Considerations about highly crystalline cellulose microfiber additive from Eucalyptus grandis for 3D-printing acrylonitrile butadiene styrene filament
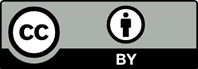
The current work aimed to produce acrylonitrile butadiene styrene (ABS) filament with cellulose microfibers additive for three-dimensional (3D)-printing and perform initial mechanical characterizations. 3D printing is a Fourth Industrial Revolution enabling technology aimed at smart production process. Cellulose is an organic molecule extremely common in nature with potential application as materials reinforcement. Highly crystalline cellulose microfibers were extracted from certified Eucalyptus grandis wood. E. grandis is a species native to Australia, but widely used in reforestation initiatives on a global scale. Cellulose microfiber was inserted at 0.5% in weight into commercial ABS to produce filaments for 3D printing. After the production of pure ABS and ABS with microcellulose filaments, specimens were printed using fused deposition modeling for traction, flexion, and impact tests, in addition to measuring the melt flow index. The results between the two materials were compared, revealing that most of the mechanical properties were similar within the limits of experimental errors, but the strain at break in the traction test was improved in microfibers composite, in addition to an improvement in the elastic modulus and stress at break in flexion test. On melt flow index measurement, both materials were found to be considerably more fluid than the polymer from commercial producer sources. This is an indication that the ABS degraded throughout the process, losing molar mass. However, our work demonstrated that it is possible to add highly crystalline cellulose microfibers to ABS to form filaments for 3D printing.
- Nobre AG, da Silva LPN, de Andrade FRD, 2022, Graphene geology and the fourth industrial revolution. In: Iano Y, Saotome O, Vásquez GLK, et al., editors. Smart Innovation, Systems and Technologies. Switzerland, Cham: Springer. p. 220–226. https://doi.org/10.1007/978-3-031-04435-9_34
- Redwood B, Schaffer F, Garret B, 2018, The 3D Printing Handbook. 1st ed. Amsterdam: Coers and Roest.
- Mohamed OA, Masood SH, Bhowmik JL, 2015, Optimization of fused deposition modeling process parameters: A review of current research and future prospects. Adv Manuf, 3: 42–53. https://doi.org/10.1007/s40436-014-0097-7
- Wickramasinghe S, Do T, Tran P, 2022, Flexural behavior of 3D printed bio-inspired interlocking suture structures. Mater Sci Addit Manuf, 1: 9. https://doi.org/10.18063/msam.v1i2.9
- Serdeczny MP, Comminal R, Mollah MT, et al., 2022, Viscoelastic simulation and optimisation of the polymer flow through the hot-end during filament-based material extrusion additive manufacturing. Virtual Phys Prototyp, 17: 205–219. https://doi.org/10.1080/17452759.2022.2028522
- Moore JD, 1973, Acrylonitrile-butadiene-styrene (ABS)-a review. Composites, 4: 118–130. https://doi.org/10.1016/0010-4361(73)90585-5
- Kulich DM, Gaggar SK, Stepien LR, 2001, Acrylonitrilebutadiene-styrene polymers. In: Encyclopedia of Polymer Science and Technology. Pittsburgh: John Wiley and Sons, Carnegie Mellon University. p. 174–203. https://doi.org/10.1002/0471440264.pst011
- Huang B, Meng S, He H, et al., 2018, Study of processing parameters in fused deposition modeling based on mechanical properties of acrylonitrile-butadiene-styrene filament. Polym Eng Sci, 59: 120–128. https://doi.org/10.1002/pen.24875
- Bradford M, 2018, ‘Eucalyptus grandis’ (Rose gum) in northern Queensland: A species under fire. North Qld Nat, 48: 30–38.
- Meskimen G, Francis JK, 1990, Eucalyptus grandis hill ex maiden. Rose gum eucalyptus. In: Burns RM, Honkala BH, editors. Silvics of North America. Vol. 2. Washington, D.C: UN Department of Agriculture. p. 305–312.
- Morán JI, Alvarez VA, Cyras VP, et al., 2007, Extraction of cellulose and preparation of nanocellulose from sisal fibers. Cellulose, 15: 149–159. https://doi.org/10.1007/s10570-007-9145-9
- Moon RJ, Martini A, Nairn J, et al., 2011, Cellulose nanomaterials review: Structure, properties and nanocomposites. Chem Soc Rev, 40: 3941–3994. https://doi.org/10.1039/C0CS00108B
- Silva DJ, D’Almeida MLO, 2009, Nanocristais de cellulose [Cellulose nanocrystals]. O Papel, 70: 34–52. [Article in Portuguese]
- Silva R, Haraguchi SK, Muniz EC, et al., 2009, Applications of lignocellulosic fibers in polymer chemistry and in composites. Quím Nova, 32: 661–671. https://doi.org/10.1590/S0100-40422009000300010
- Zhang X, Yang H, Chen J, 2018, Life-cycle carbon budget of China’s harvested wood products in 1900-2015. For Policy Econ, 92: 181–192. https://doi.org/10.1016/j.forpol.2018.05.005
- Budzinski M, Bezama A, Thran D, 2020, Estimating the potentials for reducing the impacts on climate change by increasing the cascade use and extending the lifetime of wood products in Germany. Resour Conserv Recycl X, 6: 100034. https://doi.org/10.1016/j.rcrx.2020.100034
- Hurmekoski E, Kunttu J, Heinonen T, et al., 2023, Does expanding wood use in construction and textile markets contribute to climate change mitigation? Renew Sustain Energy Rev, 174: 113152. https://doi.org/10.1016/j.rser.2023.113152
- Blomsma F, Brennan G, 2017, The emergence of circular economy: A new framing around prolonging resource productivity. J Ind Ecol, 21: 603–614. https://doi.org/10.1111/jiec.12603
- Nobre AG, Martínez JAE, Florêncio O, 2021, Mineral nanotechnology in circular economy. In: Iano Y, Saotome O, Kemper G, et al., editors. Smart Innovation, Systems and Technologies. Switzerland, Cham: Springer. p. 342–348. https://doi.org/10.1007/978-3-030-75680-2_26
- Araújo CKD, Salvador R, Piekarski CM, et al., 2019, Circular economy practices on wood panels: A bibliographic analysis. Sustainability, 11: 1057. https://doi.org/10.3390/su11041057
- Shogren R, Wood D, Orts W, et al., 2019, Plant-based materials and transitioning to a circular economy. Sustain Prod Consum, 19: 194–215. https://doi.org/10.1016/j.spc.2019.04.007
- Salem KS, Naithani V, Jameel H, et al., 2020, Lignocellulosic fibers from renewable resources using green chemistry for a circular economy. Glob Chall, 5: 2000065. https://doi.org/10.1002/gch2.202000065
- Marques A, Cunha J, De Meyer A, et al., 2020, Contribution towards a comprehensive methodology for wood-based biomass material flow analysis in a circular economy setting. Forests, 11: 106. https://doi.org/10.3390/f11010106
- Nandy S, Goswami S, Marques A, et al., 2021, Cellulose: A contribution for the zero e-waste challenge. Adv Mater Technol, 6: 2000994. https://doi.org/10.1002/admt.202000994
- Jahan I, Zhang G, Bhuiyan M, et al., 2022, Circular economy of construction and demolition wood waste-a theoretical framework approach. Sustainability, 14: 10478. https://doi.org/10.3390/su141710478
- Uppal N, Pappu A, Gowri VKS, et al., 2022, Cellulosic fibre-based epoxy composites: From bioresources to a circular economy. Ind Crops Prod, 182: 114895. https://doi.org/10.1016/j.indcrop.2022.114895
- Eqbalpour M, Andooz A, Kowsari E, et al., 2023, A comprehensive review on how ionic liquids enhance the pyrolysis of cellulose, lignin, and lignocellulose toward a circular economy. WIREs Energy Environ, 1: e473. https://doi.org/10.1002/wene.473
- Beling RR, 2016, Brazilian Forestry and Timber Yearbook. Santa Cruz do Sul: Editora Gazeta Santa Cruz.
- United Nations, 2021, Forest Products Annual Market Review 2020-2021. Geneva: Food and Agriculture Organization of the United Nations.
- Santana RC, De Barros NF, Leite HG, et al., 2008, Biomass estimation of Brazilian eucalypt plantations. Rev Árvore, 32: 697–706. https://doi.org/10.1590/S0100-67622008000400011
- Schumacher MV, Viera M, 2016, Silvicultura do Eucalipto no Brasil. Santa Maria: Editora da Universidade Federal de Santa Maria.
- Scott DF, Lesch W, 1997, Streamflow responses to afforestation with Eucalyptus grandis and Pinus patula and to felling in the Mokobulaan experimental catchments, South Africa. J Hydrol, 199: 360–377. https://doi.org/10.1016/S0022-1694(96)03336-7
- Zhang D, Zhang J, Yang W, et al., 2012, Effects of afforestation with Eucalyptus grandis on soil physicochemical and microbiological properties. Soil Res, 50: 167–176. https://doi.org/10.1071/SR11104
- Da Silva JRV, Alves PLC, Toledo REB, 2012, Weed control strip influences the initial growth of Eucalyptus grandis. Acta Sci Agron, 34: 29–35. https://doi.org/10.4025/actasciagron.v34i1.12252
- Qu J, Luo C, Zhang Q, et al., 2013, Easy synthesis of graphene sheets from alfalfa plants by treatment of nitric acid. Mater Sci Eng B, 178: 380–382. https://doi.org/10.1016/j.mseb.2013.01.016
- Sanchez M, Terence MC, 2017, Obtenção de Nanocristais de Celulose a Partir de Fontes Alternativas. São Paulo: Editora Laços.
- Borysiak S, Garbarczyk J, 2003, Applying the WAXS method to estimate the supermolecular structure of cellulose fibers after mercerisation. Fibre Text East Eur, 11: 44.
- Teixeira EM, de Oliveira CR, Mattoso LHC, et al., 2010, Cotton nanofibers obtained by different hydrolytic acid conditions. Polímeros, 20: 264–268. https://doi.org/10.1590/S0104-14282010005000046
- Segal L, Creely JJ, Martin AE Jr., et al., 1959, An empirical method for estimating the degree of crystallinity of native cellulose using the X-ray diffractometer. Text Res J, 29: 786–794. https://doi.org/10.1177/004051755902901003
- Park S, Baker JO, Himmel ME, et al., 2010, Cellulose crystallinity index: Measurement techniques and their impact on interpreting cellulase performance. Biotechnol Biofuels, 3: 10. https://doi.org/10.1186/1754-6834-3-10
- Poletto M, Zattera AJ, Forte MMC, et al., 2012, Thermal decomposition of wood: Influence of wood components and cellulose crystallite size. Bioresour Technol, 109: 148–153. https://doi.org/10.1016/j.biortech.2011.11.122
- Mukwaya V, Yu W, AM Asad R, et al., 2017, An environmentally friendly method for the isolation of cellulose nano fibrils from banana rachis fibers. Text Res J, 87: 81–90. https://doi.org/10.1177/0040517515622155