Enhancing interlaminar adhesion in multi-material 3D printing: A study of conductive PLA and TPU interfaces through fused filament fabrication
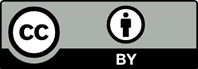
In the rapidly expanding field of additive manufacturing, multi-material fused filament fabrication represents a frontier with vast potential for creating composite structures that blend the benefits of different material properties. Interlaminar adhesion between dissimilar materials remains a challenge for the realization of multifunctional structure for practical use. This study investigates the interlaminar adhesion between conductive polylactic acid and thermoplastic polyurethane, materials representative of rigid and flexible characteristics, respectively. We present a comparative analysis of two adhesion enhancement approaches: the incorporation of mechanical interlocking features and the modification of surface roughness at the interface. Through tensile testing, we evaluate the effectiveness of these methods against a benchmark coupon with unmodified interface. Micro-computed tomography analysis, surface morphology analysis, and mechanical performance assessments elucidate the failure modes and provide insights into the interfacial behavior of these interface designs. We found that the interface design with top infill modification showed the highest interlaminar adhesion strength, with an improvement of at least 25% compared to the benchmark coupon. Our findings aim to inform the design and manufacturing practices in multi-material 3D printing and to open new avenues for the development of multifunctional, composite 3D-printed systems.
Wai Yee Yeong serves as the Editorial Board Member of the journal, but did not in any way involve in the editorial and peer-review process conducted for this paper, directly or indirectly.
- Goh GL, Agarwala S, Goh GD, et al. Additively manufactured multi-material free-form structure with printed electronics. Int J Adv Manuf Technol. 2018;94(1):1309-1316. doi: 10.1007/s00170-017-0972-z
- Goh GL, Tay MF, Lee JM, et al. Potential of printed electrodes for electrochemical impedance spectroscopy (EIS): Toward membrane fouling detection. Adv Electron Mater. 2021;7(10):2100043. doi: 10.1002/aelm.202100043
- Goh GL, Zhang H, Chong TH, Yeong WY. 3D printing of multilayered and multimaterial electronics: A review. Adv Electron Mater. 2021;7(10):2100445. doi: 10.1002/aelm.202100445
- Goh GD, Agarwala S, Goh GL, Dikshit V, Sing SL, Yeong WY. Additive manufacturing in unmanned aerial vehicles (UAVs): Challenges and potential. Aerospace Sci Technol. 2017;63:140-151. doi: 10.1016/j.ast.2016.12.019
- Soetedjo AAP, Lee JM, Lau HH, et al. Tissue engineering and 3D printing of bioartificial pancreas for regenerative medicine in diabetes. Trends Endocrinol Metab. 2021;32(8):609-622. doi: 10.1016/j.tem.2021.05.007
- Cuan-Urquizo E, Guerra Silva R. Fused filament fabrication of cellular, lattice and porous mechanical metamaterials: A review. Virtual Phys Prototyp. 2023;18(10):e2224300. doi: 10.1080/17452759.2023.2224300
- Ribeiro M, Sousa Carneiro O, Ferreira da Silva A. Interface geometries in 3D multi-material prints by fused filament fabrication. Rapid Prototyp J. 2019;25(1):38-46. doi: 10.1108/RPJ-05-2017-0107
- Englert L, Heuer A, Engelskirchen MK, et al. Hybrid material additive manufacturing: Interlocking interfaces for fused filament fabrication on laser powder bed fusion substrates. Virtual Phys Prototyp. 2022;17(3):508-527. doi: 10.1080/17452759.2022.2048228
- Brancewicz-Steinmetz E, Sawicki J, Byczkowska P. The influence of 3D printing parameters on adhesion between polylactic acid (PLA) and thermoplastic polyurethane (TPU). Materials (Basel). 2021;14(21):6464. doi: 10.3390/ma14216464
- Tamburrino F, Graziosi S, Bordegoni M. The influence of slicing parameters on the multi-material adhesion mechanisms of FDM printed parts: An exploratory study. Virtual Phys Prototyp. 2019;14(4):316-332. doi: 10.1080/17452759.2019.1607758
- Freund R, Watschke H, Heubach J, Vietor T. Determination of influencing factors on interface strength of additively manufactured multi-material parts by material extrusion. Appl Sci. 2019;9(9):1782. doi: 10.3390/app9091782
- Rodriguez C, Narahara H, Koresawa H, Hisayuki N, Akimitsu S. Enhancement of Electrically Conductive FDM Parts Adhesion Strength to Different Polymers through Atmospheric Pressure Plasma Treatment. In: Proceedings of JSPE Semestrial Meeting 2017 JSPE Spring Conference; 2017. p. 1025-1026. doi: 10.11522/pscjspe.2017S.0_1025
- Penter L, Maier J, Kauschinger B, Lebelt T, Modler N, Ihlenfeldt S. 3D Printing Technology for Low Cost Manufacturing of Hybrid Prototypes from Multi Material Composites. Berlin, Heidelberg: Springer; 2021. p. 396-405. doi: 10.1007/978-3-662-62138-7_40
- Rodriguez C, Narahara H, Koresawa H, Hisayuki N. The Effect of Atmospheric Pressure Plasma on Inter-Laminar Adhesion Strength of FDM Parts Manufactured with Different Functional Polymers. In: Proceedings of JSPE Semestrial Meeting 2019 JSPE Spring Conference; 2019. p. 519-520. doi: 10.11522/pscjspe.2019S.0_519
- Tao R, Shi J, Granier F, Moeini M, Akbarzadeh A, Therriault D. Multi-material fused filament fabrication of flexible 3D piezoelectric nanocomposite lattices for pressure sensing and energy harvesting applications. Appl Mater Today. 2022;29:101596. doi: 10.1016/j.apmt.2022.101596
- Roach DJ, Hamel CM, Dunn CK, Johnson MV, Kuang X, Qi HJ. The m4 3D printer: A multi-material multi-method additive manufacturing platform for future 3D printed structures. Addit Manuf. 2019;29:100819. doi: 10.1016/j.addma.2019.100819
- Fenollosa F, Gomà JR, Buj-Corral I, et al. Foreseeing new multi-material FFF-additive manufacturing concepts meeting mimicking requirements with living tissues. Procedia Manuf. 2019;41:1063-1070. doi: 10.1016/j.promfg.2019.10.034
- Stano G, Ovy SAI, Percoco G, Zhang R, Lu H, Tadesse Y. Additive manufacturing for bioinspired structures: Experimental study to improve the multimaterial adhesion between soft and stiff materials. 3D Print Addit Manuf. 2023;10(5):1080-1089. doi: 10.1089/3dp.2022.0186
- Goh GL, Goh GD, Nguyen VP, et al. A 3D printing-enabled artificially innervated smart soft gripper with variable joint stiffness. Adv Mater Technol. 2023;8(24):2301426. doi: 10.1002/admt.202301426
- Jiao J, Guo Y, Tong Q, et al. Stiffness-tunable and shape-locking soft actuators based on 3D-printed hybrid multi-materials. Soft Sci. 2022;2(4):20. doi: 10.20517/ss.2022.19
- Goh GL, Huang X, Toh W, et al. Joint angle prediction for a cable-driven gripper with variable joint stiffness through numerical modeling and machine learning. Int J AI Mater Des. 2024;1(1):2328. doi: 10.36922/ijamd.2328
- Awaja F, Gilbert M, Kelly G, Fox B, Pigram PJ. Adhesion of polymers. Prog Polymer Sci. 2009;34(9):948-968. doi: 10.1016/j.progpolymsci.2009.04.007
- Kwon N, Deshpande H, Hasan MK, Darnal A, Kim J. Multi-ttach: Techniques to Enhance Multi-material Attachments in Low-cost FDM 3D Printing. In: Presented at: Proceedings of the 6th Annual ACM Symposium on Computational Fabrication Virtual Event, USA; 2021. doi: 10.1145/3485114.3485116
- Kakaraparthi S, Chen N. A multi-material additive manufacturing virtual prototyping method for design to improve part strength. Int J Adv Manuf Technol. 2023;127:1-12. doi: 10.1007/s00170-023-11660-2
- Hasanov S, Gupta A, Nasirov A, Fidan I. Mechanical characterization of functionally graded materials produced by the fused filament fabrication process. J Manuf Processes. 2020;58:923-935. doi: 10.1016/j.jmapro.2020.09.011
- Mustafa I, Kwok TH. Interlacing infills for multi-material fused filament fabrication using layered depth material images. Micromachines. 2022;13(5):773. doi: 10.3390/mi13050773
- Rendas P, Figueiredo L, Geraldo M, Vidal C, Soares BA. Improvement of tensile and flexural properties of 3D printed PEEK through the increase of interfacial adhesion. J Manuf Processes. 2023;93:260-274. doi: 10.1016/j.jmapro.2023.03.024
- Rodriguez JF, Thomas JP, Renaud JE. Characterization of the mesostructure of fused‐deposition acrylonitrile‐butadiene‐styrene materials. Rapid Prototyp J. 2000;6(3):175-186. doi: 10.1108/13552540010337056
- Brancewicz-Steinmetz E, Valverde Vergara R, Buzalski V, Sawicki J. Study of the adhesion between TPU and PLA in multi-material 3D printing. J Achiev Mater Manuf Eng. 2022;115(2):49-56.
- Yin J, Lu C, Fu J, Huang Y, Zheng Y. Interfacial bonding during multi-material fused deposition modeling (FDM) process due to inter-molecular diffusion. Mater Des. 2018;150:104-112. doi: 10.1016/j.matdes.2018.04.029
- Gao X, Qi S, Kuang X, Su Y, Li J, Wang D. Fused filament fabrication of polymer materials: A review of interlayer bond. Addit Manuf. 2021;37:101658. doi: 10.1016/j.addma.2020.101658
- Cunha P, Teixeira R, Carneiro O, Silva A. Multi-material fused filament fabrication: An expedited methodology to assess the affinity between different materials. Prog Addit Manuf. 2023;8(2):195-204. doi: 10.1007/s40964-022-00322-6
- Kalia K, Ameli A. Interfacial Bond Strength of Various Rigid/ Soft Multi-Materials Printed via Fused Filament Fabrication Process. New York: American Society of Mechanical Engineers; 2020. doi: 10.1115/SMASIS2020-2298
- Vanaei HR, Raissi K, Deligant M, et al. Toward the understanding of temperature effect on bonding strength, dimensions and geometry of 3D-printed parts. J Mater Sci. 2020;55(29):14677-14689. doi: 10.1007/s10853-020-05057-9
- Srinivas V, van Hooy-Corstjens CSJ, Rastogi S, Harings JAW. Promotion of molecular diffusion and/or crystallization in fused deposition modeled poly(lactide) welds. Polymer. 2020;202:122637. doi: 10.1016/j.polymer.2020.122637
- Watschke H, Waalkes L, Schumacher C, Vietor T. Development of novel test specimens for characterization of multi-material parts manufactured by material extrusion. Appl Sci. 2018;8(8):1220. doi: 10.3390/app8081220