Gaussian process-based interpretable prediction of melt track morphology through melt pool in additive manufacturing
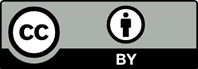
Melt track monitoring in the laser powder bed fusion (LPBF) process is crucial for preventing internal defects in as-printed parts. Uncontrollable melt pool dynamic behavior easily leads to melt track morphology defects. Existing monitoring methods face challenges in balancing modeling accuracy and physical interpretability. Specifically, traditional physics-based models typically require complex monitoring equipment, extensive simulation data, and empirical formulas, resulting in high costs and limited applicability. Meanwhile, conventional data-driven models lack physical constraints, leading to insufficient interpretability, process parameter sensitivity, and poor generalization. To address these challenges, this article proposes a deep Gaussian process-based method for LPBF melt track morphology prediction. The proposed model employs kernel functions in the first layer to learn melt pool evolution patterns and embeds the Rosenthal equation into the second-layer kernel function as a physical constraint, constructing a physically interpretable multilayer Gaussian process framework. Finally, a softmax classifier based on melt track geometric deviation achieves five-category melt track morphology recognition. Multi-condition experimental results demonstrated that the proposed method achieved root mean square errors of 0.069, 0.020, and 0.039 for melt track geometry, outperforming traditional data-driven models in prediction accuracy. The classification accuracy reached 90.76%. Furthermore, the influence of different features on melt track morphology is quantified through time-lagged mutual information analysis and other visualization methods. This study provides an effective solution for achieving quality monitoring and defect prediction in the LPBF process.

- Khairallah SA, Martin AA, Lee JR, et al. Controlling interdependent meso-nanosecond dynamics and defect generation in metal 3D printing. Science. 2020;368(6491):660-665. doi: 10.1126/science.aay7830
- Fang Q, Tan Z, Li H, et al. In-situ capture of melt pool signature in selective laser melting using U-Net-based convolutional neural network. J Manuf Process. 2021;68:347-355. doi: 10.1016/j.jmapro.2021.05.052
- Yang L, Lo L, Ding S, Özel T. Monitoring and detection of meltpool and spatter regions in laser powder bed fusion of super alloy Inconel 625. Prog Addit Manuf. 2020;5(4):367-378. doi: 10.1007/s40964-020-00140-8
- Liu J, Wei B, Chang H, Li J, Yang G. Review of visual measurement methods for metal vaporization processes in laser powder bed fusion. Micromachines (Basel). 2023;14(7):1351. doi: 10.3390/mi14071351
- Forien JB, Calta NP, DePond PJ, Guss GM, Roehling TT, Matthews MJ. Detecting keyhole pore defects and monitoring process signatures during laser powder bed fusion: A correlation between in situ pyrometry and ex situ X-ray radiography. Addit Manuf. 2020;35:101336. doi: 10.1016/j.addma.2020.101336
- Khanzadeh M, Chowdhury S, Tschopp MA, Doude HR, Marufuzzaman M, Bian L. In-situ monitoring of melt pool images for porosity prediction in directed energy deposition processes. IISE Trans. 2018;51(5):437-455. doi: 10.1080/24725854.2017.1417656
- Khanzadeh M, Dantin M, Tian W, Priddy MW, Doude H, Bian L. Fast prediction of thermal data stream for direct laser deposition processes using network-based tensor regression. J Manuf Sci Eng. 2021;144(4):041004. doi: 10.1115/1.4052207
- Scime L, Beuth J. Anomaly detection and classification in a laser powder bed additive manufacturing process using a trained computer vision algorithm. Addit Manuf. 2018;19:114-126. doi: 10.1016/j.addma.2017.11.009
- Okaro IA, Jayasinghe S, Sutcliffe C, Black K, Paoletti P, Green PL. Automatic fault detection for laser powder-bed fusion using semi-supervised machine learning. Addit Manuf. 2019;27:42-53. doi: 10.1016/j.addma.2019.01.006
- Yuan B, Giera B, Guss G, Matthews M, McMains S. Semi-supervised convolutional neural networks for in-situ video monitoring of selective laser melting. In: 2019 IEEE Winter Conference on Applications of Computer Vision (WACV). United States: IEEE; 2019. p. 744-753. doi: 10.1109/WACV.2019.00084
- Yuan B, Guss GM, Wilson AC, et al. Machine-learning-based monitoring of laser powder bed fusion. Adv Mater Technol. 2018;3(12):1800136. doi: 10.1002/admt.201800136
- Mojahed Yazdi R, Imani F, Yang H. A hybrid deep learning model of process-build interactions in additive manufacturing. J Manuf Syst. 2020;57:460-468. doi: 10.1016/j.jmsy.2020.11.001
- Lopez F, Witherell P, Lane B. Identifying uncertainty in laser powder bed fusion additive manufacturing models. J Mech Des. 2016;138(11):114502. doi: 10.1115/1.4034103
- Mahmoudi M, Ezzat A, Elwany A. Layerwise anomaly detection in laser powder-bed fusion metal additive manufacturing. J Manuf Sci Eng. 2019;141(3):031002. doi: 10.1115/1.4042108
- Gaikwad A, Giera B, Guss GM, Forien JB, Matthews MJ, Rao P. Heterogeneous sensing and scientific machine learning for quality assurance in laser powder bed fusion - a single-track study. Addit Manuf. 2020;36:101659. doi: 10.1016/j.addma.2020.101659
- Guo K, Qiao L, Huang Z, Anwer N, Cao Y. A computational model of melt pool morphology for selective laser melting process. Int J Adv Manuf Technol. 2022;121(3-4):1651-1673. doi: 10.1007/s00170-022-09366-y
- Zhang H, Vallabh CK, Zhao X. Registration and fusion of large-scale melt pool temperature and morphology monitoring data demonstrated for surface topography prediction in LPBF. Addit Manuf. 2022;58:103075. doi: 10.1016/j.addma.2022.103075
- Biggio L, Wieland A, Chao MA, Kastanis I, Fink O. Uncertainty-aware prognosis via deep gaussian process. IEEE Access. 2021;9:123517-123527. doi: 10.1109/ACCESS.2021.3110049
- Fan Z, Lu M, Huang H. Selective laser melting of alumina: A single track study. Ceram Int. 2018;44(8):9484-9493. doi: 10.1016/j.ceramint.2018.02.166
- Yadroitsev I, Krakhmalev P, Yadroitsava I, Johansson S, Smurov I. Energy input effect on morphology and microstructure of selective laser melting single track from metallic powder. J Mater Process Technol. 2013;213(4):606-613. doi: 10.1016/j.jmatprotec.2012.11.014
- Yang J, Liu G, Zhu W, et al. High-precision and ultraspeed monitoring of melt-pool morphology in laser-directed energy deposition using deep learning. Addit Manuf Front. 2025;4(2):200199. doi: 10.1016/j.amf.2025.200199
- Xiang Y, Zhang S, Wei Z, et al. Forming and defect analysis for single track scanning in selective laser melting of Ti6Al4V. Appl Phys A. 2018;124(10):685. doi: 10.1007/s00339-018-2056-9
- Hu Z, Nagarajan B, Song X, Huang R, Zhai W, Wei J. Formation of SS316L single tracks in micro selective laser melting: Surface, geometry, and defects. Adv Mater Sci Eng. 2019;2019:9451406. doi: 10.1155/2019/9451406
- Zhou H, Su H, Guo Y, et al. Formation and evolution of surface morphology in overhang structure of IN718 superalloy fabricated by laser powder bed fusion. Acta Metall Sin. 2023;36(9):1433-1453. doi: 10.1007/s40195-023-01546-3
- Li C, Guo YB, Zhao JB. Interfacial phenomena and characteristics between the deposited material and substrate in selective laser melting Inconel 625. J Mater Process Technol. 2017;243:269-281. doi: 10.1016/j.jmatprotec.2016.12.033
- Khairallah SA, Anderson AT, Rubenchik A, King WE. Laser powder-bed fusion additive manufacturing: Physics of complex melt flow and formation mechanisms of pores, spatter, and denudation zones. Acta Mater. 2016;108:36-45. doi: 10.1016/j.actamat.2016.02.014
- Chen H, Lin X, Sun Y, Wang S, Zhu K, Dan B. Revealing formation mechanism of end of process depression in laser powder bed fusion by multi-physics meso-scale simulation. Virtual Phys Prototyp. 2024;19(1):e2326599. doi: 10.1080/17452759.2024.2326599
- Yuan P, Gu D. Molten pool behaviour and its physical mechanism during selective laser melting of TiC/AlSi10Mg nanocomposites: Simulation and experiments. J Phys D Appl Phys. 2015;48(3):035303. doi: 10.1088/0022-3727/48/3/035303
- Yuan W, Chen H, Cheng T, Wei Q. Effects of laser scanning speeds on different states of the molten pool during selective laser melting: Simulation and experiment. Mater Des. 2020;189:108542. doi: 10.1016/j.matdes.2020.108542
- Caprio L, Demir A, Previtali B. Observing molten pool surface oscillations during keyhole processing in laser powder bed fusion as a novel method to estimate the penetration depth. Addit Manuf. 2020;36:101470. doi: 10.1016/j.addma.2020.101470
- Tang M, Pistorius PC, Beuth JL. Prediction of lack-of-fusion porosity for powder bed fusion. Addit Manuf. 2017;14:39-48. doi: 10.1016/j.addma.2016.12.001
- Ning J, Mirkoohi E, Dong Y, Sievers DE, Garmestani H, Liang SY. Analytical modeling of 3D temperature distribution in selective laser melting of Ti-6Al-4V considering part boundary conditions. J Manuf Process. 2019;44:319-326. doi: 10.1016/j.jmapro.2019.06.013
- Promoppatum P, Yao SC, Pistorius PC, Rollett AD. A comprehensive comparison of the analytical and numerical prediction of the thermal history and solidification microstructure of inconel 718 products made by laser powder-bed fusion. Engineering. 2017;3(5):685-694. doi: 10.1016/J.ENG.2017.05.023
- Wang W, Liang SY. A 3D analytical modeling method for keyhole porosity prediction in laser powder bed fusion. Int J Adv Manuf Technol. 2022;120(5-6):3017-3025. doi: 10.1007/s00170-022-08898-7
- Yang J, Han J, Yu H, et al. Role of molten pool mode on formability, microstructure and mechanical properties of selective laser melted Ti-6Al-4V alloy. Mater Des. 2016;110:558-570. doi: 10.1016/j.matdes.2016.08.036
- Kamath C, El-dasher B, Gallegos GF, King WE, Sisto A. Density of additively-manufactured, 316L SS parts using laser powder-bed fusion at powers up to 400 W. Int J Adv Manuf Technol. 2014;74(1-4):65-78. doi: 10.1007/s00170-014-5954-9
- Salimbeni H, Deisenroth M. Doubly stochastic variational inference for deep Gaussian processes. In: Advances in Neural Information Processing Systems. United States: Morgan Kaufmann Publishers Inc.; 2017. p. 30. doi: 10.48550/arXiv.1705.08933
- Roth K, Pemula L, Zepeda J, Scholkopf B, Brox T, Gehler P. Towards total recall in industrial anomaly detection. In: IEEE/CVF Conference on Computer Vision and Pattern Recognition (CVPR). United States: IEEE; 2022. p. 14298-14308. doi: 10.1109/cvpr52688.2022.01392
- Shojaie A, Fox EB. Granger causality: A review and recent advances. Annu Rev Stat Appl. 2022;9(1):289-319. doi: 10.1146/annurev-statistics-040120-010930