Fast layer fiber orientation optimization method for continuous fiber-reinforced material extrusion process
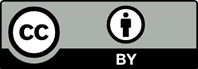
Material extrusion (MEX) is an additive manufacturing process that uses thermoplastic layer-by-layer building. The use of continuous fiber-reinforced filament enhances mechanical properties, making MEX suitable for use in aerospace, automotive, and robotics industries. This study proposes a laminate optimization method to improve the stiffness of printed parts with low computing time. The 2D stress-flow-based method optimizes fiber’s orientation for each layer in the stacking direction, giving results for a 3D part optimization in a few minutes. Developed with Ansys Parametric Design Language, the computation tool was tested on printed wrenches, resulting in an 18% increase in stiffness. The proposed method is applicable to any printable shape.
Yicha Zhang serves as the Editorial Board Member of the journal, but did not in any way involve in the editorial and peer-review process conducted for this paper, directly or indirectly.
Zheng H, Zhang W, Li B, et al., 2022, Recent advances of interphases in carbon fiber-reinforced polymer composites: A review. Compos B Eng, 233: 109639. https://doi.org/10.1016/j.compositesb.2022.109639
Li J, Durandet Y, Huang X, et al., 2022, Additively manufactured fiber-reinforced composites: A review of mechanical behavior and opportunities. J Mater Sci Technol, 119: 219–244. https://doi.org/10.1016/j.jmst.2021.11.063
Liao G, Li Z, Cheng Y, et al., 2018, Properties of oriented carbon fiber/polyamide 12 composite parts fabricated by fused deposition modeling. Mater Des, 139: 283–292. https://doi.org/10.1016/j.matdes.2017.11.027
Yan C, Hao L, Xu L, et al., 2011, Preparation, characterisation and processing of carbon fibre/polyamide-12 composites for selective laser sintering. Compos Sci Technol, 71: 1834–1841. http://dx.doi.org/10.1016/j.compscitech.2011.08.013
Goodridge RD, Shofner ML, Hague RJM, et al., 2011, Processing of a polyamide-12/carbon nanofiber composite by laser sintering. Poly Test, 30: 94–100. http://dx.doi.org/10.1016/j.polymertesting.2010.10.011
Jansson A, Pejryd L, 2016, Characterisation of carbon fibre-reinforced polyamide manufactured by selective laser sintering. Addit Manuf, 9: 7–13. http://dx.doi.org/10.1016/j. addma.2015.12.003
Hofstätter T, Pedersen DB, Tosello G, et al., 2017, Applications of fiber-reinforced polymers in additive manufacturing. Procedia CIRP, 66: 312–316. https://doi-org.ezproxy.utbm.fr/10.1016/j.procir.2017.03.171
Tekinalp HL, Kunc V, Velez-Garcia GM, et al., 2014, Highly oriented carbon fiber-polymer composites via additive manufacturing. Compos Sci Technol, 105: 144–150. http://dx.doi.org/10.1016/j.compscitech.2014.10.009
van de Werken N, Tekinalp H, Khanbolouki P, et al., 2020, Additively manufactured carbon fiber-reinforced composites: State of the art and perspective. Addit Manuf, 31: 100962. https://doi.org/10.1016/j.addma.2019.100962
Tian X, Liu T, Yang C, et al., 2016, Interface and performance of 3D printed continuous carbon fiber reinforced PLA composites. Composites Part A, 88: 198–205. http://dx.doi.org/10.1016/j.compositesa.2016.05.032
Aravind AU, Bhagat AR, Radhakrishnan R, et al., 2020, A novel use of twisted continuous carbon fibers in additive manufacturing of composites. Materials Today: Proceedings. https://doi.org/10.1016/j.matpr.2020.07.665
Material Datasheet: Composites, Markforged. Available from: https://www-objects.markforged.com/craft/materials/ compositesv5.2.pdf [Last accessed on 2022 Dec 13].
Mahajan C, Cormier D, 2015, 3D Printing of Carbon Fiber Composites with Preferentially Aligned Fibers. Proceedings of the 2015 Industrial and Systems Engineering Research Conference.
Goh GD, Toh W, Yap YL, et al., 2021, Additively manufactured continuous carbon fiber-reinforced thermoplastic for topology optimized unmanned aerial vehicle structures. Composites Part B, 216: 108840. https://doi.org/10.1016/j.compositesb.2021.108840
Lewicki JP, Rodriguez JN, Zhu C, et al., 2017, 3D-Printing of meso-structurally ordered carbon fiber/polymer composites with unprecedented orthotropic physical properties. Sci Rep, 7: 43401. https://doi.org/10.1038/srep43401
Zhou Y, Nomura T, Saitou K, 2018, Multi-component topology and material orientation design of composite structures (MTO-C). Comput Methods Appl Mech Eng, 342: 438–457. https://doi.org/10.1016/j.cma.2018.07.039
Ding H, Xu B, 2021, A novel discrete-continuous material orientation optimization model for stiffness-based concurrent design of fiber composite. Compos Struct, 273: 114288. https://doi.org/10.1016/j.compstruct.2021.114288
Li Y, Xu K, Liu X, et al., 2021, Stress-oriented 3D printing path optimization based on image processing algorithms for reinforced load-bearing parts. CIRP Ann Manuf Technol, 70: 195–198. https://doi.org/10.1016/j.cirp.2021.04.037
Safonov AA, 2019, 3D topology optimization of continuous fiber-reinforced structures via natural evolution method. Compos Struct, 215: 289–297. https://doi.org/10.1016/j.compstruct.2019.02.063
Nomura T, Kawamoto A, Kondoh T, et al., 2019, Inverse design of structure and fiber orientation by means of topology optimization with tensor field variables. Composites Part B, 176: 107187. https://doi.org/10.1016/j.compositesb.2019.107187
Jung T, Lee J, Nomura T, et al., 2022, Inverse design of three-dimensional fiber-reinforced composites with spatially-varying fiber size and orientation usign multiscale topology optimization. Compos Struct, 279: 114768. https://doi.org/10.1016/j.compstruct.2021.114768