Using agglomerate-free nanopowder as sliding friction reducer between alumina platelets in an ultraviolet-curable slurry for vat polymerization additive manufacturing
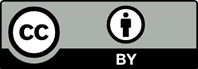
Nature’s ability to adapt and survive the harshest environment offers humankind an important source of muses in the efforts to create and improve existing materials. In this study, we demonstrated a concept of using agglomerate-free nanopowder as a sliding friction reducer between alumina platelets in a slurry. An ultraviolet-curable slurry containing predominantly alumina platelets exhibited favorable rheological characteristics to align the platelets with a coating blade in a vat polymerization printer. Consequently, a ceramic part with nacre‑like structure could be printed and infiltrated with a secondary phase. Microscopy study on the fracture surfaces revealed various toughening mechanisms such as severing of the bridges between platelets and crack deflection by the platelets. Fracture of a three-point bent part mainly occurred due to the pull-out of platelets and failure of the polymer phase. The findings of this study suggest promising avenues for future research, including the additive manufacturing of larger objects consisting of nacre-like microstructures.
- Gao H, Ji B, Jager IL, Arzt E, Fratzl P. Materials become insensitive to flaws at nanoscale: Lessons from nature. Proc Natl Acad Sci U S A. 2003;100(10):5597-600. doi: 10.1073/pnas.0631609100
- Gibson LJ, Ashby MF, Karam G, Wegst U, Shercliff H. The mechanical properties of natural materials. II. Microstructures for mechanical efficiency. Proc R Soc London A. 1997;450(1938):141-162. doi: 10.1098/rspa.1995.0076
- Ashby MF, Gibson LJ, Wegst U, Olive R. The mechanical properties of natural materials. I. Material property charts. Proc R Soc London A. 1995;450(1938):123-140. doi: 10.1098/rspa.1995.0075
- Mayer G. Rigid biological systems as models for synthetic composites. Science. 2005;310(5751):1144-1147. doi: 10.1126/science.1116994
- Wegst UG, Bai H, Saiz E, Tomsia AP, Ritchie RO. Bioinspired structural materials. Nat Mater. 2015;14(1):23-36. doi: 10.1038/nmat4089
- Wang R, Suo Z, Evans A, Yao N, Aksay IA. Deformation mechanisms in nacre. J Mater Res. 2001;16(9):2485-2493. doi: 10.1557/JMR.2001.0340
- Rabiei R, Bekah S, Barthelat F. Failure mode transition in nacre and bone-like materials. Acta Biomater. 2010;6(10):4081-4089. doi: 10.1016/j.actbio.2010.04.008
- Zhao H, Yang Z, Guo L. Nacre-inspired composites with different macroscopic dimensions: Strategies for improved mechanical performance and applications. NPG Asia Mater. 2018;10(4):1-22. doi: 10.1038/s41427-018-0009-6
- Gan MX, Wong CH. Properties of selective laser melted spodumene glass-ceramic. J Eur Ceram Soc. 2017;37(13):4147-4154. doi: 10.1016/j.jeurceramsoc.2017.04.060
- Gan MX, Wong CH. Experimental studies on the properties of selectively laser melted alumina-spodumene composite. Ceram Int. 2018;44(15):19008-19015. doi: 10.1016/j.ceramint.2018.07.144
- Griffith ML, Halloran JW. Freeform fabrication of ceramics via stereolithography. J Am Ceram Soc. 1996;79(10):2601-2608. doi: 10.1111/j.1151-2916.1996.tb09022.x
- Lee YH, Lee JB, Maeng WY, Koh YH, Kim HE. Photocurable ceramic slurry using solid camphor as novel diluent for conventional digital light processing (DLP) process. J Eur Ceram Soc. 2019;39(14):4358-4365. doi: 10.1016/j.jeurceramsoc.2019.05.069
- Zhang K, Xie C, Wang G, He R, Ding G, Wang M, et al. High solid loading, low viscosity photosensitive Al2O3 slurry for stereolithography based additive manufacturing. Ceram Int. 2019;45(1):203-208. doi: 10.1016/j.ceramint.2018.09.152
- Wu X, Zhang Z, Ma D, Lu X, Chen Z, Gao Y, et al. Influence of Al2O3 platelets addition on ceramic slurry and local flow induced platelets alignment in ceramic mask stereolithography process. Ceram Int. 2022;48(9): 13134-13143. doi: 10.1016/j.ceramint.2022.01.190
- Yang Y, Wang Z, He Q, Li X, Lu G, Jiang L, et al. 3D printing of nacre-inspired structures with exceptional mechanical and flame-retardant properties. Research (Wash DC). 2022;2022:e9840574. doi: 10.34133/2022/9840574
- Li T, Liu Q, Qi H, Zhai W. Prestrain programmable 4D printing of nanoceramic composites with bioinspired microstructure. Small. 2022;18(47):e2204032. doi: 10.1002/smll.202204032
- Lewis JA. Colloidal processing of ceramics. J Am Ceram Soc. 2004;83(10):2341-2359. doi: 10.1111/j.1151-2916.2000.tb01560.x
- Song F, Soh AK, Bai YL. Structural and mechanical properties of the organic matrix layers of nacre. Biomaterials. 2003;24(20):3623-3631. doi: 10.1016/s0142-9612(03)00215-1
- Goswami A, Umarji AM, Madras G. Thermomechanical and fractographic behavior of poly (HDDA‐co‐MMA): A study for its application in microcantilever sensors. Polym Adv Technol. 2012;23(12):1604-1611. doi: 10.1002/pat.3035