Emerging 3D-printed zeolitic gas adsorbents
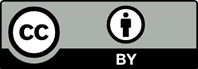
The development of zeolitic adsorbents is an essential subject of interest in the realm of green chemistry, especially in the aspect of gas adsorption. The intrinsic molecular sieving capacity of zeolites allows them to be widely adopted as effective gas adsorbents. As a layer-by-layer deposition technology, three-dimensional (3D) printing can achieve more complex zeolitic gas adsorbent structures than conventional manufacturing methods by offering flexible freeform construction and controllable 3D structural design. This review article focuses on the recent development of 3D-printed zeolitic gas adsorbents, which integrate advanced zeolitic structures and emerging additive manufacturing technologies for gas absorption. A description of zeolites and their conventional fabrication methods is given for a basic understanding of zeolitic gas adsorbents. 3D printing technologies are also introduced and discussed for the fabrication of zeolitic adsorbents such as monoliths. Next, the recent progress in the fabrication of zeolitic gas adsorbents using 3D printing is illustrated and summarized, which boosts the application of 3D-printed zeolite absorbents in different fields of gas adsorption. Conclusions are given with an outlook on opportunities ahead for future research. It is expected that the development of advanced zeolitic materials and structures for gas adsorption purposes will be significantly accelerated through 3D printing technologies.
Sharon Mui Ling Nai serves as the Editorial Board Member of the journal, but did not in any way involve in the editorial and peer-review process conducted for this paper, directly or indirectly.
- Anastas P, Eghbali N, 2010, Green chemistry: Principles and practice. Chem Soc Rev, 39: 301–312. https://doi.org/10.1039/B918763B
- Li Y, Li L, Yu J, 2017, Applications of zeolites in sustainable chemistry. Chem, 3: 928–949. https://doi.org/10.1016/j.chempr.2017.10.009
- Min BK, Friend CM, 2007, Heterogeneous gold-based catalysis for green chemistry: Low-temperature CO oxidation and propene oxidation. Chem Rev, 107: 2709–2724. https://doi.org/10.1021/cr050954d
- Yue X, Ma NL, Sonne C, et al., 2021, Mitigation of indoor air pollution: A review of recent advances in adsorption materials and catalytic oxidation. J Hazard Mater, 405: 124138. https://doi.org/10.1016/j.jhazmat.2020.124138
- Zeng H, Qu X, Xu D, et al., 2022, Porous adsorption materials for carbon dioxide capture in Industrial flue gas. Front Chem, 10: 939701.
- Zagho MM, Hassan MK, Khraisheh M, et al., 2021, A review on recent advances in CO2 separation using zeolite and zeolite-like materials as adsorbents and fillers in mixed matrix membranes (MMMs). Chem Eng J Adv, 6: 100091.
- Dyer A, 1988, An Introduction to Zeolite Molecular Sieves. New York, United States: John Wiley and Sons Inc. Available from: https://www.osti.gov/biblio/5362126 [Last accessed on 2023 Sep 21].
- Ozin GA, Kuperman A, Stein A, 1989, Advanced zeolite, materials science. Angew Chem Int Ed, 28: 359–376. https://doi.org/10.1002/anie.198903591
- Busca G, (eds), 2014, Zeolites and other structurally microporous solids as acid-base materials. In: Heterogeneous Catalytic Materials. Ch. 7. Amsterdam: Elsevier, p.197–249. Available from: https://www.sciencedirect.com/science/ article/pii/B9780444595249000079 [Last accessed on 2023 Sep 21].
- Sherman JD, 1999, Synthetic zeolites and other microporous oxide molecular sieves. Proc Natl Acad Sci, 96: 3471–3478. https://doi.org/10.1073/pnas.96.7.3471
- Combariza AF, Sastre G, 2011, Influence of zeolite surface in the sorption of methane from molecular dynamics. J Phys Chem C, 115: 13751–13758. https://doi.org/10.1021/jp202043t
- Oheix E, Reicher C, Nouali H, et al., 2022, Rational design and characterisation of novel mono- and bimetallic antibacterial Linde type A zeolite materials. J Funct Biomater, 13: 73. https://doi.org/10.3390/jfb13020073
- Praipipat P, Ngamsurach P, Roopkhan N, 2023, Zeolite A powder and beads from sugarcane bagasse fly ash modified with iron(III) oxide-hydroxide for lead adsorption. Sci Rep, 13: 1873. https://doi.org/10.1038/s41598-023-29055-4
- Bingre R, Louis B, Nguyen P, 2018, An overview on zeolite shaping technology and solutions to overcome diffusion limitations. Catalysts, 8: 163. https://doi.org/10.3390/catal8040163
- Coronas J, 2010, Present and future synthesis challenges for zeolites. Chem Eng J, 156: 236–242.
- Williams JL, 2001, Monolith structures, materials, properties and uses. Catal Today, 69: 3–9.
- Halevi O, Chen TY, Lee PS, et al., 2020, Nuclear wastewater decontamination by 3D-printed hierarchical zeolite monoliths. RSC Adv, 10: 5766–5776. https://doi.org/10.1039/C9RA09967K
- Hawaldar NH, 2018, Slurry Preparation of Zeolite and Metal-organic Framework for Extrusion Based 3D-printing. United States: Purdue University. Available from: https:// docs.lib.purdue.edu/dissertations/AAI10809712 [Last accessed 2023 Sep 21].
- Chua CK, Leong KF, 2016, 3D Printing and Additive Manufacturing. Singapore: World Scientific. https://doi.org/10.1142/10200
- Comroe ML, Kolasinski KW, Saha D, 2022, Direct ink 3D printing of porous carbon monoliths for gas separations. Molecules, 27: 5653. https://doi.org/10.3390/molecules27175653
- Middelkoop V, Coenen K, Schalck J, et al., 2019, 3D printed versus spherical adsorbents for gas sweetening. Chem Eng J, 357: 309–319.
- Toh WQ, Wang P, Tan X, et al., 2016, Microstructure and wear properties of electron beam melted Ti-6Al-4V parts: A comparison study against as-cast form. Metals, 6: 284. https://doi.org/10.3390/met6110284
- Zhu ZG, Nguyen QB, Ng FL, et al., 2018, Hierarchical microstructure and strengthening mechanisms of a CoCrFeNiMn high entropy alloy additively manufactured by selective laser melting. Scr Mater, 154: 20–24.
- Hon KKB, Li L, Hutchings IM, 2008, Direct writing technology-advances and developments. CIRP Ann Manuf Technol, 57: 601–620.
- Thakkar H, Eastman S, Al-Naddaf Q, et al., 2017, 3D-printed metal-organic framework monoliths for gas adsorption processes. ACS Appl Mater Interfaces, 9: 35908–35916. https://doi.org/10.1021/acsami.7b11626
- Yuan S, Bai J, Chua CK, et al., 2016, Material evaluation and process optimization of CNT-coated polymer powders for selective laser sintering. Polymers (Basel), 8: 370. https://doi.org/10.3390/polym8100370
- Wang S, Bai P, Sun M, et al., 2019, Fabricating mechanically robust binder-free structured zeolites by 3D printing coupled with zeolite soldering: A superior configuration for CO2 capture. Adv Sci (Weinh), 6: 1901317. https://doi.org/10.1002/advs.201901317
- Nadagouda MN, Ginn M, Rastogi V, 2020, A review of 3D printing techniques for environmental applications. Curr Opin Chem Eng, 28: 173–178.
- Hubesch R, Mazur M, Föger K, et al., 2021, Zeolites on 3D-printed open metal framework structure: Metal migration into zeolite promoted catalytic cracking of endothermic fuels for flight vehicles. Chem Commun, 57: 9586–9589. https://doi.org/10.1039/D1CC04246G
- Low ZX, Chua YT, Ray BM, et al., 2017, Perspective on 3D printing of separation membranes and comparison to related unconventional fabrication techniques. J Membr Sci, 523: 596–613.
- Lawson S, Snarzyk M, Hanify D, et al., 2020, Development of 3D-printed polymer-MOF monoliths for CO2 adsorption. Ind Eng Chem Res, 59: 7151–7160. https://doi.org/10.1021/acs.iecr.9b05445
- Zhakeyev A, Wang P, Zhang L, et al., 2017, Additive manufacturing: Unlocking the evolution of energy materials. Adv Sci, 4: 1700187. https://doi.org/10.1002/advs.201700187
- Li X, Rezaei F, Rownaghi AA, 2019, Methanol-to-olefin conversion on 3D-printed ZSM-5 monolith catalysts: Effects of metal doping, mesoporosity and acid strength. Microporous Mesoporous Mater, 276: 1–12.
- Wright PA, Pearce GM, (eds), 2010, Structural chemistry of zeolites. In: Zeolites and Catalysis. Germany: Wiley-VCH, Federal Republic of Germany, p.171–207. https://doi.org/10.1002/9783527630295.ch7
- Derbe T, Temesgen S, Bitew M, 2021, A short review on synthesis, characterization, and applications of zeolites. Adv Mater Sci Eng, 2021: 6637898. https://doi.org/10.1155/2021/6637898
- Emami Moghaddam SA, Harun R, Mokhtar MN, et al., 2018, Potential of zeolite and algae in biomass immobilization. Biomed Res Int, 2018: 6563196. https://doi.org/10.1155/2018/6563196
- Weckhuysen BM, 2016, Zeolites shine bright. Nat Mater, 15: 933–934. https://doi.org/10.1038/nmat4730
- Jha B, Singh DN, (eds), 2016, Basics of zeolites. In: Fly Ash Zeolites: Innovations, Applications, and Directions. Singapore, Berlin: Springer Singapore, p.5–31. https://doi.org/10.1007/978-981-10-1404-8_2
- Baerlocher C, McCusker LB, Olson DH, (eds), 2007, Introduction and explanatory notes. In: Atlas of Zeolite Framework Types. 6th ed. Amsterdam: Elsevier Science B.V, p.3–11. Available from: https://www.sciencedirect.com/ science/article/pii/B9780444530646501870 [Last accessed on 2023 Sep 21].
- Król M, 2020, Natural vs. synthetic zeolites. Crystals, 10: 622. https://doi.org/10.3390/cryst10070622
- Mijailović NR, Nedić Vasiljević B, Ranković M, et al., 2022, Environmental and pharmacokinetic aspects of zeolite/ pharmaceuticals systems-Two facets of adsorption ability. Catalysts, 12: 837. https://doi.org/10.3390/catal12080837
- Hollman GG, Steenbruggen G, Janssen-Jurkovičová M, 1999, A two-step process for the synthesis of zeolites from coal fly ash. Fuel, 78: 1225–1230.
- Yuna Z, 2016, Review of the natural, modified, and synthetic zeolites for heavy metals removal from wastewater. Environ Eng Sci, 33: 443–454. https://doi.org/10.1089/ees.2015.0166
- Sircar S, Myers AL, 2003, Gas separation by zeolites. In: Handbook of Zeolite Science and Technology. Boca Raton: CRC Press, p. 22.
- Tran YT, Lee J, Kumar P, et al., 2019, Natural zeolite and its application in concrete composite production. Compos B Eng, 165: 354–364.
- Li J, Gao M, Yan W, et al., 2023, Regulation of the Si/Al ratios and Al distributions of zeolites and their impact on properties. Chem Sci, 14: 1935–1959. https://doi.org/10.1039/D2SC06010H
- Bakhtyari A, Mofarahi M, Lee CH, (eds), 2020, CO2 adsorption by conventional and nanosized zeolites. In: Advances in Carbon Capture. Ch. 9. United Kingdom: Woodhead Publishing, p.193–228. Available from: https://www.sciencedirect.com/science/article/pii/ B9780128196571000098 [Last accessed 2023 Sep 21].
- Langwaldt J, 2008, Ammonium removal from water by eight natural zeolites: A comparative study. Sep Sci Technol, 43: 2166–2182. https://doi.org/10.1080/01496390802063937
- Karousos DS, Sapalidis AA, Kouvelos EP, et al., 2016, A study on natural clinoptilolite for CO2/N2 gas separation. Sep Sci Technol, 51: 83–95. https://doi.org/10.1080/01496395.2015.1085880
- Kraljević Pavelić S, Simović Medica J, Gumbarević D, et al., 2018, Critical review on zeolite clinoptilolite safety and medical applications in vivo. Front Pharmacol, 9: 01350.
- Bandura L, Woszuk A, Kołodyńska D, et al., 2017, Application of mineral sorbents for removal of petroleum substances: A review. Minerals, 7: 37. https://doi.org/10.3390/min7030037
- Villarreal A, Garbarino G, Riani P, et al., 2017, Adsorption and separation of CO2 from N2-rich gas on zeolites: Na-X faujasite vs Na-mordenite. J CO2 Util, 19: 266–275.
- Shukla P, Dong K, Rudolph V, et al., 2019, Adsorptive dehydration of ethanol using 3A zeolite: An evaluation of transport behaviour in a two-phase zeolite pellet. Adsorption, 25: 1611–1623. https://doi.org/10.1007/s10450-019-00145-y
- Larasati ZS, Widiastuti N, 2018, Adsorption-desorption of CO2 and H2 gases on zeolite-X supported on glass fiber. AIP Conf Proc, 2049: 020083. https://doi.org/10.1063/1.5082488
- Guo X, Zhang P, Navrotsky A, 2020, The thermodynamics of gas absorption and guest-induced flexibility in zeolite Y. Microporous Mesoporous Mater, 294: 109893.
- Bradley SA, Broach RW, Mezza TM, et al., (eds), 2010, Zeolite characterization. In: Zeolites in Industrial Separation and Catalysis. Great Britain: Wiley-VCH, p.85–171. https://doi.org/10.1002/9783527629565.ch4
- Stelzer J, Paulus M, Hunger M, et al., 1998, Hydrophobic properties of all-silica zeolite beta1Dedicated to Professor Lovat V.C. Rees in recognition and appreciation of his lifelong devotion to zeolite science and his outstanding achievements in this field.1. Microporous Mesoporous Mater, 22: 1–8.
- Feng C, Jiaqiang E, Han W, et al., 2021, Key technology and application analysis of zeolite adsorption for energy storage and heat-mass transfer process: A review. Renew Sustain Energy Rev, 144: 110954.
- Pérez-Pellitero J, Pirngruber GD, (eds), 2020, Industrial zeolite applications for gas adsorption and separation processes. In: New Developments in Adsorption/Separation of Small Molecules by Zeolites. Cham: Springer International Publishing, p.195–225. https://doi.org/10.1007/430_2020_75
- Rezaei F, Webley P, 2010, Structured adsorbents in gas separation processes. Sep Purif Technol, 70: 243–256.
- Wu J, Zhu X, Yang F, et al., 2022, Shaping techniques of adsorbents and their applications in gas separation: A review. J Mater Chem A, 10: 22853–22895. https://doi.org/10.1039/D2TA04352A
- Boer DG, Langerak J, Pescarmona PP, 2023, Zeolites as selective adsorbents for CO2 separation. ACS Appl Energy Mater, 6: 2634–2656. https://doi.org/10.1021/acsaem.2c03605
- Tomašić V, Jović F, 2006, State-of-the-art in the monolithic catalysts/reactors. Appl Catal A Gen, 311: 112–121.
- Li YY, Perera SP, Crittenden BD, 1998, Zeolite monoliths for air separation: Part 1: Manufacture and characterization. Chem Eng Res Des, 76: 921–930.
- Aranzabal A, Iturbe D, Romero-Sáez M, et al., 2010, Optimization of process parameters on the extrusion of honeycomb shaped monolith of H-ZSM-5 zeolite. Chem Eng J, 162: 415–423.
- Fedosov DA, Smirnov AV, Knyazeva EE, et al., 2011, Zeolite membranes: Synthesis, properties, and application. Pet Chem, 51: 657–667. https://doi.org/10.1134/S0965544111080032
- Mette B, Kerskes H, Drück H, et al., 2014, Experimental and numerical investigations on the water vapor adsorption isotherms and kinetics of binderless zeolite 13X. Int J Heat Mass Transf, 71: 555–561.
- Silva JAC, Schumann K, Rodrigues AE, 2012, Sorption and kinetics of CO2 and CH4 in binderless beads of 13X zeolite. Microporous Mesoporous Mater, 158: 219–228.
- Scheffler M, Scheffler F, 2006, Zeolite coatings on porous monoliths. Adv Sci Technol, 45: 1260–1267.
- Li L, Xue B, Chen J, et al., 2005, Direct synthesis of zeolite coatings on cordierite supports by in situ hydrothermal method. Appl Catal A Gen, 292: 312–321.
- Aimen Isa M, Hanif Halim M, Chew TL, et al., 2020, Formation of NaY zeolite membrane: Influence of intermediate layer and its characterization. IOP Conf Ser Mater Sci Eng, 736: 052019. https://doi.org/10.1088/1757-899X/736/5/052019
- Stuecker JN, Miller JE, Ferrizz RE, et al., 2004, Advanced support structures for enhanced catalytic activity. Ind Eng Chem Res, 43: 51–55. https://doi.org/10.1021/ie030291v
- Liu J, Huo W, Ren B, et al., 2018, A novel approach to fabricate porous alumina ceramics with excellent properties via pore-forming agent combined with sol impregnation technique. Ceram Int, 44: 16751–16757.
- Hull CW, 1984, Apparatus for Production of Three-dimensional Objects by Stereolithography. United States Patent, Application, No. 638905, Filed. Avialable from: https://pubchem.ncbi.nlm.nih.gov/patent/US-6027324-A [Last accessed on 2023 Sep 21].
- Pagac M, Hajnys J, Ma QP, et al., 2021, A review of vat photopolymerization technology: Materials, applications, challenges, and future trends of 3D printing. Polymers (Basel), 13: 598. https://doi.org/10.3390/polym13040598
- Nohut S, Schwentenwein M, 2022, Vat photopolymerization additive manufacturing of functionally graded materials: A review. J Manuf Mater Process, 6: 17.
- Zhang F, Li Z, Xu M, et al., 2022, A review of 3D printed porous ceramics. J Eur Ceram Soc, 42: 3351–3373.
- Shahzad A, Lazoglu I, 2021, Direct ink writing (DIW) of structural and functional ceramics: Recent achievements and future challenges. Compos B Eng, 225: 109249.
- Pan Y, Zhu P, Wang R, et al., 2019, Direct ink writing of porous cordierite honeycomb ceramic. Ceram Int, 45: 15230–15236.
- Solís Pinargote NW, Smirnov A, Peretyagin N, et al., 2020, Direct ink writing technology (3D printing) of graphene-based ceramic nanocomposites: A review. Nanomater, 10: 1300. https://doi.org/10.3390/nano10071300
- Crump SS, 1992, Apparatus and Method for Creating Three-dimensional Objects. United States Patent, Application, No. 5,121,329, Filed. Available from: https://patents.google. com/patent/US5121329/en [Last accessed on 2023 Sep 21].
- Lakhdar Y, Tuck C, Binner J, et al., 2021, Additive manufacturing of advanced ceramic materials. Prog Mater Sci, 116: 100736.
- Smay JE, Gratson GM, Shepherd RF, et al., 2002, Directed colloidal assembly of 3D periodic structures. Adv Mater, 14: 1279–1283. https://doi.org/10.1002/1521-4095(20020916)14:18<1279::AID-ADMA1279>3.0.CO;2-A
- Schlordt T, Schwanke S, Keppner F, et al., 2013, Robocasting of alumina hollow filament lattice structures. J Eur Ceram Soc, 33: 3243–3248.
- Ziaee M, Crane NB, 2019, Binder jetting: A review of process, materials, and methods. Addit Manuf, 28: 781–801.
- Mirzababaei S, Pasebani S, 2019, A review on binder jet additive manufacturing of 316L stainless steel. J Manuf Mater Process, 3: 82. https://doi.org/10.3390/jmmp3030082
- Bose S, Vahabzadeh S, Bandyopadhyay A, 2013, Bone tissue engineering using 3D printing. Mater Today, 16: 496–504.
- Chung H, Das S, 2008, Functionally graded Nylon-11/silica nanocomposites produced by selective laser sintering. Mater Sci Eng A, 487: 251–257.
- Zhang G, Chen H, Yang S, et al., 2018, Frozen slurry-based laminated object manufacturing to fabricate porous ceramic with oriented lamellar structure. J Eur Ceram Soc, 38: 4014–4019.
- Van Noyen J, De Wilde A, Schroeven M, et al., 2012, Ceramic processing techniques for catalyst design: Formation, properties, and catalytic example of ZSM-5 on 3-dimensional fiber deposition support structures. Int J Appl Ceram Technol, 9: 902–910. https://doi.org/10.1111/j.1744-7402.2012.02781.x
- Thakkar H, Eastman S, Hajari A, et al., 2016, 3D-printed zeolite monoliths for CO2 removal from enclosed environments. ACS Appl Mater Interfaces, 8: 27753–27761. https://doi.org/10.1021/acsami.6b09647
- Liu X, He J, Li R, 2012, High-pressure hydrogen adsorption in the zeolites: A grand canonical Monte Carlo study. ISRN Renew Energy, 2012: 491396. https://doi.org/10.5402/2012/491396
- Asgar Pour Z, Sebakhy KO, 2022, A review on the effects of organic structure-directing agents on the hydrothermal synthesis and physicochemical properties of zeolites. Chemistry, 4: 431–446.
- Lawson S, Newport K, Al-Naddaf Q, et al., 2021, Binderless zeolite monoliths production with sacrificial biopolymers. Chem Eng J, 407: 128011.
- Zhang H, Wang P, Zhang H, et al., 2020, Structured zeolite monoliths with ultrathin framework for fast CO2 adsorption enabled by 3D printing. Ind Eng Chem Res, 59: 8223–8229. https://doi.org/10.1021/acs.iecr.9b07060
- Couck S, Lefevere J, Mullens S, et al., 2017, CO2, CH4 and N2 separation with a 3DFD-printed ZSM-5 monolith. Chem Eng J, 308: 719–726.
- Wang S, Bai P, Wei Y, et al., 2019, Three-dimensional-printed core-shell structured MFI-type zeolite monoliths for volatile organic compound capture under humid conditions. ACS Appl Mater Interfaces, 11: 38955–38963. https://doi.org/10.1021/acsami.9b13819
- Merilaita N, Vastamäki T, Ismailov A, et al., 2021, Stereolithography as a manufacturing method for a hierarchically porous ZSM-5 zeolite structure with adsorption capabilities. Ceram Int, 47: 10742–10748.
- Hawaldar N, Park HY, Jung YG, et al., 2018, Extrusion-based 3D printing of molecular sieve zeolite for gas adsorption applications. Mater Sci Technol, 33–40. https://doi.org/10.7449/2018mst/2018/mst_2018_33_40
- Lawson S, Adebayo B, Robinson C, et al., 2020, The effects of cell density and intrinsic porosity on structural properties and adsorption kinetics in 3D-printed zeolite monoliths. Chem Eng Sci, 218: 115564.
- Couck S, Cousin-Saint-Remi J, Van der Perre S, et al., 2018, 3D-printed SAPO-34 monoliths for gas separation. Microporous Mesoporous Mater, 255: 185–191.
- Feilden E, Blanca EGT, Giuliani F, et al., 2016, Robocasting of structural ceramic parts with hydrogel inks. J Eur Ceram Soc, 36: 2525–2533.
- Liu G, Guo J, Meng F, et al., 2014, Effects of colloidal silica binder on catalytic activity and adhesion of HZSM-5 coatings for structured reactors. Chin J Chem Eng, 22: 875–881.
- Lee KY, Lee HK, Ihm SK, 2010, Influence of catalyst binders on the acidity and catalytic performance of HZSM-5 zeolites for methanol-to-propylene (MTP) process: Single and binary binder system. Top Catal, 53: 247–253. https://doi.org/10.1007/s11244-009-9412-0
- Lefevere J, Protasova L, Mullens S, et al., 2017, 3D-printing of hierarchical porous ZSM-5: The importance of the binder system. Mater Des, 134: 331–341.
- Yang Y, Zhou Z, Chu X, et al., 2022, 3D-printed zeolite with combined structure for xylene isomerization. Mater Des, 219: 110744.
- Shukrun Farrell E, Schilt Y, Moshkovitz MY, et al., 2020, 3D printing of ordered mesoporous silica complex structures. Nano Lett, 20: 6598–6605. https://doi.org/10.1021/acs.nanolett.0c02364
- Bastani D, Esmaeili N, Asadollahi M, 2013, Polymeric mixed matrix membranes containing zeolites as a filler for gas separation applications: A review. J Ind Eng Chem, 19: 375–393.
- Thakkar H, Lawson S, Rownaghi AA, et al., 2018, Development of 3D-printed polymer-zeolite composite monoliths for gas separation. Chem Eng J, 348: 109–116.
- Wudy K, Hinze M, Ranft F, et al., 2017, Selective laser sintering of zeolite filled polypropylene composites: Processing and properties of bulk adsorbents. J Mater Process Tech, 246: 136–143.
- Zhang Y, Josien L, Salomon JP, et al., 2021, Photopolymerization of zeolite/polymer-based composites: Toward 3D and 4D printing applications. ACS Appl Polym Mater, 3: 400–409. https://doi.org/10.1021/acsapm.0c01170
- Liu J, He J, Wang L, et al., 2016, NiO-PTA supported on ZIF-8 as a highly effective catalyst for hydrocracking of Jatropha oil. Sci Rep, 6: 23667. https://doi.org/10.1038/srep23667
- Huang H, Zhang W, Liu D, et al., 2011, Effect of temperature on gas adsorption and separation in ZIF-8: A combined experimental and molecular simulation study. Chem Eng Sci, 66: 6297–6305.
- Evans KA, Kennedy ZC, Arey BW, et al., 2018, Chemically active, porous 3D-printed thermoplastic composites. ACS Appl Mater Interfaces, 10: 15112–15121. https://doi.org/10.1021/acsami.7b17565
- Bible M, Sefa M, Fedchak JA, et al., 2018, 3D-printed acrylonitrile butadiene styrene-metal organic framework composite materials and their gas storage properties. 3D Print Addit Manuf, 5: 63–72. https://doi.org/10.1089/3dp.2017.0067
- Lefevere J, Claessens B, Mullens S, et al., 2019, 3D-printed zeolitic imidazolate framework structures for adsorptive separations. ACS Appl Nano Mater, 2: 4991–4999. https://doi.org/10.1021/acsanm.9b00934
- Magzoub F, Li X, Lawson S, et al., 2020, 3D-printed HZSM-5 and 3D-HZM5@SAPO-34 structured monoliths with controlled acidity and porosity for conversion of methanol to dimethyl either. Fuel, 280: 118628. 118. Lee J, Chuah CY, Tan WS, et al., 2022, 3D-printed monolithic porous adsorbents from a solution-processible, hypercrosslinkable, functionalizable polymer. Chem Eng J, 427: 130883.
- Li X, Rezaei F, Rownaghi AA, 2018, 3D-printed zeolite monoliths with hierarchical porosity for selective methanol to light olefin reaction. React Chem Eng, 3: 733–746. https://doi.org/10.1039/C8RE00095F
- Chu X, Tang X, Chen W, et al., 2023, Direct-ink-write printing performance of zeolite catalysts with porous structures. Ceram Int, 49: 13531–13541.
- Bragina AA, Lysikov AI, Parkhomchuk EV, 2022, Forming of block zeolites using 3D printing technology. Pet Chem, 62: 853–861. https://doi.org/10.1134/S0965544122070088
- Morishige K, 2011, Adsorption and separation of CO2/CH4 on amorphous silica molecular sieve. J Phys Chem C, 115: 9713–9718. https://doi.org/10.1021/jp202572w
- Li Y, Yi H, Tang X, et al., 2013, Adsorption separation of CO2/CH4 gas mixture on the commercial zeolites at atmospheric pressure. Chem Eng J, 229: 50–56.
- Zhao R, Liu L, Zhao L, et al., 2018, Thermodynamic analysis on carbon dioxide capture by electric swing adsorption (ESA) technology. J CO2 Util, 26: 388–396.
- Regufe MJ, Ferreira AFP, Loureiro JM, et al., 2019, Electrical conductive 3D-printed monolith adsorbent for CO2 capture. Microporous Mesoporous Mater, 278: 403–413.
- Gelles T, Krishnamurthy A, Adebayo B, et al., 2020, Abatement of gaseous volatile organic compounds: A material perspective. Catal Today, 350: 3–18.
- Krishnamurthy A, Adebayo B, Gelles T, et al., 2020, Abatement of gaseous volatile organic compounds: A process perspective. Catal Today, 350: 100–119.
- Pellejero I, Almazán F, Lafuente M, et al., 2020, Functionalization of 3D printed ABS filters with MOF for toxic gas removal. J Ind Eng Chem, 89: 194–203.
- Dhainaut J, Bonneau M, Ueoka R, et al., 2020, Formulation of metal-organic framework inks for the 3D Printing of robust microporous solids toward high-pressure gas storage and separation. ACS Appl Mater Interfaces, 12: 10983–10992. https://doi.org/10.1021/acsami.9b22257
- Thompson JF, Bellerjeau C, Marinick G, et al., 2019, Intrinsic thermal desorption in a 3D printed multifunctional composite CO2 sorbent with embedded heating capability. ACS Appl Mater Interfaces, 11: 43337–43343. https://doi.org/10.1021/acsami.9b14111