Preliminary investigation on tensile and fatigue properties of Ti6Al4V manufactured by selected laser melting
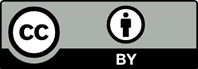
Selective laser melting (SLM) is a promising additive manufacturing method that falls under the category of powder bed fusion (PBF) technology. It has many advantages such as material versatility, efficiency, and the ability to print complex parts without additional machining. However, its surface quality and fatigue properties have been found to be inferior to traditional manufacturing methods. Process-related defects such as pores, incomplete fusion, and un-melted powders give rise to areas of stress concentrations, which lead to mechanical inferiority such as poor fatigue strength. This study aims to investigate and optimize the printing process parameters for Ti6Al4V fabricated by SLM to reduce process-related defects and to investigate their relative density, tensile, and fatigue properties. Ti6Al4V specimens were printed in both 30- and 130-μm layer thicknesses using SLM280 and subjected to tensile and fatigue testing according to ASTM standards. The relative density of Ti6Al4V samples built by 30-µm layer thickness is 99.97 ± 0.02 % (n = 8). The relative density of Ti6Al4V samples built by 130-µm layer thickness is 99.96 ± 0.02 % (n = 8). The average ultimate tensile strength (UTS) of specimens with 30-μm layer thickness is 1152.8 ± 23.8 MPa (n = 4). The average UTS of specimens with 130-μm layer thickness is 1075.5 ± 46.8 MPa (n = 4). S/N curve of the fatigue performance of Ti6Al4V samples printed by 30-μm layer thickness was also obtained. Possible factors impacting the tensile property of SLM-produced parts, such as layer thickness, build orientation, and post-process, are discussed in this paper. Furthermore, crack propagation and surface quality were observed using optical microscopes, laser scanning microscopes, and scanning electron microscopes. The findings of this study will contribute to the improvement of SLM-printed Ti6Al4V parts, which can be potentially applied in the aerospace industry, where fatigue strength is critical to ensuring safety.
Chee Kai Chua serves as the Editor-in-Chief of the journal, but did not in any way involve in the editorial and peer-review process conducted for this paper, directly or indirectly.
- Haydar HJ, Al-Deen J, AbidAli AK, et al., 2021, Improved performance of TI6AL4V alloy in biomedical applicationsreview. J Phys Conf Ser, 1973: 012146. https://doi.org/10.1088/1742-6596/1973/1/012146
- Pramanik A, Littlefair G, 2015, Machining of titanium alloy (Ti-6Al-4V)-theory to application. Mach Sci Technol, 19: 1–49. https://doi.org/10.1080/10910344.2014.991031
- Titanium Metal, Editorial by Industrial Quick Search. Available from: https://www.iqsdirectory.com/articles/titanium/titanium-metal.html [Last accessed on 2023 May 04].
- Thijs L, Verhaeghe F, Craeghs T, et al., 2010, A study of the microstructural evolution during selective laser melting of Ti-6Al-4V. Acta Mater, 58: 3303–3312. https://doi.org/10.1016/j.actamat.2010.02.004
- Mareci D, Chelariu R, Gordin DM, et al., 2009, Comparative corrosion study of Ti-Ta alloys for dental applications. Acta Biomater, 5: 3625–3639. https://doi.org/10.1016/j.actbio.2009.05.037
- Elias CN, Lima JNC, Valiev R, et al., 2008, Biomedical applications of titanium and its alloys. JOM, 60: 46–49. https://doi.org/10.1007/s11837-008-0031-1
- Barbas A, Bonnet AS, Lipinski P, et al., 2012, Development and mechanical characterization of porous titanium bone substitutes. J Mech Behav Biomed Mater, 9: 34–44. https://doi.org/10.1016/j.jmbbm.2012.01.008
- Titanium-element Information, Properties and Uses: Periodic Table, Periodic Table-Royal Society of Chemistry. Available from: https://www.rsc.org/periodic-table/element/22/titanium#:~:text=titanium%20is%20as%20strong%20as,to%20withstand%20extremes%20of%20temperature [Last accessed on 2023 May 04].
- Farinia Group, 2015, How can Aerospace Benefit from 3D Printed Titanium Ti6Al4V. Available from: https://www.farinia.com/additive-manufacturing/3d-materials/howcan-aerospace-benefit-from-3d-printed- titanium-ti6al4v [Last accessed on 2023 May 04].
- De Viteri VS, Fuentes E. Titanium and Titanium Alloys as Biomaterials. Intechopen. Available from: https://www.intechopen.com/chapters/44858 [Last accessed on 2023 May 04].
- Wong KV, Hernandez A, 2012, A review of additive manufacturing. ISRN Mech Eng, 2012: 208760. https://doi.org/10.5402/2012/208760
- Sing SL, Yeong WY, Wiria FE, et al., 2017, Direct selective laser sintering and melting of ceramics: A review. Rapid Prototyp J, 23: 611–623. https://doi.org/10.1108/rpj-11-2015-0178
- Kok Y, Tan XP, Wang P, et al., 2017, Anisotropy and heterogeneity of microstructure and mechanical properties in metal additive manufacturing: A critical review. Mater Des, 139: 565–586. https://doi.org/10.1016/j.matdes.2017.11.021
- Jiao L, Chua ZY, Moon SK, et al., 2018, Femtosecond laser produced hydrophobic hierarchical structures on additive manufacturing parts. Nanomaterials (Basel), 8: 601. https://doi.org/10.3390/nano8080601
- Yap CY, Chua CK, Dong ZL, et al., 2015, Review of selective laser melting: Materials and applications. Appl Phys Rev, 2: 041101. https://doi.org/10.1063/1.4935926
- Zhang LC, Attar H, 2015, Selective laser melting of titanium alloys and titanium matrix composites for biomedical applications: A review. Adv Eng Mater, 18: 463–475. https://doi.org/10.1002/adem.201500419
- Tan JHK, Sing SL, Yeong WY, 2020, Microstructure modelling for metallic additive manufacturing: A review. Virtual Phys Prototyp, 15: 87–105. https://doi.org/10.1080/17452759.2019.1677345
- Boyer RR, 1996, An overview on the use of titanium in the aerospace industry. Mater Sci Eng A, 213: 103–114. https://doi.org/10.1016/0921-5093(96)10233-1
- Boyer RR, 1994, Aerospace applications of beta titanium alloys. JOM, 46: 20–23. https://doi.org/10.1007/BF03220743
- Boyer RR, Vassel A, Eylon D, et al., editors, 1994, Aerospace Applications of beta Titanium-keynote Presentation, Beta Titanium Alloys. Warrendale, PA: Societe Francaise de Metallurgie et de Materiaux. p. 253–264.
- Nguyen HD, Pramanik A, Basak AK, et al., 2022, A critical review on additive manufacturing of TI-6AL-4V alloy: Microstructure and mechanical properties. J Mater Res Technol, 18: 4641–4661. https://doi.org/10.1016/j.jmrt.2022.04.055
- Zhang B, Li Y, Bai Q, 2017, Defect formation mechanisms in selective laser melting: A review. Chin J Mech Eng, 30: 515–527. https://doi.org/10.1007/s10033-017-0121-5
- Cheng M, Lu Z, Wu J, et al., 2022, Effect of thermal induced porosity on high-cycle fatigue and very high-cycle fatigue behaviors of hot-isostatic-pressed Ti-6Al-4V powder components. J Mater Sci Technol, 98: 177–185. https://doi.org/10.1016/j.jmst.2021.04.066
- Belan J, Bokůvka O, Uhričik M, et al., 2021, The influence of quenching on fatigue life of Ti6Al4V alloy. IOP Conf Ser Mater Sci Eng, 1178: 012006. https://doi.org/10.1088/1757-899X/1178/1/012006
- Kumar P, Ramamurty U, 2019, Microstructural optimization through heat treatment for enhancing the fracture toughness and fatigue crack growth resistance of selective laser melted Ti-6AL-4V alloy. Acta Mater, 169: 45–59. https://doi.org/10.1016/j.actamat.2019.03.003
- Shipley H, McDonnell D, Culleton M, et al., 2018, Optimisation of process parameters to address fundamental challenges during selective laser melting of Ti-6AL-4V: A review. Int J Mach Tools Manuf, 128: 1–20. https://doi.org/10.1016/j.ijmachtools.2018.01.003
- Important Index and Parameters of 3D Metal Printing, Solize. Available from: https://www.solize.com/en/column/2018/0416 [Last accessed on 2023 May 04].
- ASTM International, 2021, ASTM E466-21: Standard Practice for Conducting Force Controlled Constant Amplitude Axial Fatigue Tests of Metallic Materials. West Conshohocken, PA: ASTM International.
- Simonelli M, Tse YY, Tuck C, 2014, Effect of the build orientation on the mechanical properties and fracture modes of SLM Ti-6AL-4V. Mater Sci Eng A, 616: 1–11. https://doi.org/10.1016/j.msea.2014.07.086
- ASTM International, 2021, ASTM E8-21: Standard Test Methods for Tension Testing of Metallic Materials. West Conshohocken, PA: ASTM International.
- Campanelli SL, Contuzzi N, Ludovico AD, et al., 2014, Manufacturing and characterization of Ti6al4v lattice components manufactured by selective laser melting. Materials (Basel), 7: 4803–4822. https://doi.org/10.3390/ma7064803
- Cardaropoli F, Alfieri V, Caiazzo F, et al., 2012, Dimensional analysis for the definition of the influence of process parameters in selective laser melting of Ti-6Al-4V alloy. Proc Inst Mech Eng Part B J Eng Manuf, 226: 1136–1142. https://doi.org/10.1177/0954405412441885
- Păcurar R, Păcurar A, 2014, Finite element analysis to improve the accuracy of parts made by stainless steel 316L material using selective laser melting technology. Appl Mech Mater, 657: 236–240. https://doi.org/10.4028/www.scientific.net/AMM.657.236
- Scanning Patterns for Selective Laser Melting. Inside Metal Additive Manufacturing. Available from: https://www.insidemetaladditivemanufacturing.com/blog/-scanningpatterns-in-slm [Last accessed on 2023 May 04].
- Kruth JP, Badrossamay M, Yasa E, et al., 2010, Part and Material Properties in Selective Laser Melting of Metals. In: Proceedings of the 16th International Symposium on Electromachining.