Study on 3D printing process of continuous polyglycolic acid fiber-reinforced polylactic acid degradable composites
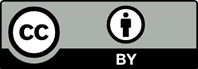
A continuous polyglycolic acid (PGA) fiber-reinforced polylactic acid (PLA) degradable composite was proposed for application in biodegradable load-bearing bone implant. The fused deposition modeling (FDM) process was used to fabricate composite specimens. The influences of the printing process parameters, such as layer thickness, printing spacing, printing speed, and filament feeding speed on the mechanical properties of the PGA fiber-reinforced PLA composites, were studied. The thermal properties of the PGA fiber and PLA matrix were investigated by using differential scanning calorimetry (DSC) and thermogravimetric analysis (TGA). The internal defects of the as-fabricated specimens were characterized by the micro-Xray 3D imaging system. During the tensile experiment, a full-field strain measurement system was used to detect the strain map and analysis the fracture mode of the specimens. A digital microscope and field emission electron scanning microscopy were used to observe the interface bonding between fiber and matrix and fracture morphologies of the specimens. The experimental results showed that the tensile strength of specimens was related to their fiber content and porosity. The printing layer thickness and printing spacing had significant impacts on the fiber content. The printing speed did not affect the fiber content but had a slight effect on the tensile strength. Reducing the printing spacing and layer thickness could increase the fiber content. The tensile strength (along the fiber direction) of the specimen with 77.8% fiber content and 1.82% porosity was the highest, reaching 209.32 ± 8.37 MPa, which is higher than the tensile strength of the cortical bone and polyether ether ketone (PEEK), indicating that the continuous PGA fiber-reinforced PLA composite has great potential in the manufacture of biodegradable load-bearing bone implants.
1. Javaid M, Haleem A, 2018, Additive manufacturing applications in orthopaedics: A review. J Clin Orthop Trauma, 9(3):202–206. https://doi.org/10.1016/j.jcot.2018.04.008
2. Rony L, Lancigu R, Hubert L, 2018, Intraosseous metal implants in orthopedics: A review. Morphologie, 102(339):231–242. https://doi.org/10.1016/j.morpho.2018.09.003
3. Tong Y, Kaplan DJ, Spivak JM, et al., 2020, Three-dimensional printing in spine surgery: A review of current applications. Spine J, 20(6):833–846. https://doi.org/10.1016/j.spinee.2019.11.004
4. Li C, Pisignano D, Zhao Y, et al., 2020, Advances in medical applications of additive manufacturing. Engineering, 6(11):1222–1231. https://doi.org/10.1016/j.eng.2020.02.018
5. Kaur M, Singh K, 2019, Review on titanium and titanium based alloys as biomaterials for orthopaedic applications. Mater Sci Eng C, 102:844–862. https://doi.org/10.1016/j.msec.2019.04.064
6. Chen CH, Chang WJ, Chen YS, et al., 2022, Development of a novel hybrid suture anchor for osteoporosis by integrating titanium 3D printing and traditional machining. Int J Bioprint, 8(4):608. https://doi.org/10.18063/ijb.v8i4.608
7. Wang F, Chen H, Yang P, et al., 2020, Three-dimensional printed porous tantalum prosthesis for treating inflammation after total knee arthroplasty in one-stage surgery: A case report. J Int Med Res, 48(3):300060519891280. https://doi.org/10.1177/0300060519891280
8. Bandyopadhyay A, Mitra I, Shivaram A, et al., 2019, Direct comparison of additively manufactured porous titanium and tantalum implants towards in vivo osseointegration. Addit Manuf, 28:259–266. https://doi.org/10.1016/j.addma.2019.04.025
9. Haleem A, Javaid M, 2019, Polyether ether ketone (PEEK) and its 3D printed implants applications in medical field: An overview. Clin Epidemiol Global Health, 7(4):571–577. https://doi.org/10.1016/j.cegh.2019.01.003
10. Liu D, Fu J, Fan H, et al., 2018, Application of 3D-printed PEEK scapula prosthesis in the treatment of scapular benign fibrous histiocytoma: A case report. J Bone Oncol, 12:78–82. https://doi.org/10.1016/j.jbo.2018.07.012
11. Manam NS, Harun WSW, Shri DNA, et al., 2017, Study of corrosion in biocompatible metals for implants: A review. J Alloys Compd, 701:698–715. https://doi.org/10.1016/j.jallcom.2017.01.196
12. Chen Z, Chen Y, Ding J, et al., 2023, Blending strategy to modify PEEK-based orthopedic implants. Compos Part B Eng, 250:110427. https://doi.org/10.1016/j.compositesb.2022.110427
13. Baptista R, Guedes M, 2021, Morphological and mechanical characterization of 3D printed PLA scaffolds with controlled porosity for trabecular bone tissue replacement. Mater Sci Eng C Mater Biol Appl, 118:111528. https://doi.org/10.1016/j.msec.2020.111528
14. Saniei H, Mousavi S, 2020, Surface modification of PLA 3D-printed implants by electrospinning with enhanced bioactivity and cell affinity. Polymer, 196:122467. https://doi.org/10.1016/j.polymer.2020.122467
15. Myers D, Abdel-Wahab A, Hafeez F, et al., 2022, Optimisation of the additive manufacturing parameters of polylactic acid (PLA) cellular structures for biomedical applications. J Mech Behav Biomed Mater, 136:105447. https://doi.org/10.1016/j.jmbbm.2022.105447
16. Wang X, Jiang M, Zhou Z, et al., 2017, 3D printing of polymer matrix composites: A review and prospective. Compos Part B Eng, 110:442–458. https://doi.org/10.1016/j.compositesb.2016.11.034
17. Ilyas RA, Sapuan SM, Harussani MM, et al., 2021, Polylactic acid (PLA) biocomposite: Processing, additive manufacturing and advanced applications. Polymers (Basel), 13(8):1326. https://doi.org/10.3390/polym13081326
18. Zhao X, Liu J, Li J, et al., 2022, Strategies and techniques for improving heat resistance and mechanical performances of poly(lactic acid) (PLA) biodegradable materials. Int J Biol Macromol, 218:115–134. https://doi.org/10.1016/j.ijbiomac.2022.07.091
19. Backes EH, Fernandes EM, Diogo GS, et al., 2021, Engineering 3D printed bioactive composite scaffolds based on the combination of aliphatic polyester and calcium phosphates for bone tissue regeneration. Mater Sci Eng C Mater Biol Appl, 122:111928. https://doi.org/10.1016/j.msec.2021.111928
20. Zhang H, Mao X, Du Z, et al., 2016, Three dimensional printed macroporous polylactic acid/hydroxyapatite composite scaffolds for promoting bone formation in a critical-size rat calvarial defect model. Sci Technol Adv Mater, 17(1):136–148. https://doi.org/10.1080/14686996.2016.1145532
21. Aihemaiti P, Jiang H, Aiyiti W, et al., 2022, Optimization of 3D printing parameters of biodegradable polylactic acid/hydroxyapatite composite bone plates. Int J Bioprint, 8(1):153–166. https://doi.org/10.18063/ijb.v8i1.490
22. Zhang B, Wang L, Song P, et al., 2021, 3D printed bone tissue regenerative PLA/HA scaffolds with comprehensive performance optimizations. Mater Des, 201:109490. https://doi.org/10.1016/j.matdes.2021.109490
23. Wang W, Zhang B, Li M, et al., 2021, 3D printing of PLA/ n-HA composite scaffolds with customized mechanical properties and biological functions for bone tissue engineering. Compos Part B Eng, 224(1):109192. https://doi.org/10.1016/j.compositesb.2021.109192
24. Maqsood N, Rimašauskas M, 2021, Delamination observation occurred during the flexural bending in additively manufactured PLA-short carbon fiber filament reinforced with continuous carbon fiber composite. Results Eng, 11:100246. https://doi.org/10.1016/j.rineng.2021.100246
25. Dou H, Cheng Y, Ye W, et al., 2020, Effect of process parameters on tensile mechanical properties of 3D printing continuous carbon fiber-reinforced PLA composites. Materials (Basel), 13(17):3850. https://doi.org/10.3390/ma13173850
26. Ali W, Mehboob A, Han M-G, et al., 2020, Novel biodegradable hybrid composite of polylactic acid (PLA) matrix reinforced by bioactive glass (BG) fibres and magnesium (Mg) wires for orthopaedic application. Compos Struct, 245:112322. https://doi.org/10.1016/j.compstruct.2020.112322
27. Wang G, Zhang D, Li B, et al., 2019, Strong and thermal-resistance glass fiber-reinforced polylactic acid (PLA) composites enabled by heat treatment. Int J Biol Macromol, 129:448–459. https://doi.org/10.1016/j.ijbiomac.2019.02.020
28. Long Y, Zhang Z, Fu K, et al., 2021, Efficient plant fibre yarn pre-treatment for 3D printed continuous flax fibre/ poly(lactic) acid composites. Compos Part B Eng, 227:109389.
https://doi.org/10.1016/j.compositesb.2021.109389
29. Baley C, Bourmaud A, Davies P, 2021, Eighty years of composites reinforced by flax fibres: A historical review. Compos Part A Appl Sci Manuf, 144:106333. https://doi.org/10.1016/j.compositesa.2021.106333
30. Akmal Zia A, Tian X, Liu T, et al., 2023, Mechanical and energy absorption behaviors of 3D printed continuous carbon/Kevlar hybrid thread reinforced PLA composites. Compos Struct, 303:116386. https://doi.org/10.1016/j.compstruct.2022.116386
31. Tian X, Todoroki A, Liu T, et al., 2022, 3D printing of continuous fiber reinforced polymer composites: Development, application, and prospective. CJME:AM, 001(001):50–69. https://doi.org/10.1016/j.cjmeam.2022.100016
32. Kabir SMF, Mathur K, Seyam A-FM, 2020, A critical review on 3D printed continuous fiber-reinforced composites: History, mechanism, materials and properties. Compos Struct, 232:111476. https://doi.org/10.1016/j.compstruct.2019.111476
33. Maqsood N, Rimašauskas M, 2021, Characterization of carbon fiber reinforced PLA composites manufactured by fused deposition modeling. Compos Part C, 4:100112. https://doi.org/10.1016/j.jcomc.2021.100112
34. Tian X, Liu T, Yang C, et al., 2016, Interface and performance of 3D printed continuous carbon fiber reinforced PLA composites. Compos Part A Appl Sci Manuf, 88: 198–205. https://doi.org/10.1016/j.compositesa.2016.05.032
35. Hou Z, Tian X, Zheng Z, et al., 2020, A constitutive model for 3D printed continuous fiber reinforced composite structures with variable fiber content. Composites Part B Eng, 189:107893. https://doi.org/10.1016/j.compositesb.2020.107893
36. Hedayati SK, Behravesh AH, Hasannia S, et al., 2022, Additive manufacture of PCL/nHA scaffolds reinforced with biodegradable continuous fibers: Mechanical properties, in-vitro degradation profile, and cell study. Eur Polym J, 162:110876. https://doi.org/10.1016/j.eurpolymj.2021.110876
37. Takayama T, Daigaku Y, Ito H, et al., 2014, Mechanical properties of bio-absorbable PLA/PGA fiber-reinforced composites. J Mech Sci Technol, 28(10):4151–4154. https://doi.org/10.1007/s12206-014-0927-3
38. Ko HS, Lee S, Lee D, et al., 2021, Mechanical properties and bioactivity of poly(lactic acid) composites containing poly(glycolic acid) fiber and hydroxyapatite particles. Nanomaterials (Basel), 11(1):249. https://doi.org/10.3390/nano11010249
39. Hedayati SK, Behravesh AH, Hasannia S, et al., 2020, 3D printed PCL scaffold reinforced with continuous biodegradable fiber yarn: A study on mechanical and cell viability properties. Polym Test, 83:106347. https://doi.org/10.1016/j.polymertesting.2020.106347
40. Rodríguez-Reyna SL, Mata C, Díaz-Aguilera JH, et al., 2022, Mechanical properties optimization for PLA, ABS and Nylon + CF manufactured by 3D FDM printing. Mater Today Commun, 33:104774. https://doi.org/https://doi.org/10.1016/j.mtcomm.2022.104774
41. Liu Z, Lei Q, Xing S, 2019, Mechanical characteristics of wood, ceramic, metal and carbon fiber-based PLA composites fabricated by FDM. J Mater Res Technol, 8(5):3741–3751. https://doi.org/10.1016/j.jmrt.2019.06.034
42. Han X, Yang D, Yang C, et al., 2019, Carbon fiber reinforced PEEK composites based on 3D-printing technology for orthopedic and dental applications. J Clin Med, 8(2):240. https://doi.org/10.3390/jcm8020240
43. Vlasea M, Basalah A, Azhari A, et al., (eds), 2015, Chapter 11: Additive manufacturing for bone load bearing applications, in 3D Bioprinting and Nanotechnology in Tissue Engineering and Regenerative Medicine (Second Edition), Academic Press, 231–263.