Development and Biomechanical Evaluation of an Anatomical 3D Printing Modularized Proximal Inter-Phalangeal Joint Implant Based on the Computed Tomography Image Reconstructions
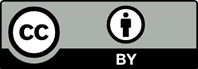
In this study, we developed a modularized proximal interphalangeal (PIP) joint implant that closely resembles the anatomical bone articular surface and cavity contour based on computed tomography (CT) image reconstruction. Clouds of points of 48 groups reconstructed phalanx articular surfaces of CT images, including the index, middle, ring, and little fingers, were obtained and fitted to obtain the articular surface using iterative closest points algorithm. Elliptical-cone stems, including the length, the major and minor axis at the stem metaphyseal/diaphyseal side for the proximal and middle phalanxes, were designed. The resurfacing PIP joint implant components included the bi-condylar surface for the proximal phalanx with elliptical-cone stem, ultra-high molecular weight polyethylene bi-concave articular surface for middle phalanx with hook mechanism, and the middle phalanx with elliptical-cone stem. Nine sets of modularized designs were made to meet the needs of clinical requirements and the weakness structure from the nine sets, that is, the worst structure case combination was defined and manufactured using titanium alloy three-dimensional (3D) printing. Biomechanical tests including anti-loosening pull-out strength for the proximal phalanx, elliptical-cone stem, and articular surface connection strength for the middle phalanx, and static/dynamic (25000 cycles) dislocation tests under three daily activity loads for the PIP joint implant were performed to evaluate the stability and anti-dislocation capability. Our experimental results showed that the pull-out force for the proximal phalanx implant was 727.8N. The connection force for the hook mechanism to cone stem of the middle phalanx was 49.9N and the hook mechanism was broken instead of stem pull out from the middle phalanx. The static dislocation forces/dynamic fatigue limits (pass 25000 cyclic load) of daily activities for piano-playing, pen-writing, and can-opening were 525.3N/262.5N, 316.0N/158N, and 115.0N/92N, respectively, and were higher than general corresponding acceptable forces of 19N, 17N, and 45N from the literatures. In conclusion, our developed modularized PIP joint implant with anatomical articular surface and elliptical-cone stem manufactured by titanium alloy 3D printing could provide enough joint stability and the ability to prevent dislocation.
1. Yamamoto M, 2017, A Systematic Review of Different Implants and Approaches for Proximal Interphalangeal Joint Arthroplasty. Plast Reconstr Surg, 139:1139e–51. https://doi.org/10.1097/prs.0000000000003260
2. Lans J, 2019. Factors Associated with Reoperation after Silicone Proximal Interphalangeal Joint Arthroplasty. Hand, 15:674–8. https://doi.org/10.1177/1558944719864453
3. Srnec JJ, 2017, Implant Arthroplasty for Proximal Interphalangeal, Metacarpophalangeal, and
Trapeziometacarpal Joint Degeneration. J Hand Surg Am, 42:817–25. https://doi.org/10.1016/j.jhsa.2017.07.030
4. Bales JG, 2014, Long-Term Results of Swanson Silicone Arthroplasty for Proximal Interphalangeal Joint Osteoarthritis. J Hand Surg Am, 39:455–61. https://doi.org/10.1016/j.jhsa.2013.11.008
5. Selig HF, 2020, Outcome of Proximal Interphalangeal Joint Replacement with Pyrocarbon Implants: A Long-Term Longitudinal Follow-up Study. Arch Orthop Trauma Surg, 140:1847–57. https://doi.org/10.1007/s00402-020-03592-3
6. Zaeri A, Cao K, Zhang FC, et al., 2022, A Review of the Structural and Physical Properties that Govern Cell Interactions with Structured Biomaterials Enabled by Additive Manufacturing. Bioprinting, 26:e0020. https://doi.org/10.1016/j.bprint.2022.e00201
7. Aversano FJ, 2018, Salvaging a Failed Proximal Interphalangeal Joint Implant. Hand Clin, 34:217–27. https://doi.org/10.1016/j.hcl.2017.12.011
8. Griffart A, 2019, Arthroplasty of the Proximal Interphalangeal Joint with the Tactys Modular Prosthesis: Results in Case of Index Finger and Clinodactyly. Hand Surg Rehabil, 38:179–85. https://doi.org/10.1016/j.hansur.2019.03.001
9. Ying H, 2017, An Iterative Closest Points Algorithm for Registration of 3D Laser Scanner Point Clouds with Geometric Features. Sensors, 17:1862. https://doi.org/10.3390/s17081862
10. Li CH, Wu CH, Lin CL, 2020, Design of a Patient-Specific Mandible Reconstruction Implant with Dental Prosthesis for Metal 3D Printing Using Integrated Weighted Topology Optimization and Finite Element Analysis. J Mech Behav Biomed Mater, 105:103700. https://doi.org/10.1016/j.jmbbm.2020.103700
11. Butz KD, 2012, A Biomechanical Analysis of Finger Joint Forces and Stresses Developed during Common Daily Activities. Comput Methods Biomech Biomed Eng, 15:131–40. https://doi.org/10.1080/10255842.2010.517525
12. Purves WK, 1980, Resultant Finger Joint Loads in Selected Activities. J Biomed Eng, 2:285–9.
13. Completo A, 2018, Biomechanical Evaluation of Pyrocarbon Proximal Interphalangeal Joint Arthroplasty: An In-Vitro Analysis. Clin Biomech, 52:72–8. https://doi.org/10.1016/j.clinbiomech.2018.01.005
14. Lin CL, Wang YT, Chang CM, et al., 2022, Design Criteria for Patient-specific Mandibular Continuity Defect Reconstructed Implant with Lightweight Structure using Weighted Topology Optimization and Validated with Biomechanical Fatigue Testing. Int J Bioprint, 8:437. https://doi.org/10.18063/ijb.v8i1.437
15. Stokoe S, 1990, A Finger Function Simulator and Surface Replacement Prosthesis for the Metacarpo-Phalangeal Joint. PhD Thesis, University of Durham.
16. Joyce TJ, Ash HE, Unsworth A, 1996, The Wear of Cross-linked Polyethylene Against Itself. Proc Inst Mech Eng H, 210:11–6. https://doi.org/10.1243/pime_proc_1996_210_386_02
17. Hara D, Nakashima Y, Sato T, et al., 2016, Bone Bonding Strength of Diamond-structured Porous Titanium-alloy Implants Manufactured Using the Electron Beam-melting Technique. Mater Sci Eng C, 59:1047–52. https://doi.org/10.1016/j.msec.2015.11.025