Characterization of triply periodic minimal surface structures obtained using toolpath-based construction design
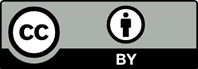
Triply periodic minimal surface (TPMS) cellular structures of Ti6Al4V with theoretically calculated relative densities ranging from 4% to 22.6% were designed using a toolpath-based construction method and fabricated by laser powder bed fusion, and their macrostructure, microstructure, and compression performance were investigated. The results indicated that the macrostructure was the same as that of TPMS structures designed using the traditional method. In contrast, the microstructures of the as-built samples and the samples after stress-relief annealing were slightly different from those of the traditional ones. Moreover, compression test results of the Schwarz-P structures showed that the compressive modulus was positively related to the calculated relative density, and a Gibson-Ashby model was established to quantitatively describe the relationship between the compressive modulus and theoretical relative density. The findings of this work show that the mechanical performance of a TPMS structure obtained using a toolpath-based construction design can be accurately predicted using geometric parameters or printing toolpaths. This will be helpful during the design stage.
Yicha Zhang serves as the Editorial Board Member of the journal, but did not in any way involve in the editorial and peer-review process conducted for this paper, directly or indirectly.
Maconachie T, Leary M, Lozanovski B, et al., 2019, SLM lattice structures: Properties, performance, applications and challenges. Mater Design, 183: 108137. https://doi.org/10.1016/j.matdes.2019.108137
McGregor M, Patel S, McLachlin S, et al., 2021, Architectural bone parameters and the relationship to titanium lattice design for powder bed fusion additive manufacturing. Addit Manuf, 47: 102273. https://doi.org/10.1016/j.addma.2021.102273
Feng J, Fu J, Yao X, et al., 2022, Triply periodic minimal surface (TPMS) porous structures: From multi-scale design, precise additive manufacturing to multidisciplinary applications. Int J Extrem Manuf, 4: 022001.
Du Plessis A, Broeckhoven C, Yadroitsava I, et al., 2019, Beautiful and functional: A review of biomimetic design in additive manufacturing. Addit Manuf, 27: 408–427. https://doi.org/10.1016/j.addma.2019.03.033
Pham MS, Liu C, Todd I, et al., 2019, Damage-tolerant architected materials inspired by crystal microstructure. Nature, 565: 305–311. https://doi.org/10.1038/s41586-018-0850-3
Thompson MK, Moroni G, Vaneker T, et al., 2016, Design for additive manufacturing: Trends, opportunities, considerations, and constraints. CIRP Ann Manuf Technol, 65: 737–760.
Vaneker T, Bernard A, Moroni G, et al., 2020, Design for additive manufacturing: Framework and methodology. CIRP Annals, 69: 578–599. https://doi.org/10.1016/j.cirp.2020.05.006
Zhang Y, Yang S, Zhao YF, 2020, Manufacturability analysis of metal laser-based powder bed fusion additive manufacturing-a survey. Int J Adv Manuf Technol, 110: 57–78.
Shi Y, Zhang Y, Baek S, et al., 2018, Manufacturability analysis for additive manufacturing using a novel feature recognition technique. Comput Aided Design Appl, 15: 941–952. https://doi.org/10.1080/16864360.2018.1462574
Yang L, Yan C, Cao W, et al., 2019, Compression-compression fatigue behaviour of gyroid-type triply periodic minimal surface porous structures fabricated by selective laser melting. Acta Mater, 181: 49–66. https://doi.org/10.2139/ssrn.3406935
Yan X, Yue S, Ge J, et al., 2022, Microstructural and mechanical optimization of selective laser melted Ti6Al4V lattices: Effect of hot isostatic pressing. J Manuf Processes, 77: 151–162. https://doi.org/10.1016/j.jmapro.2022.02.024
Ding J, Zou Q, Qu S, et al., 2021, STL-free design and manufacturing paradigm for high-precision powder bed fusion. CIRP Annals, 70: 167–170. https://doi.org/10.1016/j.cirp.2021.03.012
Feng J, Fu J, Lin Z, et al., 2019, Layered infill area generation from triply periodic minimal surfaces for additive manufacturing. Comput Aided Design, 107: 50–63. https://doi.org/10.1016/j.cad.2018.09.005
Feng J, Fu J, Shang C, et al., 2020, Efficient generation strategy for hierarchical porous scaffolds with freeform external geometries. Addit Manuf, 31: 100943. https://doi.org/10.1016/j.addma.2019.100943
Ding L, Tan S, Chen W, et al., 2021, Manufacturability analysis of extremely fine porous structures for selective laser melting process of Ti6Al4V alloy. Rapid Prototyp J, 27: 1523–1537. https://doi.org/10.1108/RPJ-11-2020-0280
Ding L, Tan S, Chen W, et al., 2022, Development of a manufacturability predictor for periodic cellular structures in a selective laser melting process via experiment and ANN modelling. Virtual Phys Prototyp, 17: 948–965. https://doi.org/10.1080/17452759.2022.2091461
Yan C, Hao L, Hussein A, et al., 2012, Evaluations of cellular lattice structures manufactured using selective laser melting. Int J Mach Tools Manuf, 62: 32–38. https://doi.org/10.1016/j.ijmachtools.2012.06.002
Yan C, Hao L, Hussein A, et al., 2014, Advanced lightweight 316L stainless steel cellular lattice structures fabricated via selective laser melting. Mater Design, 55: 533–541. https://doi.org/10.1016/j.matdes.2013.10.027
Neikter M, Huang A, Wu X, 2019, Microstructural characterization of binary microstructure pattern in selective laser-melted Ti-6Al-4V. Int J Adv Manuf Technol, 104: 1381–1391.
Zhang Y, Tan S, Ding L, et al., 2021, A toolpath-based layer construction method for designing & printing porous structure. CIRP Annals, 70: 123–126. https://doi.org/10.1016/j.cirp.2021.04.020
Tan S, Zhang X, Ding L, et al., 2021, An Efficient Layer Construction Method to Generate Accurate Printing Toolpaths of Periodic Cellular Structures for Selective Laser Melting Process Solid Freeform Fabrication 2021. In: Proceedings of the 32th Annual International Solid Freeform Fabrication Symposium.
International Organization for Standardization. Mechanical Testing of Metals-Ductility Testing-compression Test for Porous and Cellular Metals. Geneva: International Organization for Standardization. ISO 13314-2011.
Ashby MF, 2006, The properties of foams and lattices. Philos Trans A Math Phys Eng Sci, 364: 15–30. https://doi.org/10.1098/rsta.2005.1678
Zhao X, Li S, Zhang M, et al., 2016, Comparison of the microstructures and mechanical properties of Ti-6Al-4V fabricated by selective laser melting and electron beam melting. Mater Design, 95: 21–31. https://doi.org/10.1016/j.matdes.2015.12.135
Chang C, Huang J, Yan X, et al., 2020, Microstructure and mechanical deformation behavior of selective laser melted Ti6Al4V ELI alloy porous structures. Mater Lett, 277: 128366. https://doi.org/10.1016/j.matlet.2020.128366
Vrancken B, Thijs L, Kruth JP, et al., 2012, Heat treatment of Ti6Al4V produced by selective laser melting: Microstructure and mechanical properties. J Alloys Compds, 541: 177–185. https://doi.org/10.1016/j.jallcom.2012.07.022