Novel High-Speed 3D Printing Method Using Selective Oil Sintering with Thermoplastic Polyurethane Powder Printing
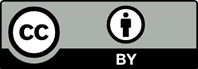
Present methods used in three-dimensional (3D) printing, such as selective laser sintering (SLS) and multijet fusion (MJF), have limited applications, especially in relation to the manufacturing of biomedical products. The speed of SLS printing is too low, and high-speed 3D printing technology with MJF uses carbon black particles as a fusing agent, which cannot be removed from the completed 3D printed products. Carbon black and high-energy lasers are not suitable for biomedical applications, especially human implants. A new high-speed 3D method is therefore required. In this study, we used hot oil droplets (175°C) as a new type of fusing agent to melt the biomaterial thermoplastic polyurethane (TPU) powder particles to define the print area. This method replaces lasers and the carbon black fusing agent in high-speed 3D printing technology and is more energy efficient. In addition, this method can be used to not only print on TPU, but also on other flexible materials.
1. Drupitha MP, Das B, Parameswaran R, et al., 2018, Hybrid Electrospun Fibers Based on TPU-PDMS and Spherical Nanohydroxyapatite for Bone Tissue Engineering. Mater Today Commun, 16:264–73. https://doi.org/10.1016/j.mtcomm.2018.06.013
2. Bachtiar EO, Erol O, Millrod M, et al., 2020, 3D Printing and Characterization of a Soft and Biostable Elastomer with High Flexibility and Strength for Biomedical Applications. J Mech Behav Biomed Mater, 104:103649. https://doi.org/10.1016/j.jmbbm.2020.103649
3. Lu Q, Song KY, Feng Y, et al., 2021, Fabrication of Suspended Uniform Polymer Microfibers by FDM 3D Printing. CIRP J Manufa Sci Technol, 32:179–87. https://doi.org/10.1016/j.cirpj.2020.11.005
4. Fina F, Goyanes A, Gaisford S, et al., 2017, Selective Laser Sintering (SLS) 3D Printing of Medicines. Int J Pharm, 529:285–93. https://doi.org/10.1016/j.ijpharm.2017.06.082
5. Guo J, Zeng Y, Li P, et al., 2019, Fine Lattice Structural Titanium Dioxide Ceramic Produced by DLP 3D Printing. Ceram Int, 45:23007–12. https://doi.org/10.1016/j.ceramint.2019.07.346
6. Srinivas RP, Alomarah A, Masood SH, et al., 2020, Mechanical Response of a Compressed Novel 3D Tetrachiral Structure Processed by MJF 3D Printing Process. Mater Today, 46:4776–81.
7. Xu Z, Wang Y, Wu D, et al., 2019, The Process and Performance Comparison of Polyamide 12 Manufactured by Multi Jet Fusion and Selective Laser Sintering. J Manuf Process, 47:419–26.
8. HP Development Company, 2018, L.P. Introduction of HP 3D Printers. Available form: http://www8.hp.com/uk/en/printers/3dprinters [Last accessed on 2018 Oct 23].
9. Sillania F, Kleijnena R, Vetterlia M, et al., 2019, Selective Laser Sintering and Multi Jet Fusion: Process-Induced Modification of the Raw Materials and Analyses of Parts Performance. Addit Manuf, 27:32–41. https://doi.org/10.1016/j.addma.2019.02.004
10. Espera AH Jr., Valino AD, Palaganas JO, et al., 2019, 3D Printing of a Robust Polyamide-12-Carbon Black Composite via Selective Laser Sintering: Thermal and Electrical Conductivity, Macromol. Mater Eng, 304:1800718. https://doi.org/10.1002/mame.201800718
11. Tey WS, Cai C, Zhou K, 2021, A Comprehensive Investigation on 3D Printing of Polyamide 11 and Thermoplastic Polyurethane via Multi Jet Fusion. Polymers, 13:2139. https://doi.org/10.3390/polym13132139