Fatigue behavior of additively manufactured Ti3Al2V alloy
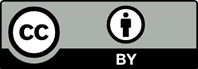
In this study, we measured the tensile, compression, and fatigue behavior of additively manufactured Ti3Al2V as a function of build orientation. Ti3Al2V alloy was prepared by mixing commercially pure titanium and Ti6Al4V in 1:1 wt. ratio. Laser powder bed fusion-based additive manufacturing technique was used to fabricate the samples. Tensile tests resulted in an ultimate strength of 989 ± 8 MPa for Ti3Al2V. Ti6Al4V 90° orientation samples showed a compressive yield strength of 1178 ± 33 MPa and that for Ti3Al2V 90° orientation samples were 968 ± 24 MPa. By varying the build orientation to account for anisotropy, Ti32 45° and Ti32 0° samples displayed almost similar compressive yield strength values of 1071 ± 16 and 1051 ± 18 MPa, respectively, which were higher than that of Ti32 90° sample. Fatigue loading revealed an endurance limit (10 million cycles) of 250 MPa for Ti6Al4V and of 219 MPa for Ti3Al2V built at 90° orientation. The effect of the build orientation was significant under fatigue loading; Ti3Al2V built at 45° and 0° orientations displayed endurance limits of 387.5 MPa and 512 MPa, respectively; more than two-fold increment in endurance limit was observed. In conclusion, the superior attributes of Ti3Al2V alloy over Ti6Al4V alloy, as demonstrated in this study, justify its potential in load-bearing applications, particularly for use in orthopedic devices.
- Bose S, Ke D, Sahasrabudhe H, et al., 2018, Additive manufacturing of biomaterials. Prog Mater Sci, 93: 45–11. https://doi.org/10.1016/j.pmatsci.2017.08.003
- Bandyopadhyay A, Mitra I, Avila JD, et al., 2023, Porous metal implants: Processing, properties, and challenges. Int J Extrem Manuf, 5: 032014. https://doi.org/10.1088/2631-7990/acdd35
- Chen LY, Cui YW, Zhang LC, 2020, Recent development in beta titanium alloys for biomedical applications. Metals, 10: 1139. https://doi.org/10.3390/met10091139
- Bandyopadhyay A, Traxel KD, Lang M, et al., 2022, Alloy design via additive manufacturing: Advantages, challenges, applications and perspectives. Mater Today, 52: 207–224. https://doi.org/10.1016/j.mattod.2021.11.026
- Liu S, Shin YC, 2019, Additive manufacturing of Ti6Al4V alloy: A review. Mater Des, 164: 107552. https://doi.org/10.1016/j.matdes.2018.107552
- Ciliveri S, Bandyopadhyay A, 2023, Understanding the influence of alloying elements on the print quality of powder bed fusion-based metal additive manufacturing: Ta and Cu addition to Ti alloy. Virtual Phys Prototyp, 18: e2248464. https://doi.org/10.1080/17452759.2023.2248464
- Han CH, Johansson CB, Wennerberg A, et al., 1998, Quantitative and qualitative investigations of surface enlarged titanium and titanium alloy implants. Clin Oral Implants Res, 9: 1–10. https://doi.org/10.1034/j.1600-0501.1998.090101.x
- Johansson CB, Lausmaa J, Röstlund T, et al., 1993, Commercially pure titanium and Ti6AI4V implants with and without nitrogen-ion implantation: Surface characterization and quantitative studies in rabbit cortical bone. J Mater Sci Mater Med, 4: 132–141. https://doi.org/10.1007/BF00120382
- Yavari SA, Wauthle R, van der Stok J, et al., 2013, Fatigue behavior of porous biomaterials manufactured using selective laser melting. Mater Sci Eng C, 33: 4849–4858. https://doi.org/10.1016/j.msec.2013.08.006
- Bandyopadhyay A, Upadhyayula M, Traxel KD, et al., 2019, Influence of deposition orientation on fatigue response of LENS™ processed Ti6Al4V. Mater Lett, 255: 126541. https://doi.org/10.1016/j.matlet.2019.126541
- Benedetti M, Cazzolli M, Fontanari V, et al., 2016, Fatigue limit of Ti6Al4V alloy produced by selective laser sintering. Proc Struct Integr, 2: 3158–3167. https://doi.org/10.1016/j.prostr.2016.06.394
- Mitra I, Bose S, Dernell WS, et al., 2021, 3D printing in alloy design to improve biocompatibility in metallic implants. Mater Today, 45: 20–34. https://doi.org/10.1016/j.mattod.2020.11.021
- Bandyopadhyay A, Espana F, Balla VK, et al., 2010, Influence of porosity on mechanical properties and in vivo response of Ti6Al4V implants. Acta Biomater, 6: 1640–1648. https://doi.org/10.1016/j.actbio.2009.11.011
- Bandyopadhyay A, Mitra I, Goodman SB, et al., 2023, Improving biocompatibility for next generation of metallic implants. Prog Mater Sci, 133: 101053. https://doi.org/10.1016/j.pmatsci.2022.101053
- Sing SL, 2022, Perspectives on additive manufacturing enabled beta-titanium alloys for biomedical applications. Int J Bioprint, 8: 478. https://doi.org/10.18063/ijb.v8i1.478
- Zhang T, Liu CT, 2022, Design of titanium alloys by additive manufacturing: A critical review. Adv Powder Mater, 1: 100014. https://doi.org/10.1016/j.apmate.2021.11.001
- Lin CW, Ju CP, Lin JH, 2005, A comparison of the fatigue behavior of cast Ti-7.5Mo with c.p. titanium, Ti-6Al-4V and Ti-13Nb-13Zr alloys. Biomaterials, 26: 2899–2907. https://doi.org/10.1016/j.biomaterials.2004.09.007
- Akahori T, Niinomi M, Fukui H, et al., 2005, Improvement in fatigue characteristics of newly developed beta type titanium alloy for biomedical applications by thermo-mechanical treatments. Mater Sci Eng C, 25: 248–254. https://doi.org/10.1016/j.msec.2004.12.007
- Niinomi M, 2008, Mechanical biocompatibilities of titanium alloys for biomedical applications. J Mech Behav Biomed Mater, 1: 30–42. https://doi.org/10.1016/j.jmbbm.2007.07.001
- Standard Specification for Wrought Titanium-13 Niobium-13 Zirconium Alloy for Surgical Implant Applications (UNS R58130). Available from: https:// www.astm.org/f1713-08r21e01.html [Last accessed on 2022 May 06].
- Ho WF, Ju CP, Lin JH, 1999, Structure and properties of cast binary Ti-Mo alloys. Biomaterials, 20: 2115–2122. https://doi.org/10.1016/S0142-9612(99)00114-3
- Ciliveri S, Bandyopadhyay A, 2021, Influence of strut-size and cell-size variations on porous Ti6Al4V structures for load-bearing implants. J Mech Behav Biomed Mater, 126: 105023. https://doi.org/10.1016/j.jmbbm.2021.105023
- Sterling AJ, Torries B, Shamsaei N, et al., 2016, Fatigue behavior and failure mechanisms of direct laser deposited Ti–6Al–4V. Mater Sci Eng A, 655: 100–112. https://doi.org/10.1016/j.msea.2015.12.026
- Bandyopadhyay A, Zhang Y, Bose S, 2020, Recent developments in metal additive manufacturing. Curr Opin Chem Eng, 28: 96–104. https://doi.org/10.1016/j.coche.2020.03.001
- Chua C, Sing SL, Chua CK, 2023, Characterisation of in-situ alloyed titanium-tantalum lattice structures by laser powder bed fusion using finite element analysis. Virtual Phys Prototyp, 18: e2138463. https://doi.org/10.1080/17452759.2022.2138463
- Yang J Gao H, Zhang D, et al., 2021, Static compressive behavior and material failure mechanism of trabecular tantalum scaffolds fabricated by laser powder bed fusion-based additive manufacturing. Int J Bioprint, 8: 438. https://doi.org/10.18063/ijb.v8i1.438
- Bandyopadhyay A, Ciliveri S, Bose S, 2022, Metal additive manufacturing for load-bearing implants. J Indian Inst Sci, 102: 561–584. https://doi.org/10.1007/s41745-021-00281-x
- Haleem A, Javaid M, 2019, 3D scanning applications in medical field: A literature-based review. Clin Epidemiol Glob Health, 7: 199–210. https://doi.org/10.1016/j.cegh.2018.05.006
- ISO. 14:00-17:00, ISO/ASTM 52909:2022. Available from: https://www.iso.org/standard/74639.html [Last accessed on 2023 Aug 16].
- Standard Test Methods of Compression Testing of Metallic Materials at Room Temperature. Available from: https://www.astm.org/e0009-19.html [Last accessed on 2023 Jan 20].
- ISO. 14:00-17:00, ISO 1143:2021. Available from: https:// www.iso.org/standard/79575.html [Last accessed on 2023 Sep 10].
- ISO. 14:00-17:00, ISO 5832-3:2021. Available from: https:// www.iso.org/standard/79626.html [Last accessed on 2023 Jul 23].
- Carroll BE, Palmer TA, Beese AM, 2015, Anisotropic tensile behavior of Ti-6Al-4V components fabricated with directed energy deposition additive manufacturing. Acta Mater, 87: 309–320. https://doi.org/10.1016/j.actamat.2014.12.054
- Wang F, Mei J, Jiang H, et al., 2007, Laser fabrication of Ti6Al4V/TiC composites using simultaneous powder and wire feed. Mater Sci Eng A, 445–446: 461–466. https://doi.org/10.1016/j.msea.2006.09.093
- Alcisto J, Enriquez A, Garcia H, et al., 2011, Tensile properties and microstructures of laser-formed Ti-6Al-4V. J Materi Eng Perform, 20: 203–212. https://doi.org/10.1007/s11665-010-9670-9
- Dinda GP, Song L, Mazumder J, 2008, Fabrication of Ti-6Al-4V scaffolds by direct metal deposition. Metall Mater Trans A, 39: 2914–2922. https://doi.org/10.1007/s11661-008-9634-y
- Galarraga H, Warren RJ, Lados DA, et al., 2017, Effects of heat treatments on microstructure and properties of Ti-6Al-4V ELI alloy fabricated by electron beam melting (EBM). Mater Sci Eng A, 685: 417–428. https://doi.org/10.1016/j.msea.2017.01.019
- Wysocki B, Maj P, Sitek R, et al., 2017, Laser and electron beam additive manufacturing methods of fabricating titanium bone implants. Appl Sci, 7: 657. https://doi.org/10.3390/app7070657
- Edwards P, O’Conner A, Ramulu M, 2013, Electron beam additive manufacturing of titanium components: Properties and performance. J Manuf Sci Eng, 135: 061016. https://doi.org/10.1115/1.4025773
- Chastand V, Quaegebeur P, Maia W, et al., 2018, Comparativestudy of fatigue properties of Ti-6Al-4V specimens built by electron beam melting (EBM) and selective laser melting (SLM). Mater Charact, 143: 76–81. https://doi.org/10.1016/j.matchar.2018.03.028
- Hollander DA, von Walter M, Wirtz T, et al., 2006, Structural, mechanical and in vitro characterization of individually structured Ti-6Al-4V produced by direct laser forming. Biomaterials, 27: 955–963. https://doi.org/10.1016/j.biomaterials.2005.07.041
- Facchini L, Magalini E, Robotti P, et al., 2010, Ductility of a Ti-6Al-4V alloy produced by selective laser melting of prealloyed powders. Rapid Prototyp J, 16: 450–459. https://doi.org/10.1108/13552541011083371
- Vilaro T, Colin C, Bartout JD, 2011, As-fabricated and heat-treated microstructures of the Ti-6Al-4V alloy processed by selective laser melting. Metall Mater Trans A, 42: 3190–3199. https://doi.org/10.1007/s11661-011-0731-y
- Yu W, Xiao Z, Zhang X, et al., 2022, Processing and characterization of crack-free 7075 aluminum alloys with elemental Zr modification by laser powder bed fusion. Mater Sci Addit Manuf, 1: 4. https://doi.org/10.18063/msam.v1i1.4
- Zhang X, Xiao Z, Yu W, et al., 2022, Influence of erbium addition on the defects of selective laser-melted 7075 aluminium alloy. Virtual Phys Prototyp, 17: 406–418. https://doi.org/10.1080/17452759.2021.1990358
- Sing SL, Huang S, Goh GD, et al., 2021, Emerging metallic systems for additive manufacturing: In-situ alloying and multi-metal processing in laser powder bed fusion. Prog Mater Sci, 119: 100795. https://doi.org/10.1016/j.pmatsci.2021.100795
- Mertova K, Dzugan J, Roudnicka M, 2018, Fatigue properties of SLM-produced Ti6Al4V with various post-processing processes. IOP Conf Ser Mater Sci Eng, 461: 012052. https://doi.org/10.1088/1757-899X/461/1/012052
- Gong H, Rafi K, Gu H, et al., 2015, Influence of defects on mechanical properties of Ti-6Al-4V components produced by selective laser melting and electron beam melting. Mater Des, 86: 545–554. https://doi.org/10.1016/j.matdes.2015.07.147
- Xu W, Sun S, Elambasseril J, et al., 2015, Ti-6Al-4V additively manufactured by selective laser melting with superior mechanical properties. JOM, 67: 668–673. https://doi.org/10.1007/s11837-015-1297-8
- Edwards P, Ramulu M, 2014, Fatigue performance evaluation of selective laser melted Ti-6Al-4V. Mater Sci Eng A, 598: 327–337. https://doi.org/10.1016/j.msea.2014.01.041
- Fatemi A, Molaei R, Sharifimehr S, et al., 2017, Multiaxial fatigue behavior of wrought and additive manufactured Ti-6Al-4V including surface finish effect. Int J Fatigue, 100: 347–366. https://doi.org/10.1016/j.ijfatigue.2017.03.044
- Pegues J, Roach M, Williamson RS, et al., 2018, Surface roughness effects on the fatigue strength of additively manufactured Ti-6Al-4V. Int J Fatigue, 116: 543–552. https://doi.org/10.1016/j.ijfatigue.2018.07.013
- Vayssette B, Saintier N, Brugger C, et al., 2018, Surface roughness of Ti-6Al-4V parts obtained by SLM and EBM: Effect on the high cycle fatigue life. Proc Eng, 213: 89–97. https://doi.org/10.1016/j.proeng.2018.02.010
- Janeček M, Novy F, Harcuba P, et al., 2015, The very high cycle fatigue behaviour of Ti-6Al-4V alloy. Acta Phys Pol Ser A, 128: 497–503. https://doi.org/10.12693/aphyspola.128.497