Data imputation strategies for process optimization of laser powder bed fusion of Ti6Al4V using machine learning
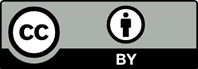
A database linking process parameters and material properties for additive manufacturing enables the performance of the material to be determined based on the process parameters, which are useful in the design and fabrication stage of a product. The data, however, are often incomplete as each individual research work focused on certain process parameters and material properties due to the wide range of variables available. Imputation of missing data is thus required to complete the material library. In this work, we attempt to collate the data of Ti6Al4V, a popular alloy used in aerospace and biomedical industries, fabricated using powder bed fusion, or commonly known as selective laser melting (SLM). Various imputation techniques of missing data of the SLM Ti6Al4V dataset, such as the k-nearest neighbor (kNN), multivariate imputation by chained equations, and graph imputation neural network (GINN) are investigated in this article. It was observed that kNN performed better in imputing variables related to process parameters, whereas GINN performed better in variables related to material properties. To further improve the quality of imputation, a strategy to use the median of the imputed values obtained from the three models has resulted in significant improvement in terms of the relative mean square error. Self-organizing map was used to visualize the relationship among the process parameters and the material properties.
Wai Yee Yeong serves as the Editorial Board Member of the journal, but did not in any way involve in the editorial and peer-review process conducted for this paper, directly or indirectly.
Liu S, Shin YC, 2019, Additive manufacturing of Ti6Al4V alloy: A review. Mater Des, 164: 107552. https://doi.org/10.1016/j.matdes.2018.107552
Elsayed M, Ghazy M, Youssef Y, et al., 2019, Optimization of SLM process parameters for Ti6Al4V medical implants. Rapid Prototyp J, 25: 433–447. https://doi.org/10.1108/rpj-05-2018-0112
Roudnicka M, Bigas J, Vojtech D, 2020, Tuning porosity and mechanical properties of Ti6Al4V alloy additively manufactured by SLM. In: Key Engineering Materials. Vol. 865. Trans Tech Publications, Switzerland, p1–5.
Popovich A, Sufiiarov V, Borisov E, et al., 2015, Microstructure and mechanical properties of Ti-6Al-4V manufactured by SLM. In: Key Engineering Materials. Vol. 651. Trans Tech Publications, Switzerland, p677–682.
Thijs L, Verhaeghe F, Craeghs T, et al., 2010, A study of the microstructural evolution during selective laser melting of Ti-6Al-4V. Acta Mater, 58: 3303–3312. https://doi.org/10.1016/j.actamat.2010.02.004
Kuo C, Su C, Chiang A, 2017, Parametric optimization of density and dimensions in three-dimensional printing of Ti-6Al-4V powders on titanium plates using selective laser melting. Int J Precis Eng Manuf, 18: 1609–1618. https://doi.org/10.1007/s12541-017-0190-5
Pal S, Lojen G, Kokol V, et al., 2018, Evolution of metallurgical properties of Ti-6Al-4V alloy fabricated in different energy densities in the Selective Laser Melting technique. J Manuf Process, 35: 538–546. https://doi.org/10.1016/j.jmapro.2018.09.012
Gong H, Rafi K, Starr T, et al., 2013, The Effects of Processing Parameters on Defect Regularity in Ti-6Al-4V Parts Fabricated by Selective Laser Melting and Electron Beam Melting. In: Conference 24th Annual International Solid Freeform Fabrication Symposium.
Kasperovich G, Haubrich J, Gussone J, et al., 2016, Correlation between porosity and processing parameters in TiAl6V4 produced by selective laser melting. Mater Des, 105: 160–170. https://doi.org/10.1016/j.matdes.2016.05.070
Ali H, Ma L, Ghadbeigi H, et al., 2017, In-situ residual stress reduction, martensitic decomposition and mechanical properties enhancement through high temperature powder bed pre-heating of Selective Laser Melted Ti6Al4V. Mater Sci Eng A, 695: 211–220.
Vilaro T, Colin C, Bartout JD, 2011, As-fabricated and heat-treated microstructures of the Ti-6Al-4V alloy processed by selective laser melting. Metall Mater Trans A, 42: 3190–3199. https://doi.org/10.1007/s11661-011-0731-y
Qiu C, Adkins NJ, Attallah MM, 2013, Microstructure and tensile properties of selectively laser-melted and of HIPed laser-melted Ti-6Al-4V. Mater Sci Eng A, 578: 230–239. https://doi.org/10.1016/j.msea.2013.04.099
Xu Y, Zhang D, Guo Y, et al., 2020, Microstructural tailoring of As-selective Laser melted Ti6Al4V alloy for high mechanical properties. J Alloys Compd, 816: 152536. https://doi.org/10.1016/j.jallcom.2019.152536
Pal S, Gubeljak N, Hudak R, et al., 2019, Tensile properties of selective laser melting products affected by building orientation and energy density. Mater Sci Eng A, 743: 637–647. https://doi.org/10.1016/j.msea.2018.11.130
Sun J, Yang Y, Wang D, 2013, Parametric optimization of selective laser melting for forming Ti6Al4V samples by Taguchi method. Opt Laser Technol, 49: 118–124. https://doi.org/10.1016/j.optlastec.2012.12.002
Bartolomeu F, Faria S, Pinto E, et al., 2016, Predictive models for physical and mechanical properties of Ti6Al4V produced by Selective Laser Melting. Mater Sci Eng A, 663: 181–192. https://doi.org/10.1016/j.msea.2016.03.113
Fotovvati B, Namdari N, Dehghanghadikolaei A, 2018, Fatigue performance of selective laser melted Ti6Al4V components: State of the art. Mater Res Express, 6: 012002. https://doi.org/10.1088/2053-1591/aae10e
Goh GD, Sing SL, Yeong WY, 2020, A review on machine learning in 3D printing: Applications, potential, and challenges. Artif Intell Rev, 54: 63–94. https://doi.org/10.1007/s10462-020-09876-9
Steiner S, Zeng Y, Young TM, et al., 2016, A study of missing data imputation in predictive modeling of a wood-composite manufacturing process. J Qual Technol, 48: 284–296. https://doi.org/10.1080/00224065.2016.11918167
Wang Y, Li K, Gan S, et al., 2019, Missing data imputation with OLS-based autoencoder for intelligent manufacturing. IEEE Trans Ind Appl, 55: 7219–7229. https://doi.org/10.1109/TIA.2019.2940585
Andridge RR, Little RJ, 2010, A review of hot deck imputation for survey non‐response. Int Stat Rev, 78: 40–64. https://doi.org/10.1111/j.1751-5823.2010.00103.x
Jadhav A, Pramod D, Ramanathan K, 2019, Comparison of performance of data imputation methods for numeric dataset. Appl Artif Intell, 33: 913–933. https://doi.org/10.1080/08839514.2019.1637138
Altman NS, 1992, An introduction to Kernel and nearest-neighbor nonparametric regression. Am Stat, 46: 175–185. https://doi.org/10.2307/2685209
Imandoust SB, Bolandraftar M, 2013, Application of K-nearest neighbor (KNN) approach for predicting economic events: Theoretical background. Int J Eng Res Appl, 3: 605–610.
Wilson DR, Martinez TR, 2000, Reduction techniques for instance-based learning algorithms. Mach Learn, 38: 257–286. https://doi.org/10.1023/A:1007626913721
sklearn.impute.KNNImputer-scikit-learn 0.23.2 documentation. Available from: https://scikit-learn.org/stable/modules/generated/sklearn.impute.KNNImputer. html [Last accessed on 2020 Oct 05].
sklearn.metrics.pairwise.nan_euclidean_distances-scikit-learn 0.23.2 documentation. Available from: https://scikit-learn.org/stable/modules/generated/sklearn.metrics. pairwise.nan_euclidean_distances.html [Last accessed on 2020 Oct 05].
Van Buuren S, Groothuis-Oudshoorn K, 2010, Mice: Multivariate imputation by chained equations in R. J Stat Softw, 45: 1–67. https://doi.org/10.18637/jss.v045.i03
Azur MJ, Stuart EA, Frangakis C, et al., 2011, Multiple imputation by chained equations: What is it and how does it work? Int J Methods Psychiatr Res, 20: 40–49. https://doi.org/10.1002/mpr.329
Rubin DB, 1987, Multiple Imputation for Nonresponse in Surveys (Wiley Series in Probability and Statistics). John Wiley and Sons Inc., New York. https://doi.org/10.1002/9780470316696
6.4. Imputation of Missing Values-scikit-learn 0.23.2 Documentation. Available from: https://scikit-learn.org/ stable/modules/impute.html#multiple-vs-singleimputation [Last accessed on 2020 Oct 05].
Shah AD, Bartlett JW, Carpenter J, et al., 2014, Comparison of random forest and parametric imputation models for imputing missing data using MICE: A CALIBER study. Am J Epidemiol, 179: 764–774. https://doi.org/10.1093/aje/kwt312
Spinelli I, Scardapane S, Uncini A, 2020, Missing data imputation with adversarially-trained graph convolutional networks. Neural Netw, 129: 249–260. https://doi.org/10.1016/j.neunet.2020.06.005
Kohonen T, 1982, Self-organized formation of topologically correct feature maps. Biol Cybern, 43: 59–69. https://doi.org/10.1007/BF00337288
Moosavi V, Packmann S, Vallés I, 2014, SOMPY: A Python Library for Self Organizing Map (SOM). Available from: https://www.github.com/sevamoo/sompy [Last accessed on 2020 Oct 05].
Qian J, Nguyen NP, Oya Y, et al., 2019, Introducing self-organized maps (SOM) as a visualization tool for materials research and education. Results Mater, 4: 100020. https://doi.org/10.1016/j.rinma.2019.100020
Nguyen CD, Carlin JB, Lee KJ, 2017, Model checking in multiple imputation: an overview and case study. Emerging Themes Epidemiol, 14: 8. https://doi.org/10.1186/s12982-017-0062-6
Metelkova J, Kinds Y, Kempen K, et al., 2018, On the influence of laser defocusing in Selective Laser melting of 316L. Addit Manuf, 23: 161–169. https://doi.org/10.1016/j.addma.2018.08.006
Slobodzian GE. White Paper-apples to Apples: Which Camera Technologies Work Best for Beam Profiling Applications, Part 2: Baseline Methods and Mode Effects. Available from: https://www.ophiropt.com/laser--measurement/knowledge-center/article/8065 [Last accessed on 2020 Oct 12].
Kuruvilla M, Srivatsan TS, Petraroli M, et al., 2008, An investigation of microstructure, hardness, tensile behaviour of a titanium alloy: Role of orientation. Sadhana, 33: 235–250. https://doi.org/10.1007/s12046-008-0017-2
Jiang PF, Zhang CH, Zhang S, et al., 2021, Additive manufacturing of novel ferritic stainless steel by selective laser melting: Role of laser scanning speed on the formability, microstructure and properties. Opt Laser Technol, 140: 107055. https://doi.org/10.1016/j.optlastec.2021.107055
Wang Z, Xiao Z, Tse Y, et al., 2019, Optimization of processing parameters and establishment of a relationship between microstructure and mechanical properties of SLM titanium alloy. Opt Laser Technol, 112: 159–167. https://doi.org/10.1016/j.optlastec.2018.11.014