An exploratory study on biocompatible Ti-6Mn-4Mo alloy manufactured by directed energy deposition
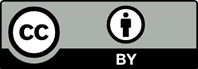
Titanium is a widely used metal in biomedical applications due to its low toxicity, but its mechanical properties need to be tailored for different applications. Efforts are called for to search for effective and yet non-toxic elements to be alloyed with Ti to improve its strength. Fitting in this category, Mn and Mo are two such alloying elements. In this study, Ti-6Mn-4Mo alloy was manufactured by laser-directed energy deposition (DED) through in situ alloying of Ti, Mn, and Mo elemental powders. This study was intended to not only demonstrate for the first time the printability of the Ti-Mn-Mo ternary system by laser DED but also investigate the basic mechanical properties and corrosion resistance of the obtained alloy. Under the as-built condition, the alloy consisted mainly of ß phase, while after heat treatment it was transformed into α phase. The average ultimate tensile strength under as-built condition was 706.0 MPa, lower than similar alloys from conventional methods. However, the average hardness reached 421.1 HV for the as-built condition, much higher than the similar alloys made through conventional methods. On the other hand, the corrosion resistance of the obtained alloy was found to be relatively low compared to similar alloys produced with traditional methods. In addition, heat treatment was not able to significantly change the tensile properties or the corrosion resistance. In essence, the exploratory study indicates that the DED-produced Ti-Mn-Mo alloy could be deposited without cracks and major voids, and shows that its high hardness and modulus are attractive to applications for high wear resistance. However, further investigation is needed to improve strength, ductility, and corrosion resistance of the alloy.
Jing Shi serves as the Editorial Board Member of the journal, but did not in any way involve in the editorial and peer-review process conducted for this paper, directly or indirectly.
- Trevisan F, Calignano F, Aversa A, et al., 2017, Additive manufacturing of titanium alloys in the biomedical field: Processes, properties and applications. J Appl Biomater Funct Mater, 16: 57–67. https://doi.org/10.5301/jabfm.5000371
- Fu W, Liu S, Jiao J, et al., 2022, Wear resistance and biocompatibility of Co-Cr dental alloys fabricated with CAST and SLM techniques. Materials, 15: 3263. https://doi.org/10.3390/ma15093263
- Niinomi M, 2002, Recent metallic materials for biomedical applications. Metallurgical Mater Trans A, 33: 477–486. https://doi.org/10.1007/s11661-002-0109-2
- Li Y, Yang C, Zhao H, et al., 2014, New developments of Ti-based alloys for biomedical applications. Materials, 7: 1709–1800. https://doi.org/10.3390/ma7031709
- Santos P, Niinomi M, Cho K, et al., 2016, Development of New Ti-Mn-Mo Alloys for Use in Biomedical Applications. In: Proceedings of the 13th World Conference on Titanium. John Wiley & Sons, Inc., pp. 1741–1745.
- Maitra V, Shi J, Lu C, 2022, Robust prediction and validation of as-built density of Ti-6Al-4V parts manufactured via selective laser melting using a machine learning approach. J Manuf Processes, 78: 183–201. https://doi.org/10.1016/j.jmapro.2022.04.020
- Kuroda D, Niinomi M, Morinaga M, et al., 1998, Design and mechanical properties of new β type titanium alloys for implant materials. Mater Sci Eng A, 243: 244–249. https://doi.org/10.1016/S0921-5093(97)00808-3
- Santos PF, Niinomi M, Cho K, et al., 2017, Effects of Mo addition on the mechanical properties and microstructures of Ti-Mn alloys fabricated by metal injection molding for biomedical applications. Mater Trans, 58: 271–279. https://doi.org/10.2320/matertrans.m2016286
- Morioka R, Cho K, Yasuda HY, 2018, Effects of Mo addition on deformation behavior of metastable beta-type Ti-Mn single crystals. Mater Sci Forum, 941: 1360–1365. https://doi.org/10.4028/www.scientific.net/MSF.941.1360
- Tanji A, Gapsari F, Syahrom A, et al., 2021, Effect of Mo addition on the pitting resistance of TiMn alloys in Hanks’ solution. J Alloys Compds, 871: 159582. https://doi.org/10.1016/j.jallcom.2021.159582
- Santos P, Niinomi M, Liu H, et al., 2016, Improvement of microstructure, mechanical and corrosion properties of biomedical Ti-Mn alloys by Mo addition. Mater Des, 110: 414–424. https://doi.org/10.1016/j.matdes.2016.07.115
- Lourenço ML, Cardoso GC, Sousa K, et al., 2020, Development of novel Ti-Mo-Mn alloys for biomedical applications. Sci Rep, 10: 6298. https://doi.org/10.1038/s41598-020-62865-4
- Maitra V, Shi J, 2023, Evaluating the predictability of surface roughness of Ti–6Al–4V alloy from selective laser melting. Adv Eng Mater, 25: 2300075. https://doi.org/10.1002/adem.202300075
- Shi J, Wang Y, 2020, Development of metal matrix composites by laser-assisted additive manufacturing technologies: A review. J Mater Sci, 55: 9883–9917. https://doi.org/10.1007/s10853-020-04730-3
- Savinov R, Wang Y, Shi J, 2020, Microstructure and properties of CeO2-doped CoCrFeMnNi high entropy alloy fabricated by laser metal deposition. J Manuf Processes, 56: 1245–1251. https://doi.org/10.1016/j.jmapro.2020.04.018
- Wang J, Wang Y, Su Y, et al., 2022, Evaluation of in-situ alloyed Inconel 625 from elemental powders by laser directed energy deposition. Mater Sci Eng A, 830: 142296. https://doi.org/10.1016/j.msea.2021.142296
- Kosec T, Bajt Leban M, Ovsenik M, et al., 2022, Estimation of the corrosion properties for titanium dental alloys produced by SLM. Mater Technol, 56: 429–435. https://doi.org/10.17222/mit.2022.519
- Suresh S, Sun CN, Tekumalla S, et al., 2021, Mechanical properties and in vitro cytocompatibility of dense and porous Ti–6Al–4V ELI manufactured by selective laser melting technology for biomedical applications. J Mech Behav Biomed Mater, 123: 104712. https://doi.org/10.1016/j.jmbbm.2021.104712
- Wang N, Dheen ST, Fuh JYH, et al., 2022, Biocompatibility and mechanical properties evaluation of Ti-6Al-4V lattice structures with varying porosities. Key Eng Mater, 923: 21–29. https://doi.org/10.4028/p-64o0e4
- Tseng SF, Wang IH, Chang CM, et al., 2022, Mechanical characteristic comparison of additively manufactured Ti-6Al-4V lattice structures in biocompatible bone tissue growth. Mater Sci Eng A, 857: 144045. https://doi.org/10.1016/j.msea.2022.144045
- Zadeh MK, Yeganeh M, Shoushtari MT, et al., 2022, Microstructure, corrosion behavior, and biocompatibility of Ti-6Al-4 V alloy fabricated by LPBF and EBM techniques. Mater Today Commun, 31: 103502. https://doi.org/10.1016/j.mtcomm.2022.103502
- Xiang S, Yuan Y, Zhang C, et al., 2022, Effects of process parameters on the corrosion resistance and biocompatibility of Ti6Al4V parts fabricated by selective laser melting. ACS Omega, 7: 5954–5961. https://doi.org/10.1021/acsomega.1c06246
- Vonavkova I, Vojtech D, Palousek D, 2020, Characterization of β-Ti alloy prepared by SLM method. Manuf Technol, 20: 690–696. https://doi.org/10.21062/mft.2020.091
- Zhao D, Han C, Li J, et al., 2020, In situ fabrication of a titanium-niobium alloy with tailored microstructures, enhanced mechanical properties and biocompatibility by using selective laser melting. Mater Sci Eng C, 111: 110784. https://doi.org/10.1016/j.msec.2020.110784
- Lu HZ, Ma HW, Luo X, et al., 2021, Microstructure, shape memory properties, and in vitro biocompatibility of porous NiTi scaffolds fabricated via selective laser melting. J Mater Res Technol, 15: 6797–6812. https://doi.org/10.1016/j.jmrt.2021.11.112
- Batalha RL, Batalha WC, Deng L, et al., 2020, Processing a biocompatible Ti–35Nb–7Zr–5Ta alloy by selective laser melting. J Mater Res, 35: 1143–1153. https://doi.org/10.1557/jmr.2020.90
- Ishimoto T, Ozasa R, Nakano K, et al., 2021, Development of TiNbTaZrMo bio-high entropy alloy (BioHEA) super-solid solution by selective laser melting, and its improved mechanical property and biocompatibility. Scr Mater, 194: 113658. https://doi.org/10.1016/j.scriptamat.2020.113658
- Luo JP, Huang YJ, Xu JY, et al., 2020, Additively manufactured biomedical Ti-Nb-Ta-Zr lattices with tunable Young’s modulus: Mechanical property, biocompatibility, and proteomics analysis. Mater Sci Eng C Mater Biol Appl, 114: 110903. https://doi.org/10.1016/j.msec.2020.110903
- Chakkravarthy V, Jose SP, Lakshmanan M, et al., 2022, Additive manufacturing of novel Ti-30Nb-2Zr biomimetic scaffolds for successful limb salvage. Mater Today Proc, 64: 1711–1716. https://doi.org/10.1016/j.matpr.2022.05.469
- Challis VJ, Xu X, Halfpenny A, et al., 2023, Understanding the effect of microstructural texture on the anisotropic elastic properties of selective laser melted Ti-24Nb-4Zr-8Sn. Acta Mater, 254: 119021. https://doi.org/10.1016/j.actamat.2023.119021
- Wolff S, Lee T, Faierson E, et al., 2016, Anisotropic properties of directed energy deposition (DED)-processed Ti–6Al–4V. J Manuf Processes, 24: 397–405. https://doi.org/10.1016/j.jmapro.2016.06.020
- Ivanov S, Gushchina M, Artinov A, et al., 2021, Effect of elevated temperatures on the mechanical properties of a direct laser deposited Ti-6Al-4V. Materials, 14: 6432. https://doi.org/10.3390/ma14216432
- Tan H, Guo M, Clare AT, et al., 2019, Microstructure and properties of Ti-6Al-4V fabricated by low-power pulsed laser directed energy deposition. J Mater Sci Technol, 35: 2027–2037. https://doi.org/10.1016/j.jmst.2019.05.008
- Shalnova SA, Gushchina MO, Strekalovskaya DA, et al., 2022, Electrochemical properties of the heat-treated Ti-6Al-4V alloy manufactured by direct energy deposition. J Alloys Compds, 899: 163226. https://doi.org/10.1016/j.jallcom.2021.163226
- Gong X, Yabansu YC, Collins PC, et al., 2020, Evaluation of Ti-Mn alloys for additive manufacturing using high-throughput experimental assays and Gaussian process regression. Materials (Basel), 13: 4641. https://doi.org/10.3390/ma13204641
- Yang R, Liu Z, Yang G, et al., 2012, Study of the Ti-20 wt. % Mo composite coating prepared by laser cladding. Procedia Eng, 36: 355–359. https://doi.org/10.1016/j.proeng.2012.03.052
- Kang N, Lin X, Mansori ME, et al., 2020, On the effect of the thermal cycle during the directed energy deposition application to the in-situ production of a Ti-Mo alloy functionally graded structure. Addit Manuf, 31: 100911. https://doi.org/10.1016/j.addma.2019.100911
- Zhan H, Ceguerra AV, Wang G, et al., 2018, Precipitation of string-shaped morphologies consisting of aligned α phase in a metastable β titanium alloy. Sci Rep, 8: 2038. https://doi.org/10.1038/s41598-018-20386-1
- Wang CH, Liu M, Hu P, et al., 2017, The effects of α″ and ω phases on the superelasticity and shape memory effect of binary Ti-Mo alloys. J Alloys Compd, 720: 488–496. https://doi.org/10.1016/j.jallcom.2017.05.299
- Alshammari Y, Yang F, Bolzoni L, 2019, Mechanical properties and microstructure of Ti-Mn alloys produced via powder metallurgy for biomedical applications. J Mech Behav Biomed Mater, 91: 391–397. https://doi.org/10.1016/j.jmbbm.2018.12.005
- Salahinejad E, Hadianfard MJ, Macdonald DD, et al., 2013, In vitro electrochemical corrosion and cell viability studies on nickel-free stainless steel orthopedic implants. PLoS One, 8: e61633. https://doi.org/10.1371/journal.pone.0061633
- Savinov R, Wang Y, Shi J, 2023, Evaluation of microstructure, mechanical properties, and corrosion resistance for Ti-doped inconel 625 alloy produced by laser directed energy deposition. Mater Sci Eng A, 884: 145542. https://doi.org/10.1016/j.msea.2023.145542
- Chandramohan P, Bhero S, Obadele BA, et al., 2017, Laser additive manufactured Ti-6Al-4V alloy: Tribology and corrosion studies. Int J Adv Manuf Technol, 92: 3051–3061. https://doi.org/10.1007/s00170-017-0410-2
- Zhou X, Xu D, Geng S, et al., 2021, Mechanical properties, corrosion behavior and cytotoxicity of Ti-6Al-4V alloy fabricated by laser metal deposition. Mater Characterization, 179: 111302. https://doi.org/10.1016/j.matchar.2021.111302
- Coakley JA, Vorontsov VA, Jones N, et al., 2015, Precipitation processes in the Beta-Titanium alloy Ti-5Al-5Mo-5V-3Cr. J Alloys Compd, 646: 946–953. https://doi.org/10.1016/j.jallcom.2015.05.251
- Kao YH, Tu GC, Huang CA, et al., 2005, A study on the hardness variation of α- and β-pure titanium with different grain sizes. Mater Sci Eng A, 398: 93–98. https://doi.org/10.1016/j.msea.2005.03.004
- Jadhav S, Powar A, Patil S, et al., 2017, Effect of volume fraction of alpha and transformed beta on the high cycle fatigue properties of bimodal Ti6Al4V alloy. IOP Conf Ser, 201: 012035. https://doi.org/10.1088/1757-899x/201/1/012035
- Iijima Y, Nagase T, Matsugaki A, et al., 2021, Design and development of Ti-Zr-Hf-Nb-Ta-Mo high-entropy alloys for metallic biomaterials. Mater Des, 202: 109548. https://doi.org/10.1016/j.matdes.2021.109548