Explainable prediction of bead geometry in laser-arc hybrid additive manufacturing of Al–Cu alloy using a particle swarm optimization-based ensemble model
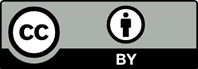
The weld bead is the basic structural unit in metal additive manufacturing, yet the multiphysics coupling inherent to hybrid laser-arc processing greatly complicates the prediction of bead dimensions. Despite the exploration of numerous predictive methods, research on explainable prediction of weld-bead dimensions remains limited. In this work, we developed a particle swarm optimization (PSO)-based ensemble prediction model (PSO-EP) for laser-arc hybrid additive manufacturing, and through SHapley Additive exPlanations (SHAP) analysis, comprehensively uncovered the underlying links between process variables and bead geometry. Experimental evidence indicated that our PSO-EP outperformed individual models and alternative ensembles, delivering superior accuracy, reflected by an R-squared value of 0.9567 for bead width and an R-squared value of 0.9492 for bead height, and markedly lowering prediction errors. The SHAP findings indicated that weld speed is the dominant determinant of bead width, while laser power plays a pivotal role in bead height. Subsequent single-factor dependence analysis showed that different process variables had significantly different impacts on bead size across their respective value intervals. This study provides important theoretical support for the intelligent development of the laser-arc hybrid additive manufacturing process.

- Chen X, Fu Y, Kong F, et al. An in-process multi-feature data fusion nondestructive testing approach for wire arc additive manufacturing. Rapid Prototyp J. 2022;28(3):573-584. doi: 10.1108/RPJ-02-2021-0034
- Shi Y, Yan C, Song B, et al. Recent advances in additive manufacturing technology: Achievements of the rapid manufacturing center in Huazhong University of science and technology. Addit Manuf Front. 2024;3(2):200144. doi: 10.1016/j.amf.2024.200144
- Yang Y, Jiang R, Han C, et al. Frontiers in laser additive manufacturing technology. Addit Manuf Front. 2024;3(4):200160. doi: 10.1016/j.amf.2024.200160
- Tan C, Li R, Su J, et al. Review on field assisted metal additive manufacturing. Int J Mach Tools Manuf. 2023;189:104032. doi: 10.1016/j.ijmachtools.2023.104032
- He F, Yuan L, Mu H, et al. Research and application of artificial intelligence techniques for wire arc additive manufacturing: A State-of-the-art review. Robot Comput Integr Manuf. 2023;82:102525. doi: 10.1016/j.rcim.2023.102525
- Qin J, Hu F, Liu Y, et al. Research and application of machine learning for additive manufacturing. Addit Manuf. 2022;52:102691. doi: 10.1016/j.addma.2022.102691
- McNamara K, Ji Y, Lia F, et al. Predicting phase transformation kinetics during metal additive manufacturing using non-isothermal Johnson-Mehl-Avrami models: Application to Inconel 718 and Ti-6Al-4V. Addit Manuf. 2022;49:102478. doi: 10.1016/j.addma.2021.102478
- Kim DO, Lee CM, Kim DH. Determining optimal bead central angle by applying machine learning to wire arc additive manufacturing (WAAM). Heliyon. 2024;10(1):e23372. doi: 10.1016/j.heliyon.2023.e23372
- Li R, Ju G, Zhao X, et al. Simulation of residual stress and distortion evolution in dual-robot collaborative wire-arc additive manufactured Al-Cu alloys. Virtual Phys Prototyp. 2024;19(1):e2409390. doi: 10.1080/17452759.2024.2409390
- Zhou X, Fang Y, Zhang T, Xiong Z. Retrospective: Advances and opportunities of 3D bioprinting in china over three decades. Addit Manuf Front. 2024;3(4):200157. doi: 10.1016/j.amf.2024.200157
- Singh S, Sharma SK, Rathod DW. A review on process planning strategies and challenges of WAAM. Mater Today Proceed. 2021;47:6564-6575. doi: 10.1016/j.matpr.2021.02.632
- Dai F, Zhang S, Li R, Zhang H. Multiaxis wire and arc additive manufacturing for overhangs based on conical substrates. Rapid Prototy J. 2022;28(1):126-142. doi: 10.1108/RPJ-12-2020-0300
- Sarıkaya M, Başcıl Önler D, Dağlı S, Hartomacıoğlu S, Günay M, Królczyk GM. A review on aluminum alloys produced by wire arc additive manufacturing (WAAM): Applications, benefits, challenges and future trends. J Mater Res Technol. 2024;33:5643-5670. doi: 10.1016/j.jmrt.2024.10.212
- Tan C, Weng F, Sui S, Chew Y, Bi G. Progress and perspectives in laser additive manufacturing of key aeroengine materials. Int J Machine Tools Manuf. 2021;170:103804. doi: 10.1016/j.ijmachtools.2021.103804
- Bai JY, Yang CL, Lin SB, Dong BL, Fan CL. Mechanical properties of 2219-Al components produced by additive manufacturing with TIG. Int J Adv Manuf Technol. 2016;86(1):479-485. doi: 10.1007/s00170-015-8168-x
- Gu J, Ding J, Williams SW, Gu H, Ma P, Zhai Y. The effect of inter-layer cold working and post-deposition heat treatment on porosity in additively manufactured aluminum alloys. J Mater Process Technol. 2016;230:26-34. doi: 10.1016/j.jmatprotec.2015.11.006
- Wang Z, Xufei L, Xin L, et al. Porosity control and properties improvement of Al-Cu alloys via solidification condition optimisation in wire and arc additive manufacturing. Virtual Phys Prototyp. 2024;19(1):e2414408. doi: 10.1080/17452759.2024.2414408
- Pardal G, Martina F, Williams S. Laser stabilization of GMAW additive manufacturing of Ti-6Al-4V components. J Mater Process Technol. 2019;272:1-8. doi: 10.1016/j.jmatprotec.2019.04.036
- Li R, Wang R, Zhou X, et al. Microstructure and mechanical properties of 2319 aluminum alloy deposited by laser and cold metal transfer hybrid additive manufacturing. J Mater Res Technol. 2023;26:6342-6355. doi: 10.1016/j.jmrt.2023.08.312
- Yu A, Pan Y, Wan F, Sun G, Zhang J, Lu X. Rapid accomplishment of cost-effective and macro-defect-free LPBF-processed Ti parts based on deep data augmentation. J Manuf Process. 2024;120:1023-1034. doi: 10.1016/j.jmapro.2024.05.003
- Zhu D, Zhu H, Liu X, et al. CREDO: Efficient and privacy-preserving multi-level medical pre-diagnosis based on ML-KNN. Inform Sci. 2020;514:244-262. doi: 10.1016/j.ins.2019.11.041
- Headley CV, Herrera Del Valle RJ, Ma J, et al. The development of an augmented machine learning approach for the additive manufacturing of thermoelectric materials. J Manuf Process. 2024;116:165-175. doi: 10.1016/j.jmapro.2024.02.045
- Phua A, Cook PS, Davies CHJ, Delaney GW. Smart recoating: A digital twin framework for optimisation and control of powder spreading in metal additive manufacturing. J Manuf Process. 2023;99:382-391. doi: 10.1016/j.jmapro.2023.04.062
- Kwak J, Lee Y, Choi M, Lee S. Deep learning based approaches to enhance energy efficiency in autonomous driving systems. Energy. 2024;307:132625. doi: 10.1016/j.energy.2024.132625
- Delhaes JM, Vieira ACL, Oliveira MD. Natural language processing for participatory corporate foresight: The participant input analyzer for identifying biases and fallacies. Technol Forecast Soc Change. 2024;209:123652. doi: 10.1016/j.techfore.2024.123652
- Ling HB, Huang D, Cui J, Wang CD. HOLT-Net: Detecting smokers via human-object interaction with lite transformer network. Eng Appl Artif Intell. 2023;126:106919. doi: 10.1016/j.engappai.2023.106919
- Le-Hong T, Lin PC, Chen JZ, Pham TDQ, Van Tran X. Data-driven models for predictions of geometric characteristics of bead fabricated by selective laser melting. J Intell Manuf. 2023;34(3):1241-1257. doi: 10.1007/s10845-021-01845-5
- Zhu X, Jiang F, Guo C, Wang Z, Dong T, Li H. Prediction of melt pool shape in additive manufacturing based on machine learning methods. Optics Laser Technol. 2023;159:108964. doi: 10.1016/j.optlastec.2022.108964
- Liu S, Brice C, Zhang X. Interrelated process-geometry-microstructure relationships for wire-feed laser additive manufacturing. Mater Today Commun. 2022;31:103794. doi: 10.1016/j.mtcomm.2022.103794
- Xia C, Pan Z, Polden J, Li H, Xu Y, Chen S. Modelling and prediction of surface roughness in wire arc additive manufacturing using machine learning. J Intell Manuf. 2022;33(5):1467-1482. doi: 10.1007/s10845-020-01725-4
- Oh WJ, Lee CM, Kim DH. Prediction of deposition bead geometry in wire arc additive manufacturing using machine learning. J Mater Res Technol. 2022;20:4283-4296. doi: 10.1016/j.jmrt.2022.08.154
- Šket K, Brezočnik M, Karner T, et al. Predictive modelling of weld bead geometry in wire arc additive manufacturing. J Manuf Mater Process. 2025;9(2):67. doi: 10.3390/jmmp9020067
- Ren Y, Zhang L, Suganthan PN. Ensemble classification and regression-recent developments, applications and future directions [review article]. IEEE Comput Intell Mag. 2016;11(1):41-53. doi: 10.1109/MCI.2015.2471235
- Huang W, Chen S, Xiao J, Jiang X, Jia Y. Laser wire-feed metal additive manufacturing of the al alloy. Optics Laser Technol. 2021;134:106627. doi: 10.1016/j.optlastec.2020.106627
- Shukla P, Chitral S, Kumar T, Kiran DV. The influence of GMAW correction parameters on stabilizing the deposition characteristics for wire arc additive manufacturing. J Manuf Process. 2023;90:54-68. doi: 10.1016/j.jmapro.2023.01.075
- Gong M, Zhang S, Lu Y, Wang D, Gao M. Effects of laser power on texture evolution and mechanical properties of laser-arc hybrid additive manufacturing. Addit Manuf. 2021;46:102201. doi: 10.1016/j.addma.2021.102201
- Ferreira SLC, Bruns RE, Ferreira HS, et al. Box-Behnken design: An alternative for the optimization of analytical methods. Anal Chim Acta. 2007;597(2):179-186. doi: 10.1016/j.aca.2007.07.011
- Fang X, Ren C, Zhang L, Wang C, Huang K, Lu B. A model of bead size based on the dynamic response of CMT-based wire and arc additive manufacturing process parameters. Rapid Prototy J. 2021;27(4):741-753. doi: 10.1108/RPJ-03-2020-0051
- Brown CE. Coefficient of variation. In: Brown CE, editor. Applied Multivariate Statistics in Geohydrology and Related Sciences. Berlin: Springer Berlin Heidelberg; 1998. p. 155-157. doi: 10.1007/978-3-642-80328-4
- Burdick RK, Borror CM, Montgomery DC. A review of methods for measurement systems capability analysis. J Q Technol. 2003;35(4):342-354. doi: 10.1080/00224065.2003.11980232
- Kennedy J, Eberhart R. Particle Swarm Optimization. Vol. 4. United States: IEEE; 1995. p. 1942-1948. doi: 10.1109/ICNN.1995.488968
- Huang GB, Zhu QY, Siew CK. Extreme learning machine: Theory and applications. Neurocomputing. 2006;70(1): 489-501. doi: 10.1016/j.neucom.2005.12.126
- Awad M, Khanna R. Support vector regression. In: Awad M, Khanna R, editors. Efficient Learning Machines: Theories, Concepts, and Applications for Engineers and System Designers. New York: Apress; 2015. p. 67-80. doi: 10.1007/978-1-4302-5990-9
- Schulz E, Speekenbrink M, Krause A. A tutorial on Gaussian process regression: Modelling, exploring, and exploiting functions. J Math Psychol. 2018;85:1-16. doi: 10.1016/j.jmp.2018.03.001
- Shapley LS. Quota solutions of n-person games. In: Harold William K, Albert William T, editors. Contributions to the Theory of Games. Vol. 2. United States: Princeton University Press; 1953. p. 343-360.
- Liu CA, Kuo BS. Model averaging in predictive regressions. Econom J. 2016;19(2):203-231. doi: 10.1111/ectj.12063
- Mu G, Wei Q, Xu Y, Zhang H, Zhang J, Li Q. Capacity estimation for lithium-ion batteries based on heterogeneous stacking model with feature fusion. Energy. 2024;313:133881. doi: 10.1016/j.energy.2024.133881
- Wang R, Cheng MN, Loh YM, Wang C, Fai Cheung C. Ensemble learning with a genetic algorithm for surface roughness prediction in multi-jet polishing. Exp Syst Appl. 2022;207:118024. doi: 10.1016/j.eswa.2022.118024
- Chung J, Shen B, Kong ZJ. Anomaly detection in additive manufacturing processes using supervised classification with imbalanced sensor data based on generative adversarial network. J Intell Manuf. 2024;35(5):2387-2406. doi: 10.1007/s10845-023-02163-8
- Chua C, Liu Y, Williams RJ, Chua CK, Sing SL. In-process and post-process strategies for part quality assessment in metal powder bed fusion: A review. J Manuf Syst. 2024;73: 75-105. doi: 10.1016/j.jmsy.2024.01.004