Microstructure, mechanical properties, and corrosion performance of additively manufactured CoCrFeMnNi high-entropy alloy before and after heat treatment
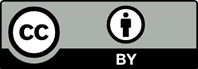
Equiatomic CoCrFeMnNi, one of the well-known high-entropy alloys, possesses attractive mechanical properties for many potential applications. In this research, the effects of heat treatment on additively manufactured CoCrFeMnNi materials were studied. A pilot experiment was conducted to select two selective laser melting (SLM) conditions of different laser scanning speeds based on the density and porosity of obtained materials. Thereafter, microstructure, tensile properties, impact fracture, microhardness, and corrosion resistance were investigated for the materials obtained under the two selected SLM conditions, with and without heat treatment. It was discovered that while the texture with a strong <100> alignment was observed in both as-built and heat treated materials, the texture of heat treated materials was stronger. Also, heat treatment drastically improved the ductility of as-built CoCrFeMnNi by 23 – 59% for the selected SLM conditions, while the ultimate tensile strength showed only negligible change. The increase of ductility was believed to result from the release of residual strain and the increase of average grain size after heat treatment. Moreover, heat treatment was able to bring noticeable improvement in energy absorption for the as-built CoCrFeMnNi, reflected by 11 – 16% more energy absorption. Besides, all studied materials showed signs of ductile fracture, but more signs of brittle fracture, such as cleavage facets, were found in the as-built materials as compared with the heat-treated materials. In addition, higher laser scan speed was found to cause moderate reduction in corrosion resistance. Effect of heat treatment was also negative and mild for lower scanning speed case. However, the highest reduction in corrosion resistance was observed after heat treatment of the high laser scanning speed case.
Jing Shi serves as the Editorial Board Member of the journal, but did not in any way involve in the editorial and peer-review process conducted for this paper, directly or indirectly.
Moghaddam AO, Shaburova NA, Samodurova MN, et al., 2021, Additive manufacturing of high entropy alloys: A practical review. J Mater Sci Technol, 77: 131–162.
Yeh JW, Chen SK, Lin SJ, et al., 2004, Nanostructured high‐entropy alloys with multiple principal elements: novel alloy design concepts and outcomes. Adv Eng Mater, 6: 299–303.
Eißmann N, Klöden B, Weißgärber T, et al., 2017, High-entropy alloy CoCrFeMnNi produced by powder metallurgy. Powder Metallurgy, 60: 184–197.
Wang X, Guo W, Fu Y, 2021, High-entropy alloys: Emerging materials for advanced functional applications. J Mater Chem A, 9: 663–701.
Chen S, Tong Y, Liaw PK, 2018, Additive manufacturing of high-entropy alloys: A review. Entropy, 20: 937. https://doi.org/10.3390/e20120937
Cantor B, Chang ITH, Knight P, et al., 2004, Microstructural development in equiatomic multicomponent alloys. Mater Sci Eng A, 375: 213–218.
Zaddach AJ, Niu C, Koch CC, et al., 2013, Mechanical properties and stacking fault energies of NiFeCrCoMn high-entropy alloy. JOM, 65: 1780–1789.
Drissi-Daoudi R, Pandiyan V, Logé R, et al., 2022, Differentiation of materials and laser powder bed fusion processing regimes from airborne acoustic emission combined with machine learning. Virtual Phys Prototyp, 17: 181–204.
Sing SL, 2022, Perspectives on additive manufacturing enabled Beta-titanium alloys for biomedical applications. Int J Bioprint, 8: 478. https://doi.org/10.18063/ijb.v8i1.478
Shi J, Wang Y, 2020, Development of metal matrix composites by laser-assisted additive manufacturing technologies: A review. J Mater Sci, 55: 9883–9917.
Wang Y, Shi J, Liu Y, 2019, Competitive grain growth and dendrite morphology evolution in selective laser melting of Inconel 718 superalloy. J Cryst Growth, 521: 15–29.
Brif Y, Thomas M, Todd I, 2015, The use of high-entropy alloys in additive manufacturing. Scr Mater, 99: 93–96.
Li R, Niu P, Yuan T, et al., 2018, Selective laser melting of an equiatomic CoCrFeMnNi high-entropy alloy: Processability, non-equilibrium microstructure and mechanical property. J Alloys Compounds, 746: 125–134.
Chen P, Li S, Zhou Y, et al., 2020, Fabricating CoCrFeMnNi high entropy alloy via selective laser melting in-situ alloying. J Mater Sci Technol, 43: 40–43.
Guo J, Goh M, Zhu Z, et al., 2018, On the machining of selective laser melting CoCrFeMnNi high-entropy alloy. Mater Des, 153: 211–220.
Savinov R, Wang Y, Wang J, et al., 2021, Comparison of microstructure and properties of CoCrFeMnNi high-entropy alloy from selective laser melting and directed energy deposition processes. Procedia Manuf, 53: 435–442.
Zhang C, Feng K, Kokawa H, et al., 2020, Cracking mechanism and mechanical properties of selective laser melted CoCrFeMnNi high entropy alloy using different scanning strategies. Mater Sci Eng A, 789: 139672.
Chew Y, Bi GJ, Zhu ZG, et al., 2019, Microstructure and enhanced strength of laser aided additive manufactured CoCrFeNiMn high entropy alloy. Mater Sci Eng A, 744: 137–144.
Keshavarz MK, Sikan F, Boutet CE, et al., 2019, Impact properties of half stress-relieved and hot isostatic pressed Ti–6Al–4V components fabricated by laser powder bed fusion. Mater Sci Eng A, 760: 481–488.
Lee KA, Kim YK, Yu JH, et al., 2017, Effect of heat treatment on microstructure and impact toughness of Ti-6Al-4V manufactured by selective laser melting process. Arch Metallurgy Mater, 62: 1341–1346.
Krishnadev M, Larouche M, Lakshmanan VI, et al., 2010, Failure analysis of failed wire rope. J Failure Anal Prev, 10: 341–348.
Kim JH, Lim KR, Won JW, et al., 2018, Mechanical properties and deformation twinning behavior of as-cast CoCrFeMnNi high-entropy alloy at low and high temperatures. Mater Sci Eng A, 712: 108–113.
Xia SQ, Gao MC, Zhang Y, 2018, Abnormal temperature dependence of impact toughness in AlxCoCrFeNi system high entropy alloys. Mater Chem Phys, 210: 213–221.
Bi G, Chew Y, Weng F, et al., 2018, Process study and characterization of properties of FeCrNiMnCo high-entropy alloys fabricated by laser-aided additive manufacturing. In: Advanced Laser Processing and Manufacturing II. Vol. 10813. United States: SPIE. pp. 43–52.
Kim YK, Kim MC, Lee KA, 2022, 1.45 GPa ultrastrong cryogenic strength with superior impact toughness in the in-situ nano oxide reinforced CrMnFeCoNi high-entropy alloy matrix nanocomposite manufactured by laser powder bed fusion. J Mater Sci Technol, 97: 10–19.
Vaidya M, Guruvidyathri K, Murty BS, 2019, Phase formation and thermal stability of CoCrFeNi and CoCrFeMnNi equiatomic high entropy alloys. J Alloys Compounds, 774: 856–864.
Vaidya M, Anupam A, Bharadwaj JV, et al., 2019, Grain growth kinetics in CoCrFeNi and CoCrFeMnNi high entropy alloys processed by spark plasma sintering. J Alloys Compounds, 791: 1114–1121.
Laplanche G, Horst O, Otto F, et al., 2015, Microstructural evolution of a CoCrFeMnNi high-entropy alloy after swaging and annealing. J Alloys Compounds, 647: 548–557.
Sathiaraj GD, Tsai CW, Yeh JW, et al., 2016, The effect of heating rate on microstructure and texture formation during annealing of heavily cold-rolled equiatomic CoCrFeMnNi high entropy alloy. J Alloys Compounds, 688: 752–761.
Aiso T, Nishimoto M, Muto I, et al., 2021, Roles of alloying elements in the corrosion resistance of equiatomic CoCrFeMnNi high-entropy alloy and application to corrosion-resistant alloy design. Mater Trans, 62: 1677–1680.
Pathak S, Kumar N, Mishra RS, et al., 2019, Aqueous corrosion behavior of cast CoCrFeMnNi alloy. J Mater Eng Perform, 28: 5970–5977.
Peng H, Lin Z, Li R, et al., 2020, Corrosion behavior of an equiatomic CoCrFeMnNi high-entropy alloy-a comparison between selective laser melting and cast. Front Mater, 7: 244.
Popescu AMJ, Branzoi F, Burada M, et al., 2022, Influence of heat treatment on the corrosion behavior of electrodeposited CoCrFeMnNi high-entropy alloy thin films. Coatings, 12; 1108. https://doi.org/10.3390/coatings12081108
Melia MA, Carroll JD, Whetten SR, et al., 2019, Mechanical and corrosion properties of additively manufactured CoCrFeMnNi high entropy alloy. Addit Manuf, 29: 100833.
Kong D, Wang L, Zhu G, et al., 2023, Heat treatment effects on the metastable microstructure, mechanical property and corrosion behavior of Al-added CoCrFeMnNi alloys fabricated by laser powder bed fusion. J Mater Sci Technol, 138: 171–182.
Ren J, Mahajan C, Liu L, et al., 2019, Corrosion behavior of selectively laser melted CoCrFeMnNi high entropy alloy. Metals, 9: 1029.
Wang B, Sun M, Li B, et al., 2020, Anisotropic response of CoCrFeMnNi high-entropy alloy fabricated by selective laser melting. Materials, 13: 5687. https://doi.org/10.3390/ma13245687
Xu Z, Zhang H, Du X, et al., 2020, Corrosion resistance enhancement of CoCrFeMnNi high-entropy alloy fabricated by additive manufacturing. Corrosion Sci, 177: 108954.
Xiang S, Yuan Y, Zhang C, et al., 2022, Effects of process parameters on the corrosion resistance and biocompatibility of Ti6Al4V parts fabricated by selective laser melting. ACS Omega, 7: 5954–5961.
Cacace S, Semeraro Q, 2022, Fast optimisation procedure for the selection of L-PBF parameters based on utility function. Virtual Phys Prototyp, 17: 125–137.
Gong X, Zeng D, Groeneveld-Meijer W, et al., 2022, Additive manufacturing: A machine learning model of process-structure-property linkages for machining behavior of Ti-6Al-4V. Mater Sci Addit Manuf, 1: 6.
Lu C, Shi J, 2022, Relative density and surface roughness prediction for Inconel 718 by selective laser melting: Central composite design and multi-objective optimization. Int J Adv Manuf Technol, 119: 3931–3949.
Davis JR, 1998, Metals Handbook. Handbook Committee. Netherlands: ASM International.
Maitra V, Shi J, Lu C, 2022, Robust prediction and validation of as-built density of Ti-6Al-4V parts manufactured via selective laser melting using a machine learning approach. J Manuf Processes, 78: 183–201.
Cherry JA, Davies HM, Mehmood S, et al., 2015, Investigation into the effect of process parameters on microstructural and physical properties of 316L stainless steel parts by selective laser melting. Int J Adv Manuf Technol, 76: 869–879.
Bai Y, Yang Y, Wang D, et al., 2017, Influence mechanism of parameters process and mechanical properties evolution mechanism of maraging steel 300 by selective laser melting. Mater Sci Eng A, 703: 116–123.
Ye D, Zhu K, Fuh JY, et al., 2019, The investigation of plume and spatter signatures on melted states in selective laser melting. Optics Laser Technol, 111: 395–406.
Dai S, Zhu H, Zeng X, 2020, Effect of line energy density and wall thickness on the top surface quality of AlSi10Mg sample fabricated via selective laser melting. In: IOP Conf Ser Mater Sci Eng, 774: 012088.
Pal S, Lojen G, Hudak R, et al., 2020, As-fabricated surface morphologies of Ti-6Al-4V samples fabricated by different laser processing parameters in selective laser melting. Addit Manuf, 33: 101147.
Xiang S, Luan H, Wu J, et al., 2019, Microstructures and mechanical properties of CrMnFeCoNi high entropy alloys fabricated using laser metal deposition technique. J Alloys Compounds, 773: 387–392.
Wang Q, Amar A, Jiang C, et al., 2020, CoCrFeNiMo0. 2 high entropy alloy by laser melting deposition: Prospective material for low temperature and corrosion resistant applications. Intermetallics, 119: 106727.
Bian P, Shi J, Liu Y, et al., 2020, Influence of laser power and scanning strategy on residual stress distribution in additively manufactured 316L steel. Optics Laser Technol, 132: 106477.
Joseph J, Stanford N, Hodgson P, et al., 2017, Tension/ compression asymmetry in additive manufactured face centered cubic high entropy alloy. Scripta Mater, 129: 30–34.
Wang Y, Shi J, Lu S, et al., 2017, Selective laser melting of graphene-reinforced Inconel 718 superalloy: evaluation of microstructure and tensile performance. J Manuf Sci Eng, 139: 041005.
Ratanaphan S, Yoon Y, Rohrer GS, 2014, The five parameter grain boundary character distribution of polycrystalline silicon. J Mater Sci, 49: 4938–4945.
Bachmann F, Hielscher R, Schaeben H, 2010, Texture analysis with MTEX–free and open source software toolbox. In: Solid State Phenomena. Vol. 160. Switzerland: Trans Tech Publications Ltd. pp. 63–68.
Wright S, 2014, Time for a Change-New Perspectives in Grain Size Analysis. Available from: https://www.edaxblog. com/2014/06/23/time-for-a-change-new-perspectives-in-grain-size-analysis [Last accessed on 2023 Jan 10].
He X, DebRoy T, Fuerschbach PW, 2003, Alloying element vaporization during laser spot welding of stainless steel. J Phys D Appl Phys, 36: 3079.
Alcock CB, Itkin VP, Horrigan MK, 1984, Vapour pressure equations for the metallic elements: 298–2500K. Can Metallurgical Q, 23: 309–313.
Mouanga M, Berçot P, 2010, Comparison of corrosion behaviour of zinc in NaCl and in NaOH solutions; Part II: Electrochemical analyses. Corrosion Sci, 52: 3993–4000.
Collazo A, Figueroa R, Pérez C, et al., 2022, Effect of laser speed and hatch spacing on the corrosion behavior of 316L stainless steel produced by selective laser melting. Materials, 15: 1353.
Lu Y, Gan Y, Lin J, et al., 2017, Effect of laser speeds on the mechanical property and corrosion resistance of CoCrW alloy fabricated by SLM. Rapid Prototyp J, 23: 28–33.
Zhu M, Zhao B, Yuan Y, et al., 2021, Effect of annealing time on microstructure and corrosion behavior of CoCrFeMnNi high-entropy alloy in alkaline soil simulation solution. Corrosion Commun, 3: 45–61.
Sing SL, Huang S, Yeong WY, 2020, Effect of solution heat treatment on microstructure and mechanical properties of laser powder bed fusion produced cobalt-28chromium- 6molybdenum. Mater Sci Eng A, 769: 138511.
Gludovatz B, Hohenwarter A, Catoor D, et al., 2014, A fracture-resistant high-entropy alloy for cryogenic applications. Science, 345: 1153–1158.
Piglione A, Dovgyy B, Liu C, et al., 2018, Printability and microstructure of the CoCrFeMnNi high-entropy alloy fabricated by laser powder bed fusion. Mater Lett, 224: 22–25.
Haase C, Tang F, Wilms MB, et al., 2017, Combining thermodynamic modeling and 3D printing of elemental powder blends for high-throughput investigation of high-entropy alloys–Towards rapid alloy screening and design. Mater Sci Eng A, 688: 180–189.
Schuh B, Mendez-Martin F, Völker B, et al., 2015, Mechanical properties, microstructure and thermal stability of a nanocrystalline CoCrFeMnNi high-entropy alloy after severe plastic deformation. Acta Mater, 96: 258–268.
Otto F, Hanold NL, George EP, 2014, Microstructural evolution after thermomechanical processing in an equiatomic, single-phase CoCrFeMnNi high-entropy alloy with special focus on twin boundaries. Intermetallics, 54: 39–48.
Li D, Zhang Y, 2016, The ultrahigh charpy impact toughness of forged AlxCoCrFeNi high entropy alloys at room and cryogenic temperatures. Intermetallics, 70: 24–28.
Zhang Y, Zuo TT, Tang Z, et al., 2014, Microstructures and properties of high-entropy alloys. Progress Mater Sci, 61: 1–93.
Leng Y, 2009, Materials characterization: Introduction to Microscopic and Spectroscopic Methods. United States: John Wiley & Sons.