Flexural behavior of 3D printed bio-inspired interlocking suture structures
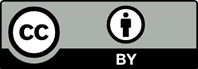
Additive manufacturing has allowed producing various complex structures inspired by natural materials. In this research, the bio-inspired suture structure was 3D printed using the fused deposition modeling printing technique to study its bending response behavior. Suture is one of the most commonly found structures in biological bodies. The primary purpose of this structure in nature is to improve flexibility by absorbing energy without causing permeant damage to the biological structure. An interesting discovery of the suture joint in diabolical ironclad beetle has given a great opportunity to further study the behavior of these natural suture designs. Inspired by the elliptical shape and the interlocking features of this suture, specimens were designed and 3D printed using polylactic acid thermoplastic polymer. A three-point bending test was then conducted to analyze the flexural behavior of each suture design, while digital image correlation and numerical simulation were performed to capture the insights of deformation process.
Phuong Tran serves as the Editorial Board Member of the journal, but did not in any way involve in the editorial and peer-review process conducted for this paper, directly or indirectly.
Ghazlan A, Ngo T, Tan P, et al., 2021, Inspiration from nature’s body armours-a review of biological and bioinspired composites. Compos B Eng, 205: 108513. https://doi.org/10.1016/j.compositesb.2020.108513
Ahamed MK, Wang H, Hazell PJ, 2022, From biology to biomimicry: Using nature to build better structures a review. Constr Build Mater, 320: 126195. https://doi.org/10.1016/j.conbuildmat.2021.126195
Du Plessis A, Broeckhoven C, Yadroitsava I, et al., 2019, Beautiful and functional: A review of biomimetic design in additive manufacturing. Addit Manuf, 27: 408–427. https://doi.org/10.1016/j.addma.2019.03.033
Plocher J, Mencattelli L, Narducci F, et al., 2021, Learning from nature: Bio-inspiration for damage-tolerant high-performance fibre-reinforced composites. Compos Sci Technol, 208: 108669. https://doi.org/10.1016/j.compscitech.2021.108669
Liu J, Li S, Fox K, et al., 2022, 3D concrete printing of bioinspired bouligand structure: A study on impact resistance. Addit Manuf, 50: 102544. https://doi.org/10.1016/j.addma.2021.102544
Tee YL, Maconachie T, Pille P, et al., 2021, From nature to additive manufacturing: Biomimicry of porcupine quill. Mater Des, 210: 110041. https://doi.org/10.1016/j.matdes.2021.110041
Peng C, Tran P, 2020, Bioinspired functionally graded gyroid sandwich panel subjected to impulsive loadings. Compos B Eng, 188: 107773. https://doi.org/10.1016/j.compositesb.2020.107773
Achrai B, Wagner HD, 2013, Micro-structure and mechanical properties of the turtle carapace as a biological composite shield. Acta Biomater, 9: 5890–5902. https://doi.org/10.1016/j.actbio.2012.12.023
Krauss S, Monsonego‐Ornan E, Zelzer E, et al., 2009, Mechanical function of a complex three‐dimensional suture joining the bony elements in the shell of the red‐eared slider turtle. Adv Mater, 21: 407–412. https://doi.org/10.1002/adma.200801256
Lee N, Horstemeyer M, Rhee H, et al., 2014, Hierarchical multiscale structure-property relationships of the red-bellied woodpecker (Melanerpes carolinus) beak. J R Soc Interf, 11: 20140274. https://doi.org/10.1098/rsif.2014.0274
Liu Z, Zhang Z, Ritchie RO, 2020, Interfacial toughening effect of suture structures. Acta Biomater, 102: 75–82. https://doi.org/10.1016/j.actbio.2019.11.034
Vincent JF, Wegst UG, 2004, Design and mechanical properties of insect cuticle. Arthrop Struct Dev, 33: 187–99. https://doi.org/10.1016/j.asd.2004.05.006
Yang W, Naleway SE, Porter MM, et al., 2015, The armored carapace of the boxfish. Acta Biomater, 23: 1–10. https://doi.org/10.1016/j.actbio.2015.05.024
Magwene PM, Socha JJ, 2013, Biomechanics of turtle shells: How whole shells fail in compression. J Exp Zool A Ecol Genet, 319: 86–98. https://doi.org/10.1002/jez.1773
Jia Z, Yu Y, Wang L, 2019, Learning from nature: Use material architecture to break the performance tradeoffs. Mater Des, 168: 107650. https://doi.org/10.1016/j.matdes.2019.107650
Chen IH, Yang W, Meyers MA, 2015, Leatherback sea turtle shell: A tough and flexible biological design. Acta Biomater, 28: 2–12. https://doi.org/10.1016/j.actbio.2015.09.023
Alheit B, Bargmann S, Reddy B, 2020, Computationally modelling the mechanical behaviour of turtle shell sutures a natural interlocking structure. J Mech Behav Biomed Mater, 110: 103973. https://doi.org/10.1016/j.jmbbm.2020.103973
Gao C, Li Y, 2019, Mechanical model of bio-inspired composites with sutural tessellation. J Mech Phys Solids, 122: 190–204. https://doi.org/10.1016/j.jmps.2018.09.015
Lin E, Li Y, Ortiz C, et al., 2014, 3D printed, bio-inspired prototypes and analytical models for structured suture interfaces with geometrically-tuned deformation and failure behavior. J Mech Phys Solids, 73: 166–182. https://doi.org/10.1016/j.jmps.2014.08.011
Malik IA, Mirkhalaf M, Barthelat F, 2017, Bio-inspired “jigsaw”-like interlocking sutures: Modeling, optimization, 3D printing and testing. J Mech Phys Solids, 102: 224–238. https://doi.org/10.1016/j.jmps.2017.03.003
Schmidt MJ, Farke D, Staszyk C, et al., 2022, Closure times of neurocranial sutures and synchondroses in Persian compared to Domestic Shorthair cats. Sci Rep, 12: 1–13. https://doi.org/10.1038/s41598-022-04783-1
Nicolay CW, Vaders MJ, 2006, Cranial suture complexity in white‐tailed deer (Odocoileus virginianus). J Morphol, 267: 841–849. https://doi.org/10.1002/jmor.10445
Bailleul AM, Scannella JB, Horner JR, et al., 2016, Fusion patterns in the skulls of modern archosaurs reveal that sutures are ambiguous maturity indicators for the Dinosauria. PLoS One, 11: e0147687. https://doi.org/10.1371/journal.pone.0147687
Rivera J, Hosseini MS, Restrepo D, et al., 2020, Toughening mechanisms of the elytra of the diabolical ironclad beetle. Nature, 586: 543–548.
Arakane Y, Lomakin J, Gehrke SH, et al., 2012, Formation of rigid, non-flight forewings (elytra) of a beetle requires two major cuticular proteins. PLoS Genet, 8: e1002682. https://doi.org/10.1371/journal.pgen.1002682
Fédrigo O, Wray GA, 2010, Developmental evolution: How beetles evolved their shields. Curr Biol, 20: R64–R66. https://doi.org/10.1016/j.cub.2009.12.012
Linz DM, Hu AW, Sitvarin MI, et al., 2016, Functional value of elytra under various stresses in the red flour beetle, Tribolium castaneum. Sci Rep, 6: 1–10. https://doi.org/10.1038/srep34813
Tomoyasu Y, Arakane Y, Kramer KJ, et al., 2009, Repeated co-options of exoskeleton formation during wing-to-elytron evolution in beetles. Curr Biol, 19: 2057–2065. https://doi.org/10.1016/j.cub.2009.11.014
Chen PY, 2020, Diabolical ironclad beetles inspire tougher joints for engineering applications. Nature, 586: 502–504. https://doi.org/10.1038/d41586-020-02840-1
Lazarus BS, Velasco-Hogan A, Gómez-del Río T, et al., 2020, A review of impact resistant biological and bioinspired materials and structures. J Mater Res Technol, 9: 15705– 15738. https://doi.org/10.1016/j.jmrt.2020.10.062
Huang W, Restrepo D, Jung JY, et al., 2019, Multiscale toughening mechanisms in biological materials and bioinspired designs. Adv Mater, 31: 1901561. https://doi.org/10.1002/adma.201901561
Studart AR, 2016, Additive manufacturing of biologically-inspired materials. Chem Soc Rev, 45: 359–376. https://doi.org/10.1039/C5CS00836K
Gharde S, Surendren A, Korde JM, et al., 2019, Recent advances in additive manufacturing of bio-inspired materials. In: Biomanufacturing, Springer, Berlin, p35–68. https://doi.org/10.1007/978-3-030-13951-3_2
Dev S, Srivastava R, 2021, Effect of infill parameters on material sustainability and mechanical properties in fused deposition modelling process: A case study. Prog Addit Manuf, 6: 631–642.
Gu GX, Chen CT, Richmond DJ, et al., 2018, Bioinspired hierarchical composite design using machine learning: simulation, additive manufacturing, and experiment. Mater Horiz, 5: 939–945. https://doi.org/10.1039/C8MH00653A
Dimas LS, Buehler M, 2014, Modeling and additive manufacturing of bio-inspired composites with tunable fracture mechanical properties. Soft Matter, 10: 4436–4442. https://doi.org/10.1039/C3SM52890A
Samykano M, Selvamani S, Kadirgama K, et al., 2019, Mechanical property of FDM printed ABS: Influence of printing parameters. Int J Adv Manuf Technol, 102: 2779–2796. https://doi.org/10.1007/s00170-019-03313-0
Mazzanti V, Malagutti L, Mollica F, 2019, FDM 3D printing of polymers containing natural fillers: A review of their mechanical properties. Polymers, 11: 1094. https://doi.org/10.3390/polym11071094
Cuiffo MA, Snyder J, Elliott AM, et al., 2017, Impact of the fused deposition (FDM) printing process on polylactic acid (PLA) chemistry and structure. Appl Sci, 7: 579. https://doi.org/10.3390/app7060579
Luis E, Pan HM, Sing SL, et al., 2020, 3D direct printing of silicone meniscus implant using a novel heat-cured extrusion-based printer. Polymers, 12: 1031. https://doi.org/10.3390/polym12051031
Velasco‐Hogan A, Xu J, Meyers MA, 2018, Additive manufacturing as a method to design and optimize bioinspired structures. Adv Mater, 30: 1800940. https://doi.org/10.1002/adma.201800940
Wang D, Chen D, Chen Z, 2020, Recent progress in 3D printing of bioinspired structures. Front Mater, 7: 286. https://doi.org/10.3389/fmats.2020.00286
Ehrmann G, Ehrmann A, 2021, Investigation of the shape-memory properties of 3D printed PLA structures with different infills. Polymers, 13: 164. https://doi.org/10.3390/polym13010164
Raj SA, Muthukumaran E, Jayakrishna K, 2018, A case study of 3D printed PLA and its mechanical properties. Mater Today Proc, 5: 11219–26. https://doi.org/10.1016/j.matpr.2018.01.146
Kiendl J, Gao C, 2020, Controlling toughness and strength of FDM 3D-printed PLA components through the raster layup. Compos B Eng, 180: 107562. https://doi.org/10.1016/j.compositesb.2019.107562
Rajpurohit SR, Dave HK, 2018, Effect of process parameters on tensile strength of FDM printed PLA part. Rapid Prototyp J, 24: 1317–1324. https://doi.org/10.1108/RPJ-06-2017-0134
Cao Y, Wang W, Wang J, et al., 2019, Experimental and numerical study on tensile failure behavior of bionic suture joints. J Mech Behav Biomed Mater, 92: 40–49. https://doi.org/10.1016/j.jmbbm.2019.01.001
Malik IA, Barthelat F, 2018, Bioinspired sutured materials for strength and toughness: Pullout mechanisms and geometric enrichments. Int J Solids Struct, 138: 118–133. https://doi.org/10.1016/j.ijsolstr.2018.01.004
Miura T, Perlyn CA, Kinboshi M, et al., 2009, Mechanism of skull suture maintenance and interdigitation. J Anat, 215: 642–655. https://doi.org/10.1111/j.1469-7580.2009.01148.x
Standard A, 2014, ASTM D638-14 Standard Test Method for Tensile Properties of Plastics. ASTM International, West Conshohocken, PA.
Blaber BA, Antoniou A, 2015, Ncorr: Open-source 2D digital image correlation matlab software. Exp Mech, 55: 1105–1122.
Peng C, Fox K, Qian M, et al., 2021, 3D printed sandwich beams with bioinspired cores: Mechanical performance and modelling. Thin Walled Struct, 161: 107471. https://doi.org/10.1016/j.tws.2021.107471
Habib F, Iovenitti P, Masood S, et al., 2017, In-plane energy absorption evaluation of 3D printed polymeric honeycombs. Virtual Phys Prototyp, 12: 117–131. https://doi.org/10.1080/17452759.2017.1291354
Kardel K, Ghaednia H, Carrano AL, et al., Experimental and theoretical modeling of behavior of 3D-printed polymers under collision with a rigid rod. Addit Manuf, 14: 87–94. https://doi.org/10.1016/j.addma.2017.01.004
Lee SH, Lee KG, Hwang JH, et al., 2019, Evaluation of mechanical strength and bone regeneration ability of 3D printed kagome-structure scaffold using rabbit calvarial defect model. Mater Sci Eng C, 98: 949–959. https://doi.org/10.1016/j.msec.2019.01.050
Liu L, Jiang Y, Boyce M, et al., 2017, The effects of morphological irregularity on the mechanical behavior of interdigitated biological sutures under tension. J Biomech, 58: 71–78. https://doi.org/10.1016/j.jbiomech.2017.04.017