Computational Fluid Dynamics Assessment of the Effect of Bioprinting Parameters in Extrusion Bioprinting
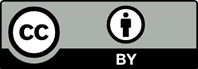
Wall shear stress is the most critical factor in determining the viability of cells during the bioprinting process, and controlling wall shear stress remains a challenge in extrusion bioprinting. We investigated the effect of various bioprinting parameters using computational simulations on maximum wall shear stress (MWSS) in the nozzle to optimize the bioprinting process. Steady-state simulations were done for three nozzle geometries (conical, tapered conical, and cylindrical) with varying nozzle diameters (0.1 mm–0.5 mm) at different inlet pressure (0.025 MPa–0.25 MPa) as inlet conditions. NonNewtonian power law was used to model the bioink rheology and four different bioinks with power-law constants ranging from 0.0863 to 0.5050 were examined. To capture the dynamic behavior of the bioink and the thread profile of the extruded bioink, transient simulations were carried out. Our results indicate that although the MWSS is lowest in the cylindrical nozzle, this stress condition lasts for a longer portion of the nozzle and for the same inlet pressure and nozzle diameter, the mass flow rate is lower compared to the tapered conical and conical nozzle, contributing to lower cell viability.
1. Vijayavenkataraman S, Yan WC, Lu WF, et al., 2018, 3D Bioprinting of Tissues and Organs for Regenerative Medicine. Adv Drug Deliv Rev, 132:296–332. https://doi.org/10.1016/j.addr.2018.07.004
2. Magalhães IP, Oliveira PM, Dernowsek J, et al., 2019, Investigation of the Effect of Nozzle Design on Rheological Bioprinting Properties Using Computational Fluid Dynamics. Matéria (Rio de Janeiro), 24:714. https://doi.org/10.1590/s1517-707620190003.0714
3. Wang Z, Abdulla R, Parker B, et al., 2015, A Simple and High resolution Stereolithography-based 3D Bioprinting System Using Visible Light Crosslinkable Bioinks. Biofabrication, 7:045009. https://doi.org/10.1088/1758-5090/7/4/045009
4. Zhang J, Wehrle E, Rubert M, et al., 2021, 3D Bioprinting of Human Tissues: Biofabrication, Bioinks, and Bioreactors. Int J Mol Sci, 22:3971. https://doi.org/10.3390/ijms22083971
5. Biazar E, Najafi SM, Heidari KS, et al., 2018, 3D Bio-printing Technology for Body Tissues and Organs Regeneration. J Med Eng Technol, 42:187–202. https://doi.org/10.1080/03091902.2018.1457094
6. Boularaoui S, Al Hussein G, Khan KA, et al., 2020, An Overview of Extrusion-based Bioprinting with a Focus on Induced Shear Stress and its Effect on Cell Viability. Bioprinting, 20:e00093.
7. Bahrd A, 2017, Computational Fluid Dynamics and Quantitative Cell Viability Measurements in Dispensing-Based Biofabrication. p. 37.
8. Gómez-Blanco JC, Mancha-Sánchez E, Marcos AC, et al., Bioink Temperature Influence on Shear Stress, Pressure and Velocity Using Computational Simulation. Processes, 8:865.
9. Emmermacher J, Spura D, Cziommer J, et al., 2020, Engineering Considerations on Extrusion-based Bioprinting: Interactions of Material Behavior, Mechanical Forces and Cells in the Printing Needle. Biofabrication, 12:025022.
10. Göhl J, Markstedt K, Mark A, et al., 2018, Simulations of 3D Bioprinting: Predicting Bioprintability of Nanofibrillar Inks. Biofabrication, 10:034105. https://doi.org/10.1088/1758-5090/aac872
11. Gómez-Blanco JC, Mancha-Sánchez E, Ortega-Morán JF, et al., 2020, Computational Fluid Dynamics Study of Inlet Velocity on Extrusion-Based Bioprinting. in XV Mediterranean Conference on Medical and Biological Engineering and Computing MEDICON 2019. Cham: Springer International Publishing.
12. Reina-Romo E, Mandal S, Amorim P, et al., 2021, Towards the Experimentally-Informed In Silico Nozzle Design Optimization for Extrusion-Based Bioprinting of Shear-Thinning Hydrogels. Front Bioeng Biotechnol, 9:701778. https://doi.org/10.3389/fbioe.2021.701778
13. Gillispie G, Prim P, Copus J, et al., 2020, Assessment Methodologies for Extrusion-Based Bioink Printability. Biofabrication, 12:022003. https://doi.org/10.1088/1758-5090/ab6f0d
14. Rapp BE, 2016, Fluids, in Microfluidics: Modeling, Mechanics and Mathematics. Amsterdam, Netherlands: Elsevier. p. 250–51.
15. Billiet T, Gevaert E, De Schryver R, et al., 2014, The 3D Printing of Gelatin Methacrylamide Cell-laden Tissue engineered Constructs with High Cell Viability. Biomaterials, 35:49–62. https://doi.org/10.1016/j.biomaterials.2013.09.078
16. Dharmadasa V, 2016, Investigation of Cell-viability in the Bioprinting Process. In: Department of Mechanics. Sweden: KTH Royal Institute of Technology. p. 54.
17. Müller M, Öztürk E, Arlov O, et al., 2017, Alginate Sulfate Nanocellulose Bioinks for Cartilage Bioprinting Applications. Ann Biomed Eng, 45:210–23. https://doi.org/10.1007/s10439-016-1704-5
18. Markstedt K, Mantas A, Tournier I, et al., 2015, 3D Bioprinting Human Chondrocytes with Nanocellulose-Alginate Bioink for Cartilage Tissue Engineering Applications. Biomacromolecules, 16:1489–96.
19. Wu Y, Wenger A, Golzar H, et al., 2020, 3D Bioprinting of Bicellular Liver Lobule-mimetic Structures via Microextrusion of Cellulose Nanocrystal-incorporated Shear thinning Bioink. Sci Rep, 10:77146. https://doi.org/10.1038/s41598-020-77146-3
20. Pössl A, 2021, A Targeted Rheological Bioink Development Guideline and its Systematic Correlation with Printing Behavior. Biofabrication, 13:035021.
21. Paxton N, Smolan W, Böck T, et al., 2017, Proposal to Assess Printability of Bioinks for Extrusion-based Bioprinting and Evaluation of Rheological Properties Governing Bioprintability. Biofabrication, 9:044107. https://doi.org/10.1088/1758-5090/aa8dd8
22. Webb B, Doyle BJ, 2017, Parameter Optimization for 3D Bioprinting of Hydrogels. Bioprinting, 8, 8–12.
23. Talluri DJ, 2021, Numerical Modeling of the Fiber Deposition Flow in Extrusion-Based 3D Bioprinting. Rowan University, Ann Arbor. p. 103.
24. Liu W, Heinrich MA, Zhou Y, et al., 2017, Extrusion Bioprinting of Shear‐Thinning Gelatin Methacryloyl Bioinks. Adv Healthc Mater, 6:1601451. https://doi.org/10.1002/adhm.201601451
25. Kraynak J, 2021, Minimizing Cell Death During the Extrusion Bioprinting of Gelatin-Alginate Bioinks. Temple University, Libraries.
26. Anandan A, Courtial EJ, Lemarié L, et al., 2020, Rheology, Simulation and Data Analysis toward Bioprinting Cell Viability Awareness. Bioprinting, 21:e00119. https://doi.org/10.1016/j.bprint.2020.e00119
27. Li M, Tian X, Schreyer DJ, et al., 2011, Effect of Needle Geometry on Flow Rate and Cell Damage in the Dispensing based Biofabrication Process. Biotechnol Prog, 27:1777–84. https://doi.org/10.1002/btpr.679
28. Udofia E, Zhou W, 2018, Microextrusion Based 3D Printing a Review. In: Solid Freeform Fabrication 2018: Proceedings of the 29th Annual International Solid Freeform Fabrication Symposium an Additive Manufacturing Conference, Austin, TX.
29. Blaeser A, Campos DF, Puster U, et al., 2016, Controlling Shear Stress in 3D Bioprinting is a Key Factor to Balance Printing Resolution and Stem Cell Integrity. Adv Healthc Mater, 5:326–33. https://doi.org/10.1002/adhm.201500677
30. Chang R, Sun W, 2008, Effects of Dispensing Pressure and Nozzle Diameter on Cell Survival from Solid Freeform Fabrication-based Direct Cell Writing. Tissue Eng Part A, 14:41–48. https://doi.org/10.1089/ten.a.2007.0004
31. Nair K, Gandhi M, Khalil S, et al., 2009, Characterization of Cell Viability during Bioprinting Processes. Biotechnol J, 4:1168–77.https://doi.org/10.1002/biot.200900004
32. Hölzl K, Lin S, Tytgat L, et al., 2016, Bioink Properties before, during and after 3D Bioprinting. Biofabrication, 8:032002. https://doi.org/10.1088/1758-5090/8/3/032002