Stakeholder Perspectives on the Current and Future of Additive Manufacturing in Healthcare
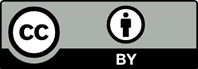
Additive manufacturing (AM) technologies have disrupted many supply chains by making new designs and functionalities possible. The opportunity to realize complex customized structures has led to significant interest within healthcare; however, full utilization critically requires the alignment of the whole supply chain. To offer insights into this process, a survey was conducted to understand the views of different medical AM stakeholders. The results highlighted an agreement between academics, designers, manufacturers, and medical experts, that personalization and design control are the main benefits of AM. Interestingly, surface finish was consistently identified as an obstacle. Nevertheless, there was a degree of acceptance that post-processing was necessary to achieve appropriate quality control. Recommendations were made for extending the use of in situ process monitoring systems to support improved reproducibility. Variations in the future vision of AM were highlighted between stakeholder groups and areas of interest for development noted for each stakeholder. Collectively, this survey indicates that medical stakeholders agree on the capabilities of AM but have different priorities for its implementation and progression. This highlights a degree of disconnection among the supply chain at a ground level; thus, collaboration on AM specific standards and enhancement of communication between stakeholders from project inception is recommended.
1. Schwab K, 2015, The Fourth Industrial Revolution: What It Means and How to Respond. Sri Lanka: Foreign Affairs.
2. Caviggioli F, Ughetto E, 2019, A Bibliometric Analysis of the Research Dealing with the Impact of Additive Manufacturing on Industry, Business and Society. Int J Prod Econ, 208:254–68. https://doi.org/10.1016/j.ijpe.2018.11.022
3. Kietzmann J, Berthon P, 2015, Disruptions, Decisions, and Destinations: Enter the Age of 3-D Printing and Additive Manufacturing. Bus Horiz, 58:209–15. https://doi.org/10.1016/j.bushor.2014.11.005
4. Peng T, Kellens K, Tang R, et al., 2018, Sustainability of Additive Manufacturing: An Overview on its Energy Demand and Environmental Impact. Addit Manuf, 21:694–704. https://doi.org/10.1016/j.addma.2018.04.022
5. Bagaria V, Pawar PB, 2018, 3D Printing-creating a Blueprint for the Future of Orthopedics: Current Concept Review and the Road Ahead! J Clin Orthop Trauma, 9:207–212. https://doi.org/10.1016/j.jcot.2018.07.007
6. Pugalendhi A, Ranganathan R, 2021, A Review of Additive Manufacturing Applications in Ophthalmology. Proc Inst Mech Eng H, 235:1146–62. https://doi.org/10.1016/j.addma.2019.03.015
7. Culmone C, Smit G, Breedveld P, 2019, Additive manufacturing of medical instruments: A state-of-the-art review. Addit Manuf, 27:461–73.
8. Garg B, Mehta N, 2018, Current Status of 3D Printing in Spine Surgery. J Clin Orthop Trauma, 9:218–25. https://doi.org/10.1016/j.jcot.2018.08.006
9. da Silva LR, Sales WF, Campos FD, et al., 2021, A Comprehensive Review on Additive Manufacturing of Medical Devices. Prog Addit Manuf, 6:1–37. https://doi.org/10.1007/s40964-021-00188-0
10. Hull CW, 2015, The Birth of 3D Printing. Res Technol Manage, 58:25–30.
11. Dilberoglu UM, Gharehpapagh B, Yaman U, et al., 2017, The Role of Additive Manufacturing in the Era of Industry 4.0. Proc Manuf, 11:545–54. https://doi.org/10.1016/j.promfg.2017.07.148
12. Renishaw, 2021, Renishaw News Updates. Available from: https://www.renishaw.com/en/company-news--6853 [Last accessed on 2022 Mar 01].
13. Additive G, 2021, GE Additive Press Releases. Available from: https://www.ge.com/additive/press-releases [Last accessed on 2022 Mar 01].
14. Solutions S, 2021, SLM Solutions News. Available from: https://www.slm-solutions.com/company/news [Last accessed on 2022 Mar 01].
15. TCT, 2021, TCT New Articles. Available from: www. tctmagazine.com [Last accessed on 2022 Mar 01].
16. EOS, 2022, EOS Press Centre. Available from: https://www.eos. info/en/presscenter/welcome [Last accessed on 2022 Mar 01].
17. Systems D, 2022, 3D System Resources. Available from: https://www.3dsystems.com/resources [Last accessed on 2022 Mar 01].
18. Stratasys, 2022, Stratasys News. Available from: https://www.sys-uk.com/news [Last accessed on 2022 Mar 01].
19. Oliveira TT, Reis AC, 2019, Fabrication of Dental Implants by the Additive Manufacturing Method: A Systematic Review. J Prosthet Dent, 122:270–4. https://doi.org/10.1016/j.prosdent.2019.01.018
20. Peel S, Eggbeer D, 2016, Additively Manufactured Maxillofacial Implants and Guides-achieving Routine Use. Rapid Prototyp J, 22:189–99. http://dx.doi.org/10.1108/RPJ-01-2014-0004
21. Meena VK, Kumar P, Kalra P, et al., 2021, Additive Manufacturing for Metallic Spinal Implants: A Systematic Review. Ann 3D Print Med, 3:100021. https://doi.org/10.1016/j.stlm.2021.100021
22. McGilvray KC, Easley J, Seim HB, et al., 2018, Bony Ingrowth Potential of 3D-printed Porous Titanium Alloy: A Direct Comparison of Interbody Cage Materials in an in vivo Ovine Lumbar Fusion Model. Spine J, 18:1250–60. https://doi.org/10.1016/j.spinee.2018.02.018
23. Wu SH, Li Y, Zhang YQ, et al., 2013, Porous Titanium-6 Aluminum-4 Vanadium Cage Has Better Osseointegration and Less Micromotion Than a Poly-Ether-Ether-Ketone Cage in Sheep Vertebral Fusion. Artif Organs, 37:E191–201. https://doi.org/10.1111/aor.12153
24. Cox SC, Jamshidi P, Eisenstein NM, et al., 2016, Adding Functionality with Additive Manufacturing: Fabrication of Titanium-based Antibiotic Eluting Implants. Mater Sci Eng C, 64:407–15. https://doi.org/10.1016/j.msec.2016.04.006
25. Carter LN, Addison O, Naji N, et al., 2020, Reducing MRI Susceptibility Artefacts in Implants using Additively Manufactured Porous Ti-6Al-4V Structures. Acta Biomater, 107:338–48. https://doi.org/10.1016/j.actbio.2020.02.038
26. Harrysson OL, Cansizoglu O, Marcellin-Little DJ, et al., 2008, Direct Metal Fabrication of Titanium Implants with Tailored Materials and Mechanical Properties using Electron Beam Melting Technology. Mater Sci Eng C, 28:366–73. https://doi.org/10.1016/j.msec.2007.04.022
27. Cox SC, Jamshidi P, Eisenstein NM, et al., 2017, Surface Finish has a Critical Influence on Biofilm Formation and Mammalian Cell Attachment to Additively Manufactured Prosthetics. ACS Biomater Sci Eng, 3:1616–26. https://doi.org/10.1021/acsbiomaterials.7b00336
28. Villapún VM, Carter LN, Gao N, et al., 2020, A Design Approach to Facilitate Selective Attachment of Bacteria and Mammalian Cells to Additively Manufactured Implants. Addit Manuf, 36:101528. https://doi.org/10.1016/j.addma.2020.101528
29. Lowther M, Louth S, Davey A, et al., 2019, Clinical, Industrial, and Research Perspectives on Powder Bed Fusion Additively Manufactured Metal Implants. Addit Manuf, 28:565–84. https://doi.org/10.1016/j.addma.2019.05.033
30. Kaye R, Goldstein T, Zeltsman D, et al., 2016, Three Dimensional Printing: A Review on the Utility within Medicine and Otolaryngology. Int J Pediatr Otorhinolaryngol, 89:145–148. https://doi.org/10.1016/j.ijporl.2016.08.007
31. Eshkalak SK, Ghomi ER, Dai Y, et al., 2020, The Role of Three-dimensional Printing in Healthcare and Medicine. Mater Des, 194:108940. https://doi.org/10.1016/j.matdes.2020.108940
32. Malik HH, Darwood AR, Shaunak S, et al., 2015, Three dimensional Printing in Surgery: A Review of Current Surgical Applications. J Surg Res, 199:512–22. https://doi.org/10.1016/j.jss.2015.06.051
33. Agresti A, 2003, Categorical Data Analysis. United States: John Wiley & Sons. p482.
34. Lal H, Patralekh MK, 2018, 3D Printing and its Applications in Orthopaedic Trauma: A Technological Marvel. J Clin Orthop Trauma, 9:260–8. https://doi.org/10.1016/j.jcot.2018.07.022
35. Niaki MK, Torabi SA, Nonino F, 2019, Why Manufacturers Adopt Additive Manufacturing Technologies: The Role of Sustainability. J Clean Prod, 222:381–92. https://doi.org/10.1016/j.jclepro.2019.03.019
36. Jirsák P, Brunet-Thornton R, 2019, Perspectives of Operational Additive Manufacturing: Case Studies from the Czech Aerospace Industry. J East Eur Cent Asian Res, 6:179–90. https://doi.org/10.15549/jeecar.v6i1.273
37. Delic M, Eyers DR, 2020, The Effect of Additive Manufacturing Adoption on Supply Chain Flexibility and Performance: An Empirical Analysis from the Automotive Industry. Int J Prod Econ, 228:107689. https://doi.org/10.1016/j.ijpe.2020.107689
38. Niaki MK, Nonino F, Palombi G, et al., 2019, Economic Sustainability of Additive Manufacturing: Contextual Factors Driving its Performance in Rapid Prototyping. J Manuf Technol Manage, 30:353–65 https://doi.org/10.1108/jmtm-05-2018-0131
39. Majumdar T, Eisenstein N, Frith JE, et al., 2018, Additive Manufacturing of Titanium Alloys for Orthopedic Applications: A Materials Science Viewpoint. Adv Eng Mater, 20:1800172. https://doi.org/10.1002/adem.201800172
40. Thomas-Seale LE, Kirkman-Brown JC, Attallah MM, et al., 2018, The Barriers to the Progression of Additive Manufacture: Perspectives from UK Industry. Int J Prod Econ, 198:104–18. https://doi.org/10.1016/j.ijpe.2018.02.003
41. Martinez-Marquez D, Jokymaityte M, Mirnajafizadeh A, et al., 2019, Development of 18 Quality Control Gates for Additive Manufacturing of Error Free Patient-specific Implants. Materials, 12:3110. https://doi.org/10.3390/ma12193110
42. Kandukuri S, Ze C, 2021, Progress of Metal AM and Certification Pathway. Trans Indian Natl Acad Eng, 17:1–7. https://doi.org/10.1007/s41403-021-00242-x
43. Bae CJ, Diggs AB, Ramachandran A, 2018, Quantification and certification of additive manufacturing materials and processes. In: Additive Manufacturing. Netherlands: Elsevier. p181–213. https://doi.org/10.1016/b978-0-12-812155-9.00006-2
44. Jiang R, Kleer R, Piller FT, 2017, Predicting the Future of Additive Manufacturing: A Delphi Study on Economic and Societal Implications of 3D Printing for 2030. Technol Forecast Soc Change, 117:84–97. https://doi.org/10.1016/j.techfore.2017.01.006
45. Singh S, Ramakrishna S, Singh R, 2017, Material Issues in Additive Manufacturing: A Review. J Manuf Process, 25:185–200. https://doi.org/10.1016/j.jmapro.2016.11.006
46. Oliveira JP, LaLonde AD, Ma J, 2020, Processing Parameters in Laser Powder Bed Fusion Metal Additive Manufacturing. Mater Des, 193:108762. https://doi.org/10.1016/j.matdes.2020.108762
47. Kusoglu IM, Doñate-Buendía C, Barcikowski S, et al., 2021, Laser Powder Bed Fusion of Polymers: Quantitative Research Direction Indices. Materials, 14:1169. https://doi.org/10.3390/ma14051169
48. Goh GD, Yap YL, Tan HK, et al., 2020, Process-structure properties in Polymer Additive Manufacturing Via Material Extrusion: A Review. Crit Rev Solid State Mater Sci, 45:113–33. https://doi.org/10.1080/10408436.2018.1549977
49. Spoerk M, Holzer C, Gonzalez-Gutierrez J, 2020, Material Extrusion-based Additive Manufacturing of Polypropylene: A Review on How to Improve Dimensional Inaccuracy and Warpage. J Appl Polym Sci, 137:48545. https://doi.org/10.1002/app.48545
50. Thompson MK, Moroni G, Vaneker T, et al., 2016, Design for Additive Manufacturing: Trends, Opportunities, Considerations, and Constraints. CIRP Ann., 65:737–60. https://doi.org/10.1016/j.cirp.2016.05.004
51. Gebler M, Uiterkamp AJ, Visser C, 2014, A Global Sustainability Perspective on 3D Printing Technologies. Energy Policy, 74:158–67. https://doi.org/10.1016/j.enpol.2014.08.033
52. Ford S, Despeisse M, 2016, Additive Manufacturing and Sustainability: An Exploratory Study of the Advantages and Challenges. J Clean Prod, 137:1573–87. https://doi.org/10.1016/j.jclepro.2016.04.150
53. Colorado HA, Velásquez EI, Monteiro SN, 2020, Sustainability of Additive Manufacturing: The Circular Economy of Materials and Environmental Perspectives. J Mater Res Technol, 9:8221–34. https://doi.org/10.1016/j.jmrt.2020.04.062
54. Pour MA, Zanardini M, Bacchetti A, et al., 2016, Additive Manufacturing Impacts on Productions and Logistics Systems. IFAC PapersOnLine, 49:1679–84. https://doi.org/10.1016/j.ifacol.2016.07.822
55. Moradlou H, Roscoe S, Ghadge A, 2020, Buyer-supplier Collaboration during Emerging Technology Development. Prod Plan Control, 33:1–16. https://doi.org/10.1080/09537287.2020.1810759
56. Javaid M, Haleem A, 2018, Additive Manufacturing Applications in Medical Cases: A Literature Based Review. Alex J Med, 54:411–22. https://doi.org/10.1016/j.ajme.2017.09.003
57. McDonough JR, 2020, A Perspective on the Current and Future Roles of Additive Manufacturing in Process Engineering, with an Emphasis on Heat Transfer. Therm Sci Eng Prog, 19:100594. https://doi.org/10.1016/j.tsep.2020.100594
58. Conner BP, Manogharan GP, Martof AN, et al., 2014, Making Sense of 3-D Printing: Creating a Map of Additive Manufacturing Products and Services. Addit Manuf, 1:64–76. https://doi.org/10.1016/j.addma.2014.08.005
59. Shahrubudin N, Ramlan R, 2019, An Overview of Critical Success Factors for Implementing 3D Printing Technology in Manufacturing Firms. J Appl Eng Sci, 17:379–85. https://doi.org/10.5937/jaes17-21526
60. Everton SK, Hirsch M, Stravroulakis P, et al., 2016, Review of in-situ Process Monitoring and in-situ Metrology for Metal Additive Manufacturing. Mater Des, 95:431–45. https://doi.org/10.1016/j.matdes.2016.01.099
61. Gustavo T, Elwany A, 2014, A Review on Process Monitoring and Control in Metal-based Additive Manufacturing. J Manuf Sci Eng, 136:060801.
62. Di Prima M, Coburn J, Hwang D, et al., 2016, Additively Manufactured Medical Products-the FDA Perspective. 3D Print Med, 2:1–6. https://doi.org/10.1186/s41205-016-0005-9
63. Chekurov S, Metsä-Kortelainen S, Salmi M, et al., 2018, The Perceived Value of Additively Manufactured Digital Spare Parts in Industry: An Empirical Investigation. Int J Prod Econ, 205:87–97. https://doi.org/10.1016/j.ijpe.2018.09.008
64. Tavassoli S, Brandt M, Qian M, et al., 2020, Adoption and Diffusion of Disruptive Technologies: The Case of Additive Manufacturing in Medical Technology Industry in Australia. Proc Manuf, 43:18–24. https://doi.org/10.1016/j.promfg.2020.02.103
65. McCann R, Obeidi MA, Hughes C, et al., 2021, In-situ Sensing, Process Monitoring and Machine Control in Laser Powder Bed Fusion: A review. Addit Manuf, 102058. https://doi.org/10.1016/j.addma.2021.102058
66. Molaei R, Fatemi A, 2018, Fatigue Design with Additive Manufactured Metals: Issues to Consider and Perspective for Future Research. Proc Eng., 213:5–16. https://doi.org/10.1016/j.proeng.2018.02.002
67. Becker TH, Kumar P, Ramamurty U, 2021, Fracture and Fatigue in Additively Manufactured Metals. Acta Mater, 219:117240. https://doi.org/10.1016/j.actamat.2021.117240
68. Strano G, Hao L, Everson RM, et al., 2013, Surface Roughness Analysis, Modelling and Prediction in Selective Laser Melting. J Mater Process Technol, 213:589–97. https://doi.org/10.1016/j.jmatprotec.2012.11.011
69. Hoejin K, Yirong Lin Y, Tseng TL, 2018, A Review on Quality Control in Additive Manufacturing. Rapid Prototyp J, 45:102058.
70. Nancharaiah TR, Raju DR, Raju VR, 2010, An Experimental Investigation on Surface Quality and Dimensional Accuracy of FDM Components. Int J Emerg Technol, 1:106–11.
71. Yasa E, Poyraz O, Solakoglu EU, et al., 2016, A Study on the Stair Stepping Effect in Direct Metal Laser Sintering of a Nickel-based Superalloy. Proc CIRP, 45:175–8. https://doi.org/10.1016/j.procir.2016.02.068
72. Chen Z, Xiang Y, Wei Z, et al., 2018, Thermal Dynamic Behavior during Selective Laser Melting of K418 Superalloy: Numerical Simulation and Experimental Verification. Appl Phyis A, 124:1–16. https://doi.org/10.1007/s00339-018-1737-8
73. Pal S L, Ojen G, Hudak R, et al., 2020, As-fabricated Surface Morphologies of Ti-6Al-4V Samples Fabricated by Different Laser Processing Parameters in Selective Laser Melting. Addit Manuf, 33:101147. https://doi.org/10.1016/j.addma.2020.101147
74. Zhang L, Zhu H, Liu J, et al., 2018, Track Evolution and Surface Characteristics of Selective Laser Melting Ti6Al4V. Rapid Prototyp J, 24:1554–62.
75. Maleki E, Bagherifard S, Bandini M, et al., 2020, Surface Post-treatments for Metal Additive Manufacturing: Progress, Challenges, and Opportunities. Addit Manuf, 37:101619. https://doi.org/10.1016/j.addma.2020.101619
76. Qiu C, Fones A, Hamilton HG, et al., 2016, A New Approach to Develop Palladium-modified Ti-based Alloys for Biomedical Applications. Mater Des, 109:98–111. https://doi.org/10.1016/j.matdes.2016.07.055
77. Hedayati R, Sadighi M, Mohammadi-Aghdam M, et al., 2018, Comparison of Elastic Properties of Open-cell Metallic Biomaterials with Different Unit Cell Types. J Biomed Mater Res B, 106:386–98. https://doi.org/10.1002/jbm.b.33854
78. Deing A, Luthringer B, Laipple D, et al., 2014, A Porous TiAl6V4 Implant Material for Medical Application. Int J Biomater, 2014:904230 https://doi.org/10.1155/2014/904230
79. Maietta S, Gloria A, Improta G, et al., 2019, A Further Analysis on Ti6Al4V Lattice Structures Manufactured by Selective Laser Melting. J Healthc Eng, 2019:3212594. https://doi.org/10.1155/2019/3212594