An experimental study on 3D-printed continuous fiber-reinforced composite auxetic structures
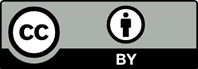
Auxetic structures have negative Poisson’s ratios (NPR). Due to the unique deformation mechanism, auxetic structures possess extraordinary mechanical properties, such as indentation resistance, shear resistance, fracture toughness, and energy absorption capability. However, the stiffness and load-bearing capacity are the weak points for auxetic structures. 3D printing of continuous fiber-reinforced composite enables the fabrication of lightweight and highly stiff complex structures, providing a perfect manufacturing method to remedy the shortcomings of auxetic structures. This work investigated the mechanical properties of 3D-printed continuous fiber-reinforced composite auxetic structures. In this study, we utilized continuous fiber-reinforced composite 3D printing to fabricate two types of auxetic structures. The fiber path configurations were varied among the test specimens to explore the effect of fiber distribution on mechanical properties. A uniaxial tensile test was performed to evaluate the tensile properties and Poisson’s ratio of continuous fiber-reinforced composite auxetic structures. Results showed that the tensile modulus and strength have been dramatically improved with a minor mass increase. The auxetic behavior can be strengthened by properly allocating the reinforcing fibers. However, the addition of continuous fiber led to different performances on the selected auxetic structures. In summary, two out of the five specimens demonstrated simultaneous improvements in stiffness, strength, and auxeticity across the conducted tests.
Jikai Liu serves as the Editorial Board Member of the journal, but did not in any way involve in the editorial and peer-review process conducted for this paper, directly or indirectly.
- Sanami M, Ravirala N, Alderson K, et al., 2014, Auxetic materials for sports applications. Procedia Eng, 72: 453–458. https://doi.org/10.1016/j.proeng.2014.06.079
- Choi JB, Lakes RS, 1995, Nonlinear analysis of the poissons ratio of negative poissons ratio foams. J Compos Mater, 29: 113–128. https://doi.org/10.1177/002199839502900106
- Lakes R, 1987, Foam structures with a negative poisson’s ratio. Science, 235: 1038–1040. https://doi.org/10.1126/science.235.4792.1038
- Donoghue JP, Alderson KL, Evans KE, 2009, The fracture toughness of composite laminates with a negative Poisson’s ratio. Phys Status Solidi, 246: 2011–2017. https://doi.org/10.1002/pssb.200982031
- Zhang XG, Ren X, Jiang W, et al., 2022, A novel auxetic chiral lattice composite: Experimental and numerical study. Compos Struct, 282: 115043. https://doi.org/10.1016/j.compstruct.2021.115043
- Wang Z, Zulifqar A, Hu H, 2016, Auxetic composites in aerospace engineering. In: Advanced Composite Materials for Aerospace Engineering. Netherlands: Elsevier, pp. 213–240. https://doi.org/10.1016/B978-0-08-100037-3.00007-9
- Bhullar SK, 2013, Influence of negative poisson’s ratio on stent applications. Adv Mater, 2: 42. https://doi.org/10.11648/j.am.20130203.14
- Saxena KK, Das R, Calius EP, 2016, Three decades of auxetics research - materials with negative poisson’s ratio: A review. Adv Eng Mater, 18: 1847–1870. https://doi.org/10.1002/adem.201600053
- Novak N, Vesenjak M, Ren Z, 2016, Auxetic cellular materials - a review. Strojniški Vestn J Mech Eng, 62: 485–493. https://doi.org/10.5545/sv-jme.2016.3656
- Pissarenko A, Yang W, Quan H, et al., 2019, Tensile behavior and structural characterization of pig dermis. Acta Biomater, 86: 77–95. https://doi.org/10.1016/j.actbio.2019.01.023
- Balan PM, Mertens AJ, Bahubalendruni MVAR, 2023, Auxetic mechanical metamaterials and their futuristic developments: A state-of-art review. Mater Today Commun, 34: 105285. https://doi.org/10.1016/j.mtcomm.2022.105285
- Kolken HMA, Zadpoor AA, 2017, Auxetic mechanical metamaterials. RSC Adv, 7: 5111–5129. https://doi.org/10.1039/C6RA27333E
- Jin Y, Xie C, Gao Q, et al., 2021, Fabrication of multi-scale and tunable auxetic scaffolds for tissue engineering. Mater Des, 197: 109277. https://doi.org/10.1016/j.matdes.2020.109277
- Zheng X, Guo X, Watanabe I, 2021, A mathematically defined 3D auxetic metamaterial with tunable mechanical and conduction properties. Mater Des, 198: 109313. https://doi.org/10.1016/j.matdes.2020.109313
- Fozdar DY, Soman P, Lee JW, et al., 2011, Three‐dimensional polymer constructs exhibiting a tunable negative poisson’s ratio. Adv Funct Mater, 21: 2712–2720. https://doi.org/10.1002/adfm.201002022
- Xue Y, Wang W, Han F, 2019, Enhanced compressive mechanical properties of aluminum based auxetic lattice structures filled with polymers. Compos B Eng, 171: 183–191. https://doi.org/10.1016/j.compositesb.2019.05.002
- Hu C, Dong J, Luo J, et al., 2020, 3D printing of chiral carbon fiber reinforced polylactic acid composites with negative Poisson’s ratios. Compos B Eng, 201: 108400. https://doi.org/10.1016/j.compositesb.2020.108400
- Tian X, Todoroki A, Liu T, et al., 2022, 3D printing of continuous fiber reinforced polymer composites: Development, application, and prospective. Chin J Mech Eng Addit Manuf Front, 1: 100016. https://doi.org/10.1016/j.cjmeam.2022.100016
- Cheng P, Peng Y, Li S, et al., 2023, 3D printed continuous fiber reinforced composite lightweight structures: A review and outlook. Compos B Eng, 250: 110450. https://doi.org/10.1016/j.compositesb.2022.110450
- van de Werken N, Tekinalp H, Khanbolouki P, et al., 2020, Additively manufactured carbon fiber-reinforced composites: State of the art and perspective. Addit Manuf, 31: 100962. https://doi.org/10.1016/j.addma.2019.100962
- Hou Z, Tian X, Zhang J, et al., 2018, 3D printed continuous fibre reinforced composite corrugated structure. Compos Struct, 184: 1005–1010. https://doi.org/10.1016/j.compstruct.2017.10.080
- Sugiyama K, Matsuzaki R, Ueda M, et al., 2018, 3D printing of composite sandwich structures using continuous carbon fiber and fiber tension. Compos A Appl Sci Manuf, 113: 114–121. https://doi.org/10.1016/j.compositesa.2018.07.029
- Liu P, Lu L, Liu J, 2023, Path-driven shell lattices designed for continuous fiber composite 3D printing. Addit Manuf, 78: 103838. https://doi.org/10.1016/j.addma.2023.103838
- Luan C, Yao X, Zhang C, et al., 2019, Large-scale deformation and damage detection of 3D printed continuous carbon fiber reinforced polymer-matrix composite structures. Compos Struct, 212: 552–560. https://doi.org/10.1016/j.compstruct.2019.01.064
- Cheng Y, Li J, Qian X, et al., 2021, 3D printed recoverable honeycomb composites reinforced by continuous carbon fibers. Compos Struct, 268: 113974. https://doi.org/10.1016/j.compstruct.2021.113974
- Dong K, Ke H, Panahi-Sarmad M, et al., 2021, Mechanical properties and shape memory effect of 4D printed cellular structure composite with a novel continuous fiber-reinforced printing path. Mater Des, 198: 109303. https://doi.org/10.1016/j.matdes.2020.109303
- Yin L, Tian X, Shang Z, et al., 2019, Characterizations of continuous carbon fiber-reinforced composites for electromagnetic interference shielding fabricated by 3D printing. Appl Phys A, 125: 266. https://doi.org/10.1007/s00339-019-2566-0
- Dong K, Wang Y, Wang Z, et al., 2023, Reusability and energy absorption behavior of 4D printed continuous fiber-reinforced auxetic composite structures. Compos A Appl Sci Manuf, 169: 107529. https://doi.org/10.1016/j.compositesa.2023.107529
- Quan C, Han B, Hou Z, et al., 2020, 3d printed continuous fiber reinforced composite auxetic honeycomb structures. Compos B Eng, 187: 107858. https://doi.org/10.1016/j.compositesb.2020.107858
- Xue X, Lin C, Wu F, et al., 2023, Lattice structures with negative Poisson’s ratio: A review. Mater Today Commun, 34: 105132. https://doi.org/10.1016/j.mtcomm.2022.105132
- Larsen UD, Sigmund O, Bouwstra S, 1997, Design and fabrication of compliant micromechanisms and structures with negative poisson’s ratio. J Microelectromechanical Syst, 6: 99–106.
- Antonov F, 2015, Anisoprint. Available from: https:// anisoprint.com [Last accessed on 2023 Sep 30].
- Zhang H, Chen J, Yang D, 2021, Fibre misalignment and breakage in 3D printing of continuous carbon fibre reinforced thermoplastic composites. Addit Manuf, 38: 101775. https://doi.org/10.1016/j.addma.2020.101775