Role of customized scan strategies and dwell time on microstructure and properties of additively manufactured 316L stainless steel
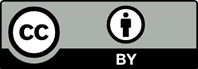
Direct energy deposition (DED)-based additive manufacturing facilitates fabrication of medium-to-large functional parts. This study assesses the role of varying scan strategies and dwell time between each layer to control the cooling rate of 316L stainless steel produced by the laser-engineered net shaping-DED method. Customized print patterns were designed, keeping other optimized print parameters constant to obtain printed parts with better dimensional tolerance. The parts, which were >99% dense, were fabricated in a controlled argon environment. A heterogeneous microstructure consisting of a cellular columnar and equiaxed substructure was obtained. Two-dimensional X-ray diffraction revealed the presence of a single-phase γ-austenitic FCC phase. A refined microstructure with less elemental segregation was noticed with an increase in dwell time between the print layers. Internal defect analysis using X-ray micro-computed tomography revealed low lack-of-fusion voids along the build direction without any micro-cracks, which is attributed to higher cooling rates between subsequent print layers. As demonstrated in a mechanical performance evaluation of tensile and micro-hardness properties, better performance can be achieved by controlling the cooling rate and customizing deposition patterns.
- Frazier WE. Metal additive manufacturing: A review. J Mater Eng Perform. 2014;23(6):1917-1928. doi: 10.1007/s11665-014-0958-z
- DebRoy T, Wei HL, Zuback JS, et al. Additive manufacturing of metallic components -process, structure and properties. Prog Mater Sci. 2018;92:112-224. doi: 10.1016/j.pmatsci.2017.10.001
- Sames WJ, List FA, Pannala S, Dehoff RR, Babu SS. The metallurgy and processing science of metal additive manufacturing. Int Mater Rev. 2016;61(5):315-360. doi: 10.1080/09506608.2015.1116649
- Zhai X, Jin L, Jiang J. A survey of additive manufacturing reviews. Mater Sci Addit Manuf. 2022;1(4):21. doi: 10.18063/msam.v1i4.21
- Turgut B, Gürol U, Onler R. Effect of interlayer dwell time on output quality in wire arc additive manufacturing of low carbon low alloy steel components. Int J Adv Manuf Technol. 2023;126(11-12):5277-5288. doi: 10.1007/s00170-023-11481-3
- D’Andrea D. Additive manufacturing of AISI 316L stainless steel: A review. Metals (Basel). 2023;13(8):1370. doi: 10.3390/met13081370
- Thompson SM, Bian L, Shamsaei N, Yadollahi A. An overview of direct laser deposition for additive manufacturing; Part I: Transport phenomena, modeling and diagnostics. Addit Manuf. 2015;8:36-62. doi: 10.1016/j.addma.2015.07.001
- Balhara H, Botcha B, Wolff SJ, Bukkapatnam STS. Ripple formations determine the heterogeneous microstructure of directed energy deposition (DED)-printed 316L components. Mater Des. 2023;227:2023. doi: 10.1016/j.matdes.2023.111756
- Izadi M, Farzaneh A, Mohammed M, Gibson I, Rolfe B. A review of laser engineered net shaping (LENS) build and process parameters of metallic parts. Rapid Prototyp J. 2020;26(6):1059-1078. doi: 10.1108/RPJ-04-2018-0088
- Pathak P, Majkic G, Erickson T, Chen T, Selvamanickam V. Two-dimensional X-ray diffraction (2D-XRD) and micro-computed tomography (micro-CT) characterization of additively manufactured 316L stainless steel. Available at SSRN 4529173 (2023). doi: 10.2139/ssrn.4529173
- Veiga F, Arizmendi M, Suarez A, Bilbao J, Uralde V. Different path strategies for directed energy deposition of crossing intersections from stainless steel SS316L-Si. J Manuf Processes. 2022;84:953-964. doi: 10.1016/j.jmapro.2022.10.039
- Amar E, Popov V, Sharma VM, Andreev Batat S, Halperin D, Eliaz N. Response surface methodology (RSM) approach for optimizing the processing parameters of 316L SS in directed energy deposition. Materials (Basel). 2023;16(23):7253. doi: 10.3390/ma16237253
- Izadi M, Farzaneh A, Gibson I, Rolfe B. The Effect of Process Parameters and Mechanical Properties of Direct Energy Deposited Stainless Steel 316. In: Solid Freeform Fabrication 2017: Proceedings of the 28th Annual International Solid Freeform Fabrication Symposium-an Additive Manufacturing Conference; 2020. p. 1058-1067.
- Kuzminova YO, Firsov DG, Konev SD, et al. Structure control of 316L stainless steel through an additive manufacturing. Lett Mater. 2019;9(4):551-555. doi: 10.22226/2410-3535-2019-4-551-555
- Karlapudy SP, Nancharaiah T, Rao VVS. Influence of different build orientation and laser scan strategies on surface quality, mechanical and material characteristics of 18 Ni-300 maraging steel processed through DMLS. Aust J Mech Eng. 2021;21(4):1381-1395. doi: 10.1080/14484846.2021.2007620
- Liu M, Kumar A, Bukkapatnam S, Kuttolamadom M. A review of the anomalies in directed energy deposition (DED) processes and potential solutions-part quality and defects. Procedia Manuf. 2021;53:507-518. doi: 10.1016/j.promfg.2021.06.093
- Ribeiro KSB, Mariani FE, Coelho RT. A study of different deposition strategies in direct energy deposition (DED) processes. Procedia Manuf. 2020;48:663-670. doi: 10.1016/j.promfg.2020.05.158
- Yadollahi A, Shamsaei N, Thompson SM, Seely DW. Effects of process time interval and heat treatment on the mechanical and microstructural properties of direct laser deposited 316L stainless steel. Mater Sci Eng A. 2015;644:171-183. doi: 10.1016/j.msea.2015.07.056
- Sciammarella FM, Najafabadi BS. Processing parameter doe for 316l using directed energy deposition. J Manuf Mater Process. 2018;2(3):61. doi: 10.3390/jmmp2030061
- Mohr G, Altenburg SJ, Hilgenberg K. Effects of inter layer time and build height on resulting properties of 316L stainless steel processed by laser powder bed fusion. Addit Manuf. 2020;32:101080. doi: 10.1016/j.addma.2020.101080
- Denlinger ER, Heigel JC, Michaleris P, Palmer TA. Effect of inter-layer dwell time on distortion and residual stress in additive manufacturing of titanium and nickel alloys. J Mater Process Technol. 2015;215:123-131. doi: 10.1016/j.jmatprotec.2014.07.030
- Standard Guide for Additive Manufacturing of Metal-Finished Part Properties-Methods for Relative Density Measurement 1. Vol. 1. United States: ASTM; 2023. p. 1-6. doi: 10.1520/F3637-23.2
- He BB, Preckwinkel U, Smith KL. Stress and texture analysis with two-dimensional x-ray diffraction. Mater Sci Forum. 2002;404-407:109-114. doi: 10.4028/www.scientific.net/msf.404-407.109
- Rupert AN, McCausland PJ, Flemming RL. Ordinary chondrite shock stage quantification using in situ 2-D X-ray diffraction of olivine. Meteorit Planet Sci. 2020;55(10):2224-2240. doi: 10.1111/maps.13572
- Dzhurinskiy D, Babu A, Pathak P, Elkin A, Dautov S, Shornikov P. Microstructure and wear properties of atmospheric plasma-sprayed Cr3C2-NiCr composite coatings. Surf Coatings Technol. 2021;428:127904. doi: 10.1016/j.surfcoat.2021.127904
- Lama A, Sarvesha R, Garcia D, et al. Macroscale property assessment and indentation characteristics of thick section friction stir welded AL 5083. Mater Sci Eng A. 2023;880:145306. doi: 10.1016/j.msea.2023.145306
- Thompson A, Maskery I, Leach RK. X-ray computed tomography for additive manufacturing: A review. Meas Sci Technol. 2016;27(7):072001. doi: 10.1088/0957-0233/27/7/072001
- Zheng B, Haley JC, Yang N, et al. On the evolution of microstructure and defect control in 316L SS components fabricated via directed energy deposition. Mater Sci Eng A. 2019;764:138243. doi: 10.1016/j.msea.2019.138243
- Suwas S, Vikram RJ. Texture evolution in metallic materials during additive manufacturing: A review. Trans Indian Natl Acad Eng. 2021;6(4):991-1003. doi: 10.1007/s41403-021-00271-6
- Kim FH, Moylan SP. Literature review of metal additive manufacturing defects. In: NIST Advanced Manufacturing Series. Gaithersburg, MD: National Institute of Standards and Technology; 2018. p. 1-17. Available from: https:// nvlpubs.nist.gov/nistpubs/ams/NIST.AMS.100-16.pdf [Last accessed on 2018 May 01]
- Kruth JP, Bartscher M, Carmignato S, Schmitt R, De Chiffre L, Weckenmann A. Computed tomography for dimensional metrology. CIRP Ann. 2011;60(2):821-842. doi: 10.1016/j.cirp.2011.05.006
- Shah P, Racasan R, Bills P. Comparison of different additive manufacturing methods using computed tomography. Case Stud Nondestruct Test Eval. 2016;6:69-78. doi: 10.1016/j.csndt.2016.05.008