Ceramic additive manufacturing via vat photopolymerization
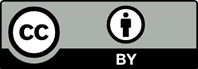
Vat photopolymerization (VPP) additive manufacturing has emerged as a transformative approach for fabricating high-performance ceramic components with intricate geometries. This review comprehensively examines VPP technologies, including stereolithography, digital light processing, and two-photon polymerization, highlighting their mechanisms, advantages, and limitations. Critical challenges faced by ceramic VPP include light scattering from particles, slurry viscosity control, sedimentation, and post-processing shrinkage. The required optimized characteristics suitable for VPP of ceramic slurries and pre-ceramic polymers are also discussed. The latter offers a promising alternative, enabling the shaping of complex architectures with reduced defects and enhanced thermal stability, supported by active/passive fillers that mitigate shrinkage and improve density. Ceramic VPP applications span biomedical implants, microreactors, aerospace components, and energy devices. Key advancements include the integration of multimaterial systems, hybrid precursors, and nanocomposites. However, challenges persist in achieving uniform curing depths, minimizing anisotropic shrinkage, and scaling production. Future research should focus on material innovation, process parameter optimization, and advanced characterization techniques to unlock the full potential of VPP for next-generation ceramic manufacturing. This technology offers an effective solution for high-value ceramic applications.

- Lee JY, An J, Chua CK. Fundamentals and applications of 3D printing for novel materials. Appl Mater Today. 2017;7:120-133. doi: 10.1016/j.apmt.2017.02.004
- Chen Z, Li Z, Li J, et al. 3D printing of ceramics: A review. J Eur Ceram Soc. 2019;39(4):661-687. doi: 10.1016/j.jeurceramsoc.2018.11.013
- Davoudinejad A. Vat photopolymerization methods in additive manufacturing. In: Additive Manufacturing. Netherlands: Elsevier; 2021. p. 159-181. doi: 10.1016/B978-0-12-818411-0.00007-0
- Rahaman MN. Ceramic Processing and Sintering. United States: CRC Press; 2017. doi: 10.1201/9781315274126
- Hull CW. Inventor; Methods and Apparatus for Production of Three-dimensional Objects by Stereolithography. USA Patent US5236637; 1986.
- Jacobs PF. Rapid Prototyping & Manufacturing: Fundamentals of Stereolithography. United States: Society of Manufacturing Engineers; 1992.
- Parra-Cabrera C, Achille C, Kuhn S, Ameloot R. 3D printing in chemical engineering and catalytic technology: Structured catalysts, mixers and reactors. Chem Soc Rev. 2018;47(1):209-230. doi: 10.1039/C7CS00631D
- Choi JW, Kim HC, Wicker R. Multi-material stereolithography. J Mater Process Technol. 2011;211(3):318-328. doi: 10.1016/j.jmatprotec.2010.10.003
- Klein J, Stern M, Franchin G, et al. Additive manufacturing of optically transparent glass. 3D Print Addit Manuf. 2015;2(3):92-105. doi: 10.1089/3dp.2015.0021
- Halloran JW. Ceramic stereolithography: Additive manufacturing for ceramics by photopolymerization. Annu Rev Mater Res. 2016;46(1):19-40. doi: 10.1146/annurev-matsci-070115-031841
- Griffith ML, Halloran JW. Ultraviolet curable ceramic suspensions for stereolithography of ceramics. In: Proceedings Solid Freeform Fabrication Symposium; 1994. p. 529-534.
- Nakamoto T, Yamaguchi K. Consideration on the Producing of High Aspect Ratio Micro Parts using UV Sensitive Photopolymer. United States: IEEE; 1996. p. 53-58.
- Bertsch A, Zissi S, Jezequel J, Corbel S, Andre J. Microstereophotolithography using a liquid crystal display as dynamic mask-generator. Microsyst Technol. 1997;3(2):42-47.
- Göppert-Mayer M. Elementary processes with two quantum transitions. Ann Phys. 2009;521(7-8):466-479. doi: 10.1002/andp.200952107-804
- Kaiser W, Garrett CGB. Two-photon excitation in CaF2:Eu2+. Phys Rev Lett. 1961;7(6):229-231. doi: 10.1103/PhysRevLett.7.229
- Paz VF, Emons M, Obata K, et al. Development of functional sub-100 nm structures with 3D two-photon polymerization technique and optical methods for characterization. J Laser Appl. 2012;24(4):042004. doi: 10.2351/1.4712151
- Bhawalkar JD, He GS, Prasad PN. Nonlinear multiphoton processes in organic and polymeric materials. Rep Prog Phys. 1996;59(9):1041. doi: 10.1088/0034-4885/59/9/001
- LaFratta CN, Fourkas JT, Baldacchini T, Farrer RA. Multiphoton fabrication. Angew Chem Int Ed. 2007;46(33):6238-6258. doi: 10.1002/anie.200603995
- Fried JR. Polymer Science and Technology. United Kingdom: Pearson Education; 2014.
- Serbin J, Egbert A, Ostendorf A, et al. Femtosecond laser-induced two-photon polymerization of inorganic-organic hybrid materials for applications in photonics. Opt Lett. 2003;28(5):301-303. doi: 10.1364/ol.28.000301
- Zipfel WR, Williams RM, Webb WW. Nonlinear magic: Multiphoton microscopy in the biosciences. Nat Biotechnol. 2003;21(11):1369-1377. doi: 10.1038/nbt899
- Tumbleston John R, Shirvanyants D, Ermoshkin N, et al. Continuous liquid interface production of 3D objects. Science. 2015;347(6228):1349-1352. doi: 10.1126/science.aaa2397
- González-Méijome JM, Compañ-Moreno V, Riande E. Determination of oxygen permeability in soft contact lenses using a polarographic method: estimation of relevant physiological parameters. Ind Eng Chem Res. 2008;47(10):3619-3629.
- Wang G, Song Y. Enhancing the yield of polycarbosilane synthesis via recycling of liquid by-product at atmospheric pressure. Ceram Int. 2018;44(6):6474-6478. doi: 10.1016/j.ceramint.2018.01.101
- Colombo P, Mera G, Riedel R, Sorarù GD. Polymer-derived ceramics: 40 years of research and innovation in advanced ceramics. J Am Ceram Soc. 2010;93(7):1805-1837. doi: 10.1111/j.1551-2916.2010.03876.x
- Martínez-Crespiera S, Ionescu E, Schlosser M, et al. Fabrication of silicon oxycarbide-based microcomponents via photolithographic and soft lithography approaches. Sens Actuat A Phys. 2011;169(1):242-249. doi: 10.1016/j.sna.2011.04.041
- Kashimura S, Tane Y, Ishifune M, et al. Practical method for the synthesis of polysilanes using Mg and Lewis acid system. Tetrahedron Lett. 2008;49(2):269-271. doi: 10.1016/j.tetlet.2007.11.083
- Jones RG, Holder SJ. High-yield controlled syntheses of polysilanes by the Wurtz-type reductive coupling reaction. Polym Int. 2006;55(7):711-718. doi: 10.1002/pi.1945
- Krempner C. Polysilane dendrimers. Polymers. 2012;4(1):408-447. doi: 10.3390/polym4010408
- Chen J, He G, Liao Z, et al. Control of structure formation of polycarbosilane synthesized from polydimethylsilane by Kumada rearrangement. J Appl Polym Sci. 2008;108(5):3114-3121. doi: 10.1002/app.27847
- Cheng X, Xie Z, Song Y, Xiao J, Wang Y. Structure and properties of polycarbosilane synthesized from polydimethylsilane under high pressure. J Appl Polym Sci. 2006;99(3):1188-1194. doi: 10.1002/app.22465
- Lodhe M, Babu N, Selvam A, Balasubramanian M. Synthesis and characterization of high ceramic yield polycarbosilane precursor for SiC. J Adv Ceram. 2015;4:307-311. doi: 10.1007/s40145-015-0169-8
- He L, Zhang Z, Yang X, Jiao L, Li Y, Xu C. Liquid polycarbosilanes: synthesis and evaluation as precursors for SiC ceramic. Polym Int. 2015;64(8):979-985. doi: 10.1002/pi.4904
- Hörz M, Zern A, Berger F, et al. Novel polysilazanes as precursors for silicon nitride/silicon carbide composites without “free” carbon. J Eur Ceram Soc. 2005;25(2-3):99-110. doi: 10.1016/j.jeurceramsoc.2004.05.003
- Blum YD, Schwartz KB, Laine RM. Preceramic polymer pyrolysis: Part 1 Pyrolytic properties of polysilazanes. J Mater Sci. 1989;24:1707-1718. doi: 10.1007/BF01138991
- Kroke E, Li YL, Konetschny C, Lecomte E, Fasel C, Riedel R. Silazane derived ceramics and related materials. Mater Sci Eng R Rep. 2000;26(4-6):97-199. doi: 10.1016/S0927-796X(00)00013-0
- Soraru GD. Silicon oxycarbide glasses from gels: Code: H1. J Sol Gel Sci Technol. 1994;2:843-848. doi: 10.1007/BF00489675
- Schmitt M. Analysis of silanes and of siloxanes formation by Raman spectroscopy. RSC Adv. 2014;4(4):1907-1917. doi: 10.1039/C3RA45816A
- Mera G, Riedel R, Poli F, Müller K. Carbon-rich SiCN ceramics derived from phenyl-containing poly (silylcarbodiimides). J Eur Ceram Soc. 2009;29(13):2873-2883. doi: 10.1016/j.jeurceramsoc.2009.03.020
- Widgeon S, Mera G, Gao Y, et al. Nanostructure and energetics of carbon-rich SiCN ceramics derived from polysilylcarbodiimides: Role of the nanodomain interfaces. Chem Mater. 2012;24(6):1181-1191. doi: 10.1021/cm3000259
- Gao Y, Mera G, Nguyen H, Morita K, Kleebe HJ, Riedel R. Processing route dramatically influencing the nanostructure of carbon-rich SiCN and SiBCN polymer-derived ceramics. Part I: Low temperature thermal transformation. J Eur Ceram Soc. 2012;32(9):1857-1866. doi: 10.1016/j.jeurceramsoc.2012.01.022
- Zhang Z, Zeng F, Han J, Luo Y, Xu C. Synthesis and characterization of a new liquid polymer precursor for Si-B-C-N ceramics. J Mater Sci. 2011;46:5940-5947. doi: 10.1007/s10853-010-4934-1
- Widgeon S, Mera G, Gao Y, Sen S, Navrotsky A, Riedel R. Effect of precursor on speciation and nanostructure of SiBCN polymer‐derived ceramics. J Am Ceram Soc. 2013;96(5):1651-1659. doi: 10.1111/jace.12217
- Griffith ML, Halloran JW. Freeform fabrication of ceramics via stereolithography. J Am Ceram Soc. 1996;79(10):2601-2608. doi: 10.1111/j.1151-2916.1996.tb09022.x
- Schwartz KB, Rowcliffe DJ. Modeling density contributions in preceramic polymer/ceramic powder systems. J Am Ceram Soc. 1986;69(5):C-106. doi: 10.1111/j.1151-2916.1986.tb04782.x
- Wang WL, Cheah CM, Fuh JYH, Lu L. Influence of process parameters on stereolithography part shrinkage. Mater Design. 1996;17(4):205-213. doi: 10.1016/S0261-3069(97)00020-1
- Travitzky N, Bonet A, Dermeik B, et al. Additive manufacturing of ceramic-based materials. Adv Eng Mater. 2014;16(6):729-754. doi: 10.1002/adem.201400097
- He R, Liu W, Wu Z, et al. Fabrication of complex-shaped zirconia ceramic parts via a DLP- stereolithography-based 3D printing method. Ceram Int. 2018;44(3):3412-3416. doi: 10.1016/j.ceramint.2017.11.135
- Zhou M, Liu W, Wu H, et al. Preparation of a defect-free alumina cutting tool via additive manufacturing based on stereolithography - Optimization of the drying and debinding processes. Ceram Int. 2016;42(10):11598-11602. doi: 10.1016/j.ceramint.2016.04.007
- Li S, Shan Y, Chen J, et al. 3D printing and biomedical applications of piezoelectric composites: A critical review. Adv Mater Technol. 2025;10(5):2401160.
- Hamza M, Kanwal Q, Hussain MI, et al. Recent progress in 3D printed piezoelectric materials for biomedical applications. Mater Sci Eng R Rep. 2025;164:100962.
- Zhang P, He R. 3D-printed silicon nitride ceramic implants for clinical applications: The state of the art and prospects. RSC Adv. 2025;15(1):406-419.
- Scheithauer U, Schwarzer E, Ganzer G, et al. Microhreactors made by lithography‐based ceramic manufacturing (LCM). In: Additive Manufacturing and Strategic Technologies in Advanced Ceramics: Ceramic Transactions. Vol. 258. United States: Wiley; 2015. p. 31-41. doi: 10.1002/9781119183860.ch3
- Schwentenwein M, Homa J. Additive manufacturing of dense alumina ceramics. Int J Appl Ceram Technol. 2015;12(1):1-7. doi: 10.1111/ijac.12324
- Scheithauer U, Schwarzer E, Moritz T, Michaelis A. Additive manufacturing of ceramic heat exchanger: Opportunities and limits of the lithography-based ceramic manufacturing (LCM). J Mater Eng Perform. 2018;27(1):14-20. doi: 10.1007/s11665-017-3056-1
- Lantada AD, de Blas Romero A, Schwentenwein M, Jellinek C, Homa J. Lithography-based ceramic manufacture (LCM) of auxetic structures: Present capabilities and challenges. Smart Mater Struct. 2016;25(5):054015. doi: 10.1088/0964-1726/25/5/054015
- Qu P, Liang G, Hussain MI, et al. Low-temperature fabrication of high-specific strength SiC-based ceramics via photopolymerization 3D printing with controllable anisotropy. Int J Extreme Manuf. 2025;7(5):055002. doi: 10.1088/2631-7990/add2e1
- Luo X, Ren W, Xing H, Hussain MI, Chen Z. Additively manufactured Li4SiO4 ceramic pebbles with radial pores for enhanced performance. Ceram Int. 2025. doi. 10.1016/j.ceramint.2025.01.332
- Ren W, Liu W, Luo X, Liu Z, Liu C, Chen Z. 3D printing of cordierite glass-ceramics. Ceram Int. 2025;51(2):1632-1642.
- Gentry SP, Halloran JW. Depth and width of cured lines in photopolymerizable ceramic suspensions. J Eur Ceram Soc. 2013;33(10):1981-1988. doi: 10.1016/j.jeurceramsoc.2013.02.012
- de Hazan Y, Penner D. SiC and SiOC ceramic articles produced by stereolithography of acrylate modified polycarbosilane systems. J Eur Ceram Soc. 2017;37(16):5205-5212. doi: 10.1016/j.jeurceramsoc.2017.03.021
- Badev A, Abouliatim Y, Chartier T, et al. Photopolymerization kinetics of a polyether acrylate in the presence of ceramic fillers used in stereolithography. J Photochem Photobiol A. 2011;222(1):117-122. doi: 10.1016/j.jphotochem.2011.05.010
- Leigh SJ, Purssell C, Bowen J, Hutchins DA, Covington JA, Billson D. A miniature flow sensor fabricated by micro-stereolithography employing a magnetite/acrylic nanocomposite resin. Sens Actuat A. 2011;168(1):66-71. doi: 10.1016/j.sna.2010.12.007
- Chen W, Kirihara S, Miyamoto Y. Fabrication and measurement of micro three‐dimensional photonic crystals of SiO2 ceramic for terahertz wave applications. J Am Ceram Soc. 2007;90(7):2078-2081. doi: 10.1111/j.1551-2916.2007.01724.x
- Du D, Asaoka T, Ushida T, Furukawa KS. Fabrication and perfusion culture of anatomically shaped artificial bone using stereolithography. Biofabrication. 2014;6(4):045002. doi: 10.1088/1758-5082/6/4/045002
- Lian Q, Sui W, Wu X, Yang F, Yang S. Additive manufacturing of ZrO2 ceramic dental bridges by stereolithography. Rapid Prototyp J. 2018;24(1):114-119. doi: 10.1108/RPJ-09-2016-0144
- Bae CJ, Halloran JW. Influence of residual monomer on cracking in ceramics fabricated by stereolithography. Int J Appl Ceram Technol. 2011;8(6):1289-1295. doi: 10.1111/j.1744-7402.2011.02611.x
- Bae CJ, Ramachandran A, Halloran JW. Quantifying particle segregation in sequential layers fabricated by additive manufacturing. J Eur Ceram Soc. 2018;38:4082-4088. doi: 10.1016/j.jeurceramsoc.2018.07.040
- Mitteramskogler G, Gmeiner R, Felzmann R, et al. Light curing strategies for lithography-based additive manufacturing of customized ceramics. Addit Manuf. 2014;1:110-118. doi: 10.1016/j.addma.2014.08.004
- Pfaffinger M, Mitteramskogler G, Gmeiner R, Stampfl J. Thermal Debinding of Ceramic-filled Photopolymers. Switzerland: Trans Tech Publ; 2015. p. 75-81. doi: 10.1002/9781119183860.ch10
- Eckel ZC, Zhou C, Martin JH, Jacobsen AJ, Carter WB, Schaedler TA. Additive manufacturing of polymer-derived ceramics. Science. 2016;351(6268):58-62. doi: 10.1126/science.aad2688
- Chaudhary RP, Parameswaran C, Idrees M, et al. Additive manufacturing of polymer-derived ceramics: Materials, technologies, properties and potential applications. Prog Mater Sci. 2022;128:100969. doi: 10.1016/j.pmatsci.2022.100969
- Toma L, Kleebe HJ, Müller MM, et al. Correlation between intrinsic microstructure and piezoresistivity in a SiOC polymer‐derived ceramic. J Am Ceram Soc. 2012; 95(3):1056-1061. doi: 10.1111/j.1551-2916.2011.05026.x
- Colombo P, Bernardo E, Parcianello G. Multifunctional advanced ceramics from preceramic polymers and nano-sized active fillers. J Eur Ceram Soc. 2013;33(3):453-469. doi: 10.1016/j.jeurceramsoc.2012.10.006
- Kim KJ, Eom JH, Kim YW, Seo WS. Electrical conductivity of dense, bulk silicon-oxycarbide ceramics. J Eur Ceram Soc. 2015;35(5):1355-1360. doi: 10.1016/j.jeurceramsoc.2014.12.009
- Li Z, Chen Z, Liu J, et al. Additive manufacturing of lightweight and high-strength polymer-derived SiOC ceramics. Virtual Phys Prototyp. 2020;15(2):163-177. doi: 10.1080/17452759.2019.1710919
- Fu Y, Xu G, Chen Z, Liu C, Wang D, Lao C. Multiple metals doped polymer-derived SiOC ceramics for 3D printing. Ceram Int. 2018;44(10):11030-11038. doi: 10.1016/j.ceramint.2018.03.075
- Zocca A, Gomes CM, Staude A, Bernardo E, Günster J, Colombo P. SiOC ceramics with ordered porosity by 3D-printing of a preceramic polymer. J Mater Res. 2013;28(17):2243-2252. doi: 10.1557/jmr.2013.129
- Zhou S, Mei H, Chang P, Lu M, Cheng L. Molecule editable 3D printed polymer-derived ceramics. Coord Chem Rev. 2020;422:213486. doi: 10.1016/j.ccr.2020.213486
- Hundley JM, Eckel ZC, Schueller E, et al. Geometric characterization of additively manufactured polymer derived ceramics. Addit Manuf. 2017;18:95-102. doi: 10.1016/j.addma.2017.09.005
- Zanchetta E, Cattaldo M, Franchin G, et al. Stereolithography of SiOC ceramic microcomponents. Adv Mater. 2016;28(2):370-376. doi: 10.1002/adma.201503470
- Li S, Duan W, Zhao T, et al. The fabrication of SiBCN ceramic components from preceramic polymers by digital light processing (DLP) 3D printing technology. J Eur Ceram Soc. 2018;38(14):4597-4603. doi: 10.1016/j.jeurceramsoc.2018.05.043
- Wang X, Schmidt F, Hanaor D, Kamm PH, Li S, Gurlo A. Additive manufacturing of ceramics from preceramic polymers: A versatile stereolithographic approach assisted by thiol-ene click chemistry. Addit Manuf. 2019;27:80-90. doi: 10.1016/j.addma.2019.02.012
- Brodnik NR, Schmidt J, Colombo P, Faber KT. Analysis of multi-scale mechanical properties of ceramic trusses prepared from preceramic polymers. Addit Manuf. 2020;31:100957. doi: 10.1016/j.addma.2019.100957
- Gyak KW, Vishwakarma NK, Hwang YH, Kim J, Yun HS, Kim DP. 3D-printed monolithic SiCN ceramic microreactors from a photocurable preceramic resin for the high temperature ammonia cracking process. 10.1039/ C9RE00201D. React Chem Eng. 2019;4(8):1393-1399. doi: 10.1039/C9RE00201D
- Schmidt J, Altun AA, Schwentenwein M, Colombo P. Complex mullite structures fabricated via digital light processing of a preceramic polysiloxane with active alumina fillers. J Eur Ceram Soc. 2019;39(4):1336-1343.doi: 10.1016/j.jeurceramsoc.2018.11.038
- Xiong SF, Liu J, Cao JW, et al. 3D printing of crack-free dense polymer-derived ceramic monoliths and lattice skeletons with improved thickness and mechanical performance. Addit Manuf. 2022;57:102964. doi: 10.1016/j.addma.2022.102964
- Jiang L, Long C, Xiong S, et al. 4D printing of shape-programmable polymer-derived ceramics via two-stage folding-assisted pyrolysis strategy. Virtual Phys Prototyp. 2024;19(1):e2406408. doi: 10.1080/17452759.2024.2406408
- Pham TA, Kim DP, Lim TW, Park SH, Yang DY, Lee KS. Three-dimensional SiCN ceramic microstructures via nano-stereolithography of inorganic polymer photoresists. 2006;16(9):1235-1241. doi: 10.1002/adfm.200600009
- Jang D, Meza LR, Greer F, Greer JR. Fabrication and deformation of three-dimensional hollow ceramic nanostructures. Nat Mater. 2013;12(10):893. doi: 10.1038/nmat3738