90:121-132. doi: 10.1016/j.jmst.2021.03.008
- Tan C, Zhou K, Ma W, Min L. Interfacial characteristic and mechanical performance of maraging steel-copper functional bimetal produced by selective laser melting based hybrid manufacture. Mater Design. 2018;155:77-85. doi: 10.1016/j.matdes.2018.05.064
- Shah K, Haq IU, Khan A, Shah SA, Khan M, Pinkerton AJ. Parametric study of development of Inconel-steel functionally graded materials by laser direct metal deposition. Mater Design (1980-2015). 2014;54:531-538. doi: 10.1016/j.matdes.2013.08.079
- Qingpeng C, Jiachen Y, Xiangyu L, et al. Effect of laser powder bed fusion gas flow rate on microstructure and mechanical properties of 316 L stainless steel. J Manuf Processes. 2024;132:850-862. doi: 10.1016/j.jmapro.2024.11.024
- Jakumeit J, Huang C, Laqua R, Zielinski J, Schleifenbaum JH. Effect of evaporated gas flow on porosity and microstructure of IN718 parts produced by LPBF-processes. IOP Conf Ser Mater Sci Eng. 2020;861(1):012011. doi: 10.1088/1757-899X/861/1/012011
- Liu L, Wang D, Deng G, et al. Laser additive manufacturing of a 316L/CuSn10 multimaterial coaxial nozzle to alleviate spattering adhesion and burning effect in directed energy deposition. J Manuf Processes. 2022;82:51-63. doi: 10.1016/j.jmapro.2022.07.038
- Onuike B, Heer B, Bandyopadhyay A. Additive manufacturing of Inconel 718-copper alloy bimetal- lic structure using laser engineered net shaping (LENS™). Addit Manuf. 2018;21:133-140.
- Liu W, Dupont JN. In-situ reactive processing of nickel aluminides by laser-engineered net shaping. Metallurgical Mater Trans A. 2003;34(11):2633-2641.
- Bergmann JP, Petzoldt F, Schürer R, Schneider S. Solid-state welding of aluminum to copper-case studies. Welding World. 2013;57(4):541-550.
- Chen J, Yang Y, Song C, Wang D, Wu S, Zhang M. Influence mechanism of process parameters on the interfacial characterization of selective laser melting 316L/CuSn10. Mater Sci Eng A. 2020;792:139316. doi: 10.1016/j.msea.2020.139316
- Zhang J, Song B, Yang L, Liu R, Zhang L, Shi Y. Microstructure evolution and mechanical properties of TiB/Ti6Al4V gradient-material lattice structure fabricated by laser powder bed fusion. Composit Part B Eng. 2020;202:108417. doi: 10.1016/j.compositesb.2020.108417
- Borisov E, Polozov I, Starikov K, Popovich A, Sufiiarov V. Structure and properties of Ti/Ti64 graded material manufactured by laser powder bed fusion. Materials (Basel). 2021;14(20):6140. doi: 10.3390/ma14206140
- Demir AG, Previtali B. Multi-material selective laser melting of Fe/Al-12Si components. Manuf Lett. 2017;11:8-11. doi: 10.1016/j.mfglet.2017.01.002
- E04 Committee. Test Method for Microindentation Hardness of Materials.
- Tan JL, Wong CH, Sorkin A. Multi-material modelling for selective laser melting. Proced Eng. 2017;216:51-57.
- Zhang W, Zhang B, Xiao H, Yang H, Wang Y, Zhu H. A layer-dependent analytical model for printability assessment of additive manufacturing copper/steel multi-material components by directed energy deposition. Micromachines (Basel). 2021;12(11):1394. doi: 10.3390/mi12111394
- Li W, Kishore MN, Zhang R, et al. Comprehensive studies of SS316L/IN718 functionally gradient material fabricated with directed energy deposition: Multi- physics and multi-materials modelling and experimental validation. Addit Manuf. 2023;61:103358.
- Chen C, Gu D, Dai D, et al. Laser additive manufacturing of layered TiB2/Ti6Al4V multi-material parts: Understanding thermal behavior evolution. Optics Laser Technol. 2019;119:105666. doi: 10.1016/j.optlastec.2019.105666
- Kannan R, Lee Y, Pierce D, et al. Additive manufacturing as a processing route for steel-aluminum bimetallic structures. Mater Design. 2023;231:112003. doi: 10.1016/j.matdes.2023.112003
- Sridar S, Klecka MA, Xiong W. Interfacial characteristics of P91 steel - inconel 740H bimetallic structure fabricated using wire-arc additive manufacturing. J Mater Processing Technol. 2022;300:117396. doi: 10.1016/j.jmatprotec.2021.117396
- Iams AD, Lienert AJ, Otazu DA, Ramoni M. Effects of deposition sequence on microstructural evolution in additively manufactured Cu-Cr-Nb alloy/superalloy bimetallic structures. Addit Manuf Lett. 2023;6:100151. doi: 10.1016/j.addlet.2023.100151
- Zhang J, Wang X, Gao J, et al. Additive manufacturing of Ti-6Al-4V/Al-Cu-Mg multi-material structures with a Cu interlayer. Int J Mech Sci. 2023;256:108477. doi: 10.1016/j.ijmecsci.2023.108477
- Wimmer A, Yalvac B, Zoeller C, et al. Experimental and numerical investigations of in situ alloying during powder bed fusion of metals using a laser beam. Metals. 2021;11(11):1842. doi: 10.3390/met11111842
- Patel KS, Solanki SD, Shah DB, Joshi SJ, Patel KM. Finite element simulation of additive manufacturing process of carbon allotropes. Int J Interact Design Manuf. 2023;18:6889-6896. doi: 10.1007/s12008-023-01221-y
- Ali MH, Yerbolat G, Kurokawa S. Modeling and simulation of multi-materials for additive manufacturing. Int J Interact Design Manuf. 2020;14(3):1057-1069. doi: 10.1007/s12008-020-00678-5
- Griffis J, Masker A, Schreiber J, Manogharan G. Site-specific property informed interface design of multi-material laser powder bed fusion. In: Additive Manufacturing; Advanced Materials Manufacturing; Biomanufacturing; Life Cycle Engineering. Vol. 1. Knoxville, Tennessee, USA: American Society of Mechanical Engineers; 2024. p. V001T01A034.
- Giraldo-Londoño O, Mirabella L, Dalloro L, Paulino GH. Multi-material thermomechanical topology optimization with applications to additive manufacturing: Design of main composite part and its support structure. Computer Methods Appl Mech Eng. 2020;363:112812.
- Zhang XS, Paulino GH, Ramos AS. Multi-material topology optimization with multiple volume constraints: A general approach applied to ground structures with material nonlinearity. Struct Multidiscip Optim. 2018;57(1):161-182. doi: 10.1007/s00158-017-1768-3
- Sanders ED, Aguiló MA, Paulino GH. Multi-material continuum topology optimization with arbitrary volume and mass constraints. Comput Methods Appl Mech Eng. 2018;340:798-823.
- Horn M, Prestel L, Schmitt M, et al. Multi-material additive manufacturing - recycling of binary metal powder mixtures by screening. Procedia CIRP. 2020;93:50-55. doi: 10.1016/j.procir.2020.04.098
- Chivel Y. New approach to multi-material processing in selective laser melting. Phys Proced. 2016;83:891-898. doi: 10.1016/j.phpro.2016.08.093
- Jacob G, Brown CU, Donmez MA, Watson SS, Slotwinski J. Effects of Powder Recycling on Stainless steel Powder and Built Material Properties in Metal Powder Bed Fusion Processes. Technical Report NIST AMS 100-6. Gaithersburg, MD: National Institute of Standards and Technology; 2017.
- Weiss C, Haefner CL, Munk J. On the influence of AlSi10Mg powder recycling behavior in the LPBF process and consequences for mechanical properties. JOM. 2022;74(3):1188-1199. doi: 10.1007/s11837-021-05080-4
- Koushik T, Shen H, Kan WH, et al. Effective Ti-6Al-4V powder recycling in LPBF additive manufacturing considering powder history. Sustainability. 2023;15(21):15582. doi: 10.3390/su152115582
- Sendino S, Martinez S, Lamikiz A. Characterization of IN718 recycling powder and its effect on LPBF manufactured parts. Procedia CIRP. 2020;94:227-232. doi: 10.1016/j.procir.2020.09.043
- Ahmed F, Ali U, Sarker D, et al. Study of powder recycling and its effect on printed parts during laser powder-bed fusion of 17-4 PH stainless steel. J Mater Process Technol. 2020;278:116522. doi: 10.1016/j.jmatprotec.2019.116522
- He X, Kong D, Zhou Y, et al. Powder recycling effects on porosity development and mechanical properties of Hastelloy X alloy during laser powder bed fusion process. Addit Manuf. 2022;55:102840. doi: 10.1016/j.addma.2022.102840
- Zhang H, Li J, Li Y. Effect of powder recycling on the organization and mechanical properties of GH4169 alloy by laser metal deposition. Coatings. 2023;13(3):659. doi: 10.3390/coatings13030659
- Popov VV, Katz-Demyanetz A, Garkun A, Bamberger M. The effect of powder recycling on the mechanical properties and microstructure of electron beam melted Ti-6Al-4 V specimens. Addit Manuf. 2018;22:834-843. doi: 10.1016/j.addma.2018.06.003
- Carrion PE, Soltani-Tehrani A, Phan N, Shamsaei N. Powder recycling effects on the tensile and fatigue behavior of additively manufactured Ti-6Al-4V parts. JOM. 2019;71(3):963-973. doi: 10.1007/s11837-018-3248-7
- Nezhadfar PD, Soltani-Tehrani A, Sterling A, Tsolas N, Shamsaei N. The Effects of Powder Recycling on the Mechanical Properties of Additively Manufactured 17-4 PH Stainless Steel. Texas: University of Texas at Austin; 2018.
- Drissi-Daoudi R, Masinelli G, De Formanoir C, Wasmer K, Jhabvala J, Logé RE. Acoustic emission for the prediction of processing regimes in Laser Powder Bed Fusion, and the generation of processing maps. Addit Manuf. 2023;67:103484. doi: 10.1016/j.addma.2023.103484
- Shevchik SA, Le-Quang T, Farahani FV, et al. Laser welding quality monitoring via graph support vector machine with data adaptive kernel. IEEE Access. 2019;7:93108-93122. doi: 10.1109/access.2019.2927661
- Wasmer K, Kenel C, Leinenbach C, Shevchik SA. In Situ and Real-Time Monitoring of Powder-Bed AM by Combining Acoustic Emission and Artificial Intelligence. In: Meboldt M, Klahn C, editors. Industrializing Additive Manufacturing - Proceedings of Additive Manufacturing in Products and Applications - AMPA2017. Cham: Springer International Publishing; 2018. p. 200-209.
- Shevchik S, Le-Quang T, Meylan B, et al. Supervised deep learning for real-time quality monitoring of laser welding with X-ray radiographic guidance. Sci Rep. 2020;10(1):3389. doi: 10.1038/s41598-020-60294-x
- Koester LW, Taheri H, Bond LJ, Faierson EJ. Acoustic monitoring of additive manu- facturing for damage and process condition determination. AIP Conf Proc. 2019;2102:020005. doi: 10.1063/1.5099709
- Shevchik SA, Masinelli G, Kenel C, Leinenbach C, Wasmer K. Deep learning for in situ and real-time quality monitoring in additive manufacturing using acoustic emission. IEEE Trans Ind Inform. 2019;15(9):5194-5203. doi: 10.1109/TII.2019.2910524
- Masinelli G, Shevchik SA, Pandiyan V, Quang-Le T, Wasmer K. Artificial intelligence for monitoring and control of metal additive manufacturing. In: Meboldt M, Klahn C, editors. Industrializing Additive Manufacturing. Cham: Springer International Publishing; 2021. p. 205-220.
- Eschner N, Weiser L, Häfner B, Lanza G. Classification of specimen density in Laser powder bed fusion (L-PBF) using in-process structure-borne acoustic process emissions. Addit Manuf. 2020;34:101324. doi: 10.1016/j.addma.2020.101324
- Ito K, Kusano M, Demura M, Watanabe M. Detection and location of microdefects during selective laser melting by wireless acoustic emission measurement. Addit Manuf. 2021;40:101915.
- Taheri H, Koester LW, Bigelow TA, Faierson EJ, Bond LJ. In situ additive manufacturing process monitoring with an acoustic technique: Clustering performance evaluation using k-means algorithm. J Manuf Sci Eng. 2019;141(4):041011. doi: 10.1115/1.4042786
- Yang L, Lo L, Ding S, Özel T. Monitoring and detection of meltpool and spatter regions in laser powder bed fusion of super alloy Inconel 625. Prog Addit Manuf. 2020;5(4):367-378. doi: 10.1007/s40964-020-00140-8
- Zhang Y, Hong GS, Ye D, Zhu K, Fuh JYH. Extraction and evaluation of melt pool, plume and spatter information for powder-bed fusion AM process monitoring. Mater Design. 2018;156:458-469. doi: 10.1016/j.matdes.2018.07.002
- Nour YA, Gupta N. In-situ monitoring of sub-surface and internal defects in additive manufacturing: A review. Mater Design. 2022;222:111063. doi: 10.1016/j.matdes.2022.111063
- Myers AJ, Quirarte G, Ogoke F, et al. High-resolution melt pool thermal imaging for metals additive manufacturing using the two-color method with a color camera. Addit Manuf. 2023;73:103663. doi: 10.1016/j.addma.2023.103663
- Griffis JC, Shahed KS, Okwudire CE, Manogharan GP. Process Modeling of Multi-Material Laser Powder Bed Fusion. In: Solid Freeform Fabrication Symposium 2023; 2023.
- Küng VE, Scherr R, Markl M, Körner C. Multi-material model for the simulation of powder bed fusion additive manufacturing. Comput Mater Sci. 2021;194:110415. doi: 10.1016/j.commatsci.2021.110415
- Auenhammer RM, Oddy C, Kim J, et al. XX-ray scattering tensor tomography based finite element modelling of heterogeneous materials. NPJ Comput Mater. 2024;10(1):50. doi: 10.1038/s41524-024-01234-5
- Auenhammer RM, Oddy C, Kim J, et al. XX-ray scattering tensor tomography based finite element modelling of heterogeneous materials. NPJ Comput Mater. 2024;10(1):50. doi: 10.1038/s41524-024-01234-5
- Binder M, Anstaett C, Herzer F, et al. Potentials and Challenges of Multi-Material Processing by Laser-Based Powder Bed Fusion. In: Solid Freeform Fabrication Symposium; 2018.
- Paul CP, Yadav SP, Rai AK, Narayanan JA, Bindra KS. Laser directed energy deposition based additive manufacturing of metallic multi-material: A review. J Metall Mater Sci. 2021;63:75-87. doi: 10.1016/j.jmapro.2020.09.008
- Sing SL, Huang S, Goh GD, et al. Emerging metallic systems for additive manufacturing: In-situ alloying and multi-metal processing in laser powder bed fusion. Prog Mater Sci. 2021;119:100795. doi: 10.1016/j.pmatsci.2021.100795
- Mehrpouya M, Tuma D, Vaneker T, Afrasiabi M, Bambach M, Gibson I. Multimaterial powder bed fusion techniques. Rapid Prototyp J. 2022;28(11):1-19. doi: 10.1108/RPJ-01-2022-0014
- Dzogbewu TC, De Beer D. Powder bed fusion of multimaterials. J Manuf Mater Process. 2023;7(1):15. doi: 10.3390/jmmp7010015
- Nandhakumar R, Venkatesan K. A process parameters review on selective laser melting-based additive manufacturing of single and multi-material: Microstructure, physical properties, tribological, and surface roughness. Mater Today Commun. 2023;35:105538. doi: 10.1016/j.mtcomm.2023.105538
- Chen H, He Y, Dash SS, Zou Y. Additive manufacturing of metals and alloys to achieve heterogeneous microstructures for exceptional mechanical properties. Mater Res Lett. 2024;12(3):149-171. doi: 10.1080/21663831.2024.2305261