Process study for directed energy deposition of 316L stainless steel with TiB2 metal matrix composites
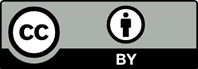
In addition to laser powder bed fusion, directed energy deposition (DED) is also gaining interest as an effective metal additive manufacturing technique. Due to its system configuration, it is more efficient and flexible for materials development. Therefore, it can be used for processing of metal matrix composites (MMCs) through the use of powder mixture as feedstock. 316L stainless steel has high corrosion resistance, biocompatibility, and ductility. Several studies have shown the feasibility of using DED to process 316L stainless steel. The material properties of 316L stainless steel can be improved using reinforcement particles such as TiB2 to form MMCs. In this study, the effects of process parameters on microstructure and mechanical properties of 316L stainless steel reinforced with TiB2 (316L/TiB2) MMC were studied. The process parameters, including laser power, scanning speed, and hopper speed, were varied and analyzed using Taguchi L9 array. It was found that the process parameters have insignificant effect on the bulk density of the samples produced. Through this study, it is also found that tumble mixing was not suitable for the powder feedstock preparation for MMCs to be processed by DED. The microstructure of DED 316L/TiB2 MMC samples consists of columnar and equiaxed grains. Columnar grains were located within the layers while equiaxed grains were located at the interlayer zones. Fine sub-grains were also observed within these grains and their boundaries were enriched with molybdenum and chromium segregations. Precipitates containing titanium were also observed to segregate at the sub-grain boundaries. Finally, the Vickers microhardness of the DED 316L/TiB2 MMC was found to be similar to pure 316L stainless steel produced by DED.
Swee Leong Sing serves as the Associate Editor of the journal, but did not in any way involve in the editorial and peer-review process conducted for this paper, directly or indirectly.
Herzog D, Seyda V, Wycisk E, et al., 2016, Additive manufacturing of metals. Acta Mater, 117: 371–392. https://doi.org/10.1016/j.actamat.2016.07.019
Frazier W, 2014, Metal additive manufacturing: A review. J Mater Eng Perform, 23: 1917–1928.
Michel F, Lockett H, Ding J, et al., 2018, A modular path planning solution for Wire + Arc additive manufacturing. Robot Comput Integr Manuf, 60: 1–11. https://doi.org/10.1016/j.rcim.2019.05.009
Ding D, Pan Z, Cuiuri D, et al., 2016, Adaptive path planning for wire-feed additive manufacturing using medial axis transformation. J Cleaner Prod, 133: 942–952. https://doi.org/10.1016/j.jclepro.2016.06.036
Feenstra DR, Cruz V, Gao X, et al., 2020, Effect of build height on the properties of large format stainless steel 316L fabricated via directed energy deposition. Addit Manuf, 34: 101205. https://doi.org/10.1016/j.addma.2020.101205
Saboori A, Aversa A, Marchese G, et al., 2019, Application of directed energy deposition-based additive manufacturing in repair. Appl Sci, 9: 3316. https://doi.org/10.3390/app9163316
Dass A, Moridi A, 2019, State of the art in directed energy deposition: From additive manufacturing to materials design. Coatings, 9: 418. https://doi.org/10.3390/coatings9070418
Dharmawan AG, Soh GS, 2022, A cylindrical path planning approach for additive manufacturing of revolved components. Mater Sci Addit Manuf, 1: 3. https://doi.org/10.18063/msam.v1i1.3
Ansari M, Jabari E, Toyserkani E, 2021, Opportunities and challenges in additive manufacturing of functionally graded metallic materials via powder-fed laser directed energy deposition: A review. J Mater Porc Technol, 294: 117117. https://doi.org/10.1016/j.jmatprotec.2021.117117
Groden C, Traxel KD, Afrouzian A, et al., 2022, Inconel 718-W7Ni3Fe bimetallic structures using directed energy deposition-based additive manufacturing. Virtual Phys Prototyp, 17: 170–180. https://doi.org/10.1080/17452759.2022.2025673
Sehhat MH, Sutton AT, Hung CH, et al., 2022, Plasma spheroidization of gas-atomized 304L stainless steel powder for laser powder bed fusion process. Mater Sci Addit Manuf, 1: 11. https://doi.org/10.18063/msam.v1i1.1
Wu CL, Zhang S, Zhang CH, et al., 2019, Effects of SiC content on phase evolution and corrosion behavior of SiC-reinforced 316L stainless steel matrix composites by laser melting deposition. Optics Laser Technol, 115: 134–139. https://doi.org/10.1016/j.optlastec.2019.02.029
Fu C, Li J, Bai J, et al., 2021, Effect of helium bubbles on irradiation hardening of additive manufacturing 316L stainless steel under high temperature He ions irradiation. J Nucl Mater, 550: 152948. https://doi.org/10.1016/j.jnucmat.2021.152948
Ertugrul O, Enrici TM, Paydas H, et al., 2020, Laser cladding of TiC reinforced 316L stainless steel composites: Feedstock powder preparation and microstructural evaluation. Powder Technol, 375: 384–396. https://doi.org/10.1016/j.powtec.2020.07.100
Du B, Zou Z, Wang X, et al., 2008, Laser cladding of in situ TiB2/Fe composite coating on steel. Appl Surf Sci, 254: 6489-6494. https://doi.org/10.1016/j.apsusc.2008.04.051
Koh HK, Moo JG, Sing SL, et al., 2022, Use of fumed silica nanostructured additives in selective laser melting and fabrication of steel matrix nanocomposites. Materials, 15: 1869. https://doi.org/10.3390/ma15051869
Chen W, Xu L, Zhang Y, et al., 2022, Additive manufacturing of high-performance 15-5PH stainless steel matrix composites. Virtual Phys Prototyp, 17: 366–381. https://doi.org/10.1080/17452759.2021.2019793
AlMangour B, Grzesiak D, Yang JM, 2017, Selective laser melting of TiB2/316L stainless steel composites: The roles of powder preparation and hot isostatic pressing post-treatment. Powder Technol, 309: 37–48. https://doi.org/10.1016/j.powtec.2016.12.073
AlMangour B, Kim YK, Grzesiak D, et al., 2019, Novel TiB2-reinforced 316L stainless steel nanocomposites with excellent room and high-temperature yield strength developed by additive manufacturing. Compos Part B Eng, 156: 51–63. https://doi.org/10.1016/j.compositesb.2018.07.050
Lu X, Chiumenti M, Cervera M, et al., 2021, Substrate design to minimize residual stresses in directed energy deposition AM processes. Mater Des, 202: 109525. https://doi.org/10.1016/j.matdes.2021.109525
Mukherjee T, Manvatkar V, De A, DebRoy T, 2017, Mitigation of thermal distortion during additive manufacturing. Script Mater, 127: 79–83. https://doi.org/10.1016/j.scriptamat.2016.09.001
Saboori A, Piscopo G, Lai M, et al., 2020, An investigation on the effect of deposition pattern on the microstructure, mechanical properties and residual stress of 316L produced by directed energy deposition. Mater Sci Eng A, 780: 139179. https://doi.org/10.1016/j.msea.2020.139179
Saeidi K, Gao X, Zhong Y, et al., 2015, Hardened austenite steel with columnar sub-grain structure formed by laser melting. Mater Sci Eng A, 625: 221–229. https://doi.org/10.1016/j.msea.2014.12.018
Tan ZE, Pang JH, Kaminski, et al., 2019, Characterisation of porosity, density, and microstructure of directed energy deposited stainless steel AISI 316L. Addit Manuf, 25: 286–296. https://doi.org/10.1016/j.addma.2018.11.014
Yadroitsev I, Krakhmalev P, Yadroitsava I, et al., 2013, Energy input effect on morphology and microstructure of selective laser melting single track from metallic powder. J Mater Proc Technol, 213: 600–613. https://doi.org/10.1016/j.jmatprotec.2012.11.014
Zhang DL, 2004, Processing of advanced materials using high-energy mechanical milling. Prog Mater Sci, 49: 537–560.
Suryanarayana C, Ivanov E, Boldyrev VV, 2002, The science and technology of mechanical alloying. Mater Sci Eng A, 304–306: 151–158. https://doi.org/10.1016/s0921-5093(00)01465-9
Fogagnolo JB, Velasco F, Robert MH, et al., 2003, Effect of mechanical alloying on the morphology, microstructure and properties of aluminium matrix composite powders. Mater Sci Eng A, 342: 131–143. https://doi.org/10.1016/s0921-5093(02)00246-0
Xu H, Lu Z, Jia C, et al., 2015, Influence of mechanical alloying time on morphology and properties of 15Cr-ODS steel powders. High Temperature Materials and Processes, 35: 473–477. https://doi.org/10.1515/htmp-2014-0229
Zhao Q, Yu L, Liu Y, et al., 2015, Morphology and structure evolution of Y2O3 nanoparticles in ODS steel powders during mechanical alloying and annealing. Adv Powder Technol, 26: 1578–1582. https://doi.org/10.1016/j.apt.2015.08.017
Rahmanifard R, Farhangi H, Novinrooz AJ, 2010, Optimization of mechanical alloying parameters in 12YWT ferritic steel nanocomposite. Mater Sci Eng A, 527: 6853–6857. https://doi.org/10.1016/j.msea.2010.07.048
Si C, Zhang Z, Zhang Q, et al., 2021, Influence of mechanical alloying on the particle size, microstructure and soft magnetic properties of coarse Fe-based amorphous powders prepared by gas atomization. J Non Cryst Solids, 559: 120675. https://doi.org/10.1016/j.jnoncrysol.2021.120675
AlMangour B, Grzesiak D, Yang JM, 2016, Rapid fabrication of bulk-form TiB2/316L stainless steel nanocomposites with novel reinforcement architecture and improved performance by selective laser melting. J Alloys Comp, 680: 480–493. https://doi.org/10.1016/j.jallcom.2016.04.156
Sarma IK, Srinivas V, Subbu SK, 2021, Effect of process parameters on micro hardness, bulk hardness and porosity of LENSTM deposited SS 316L alloy. Mater Today Proc, 46:2616–2624. https://doi.org/10.1016/j.matpr.2021.02.268