Lightweight load-bearing heat dissipation multifunctional pomelo peel-inspired structures fabricated by laser powder bed fusion
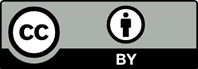
The heat dissipation structure used in modern airborne radar chassis not only requires lightweight, but also pursues better mechanical properties and heat dissipation performance. In this study, a stochastically porous pomelo peel-inspired gradient structure was fabricated by laser powder bed fusion using Al-Mg-Sc-Zr powder. This study focused on the formability, microstructure, mechanical properties, and heat dissipation performance of the biomimetic structure through experimental and finite element analysis approaches. The influence of volume fraction (VF) on structural mechanical properties, deformation modes, stress distribution, and heat dissipation performance was investigated. The results showed that the mechanical properties of the structure declined as the VFs decreased. The optimal mechanical performance was obtained at the VF of 45%, where the compressive strength, specific energy absorption (Ws), and specific compressive strength values were measured to be 63.47 MPa, 34.84 J/g, and 142.16 MPa/(g·cm-3), respectively. Moreover, the Ws of the structures was higher than that of the reported aluminum alloy structures at the same VF. The biomimetic structure exhibited improved heat dissipation performance as the VFs decreased, with Reynolds number ranging from 2700 to 13,400. The structure of 30% VF with a remarkable heat transfer efficiency index of 1.86 displayed the best heat dissipation performance. In addition, compared with the traditional fin structures, the bionic structure possessed better thermal resistance, heat transfer efficiency index, and temperature uniformity at the same VF. This study demonstrated notable potential of pomelo peel-inspired design for lightweight load-bearing applications capable of heat-dissipating performance, providing a novel perspective for design and fabrication of versatile structures in the aviation field.
- Siddique SH, Hazell PJ, Wang HX, et al., 2022, Lessons from nature: 3D printed bio-inspired porous structures for impact energy absorption-A review. Addit Manuf, 58: 103051. http://dx.doi.org/10.1016/j.addma.2022.103051
- Bandyopadhyay A, Traxel KD, Bose S, 2021, Nature-inspired materials and structures using 3D Printing. Mater Sci Eng R Rep, 145: 100609. http://dx.doi.org/10.1016/j.mser.2021.100609
- Omenetto FG, Kaplan DL, 2010, New opportunities for an ancient material. Science, 329(5991): 528–531. http://dx.doi.org/10.1126/science.1188936
- Islam MK, Hazell PJ, Escobedo JP, et al., 2021, Biomimetic armour design strategies for additive manufacturing: A review. Mater Des, 205: 109730. http://dx.doi.org/10.1016/j.matdes.2021.109730
- Mohammadi A, Hajizadeh E, Tan Y, et al., 2023, A bioinspired 3D-printable flexure joint with cellular mechanical metamaterial architecture for soft robotic hands. Int J Bioprint, 9(3): 696. http://dx.doi.org/10.18063/ijb.696
- Yang J, Gu D, Lin K, et al., 2022, Laser additive manufacturing of bio-inspired metallic structures. Chinese J Mech Eng Addit Manuf Front, 1(1): 100013. http://dx.doi.org/10.1016/j.cjmeam.2022.100013
- Benedetti M, du Plessis A, Ritchie RO, et al., 2021, Architected cellular materials: A review on their mechanical properties towards fatigue-tolerant design and fabrication. Mater Sci Eng R, 144: 100606. http://dx.doi.org/10.1016/j.mser.2021.100606
- Gu D, Shi X, Poprawe R, et al., 2021, Material-structure-performance integrated laser-metal additive manufacturing. Science, 372(6545): eabg1487. http://dx.doi.org/10.1126/science.abg1487
- Tofail SAM, Koumoulos EP, Bandyopadhyay A, et al., 2018, Additive manufacturing: scientific and technological challenges, market uptake and opportunities. Mater Today, 21(1): 22–37. http://dx.doi.org/10.1016/j.mattod.2017.07.001
- Zhang Y, Attarilar S, Wang L, et al., 2021, A review on design and mechanical properties of additively manufactured NiTi implants for orthopedic applications. Int J Bioprint, 7(2): 340. http://dx.doi.org/10.18063/ijb.v7i2.340
- Hojjatzadeh SMH, Parab ND, Guo Q, et al., 2020, Direct observation of pore formation mechanisms during LPBF additive manufacturing process and high energy density laser welding. Int J Mach Tools Manuf, 153: 103555. http://dx.doi.org/10.1016/j.ijmachtools.2020.103555
- Korkmaz ME, Gupta MK, Robak G, et al., 2022, Development of lattice structure with selective laser melting process: A state of the art on properties, future trends and challenges. J Manuf Processes, 81: 1040–1063. http://dx.doi.org/10.1016/j.jmapro.2022.07.051
- Zhou Y, Wang J, Yang Y, et al., 2022, Laser additive manufacturing of zinc targeting for biomedical application. Int J Bioprint, 8(1): 501.http://dx.doi.org/10.18063/ijb.v8i1.501
- Du Plessis A, Razavi SMJ, Benedetti M, et al., 2022, Properties and applications of additively manufactured metallic cellular materials: A review. Prog Mater Sci, 125: 100918. http://dx.doi.org/10.1016/j.pmatsci.2021.100918
- Yang J, Gao H, Zhang D, et al., 2022, Static compressive behavior and material failure mechanism of trabecular tantalum scaffolds fabricated by laser powder bed fusion-based additive manufacturing. Int J Bioprint, 8(1): 438. http://dx.doi.org/10.18063/ijb.v8i1.438
- Wang R, Gu D, Lin K, et al., 2022, Multi-material additive manufacturing of a bio-inspired layered ceramic/metal structure: Formation mechanisms and mechanical properties. Int J Mach Tools Manuf, 175: 103872. http://dx.doi.org/10.1016/j.ijmachtools.2022.103872
- Yuan L, Gu D, Lin K, et al., 2022, Electrically actuated shape recovery of NiTi components processed by laser powder bed fusion after regulating the dimensional accuracy and phase transformation behavior. Chinese J Mech Eng Addit Manuf Front, 1(4): 100056. http://dx.doi.org/10.1016/j.cjmeam.2022.100056
- Lin K, Hu K, Gu D, 2019, Metallic integrated thermal protection structures inspired by the Norway spruce stem: Design, numerical simulation and selective laser melting fabrication. Opt Laser Technol, 115: 9–19. http://dx.doi.org/10.1016/j.optlastec.2019.02.003
- Hu K, Lin K, Gu D, et al., 2019, Mechanical properties and deformation behavior under compressive loading of selective laser melting processed bio-inspired sandwich structures. Mater Sci Eng A, 762: 138089. http://dx.doi.org/10.1016/j.msea.2019.138089
- Yang C, Li QM, Wang Y, 2021, Compressive properties of cuttlebone-like lattice (CLL) materials with functionally graded density. Eur J Mech A Solids, 87: 104215. http://dx.doi.org/10.1016/j.euromechsol.2021.104215
- Lazarus BS, Luu RK, Ruiz-Perez S, et al., 2022, Equine hoof wall: Structure, properties, and bioinspired designs. Acta Biomater, 151: 426–445. http://dx.doi.org/10.1016/j.actbio.2022.08.028
- Pack RC, Romberg SK, Badran AA, et al., 2020, Carbon fiber and syntactic foam hybrid materials via core–shell material extrusion additive manufacturing. Adv Mater Technol, 5(12): 2000731. http://dx.doi.org/10.1002/admt.202000731
- Wang D, Liu L, Deng G, et al., 2022, Recent progress on additive manufacturing of multi-material structures with laser powder bed fusion. Virtual Phys Prototyping, 17(2): 329–365. http://dx.doi.org/10.1080/17452759.2022.2028343
- Yue X, Shang J, Zhang M, et al., 2022, Additive manufacturing of high porosity magnesium scaffolds with lattice structure and random structure. Mater Sci Eng A, 859: 144167. http://dx.doi.org/10.1016/j.msea.2022.144167
- Gomez S, Vlad MD, Lopez J, et al., 2016, Design and properties of 3D scaffolds for bone tissue engineering. Acta Biomater, 42: 341–350. http://dx.doi.org/10.1016/j.actbio.2016.06.032
- Ge J, Huang J, Lei Y, et al., 2020, Microstructural features and compressive properties of SLM Ti6Al4V lattice structures. Surf Coat Technol, 403: 126419. http://dx.doi.org/10.1016/j.surfcoat.2020.126419
- Tee YL, Maconachie T, Pille P, et al., 2021, From nature to additive manufacturing: Biomimicry of porcupine quill. Mater Des, 210: 110041. http://dx.doi.org/10.1016/j.matdes.2021.110041
- Sheng X, Dong D, Lu X, et al., 2020, MXene-wrapped bio-based pomelo peel foam/polyethylene glycol composite phase change material with enhanced light-to-thermal conversion efficiency, thermal energy storage capability and thermal conductivity. Composites, Part A, 138: 106067. http://dx.doi.org/10.1016/j.compositesa.2020.106067
- Zhang C, Xiao P, Ni F, et al., 2020, Converting pomelo peel into eco-friendly and low-consumption photothermic biomass sponge toward multifunctioal solar-to-heat conversion. ACS Sustainable Chem Eng, 8(13): 5328–5337. http://dx.doi.org/10.1021/acssuschemeng.0c00681
- Buhrig-Polaczek A, Fleck C, Speck T, et al., 2016, Biomimetic cellular metals-using hierarchical structuring for energy absorption. Bioinspir Biomim, 11(4): 045002. http://dx.doi.org/10.1088/1748-3190/11/4/045002
- Fischer SF, Thielen M, Loprang RR, et al., 2010, Pummelos as concept generators for biomimetically inspired low weight structures with excellent damping properties. Adv Eng Mater, 12(12): B658–B663. http://dx.doi.org/10.1002/adem.201080065
- Zhang W, Yin S, Yu TX, et al., 2019, Crushing resistance and energy absorption of pomelo peel inspired hierarchical honeycomb. Int J Impact Eng, 125: 163–172. http://dx.doi.org/10.1016/j.ijimpeng.2018.11.014
- Zhang Z, Song B, Yao Y, et al., 2022, Bioinspired, simulation‐guided design of polyhedron metamaterial for simultaneously efficient heat dissipation and energy absorption. Adv Mater Technol, 7(10): 2200076. http://dx.doi.org/10.1002/admt.202200076
- Wong M, Owen I, Sutcliffe CJ, et al., 2009, Convective heat transfer and pressure losses across novel heat sinks fabricated by selective laser melting. Int J Heat Mass Transfer, 52(1–2): 281–288. http://dx.doi.org/10.1016/j.ijheatmasstransfer.2008.06.002
- Yang B, Chen W, Xin R, et al., 2022, Pomelo peel-inspired 3D-printed porous structure for efficient absorption of compressive strain energy. J Bionic Eng, 19(2): 448–457. http://dx.doi.org/10.1007/s42235-021-00145-1
- Zhang H, Gu D, Dai D, 2022, Laser printing path and its influence on molten pool configuration, microstructure and mechanical properties of laser powder bed fusion processed rare earth element modified Al-Mg alloy. Virtual Phys Prototyping, 17(2): 308–328. http://dx.doi.org/10.1080/17452759.2022.2036530
- Zhang H, Gu D, Dai D, et al., 2020, Influence of scanning strategy and parameter on microstructural feature, residual stress and performance of Sc and Zr modified Al–Mg alloy produced by selective laser melting. Mater Sci Eng A, 788: 139593. http://dx.doi.org/10.1016/j.msea.2020.139593
- Zhang H, Gu D, Yang J, et al., 2018, Selective laser melting of rare earth element Sc modified aluminum alloy: Thermodynamics of precipitation behavior and its influence on mechanical properties. Addit Manuf, 23: 1–12. http://dx.doi.org/10.1016/j.addma.2018.07.002
- Yang J, Gu D, Lin K, et al., 2022, Laser powder bed fusion of mechanically efficient helicoidal structure inspired by mantis shrimp. Int J Mech Sci, 231: 107573. http://dx.doi.org/10.1016/j.ijmecsci.2022.107573
- Liu H, Gu D, Yang J, et al., 2022, Laser powder bed fusion of node-reinforced hybrid lattice structure inspired by crystal microstructure: Structural feature sensitivity and mechanical performance. Mater Sci Eng A, 858: 144048. http://dx.doi.org/10.1016/j.msea.2022.144048
- Bünnagel C, Monir S, Sharp A, et al., 2021, Forced air cooled heat sink with uniformly distributed temperature of power electronic modules. Appl Therm Eng, 199: 117560. http://dx.doi.org/10.1016/j.applthermaleng.2021.117560
- Liang D, Chen W, Ju Y, et al., 2021, Comparing endwall heat transfer among staggered pin fin, Kagome and body centered cubic arrays. Appl Therm Eng, 185: 116306. http://dx.doi.org/10.1016/j.applthermaleng.2020.116306
- Gee DL, Webb RL, 1980, Forced convection heat transfer in helically rib-roughened tubes. Int J Heat Mass Transfer, 23(8): 1127–1136. http://dx.doi.org/https://doi.org/10.1016/0017-9310(80)90177-5
- Chein R, Yang H, Tsai T-H, et al., 2009, Experimental study of heat sink performance using copper foams fabricated by electroforming. Microsyst Technol, 16(7): 1157–1164. http://dx.doi.org/10.1007/s00542-009-0950-y
- Bi J, Lei Z, Chen Y, et al., 2021, An additively manufactured Al-14.1Mg-0.47Si-0.31Sc-0.17Zr alloy with high specific strength, good thermal stability and excellent corrosion resistance. J Mater Sci Technol, 67: 23–35. http://dx.doi.org/10.1016/j.jmst.2020.06.036
- Li R, Wang M, Yuan T, et al., 2017, Selective laser melting of a novel Sc and Zr modified Al-6.2 Mg alloy: Processing, microstructure, and properties. Powder Technol, 319: 117–128. http://dx.doi.org/10.1016/j.powtec.2017.06.050
- Li K, Ji C, Bai S, et al., 2023, Selective laser melting of magnesium alloys: Necessity, formability, performance, optimization and applications. J Mater Sci Technol, 154: 65–93. http://dx.doi.org/10.1016/j.jmst.2022.12.053
- Kotadia HR, Gibbons G, Das A, et al., 2021, A review of laser powder bed fusion additive manufacturing of aluminium alloys: Microstructure and properties. Addit Manuf, 46: 102155. http://dx.doi.org/10.1016/j.addma.2021.102155
- Zhu Z, Hu Z, Seet HL, et al., 2023, Recent progress on the additive manufacturing of aluminum alloys and aluminum matrix composites: Microstructure, properties, and applications. Int J Mach Tools Manuf, 190: 104047. http://dx.doi.org/10.1016/j.ijmachtools.2023.104047
- Li R, Wang M, Li Z, et al., 2020, Developing a high-strength Al-Mg-Si-Sc-Zr alloy for selective laser melting: Crack-inhibiting and multiple strengthening mechanisms. Acta Mater, 193: 83–98. http://dx.doi.org/10.1016/j.actamat.2020.03.060
- Viale V, Stavridis J, Salmi A, et al., 2022, Optimisation of downskin parameters to produce metallic parts via laser powder bed fusion process: an overview. Int J Adv Manuf Technol, 123(7–8): 2159–2182. http://dx.doi.org/10.1007/s00170-022-10314-z
- Han Q, Gu H, Soe S, et al., 2018, Manufacturability of AlSi10Mg overhang structures fabricated by laser powder bed fusion. Mater Des, 160: 1080–1095. http://dx.doi.org/10.1016/j.matdes.2018.10.043
- Choy SY, Sun C-N, Sin WJ, et al., 2021, Superior energy absorption of continuously graded microlattices by electron beam additive manufacturing. Virtual Phys Prototyping, 16(1): 14–28. http://dx.doi.org/10.1080/17452759.2020.1868656
- Gao Z, Wang H, Sun H, et al., 2022, Additively manufactured high-energy-absorption metamaterials with artificially engineered distribution of bio-inspired hierarchical microstructures. Composites, Part B, 247: 110345. http://dx.doi.org/10.1016/j.compositesb.2022.110345
- Hu J, Tan ATL, Chen H, et al., 2022, Superior compressive properties of 3D printed plate lattice mechanical metamaterials. Int J Mech Sci, 231: 107586. http://dx.doi.org/10.1016/j.ijmecsci.2022.107586
- Xiao L, Xu X, Feng G, et al., 2022, Compressive performance and energy absorption of additively manufactured metallic hybrid lattice structures. Int J Mech Sci, 219: 107093. http://dx.doi.org/10.1016/j.ijmecsci.2022.107093
- Zhang J, Liu Y, Babamiri BB, et al., 2022, Enhancing specific energy absorption of additively manufactured titanium lattice structures through simultaneous manipulation of architecture and constituent material. Addit Manuf, 55: 102887. http://dx.doi.org/10.1016/j.addma.2022.102887
- Yang J, Gu D, Lin K, et al., 2021, Laser additive manufacturing of cellular structure with enhanced compressive performance inspired by Al–Si crystalline microstructure. CIRP J Manuf Sci Technol, 32: 26–36. http://dx.doi.org/10.1016/j.cirpj.2020.11.003
- Li C, Lei H, Liu Y, et al., 2018, Crushing behavior of multi-layer metal lattice panel fabricated by selective laser melting. Int J Mech Sci, 145: 389–399. http://dx.doi.org/10.1016/j.ijmecsci.2018.07.029
- Al-Saedi DSJ, Masood SH, Faizan-Ur-Rab M, et al., 2018, Mechanical properties and energy absorption capability of functionally graded F2BCC lattice fabricated by SLM. Mater Des, 144: 32–44. http://dx.doi.org/10.1016/j.matdes.2018.01.059
- Chen W, Gu D, Yang J, et al., 2022, Compressive mechanical properties and shape memory effect of NiTi gradient lattice structures fabricated by laser powder bed fusion. Int J Extreme Manuf, 4(4): 045002. http://dx.doi.org/10.1088/2631-7990/ac8ef3
- Yang X, Yang Q, Shi YS, et al., 2022, Effect of volume fraction and unit cell size on manufacturability and compressive behaviors of Ni-Ti triply periodic minimal surface lattices. Addit Manuf, 54: 102737. http://dx.doi.org/10.1016/j.addma.2022.102737
- Ho JY, Wong KK, Leong KC, et al., 2017, Convective heat transfer performance of airfoil heat sinks fabricated by selective laser melting. Int J Therm Sci, 114: 213–228. http://dx.doi.org/10.1016/j.ijthermalsci.2016.12.016
- Wong KK, Ho JY, Leong KC, et al., 2016, Fabrication of heat sinks by selective laser melting for convective heat transfer applications. Virtual Phys Prototyp, 11(3): 159–165. http://dx.doi.org/10.1080/17452759.2016.1211849
- Kuruneru STW, Vafai K, Sauret E, et al., 2020, Application of porous metal foam heat exchangers and the implications of particulate fouling for energy-intensive industries. Chem Eng Sci, 228: 115968. http://dx.doi.org/10.1016/j.ces.2020.115968
- Zhu Q, Cui Y, Zeng J, et al., 2023, Local hydrothermal characteristics and temperature uniformity improvement of microchannel heat sink with non-uniformly distributed grooves. Case Stud Therm Eng, 47: 103113. http://dx.doi.org/10.1016/j.csite.2023.103113