A bioinspired 3D-printable flexure joint with cellular mechanical metamaterial architecture for soft robotic hands
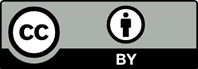
Compliant flexure joints have been widely used for cable-driven soft robotic hands and grippers due to their safe interaction with humans and objects. This paper presents a soft and compliant revolute flexure joint based on the auxetic cellular mechanical metamaterials with a heterogeneous structure. The heterogeneous architecture of the proposed metamaterial flexure joint (MFJ), which is inspired by the human finger joints, provides mechanically tunable multi-stiffness bending motion and large range of bending angle in comparison to conventional flexure joints. The multi-level variation of the joint stiffness over the range of bending motion can be tuned through the geometrical parameters of the cellular mechanical metamaterial unit cells. The proposed flexure joints are 3D printed with single flexible material in monolithic fashion using a standard benchtop 3D printer. The application of the MFJ is demonstrated in robotic in-hand manipulation and grasping thin and deformable objects such as wires and cables. The results show the capability and advantages of the proposed MFJ in soft robotic grippers and highly functional bionic hands.
1. Machekposhti DF, Tolou N, Herder JL, 2015, A review on compliant joints and rigid-body constant velocity universal joints toward the design of compliant homokinetic couplings. J Mech Des, 137: 032301. https://doi.org/10.1115/1.4029318
2. Laschi C, Cianchetti M, 2014, Soft robotics: New perspectives for robot bodyware and control. Front Bioeng Biotechnol, 2: 3. https://doi.org/10.3389/fbioe.2014.00003
3. Rus D, Tolley MT, 2015, Design, fabrication, and control of soft robots. Nature, 521: 467–475. https://doi.org/10.1038/nature14543
4. Müller VC, Hoffmann M, 2017, What is morphological computation? On how the body contributes to cognition and control. Artif Life, 23: 1–24. https://doi.org/10.1162/ARTL_a_00219
5. Mohammadi A, Lavranos J, Zhou H, et al., 2020, A practical 3D-printed soft robotic prosthetic hand with multi-articulating capabilities. PLoS One, 15: e0232766. https://doi.org/10.1371/journal.pone.0232766
6. Odhner LU, Jentoft LP, Claffee MR, et al., 2014, A compliant, underactuated hand for robust manipulation. Int J Robot Res, 33: 736–752. https://doi.org/10.1177/0278364913514466
7. Shintake J, Cacucciolo V, Floreano D, et al., 2018, Soft robotic grippers. Adv Mater, 30: 1707035. https://doi.org/10.1002/adma.201707035
8. Mutlu R, Alici G, Panhuis M, et al., 2016, 3D printed flexure hinges for soft monolithic prosthetic fingers. Soft Robot, 3: 120–133. https://doi.org/10.1089/soro.2016.0026
9. Giraud FH, Mete M, Paik J, 2022, Flexure variable stiffness actuators. Adv Intell Syst, 4: 2100282. https://doi.org/10.1002/aisy.202100282
10. Arredondo-Soto M, Cuan-Urquizo E, Gómez-Espinosa A, 2021, A review on tailoring stiffness in compliant systems, via removing material: Cellular materials and topology optimization. Appl Sci, 11: 3538. https://doi.org/10.3390/app11083538
11. Zadpoor AA, 2016, Mechanical meta-materials. Mater Horiz, 3: 371–381. https://doi.org/10.1039/C6MH00065G
12. Schaedler TA, Carter WB, 2016, Architected cellular materials. Annu Rev Mater Res, 46: 187–210. https://doi.org/10.1146/annurev-matsci-070115-031624
13. Surjadi JU, Gao L, Du H, et al., 2019, Mechanical metamaterials and their engineering applications. Adv Eng Mater, 21: 1800864. https://doi.org/10.1002/adem.201800864
14. Mohammadi A, Tan Y, Choong P, et al., 2021, Flexible mechanical metamaterials enabling soft tactile sensors with multiple sensitivities at multiple force sensing ranges. Sci Rep, 11: 24125. https://doi.org/10.1038/s41598-021-03588-y
15. Kaur M, Kim WS, 2019, Toward a smart compliant robotic gripper equipped with 3D-designed cellular fingers. Adv Intell Syst, 1: 1900019. https://doi.org/10.1002/aisy.201900019
16. Netzev M, Angleraud A, Pieters R, 2020, Soft Robotic Gripper with Compliant Cell Stacks for Industrial Part Handling. Vol. 5. United States: IEEE Robotics and Automation Letters, p6821–p6828.
17. Yan J, Xu Z, Shi P, et al., 2022, A human-inspired soft finger with dual-mode morphing enabled by variable stiffness mechanism. Soft Robot, 9: 399–411.
18. Goswami D, Liu S, Pal A, et al., 2019, 3D-architected soft machines with topologically encoded motion. Adv Funct Mater, 29: 1808713. https://doi.org/10.1002/adfm.201808713
19. Zhang J, Lu G, You Z, 2020, Large deformation and energy absorption of additively manufactured auxetic materials and structures: A review. Compos Part B Eng, 201: 108340. https://doi.org/10.1016/j.compositesb.2020.108340
20. Manti M, Cacucciolo V, Cianchetti M, 2016, Stiffening in Soft Robotics: A review of the State of the Art. Vol. 23. United States: IEEE Robotics and Automation Magazine, p93–p106.
21. Christian W, Esquembre F, Barbato L, 2011, Open source physics. Science, 334: 1077–1078. https://doi.org/10.1126/science.1196984
22. Bicchi A, 2000, Hands for Dexterous Manipulation and Robust Grasping: A Difficult Road Toward Simplicity. Vol. 16. United States: IEEE Transactions on Robotics and Automation, p652–p662.
23. Xavier MS, Tawk CD, Zolfagharian A, et al., 2022, Soft Pneumatic Actuators: A Review of Design, Fabrication, Modeling, Sensing, Control and Applications. United States: IEEE Access.
24. Sanchez J, Corrales JA, Bouzgarrou BC, et al., 2018, Robotic manipulation and sensing of deformable objects in domestic and industrial applications: A survey. Int J Robot Res, 37: 688–716. https://doi.org/10.1177/0278364918779698
25. Akbari S, Sakhaei AH, Panjwani S, et al., 2019, Multimaterial 3D printed soft actuators powered by shape memory alloy wires. Sens Actuators A Phys, 290: 177–189. https://doi.org/10.1016/j.sna.2019.03.015
26. Seckin M, Seckin AC, Turan NY, 2021, Investigation of discharge characteristics of hinges produced with 3D printing for prosthetic fingers. Politeknik Dergisi, 24: 575–583. https://doi.org/10.2339/politeknik.698316
27. Hainsworth T, Smith L, Alexander S, et al., 2020, A Fabrication Free, 3D Printed, Multi-Material, Self-Sensing Soft Actuator. Vol. 5. United States: IEEE Robotics and Automation Letters, p4118–p4125.