Base shape generation and optimization for multi-axis hybrid additive manufacturing
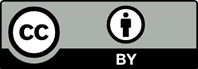
Hybrid additive manufacturing (HAM) processes combine the advantages of both additive and non-AM processing to achieve an improvement on quality, cost, and a good quality-cost balance. The non-additive manufacturing process is able to build the physical component of a computer-aided design model from zero or an existing relatively simple subvolume, called base shape in this paper. Hence, if the processing start point is an existing subvolume, how to determine an optimal base shape to save printing time, avoid manufacturing constraints and ensure component quality is an open question in the process planning. Nevertheless, this topic has rarely been investigated. Therefore, in this paper, we propose an optimization method using model skeleton-based decomposition and evolutionary computation. A set of generic evaluation criteria are defined for alternative evaluation. We also present two case studies in this paper for validating the proposed method and conclude that sequential HAM processes have a wide application potential.
- Wohlers TT, Wohlers Associates, Campbell I, et al., 2020, Wohlers Report 2020: 3D Printing and Additive Manufacturing State of the Industry. United States: Wohlers Associates.
- Zhang Y, Wang Z, Zhang Y, et al., 2020, Bio-inspired generative design for support structure generation and optimization in additive manufacturing (AM). CIRP Ann, 69: 117–120. https://doi.org/10.1016/j.cirp.2020.04.091
- Esmaeilian B, Behdad S, Wang B, 2016, The evolution and future of manufacturing: A review. J Manuf Syst, 39: 79–100. https://doi.org/10.1016/j.jmsy.2016.03.001
- Gao W, Zhang Y, Ramanujan D, et al., 2015, The status, challenges, and future of additive manufacturing in engineering. Comput Aided Des, 69: 65–89. https://doi.org/10.1016/j.cad.2015.04.001
- Vayre B, Vignat F, Villeneuve F, 2012, Metallic additive manufacturing: State-of-the-art review and prospects. Mech Ind, 13: 89–96. https://doi.org/10.1051/meca/2012003
- Le VT, Paris H, Mandil G, 2017, Process planning for combined additive and subtractive manufacturing technologies in a remanufacturing context. J Manuf Syst, 44: 243–254. https://doi.org/10.1016/j.jmsy.2017.06.003
- Ramaswami K, 1997, Process Planning for Shape Deposition Manufacturing. [Doctoral dissertation]. Stanford, CA: Stanford University.
- Flynn JM, Shokrani A, Newman ST, et al., 2016, Hybrid additive and subtractive machine tools-research and industrial developments. Int J Mach Tools Manuf, 101: 79–101. https://doi.org/10.1016/j.ijmachtools.2015.11.007
- Zhu Z, Dhokia VG, Nassehi A, et al., 2013, A review of hybrid manufacturing processes -state of the art and future perspectives. Int J Comput Integr Manuf, 26: 596–615. https://doi.org/10.1080/0951192x.2012.749530
- Sealy MP, Madireddy G, Williams RE, et al., 2018, Hybrid processes in additive manufacturing. J Manuf Sci Eng, 140: 060801. https://doi.org/10.1115/1.4038644
- Kickelbick G, 2006, Introduction to hybrid materials. In: Hybrid Materials: Synthesis, Characterization, and Applications. Hoboken: Wiley.
- Lauwers B, Klocke F, Klink A, et al., 2014, Hybrid processes in manufacturing. CIRP Ann, 63: 561–583. https://doi.org/10.1016/j.cirp.2014.05.003
- Nassehi, A., Newman, S., Dhokia, V, et al., 2011, Using formal methods to model hybrid manufacturing processes. In: Enabling Manufacturing Competitiveness and Economic Sustainability. Berlin, Heidelberg: Springer.
- Ham I, Lu SC, 1988, Computer-aided process planning: The present and the future. CIRP Ann, 37: 591–601. https://doi.org/10.1016/s0007-8506(07)60756-2
- Zhang Y, Bernard A, 2018, A KBE CAPP framework for qualified additive manufacturing. CIRP Ann, 67: 467–470. https://doi.org/10.1016/j.cirp.2018.04.045
- Kulkarni P, Marsan A, Dutta D, 2000, A review of process planning techniques in layered manufacturing. Rapid Prototyp J, 6: 18–35. https://doi.org/10.1108/13552540010309859
- Zhang Y, Bernard A, 2014, AM Feature and Knowledge Based Process Planning for Additive Manufacturing in Multiple Parts Production Context. In: Proceedings of 25th Annual International Solid Freeform Fabrication Symposium.
- Zhang Y, Bernard A, 2014, An integrated decision-making model for multi-attributes decision-making (MADM) problems in additive manufacturing process planning. Rapid Prototyp J, 20: 377–389. https://doi.org/10.1108/rpj-01-2013-0009
- Zhang Y, Bernard A, Gupta RK, et al., 2014, Evaluating the design for additive manufacturing: A process planning perspective. Procedia CIRP, 21: 144–150. https://doi.org/10.1016/j.procir.2014.03.179
- Zhang Y, Bernard A, Harik R, et al., 2015, Build orientation optimization for multi-part production in additive manufacturing. J Intell Manuf, 28: 1393–1407. https://doi.org/10.1007/s10845-015-1057-1
- Hussein A, Hao L, Yan C, et al., 2013, Advanced lattice support structures for metal additive manufacturing. J Mater Process Technol, 213: 1019–1026. https://doi.org/10.1016/j.jmatprotec.2013.01.020
- Byun HS, Lee KH, 2005, Determination of optimal build direction in rapid prototyping with variable slicing. Int J Adv Manuf Technol, 28: 307–313. https://doi.org/10.1007/s00170-004-2355-5
- Ruan J, Eiamsa-Ard K, Liou FW, 2005, Automatic process planning and toolpath generation of a multiaxis hybrid manufacturing system. J Manuf Process, 7: 57–68. https://doi.org/10.1016/s1526-6125(05)70082-7
- Zhang Y, Bernard A, 2014, Grouping parts for multiple parts production in additive manufacturing. Procedia CIRP, 17: 308–313. https://doi.org/10.1016/j.procir.2014.01.096
- Zhang Y, Gupta RK, Bernard A, 2016, Two-dimensional placement optimization for multi-parts production in additive manufacturing. Robot Comput Integr Manuf, 38: 102–117. https://doi.org/10.1016/j.rcim.2015.11.003
- Zhang Y, Bernard A, Harik R, et al., 2018, A new method for single-layer-part nesting in additive manufacturing. Rapid Prototyp J, 24: 840–854. https://doi.org/10.1108/rpj-01-2017-0008
- Akula S, Karunakaran KP, 2006, Hybrid adaptive layer manufacturing: An intelligent art of direct metal rapid tooling process. Robot Comput Integr Manuf, 22: 113–123. https://doi.org/10.1016/j.rcim.2005.02.006
- Karunakaran KP, Suryakumar S, Pushpa V, et al., 2009, Retrofitment of a CNC machine for hybrid layered manufacturing. Int J Adv Manuf Technol, 45: 690–703. https://doi.org/10.1007/s00170-009-2002-2
- Ren L, Sparks T, Ruan J, et al., 2010, Integrated process planning for a multiaxis hybrid manufacturing system. J Manuf Sci Eng, 132(2):021006. https://doi.org/10.1115/1.4001122
- Liou F, Slattery K, Kinsella M, et al., 2007, Applications of a hybrid manufacturing process for fabrication of metallic structures. Rapid Prototyp J, 13: 236–244. https://doi.org/10.1108/13552540710776188
- Kerbrat O, Mognol P, Hascoet JY, 2010, Manufacturing complexity evaluation at the design stage for both machining and layered manufacturing. CIRP J Manuf Sci Technol, 2: 208–215. https://doi.org/10.1016/j.cirpj.2010.03.007
- Newman ST, Zhu Z, Dhokia V, et al., 2015, Process planning for additive and subtractive manufacturing technologies. CIRP Ann, 64: 467–470. https://doi.org/10.1016/j.cirp.2015.04.109
- Zhu Z, Dhokia V, Newman ST, 2014, A novel decision-making logic for hybrid manufacture of prismatic components based on existing parts. J Intell Manuf, 28: 131–148. https://doi.org/10.1007/s10845-014-0966-8
- Rossi A, Lanzetta M, 2020, Integration of hybrid additive/ subtractive manufacturing planning and scheduling by metaheuristics. Comput Ind Eng, 144: 106428. https://doi.org/10.1016/j.cie.2020.106428
- Xiao X, Joshi S, 2020, Process planning for five-axis support free additive manufacturing. Addit Manuf, 36: 101569. https://doi.org/10.1016/j.addma.2020.101569
- Leite M, Cunha J, Sardinha M, et al., 2018, Tool path generation for hybrid additive manufacturing. In: Proceedings of the 29th Annual International Solid Freeform Fabrication Symposium-an Additive Manufacturing Conference.
- Chen L, Lau TY, Tang K, 2020, Manufacturability analysis and process planning for additive and subtractive hybrid manufacturing of Quasi-rotational parts with columnar features. Comput Aided Des, 118: 102759. https://doi.org/10.1016/j.cad.2019.102759
- Dewitte LN, Saldana CJ, Feldhausen TA, et al., 2020, Initial Process Planning of a Hybrid Multi-Tasking Platform. In: ASME 2020 15th International Manufacturing Science and Engineering Conference.
- Liu B, Shen H, Deng R, et al., 2020, Research on a planning method for switching moments in hybrid manufacturing processes. J Manuf Process, 56: 786–795. https://doi.org/10.1016/j.jmapro.2020.05.039
- Zheng Y, Ahmad R, 2020, Feature extraction and process planning of integrated hybrid additive-subtractive system for remanufacturing. Math Biosci Eng, 17: 7274–7301. https://doi.org/10.3934/mbe.2020373
- Eldakroury MA, Chen N, Frank MC, 2018, A new method for locating candidate substrates for multi axis hybrid manufacturing systems. Rapid Prototyp J, 24: 237–248. https://doi.org/10.1108/rpj-12-2016-0213
- Chen N, Frank M, 2019, Process planning for hybrid additive and subtractive manufacturing to integrate machining and directed energy deposition. Procedia Manuf, 34: 205–213. https://doi.org/10.1016/j.promfg.2019.06.140
- Reichler AK, Gerbers R, Falkenberg P, et al., 2019, Incremental manufacturing: Model-based part design and process planning for hybrid manufacturing of multi-material parts. Procedia CIRP, 79: 107–112. https://doi.org/10.1016/j.procir.2019.02.020
- Patil S, Ravi B, 2005, Voxel-based representation, display and thickness analysis of intricate shapes. In: Ninth International Conference on Computer Aided Design and Computer Graphics (CAD-CG’05), Hong Kong, China: IEEE.
- Lee TC, Kashyap RL, Chu CN, 1994, Building skeleton models via 3-D medial surface axis thinning algorithms. CVGIP Graph Models Image Process, 56: 462–478. https://doi.org/10.1006/cgip.1994.1042
- Schmitt LM, 2001, Theory of genetic algorithms. Theor Comput Sci, 259: 1-61. https://doi.org/10.1016/S0304-3975(00)00406-0
- Cichocka JM, Migalska A, Browne WN, et al., 2017, SILVEREYE-the Implementation of particle swarm optimization algorithm in a design optimization tool. In: Computer-Aided Architectural Design. Future Trajectories. Singapore: Springer. p. 151–169.
- Lynch ME, Gu W, El-Wardany T, et al., 2013, Design and topology/shape structural optimisation for additively manufactured cold sprayed components. Virtual Phys Prototyp, 8: 213–231. https://doi.org/10.1080/17452759.2013.837629