Laser Additive Manufacturing of Zinc Targeting for Biomedical Application
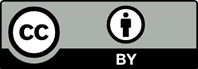
Biodegradable zinc (Zn) is expected to be used in clinical application like bone tissue engineering scaffolds, since it possesses favorable biocompatibility and suitable degradation rate. Laser powder bed fusion (LPBF), which is a typical additive manufacturing technique, offers tremendous advantages in fabricating medical devices with personalized geometric shape and complex porous structure. Therefore, the combination of LPBF and biodegradable Zn has gained intensive attention and also achieved rapid development in recent years. However, it severely challenges the formation quality and resultant performance of LPBF-processed Zn-based materials, due to the evaporation and element loss during laser processing. In this study, the current research status and future research trends for LPBF of Zn-based implants are reviewed from comprehensive viewpoints including formation quality, microstructure feature, and performance. The influences of powder characteristics and process parameters on formation quality are described systematically. The microstructure evolution, mechanical properties, as well as the degradation behavior are also discussed. Finally, the research perspectives for LPBF of Zn are summarized, aiming to provide guideline for future study.
1. Li HF, Wang PY, Lin GC, et al., 2021, The Role of Rare Earth Elements in Biodegradable Metals: A Review. Acta Biomaterialia, 129:33–42. https://doi.org/10.1016/j.actbio.2021.05.014
2. Bai L, Gong C, Chen XH, et al., 2019, Additive Manufacturing of Customized Metallic Orthopedic Implants: Materials, Structures, and Surface Modifications. Metals, 9:P1004. https://doi.org/10.3390/met9091004
3. Shuai CJ, Xue LF, Gao CD, et al., 2018, Selective Laser Melting of Zn-Ag Alloys for Bone Repair: Microstructure, Mechanical Properties and Degradation Behaviour. Virtual Phys Prototyp, 13:146–54. https://doi.org/10.1080/17452759.2018.1458991
4. Gu XN, Zhou WR, Zheng YF, et al., 2010, Corrosion Fatigue Behaviors of two Biomedical Mg Alloys-AZ91D and WE43-in Simulated Body Fluid. Acta Biomater, 6:4605–13. https://doi.org/10.1016/j.actbio.2010.07.026
5. Zhao DW, Witte F, Lu FQ, et al., 2017, Current Status on Clinical Applications of Magnesium-Based Orthopaedic Implants: A Review from Clinical Translational Perspective. Biomaterials, 112:287–302. https://doi.org/10.1016/j.biomaterials.2016.10.017
6. Demir AG, Monguzzi L, Previtali B, 2017, Selective Laser Melting of Pure Zn with High Density for Biodegradable Implant Manufacturing. Addit Manuf, 15:20–8.
7. Zheng YF, Gu XN, Witte F, 2014, Biodegradable Metals. Mater Sci Eng R Rep, 77:1–34.
8. Shuai CJ, He CX, Xu L, et al., 2018, Wrapping Effect of Secondary Phases on the Grains: Increased Corrosion Resistance of Mg-Al Alloys. Virtual Phys Prototyp, 13:292–300. https://doi.org/10.1080/17452759.2018.1479969
9. Kraus T, Moszner F, Fischerauer S, et al., 2014, Biodegradable Fe-Based Alloys for Use in Osteosynthesis: Outcome of an In Vivo Study After 52 Weeks. Acta Biomater, 10:3346–53. https://doi.org/10.1016/j.actbio.2014.04.007
10. Shuai CJ, He CX, Qian GW, et al., 2021, Mechanically Driving Supersaturated Fe-Mg Solid Solution for Bone Implant: Preparation, Solubility and Degradation. Compos B Eng, 207:108564. https://doi.org/10.1016/j.compositesb.2020.108564
11. Hojyo S, Fukada T, 2016, Zinc Transporters and Signaling in Physiology and Pathogenesis. Arch Biochem Biophys, 611:43–50. https://doi.org/10.1016/j.abb.2016.06.020
12. Gong H, Wang K, Strich R, et al., 2015, In Vitro Biodegradation Behavior, Mechanical Properties, and Cytotoxicity of Biodegradable Zn-Mg Alloy. J Biomed Mater Res B Appl Biomater, 103:1632–40.
13. Yang H, Jia B, Zhang Z, et al., 2020, Alloying Design of Biodegradable Zinc as Promising Bone Implants for Load-Bearing Applications. Nat Commun, 11:1–16.
14. Du Y, Gu D, Xi L, et al., 2020, Laser Additive Manufacturing of Bio-Inspired Lattice Structure: Forming Quality, Microstructure and Energy Absorption Behavior. Mater Sci Eng A, 773:138857.
15. Gu DD, Shi XY, Poprawe R, et al., 2021, Material-Structure-Performance Integrated Laser-Metal Additive Manufacturing. Science, 372:932–6. https://doi.org/10.1126/science.abg1487
16. Sing S, Yeong W, 2020, Laser Powder Bed Fusion for Metal Additive Manufacturing: Perspectives on Recent Developments. Virtual Phys Prototyp, 15:359–70.
17. Harooni A, Nasiri AM, Gerlich AP, et al., 2016, Processing Window Development for Laser Cladding Of Zirconium on Zirconium Alloy. J Mater Process Technol, 230:263–71. https://doi.org/10.1016/j.jmatprotec.2015.11.028
18. Liu FG, Lin X, Song K, et al., 2017, Microstructure and Mechanical Properties of Laser Forming Repaired 300M Steel. Acta Metallurgica Sin, 53:325–34. https://doi.org/10.11900/0412.1961.2016.00282
19. Narra SP, Mittwede PN, Wolf SD, et al., 2019, Additive Manufacturing in Total Joint Arthroplasty. Orthop Clin N Am, 50:13–20. https://doi.org/10.1016/j.ocl.2018.08.009
20. Campbell TA, Ivanova OS, 2013, 3D Printing of Multifunctional Nanocomposites. Nano Today, 8:119–20. https://doi.org/10.1016/j.nantod.2012.12.002
21. Zhao D, Witte F, Lu F, et al., 2017, Current Status on Clinical Applications of Magnesium-Based Orthopaedic Implants: A Review from Clinical Translational Perspective. Biomaterials, 112:287–302. https://doi.org/10.1016/j.biomaterials.2016.10.017
22. Hyer H, Zhou L, Mehta A, et al., 2021, Composition-Dependent Solidification Cracking of Aluminum-Silicon Alloys during Laser Powder Bed Fusion. Acta Mater, 208:116698. https://doi.org/10.1016/j.actamat.2021.116698
23. Zhou S, Liang YJ, Zhu Y, et al., 2021, Ultrashort-Time Liquid Phase Sintering of High-Performance Fine-Grain Tungsten Heavy Alloys by Laser Additive Manufacturing. J Mater Sci Technol, 90:30–6.
24. Chakraborty A, Tangestani R, Batmaz R, et al., 2022, In Process Failure Analysis of Thin-Wall Structures Made by Laser Powder Bed Fusion Additive Manufacturing. J Mater Sci Technol, 98:233–43.
25. Espana FA, Balla VK, Bose S, et al., 2010, Design and Fabrication of CoCrMo Alloy Based Novel Structures for Load Bearing Implants Using Laser Engineered Net Shaping. Mater Sci Eng C Mater Biol Appl, 30:50–7. https://doi.org/10.1016/j.msec.2009.08.006
26. Vignesh M, Kumar GR, Sathishkumar M, et al., 2021, Development of Biomedical Implants through Additive Manufacturing: A Review. J Mater Eng Perform, 30:4735–44. https://doi.org/10.1007/s11665-021-05578-7
27. Kok Y, Tan XP, Wang P, et al., 2018, Anisotropy and Heterogeneity of Microstructure and Mechanical Properties in Metal Additive Manufacturing: A Critical Review. Mater Des, 139:565–86. https://doi.org/10.1016/j.matdes.2017.11.021
28. Singh S, Ramakrishna S, Singh R, 2017, Material Issues in Additive Manufacturing: A Review. J Manuf Processes, 25:185–200. https://doi.org/10.1016/j.jmapro.2016.11.006
29. Hase T, Ohtagaki T, Yamaguchi M, et al., 2016, Effect of Aluminum or Zinc Solute Addition on Enhancing Impact Fracture Toughness in Mg-Ca Alloys. Acta Mater, 104:283–94.
30. Strano G, Hao L, Everson RM, et al., 2013, A New Approach to the Design and Optimisation of Support Structures in Additive Manufacturing. Int J Adv Manuf Technol, 66:1247–54. https://doi.org/10.1007/s00170-012-4403-x
31. Montani M, Demir AG, Mostaed E, et al., 2017, Processability of Pure Zn and Pure Fe by SLM for Biodegradable Metallic Implant Manufacturing. Rapid Prototyp J, 23:514–23. https://doi.org/10.1108/rpj-08-2015-0100
32. Shuai C, Cheng Y, Yang Y, et al., 2019, Laser Additive Manufacturing of Zn-2Al Part for Bone Repair: Formability, Microstructure and Properties. J Alloys Compd, 798:606–15.
33. Yang Y, Yuan F, Gao C, et al., 2018, A Combined Strategy to Enhance the Properties of Zn by Laser Rapid Solidification and Laser Alloying. J Mech Behav Biomed Mater, 82:51–60.
34. Wen P, Jauer L, Voshage M, et al., 2018, Densification Behavior of Pure Zn Metal Parts Produced by Selective Laser Melting for Manufacturing Biodegradable Implants. J Mater Process Technol, 258:128–37. https://doi.org/10.1016/j.jmatprotec.2018.03.007
35. Qin Y, Wen P, Guo H, et al., 2019, Additive Manufacturing of Biodegradable Metals: Current Research Status and Future Perspectives. Acta Biomat, 98:3–22. https://doi.org/10.1016/j.actbio.2019.04.046
36. Chen Y, Wen P, Voshage M, et al., 2019, Laser Additive Manufacturing of Zn Metal Parts for Biodegradable Implants: Effect of Gas Flow on Evaporation and Formation Quality. J Laser Appl, 31:022304.
37. Meng B, Fu MW, Fu CM, et al., 2015, Multivariable Analysis of Micro Shearing Process Customized for Progressive Forming of Micro-Parts. Int J Mech Sci, 93:191–203. https://doi.org/10.1016/j.ijmecsci.2015.01.017
38. Bhatt NH, Pati AR, Kumar A, et al., 2017, High Mass Flux Spray Cooling with Additives of Low Specific Heat and Surface Tension: A Novel Process to Enhance the Heat Removal Rate. Appl Therm Eng, 120:537–48.
39. Beals J, She Y, Jagdale V, et al., 2020, Structured Powder Particles for Feedstock Improvement for Laser Based Additive Manufacturing. Philadelphia, PA: MyScienceWork.
40. Gu DD, Meiners W, Wissenbach K, et al., 2013, Laser Additive Manufacturing of Metallic Components: Materials, Processes and Mechanisms. Int Mater Rev, 57:133–64.
41. Sing SL, An J, Yeong WY, et al., 2016, Laser and Electron-Beam Powder-Bed Additive Manufacturing of Metallic Implants: A Review on Processes, Materials and Designs. J Orthop Res, 34:369–85.
42. Brika SE, Letenneur M, Dion CA, et al., 2020, Influence of Particle Morphology and Size Distribution on the Powder Flowability and Laser Powder Bed Fusion Manufacturability of Ti-6Al-4V Alloy. Addit Manuf, 31:100929. https://doi.org/10.1016/j.addma.2019.100929
43. Leitz, K., -H., et al., 2018, Fundamental Analysis of the Influence of Powder Characteristics in Selective Laser Melting of molybdenum based on a multi-physical simulation model. Int J Refract Met Hard Mater, 72:1–8.
44. Halada K, Minagawa K, Chiba K, et al., 2009, Solidified Microstructure of Zn-Al Alloy Powders Produced by Various Atomization Methods. J Jpn Soc Powder Powder Metallurgy, 40:1160–5.
45. Tong L, Reddy RG, 2005, Synthesis of Titanium Carbide Nano-Powders by Thermal Plasma. Scr Mater, 52:1253–8.
46. Ruvalcaba BE, Arrieta E, Escarcegaa AH, et al., Manufacturing Process and Parameters Development for Water-atomized Zinc Powder for Selective Laser Melting Fabrication. United States: The University of Texas at Austin.
47. Sungkhaphaitoon P, Plookphol T, Wisutmethangoon S, 2012, Design and Development of a Centrifugal Atomizer for Producing Zinc Metal Powder. Int J Appl Phys Math, 2:77.
48. Wen P, Voshage M, Jauer L, et al., 2018, Laser Additive Manufacturing of Zn Metal Parts for Biodegradable Applications: Processing, Formation Quality and Mechanical Properties. Mater Des, 155:36–45.
49. Debroy T, Wei HL, Zuback J, et al., 2018, Additive manuFACTuring of Metallic Components-Process, Structure and Properties. Progress Mater Sci, 92:112–224.
50. Ebner T, Moser M, Shebl O, et al., 2009, Morphological Analysis at Compacting Stage is a Valuable Prognostic Tool for ICSI Patients. Reprod Biomed Online, 18:61–6. https://doi.org/10.1016/s1472-6483(10)60425-7
51. Liu C, Zhang M, Chen CJ, 2017, Effect of Laser Processing Parameters on Porosity, Microstructure and Mechanical Properties of Porous Mg-Ca Alloys Produced by Laser Additive Manufacturing. Mater Sci Eng Struct Mater Properties Microstruct Process, 703:359–71. https://doi.org/10.1016/j.msea.2017.07.031
52. Wang MF, Xiao DH, Zhou PF, et al., 2018, Effects of Rare Earth Yttrium on Microstructure and Properties of Mg-Al-Zn Alloy. J Alloys Compd, 742:232–9. https://doi.org/10.1016/j.jallcom.2018.01.234
53. Wei KW, Gao M, Wang ZM, et al., 2014, Effect of Energy Input on Formability, Microstructure and Mechanical propErties of Selective Laser Melted AZ91D Magnesium Alloy. Mater Sci Eng Struct A Struct Mater Properties Microstruct Process, 611:212–22. https://doi.org/10.1016/j.msea.2014.05.092
54. Katayama S, Kobayashi Y, Mizutani M, et al., 2001, Effect of Vacuum on Penetration and Defects in Laser Welding. J Laser Appl, 13:187–92.
55. Gu D, Shen Y, 2006, Processing and Microstructure of Submicron WC-Co Particulate Reinforced Cu Matrix Composites Prepared by Direct Laser Sintering. Mater Sci Eng A, 435:54–61.
56. Yu GQ, Gu DD, Dai DH, et al., 2016, On the Role of Processing Parameters in Thermal Behavior, Surface Morphology and Accuracy during Laser 3D Printing of Aluminum Alloy. J Phys D-Appl Phys, 49:135501. https://doi.org/10.1088/0022-3727/49/13/135501
57. Yu GQ, Gu DD, Dai DH, et al., 2016, Influence of Processing Parameters on Laser Penetration Depth and Melting/Re-Melting Densification during Selective Laser Melting of Aluminum Alloy. Appl Phys A Mater Sci Process, 122:891. https://doi.org/10.1007/s00339-016-0428-6
58. Shabahang S, Kaufman JJ, Deng DS, et al., 2011, Observation of the Plateau-Rayleigh Capillary Instability in Multi-Material Optical Fibers. Appl Phys Lett, 99:3.
59. Qiu C, Adkins N, Attallah MM, 2016, Selective Laser Melting of Invar 36: Microstructure and Properties. Acta Mater, 103:382–95.
60. Shao B, Wu S, Shan D, et al., 2019, The Effect of Thermal Cycling Process between High and Low Temperatures on the Microstructure and Properties of Mg-10Li-3Al-3Zn-0.25SI alloy. Mater Lett, 254:167-170.
61. Wei HL, Cao Y, Liao WH, et al., 2020, Mechanisms on Inter-Track Void Formation and Phase Transformation during Laser Powder Bed Fusion of Ti-6Al-4V. Addit Manuf, 34:101221. https://doi.org/10.1016/j.addma.2020.101221
62. Kh A, Jz A, Fd A, et al., 2021, Particle Distribution and Microstructure of IN718/WC Composite Coating Fabricated by Electromagnetic Compound Field-Assisted Laser Cladding. Appl Surf Sci, 545:149078.
63. Martin AA, Calta NP, Khairallah SA, et al., 2019, Dynamics of Pore Formation during Laser Powder Bed Fusion Additive Manufacturing. Nat Commun, 10:1987.
64. Kreitcberg A, Brailovski V, Prokoshkin S, 2018, New Biocompatible Near-Beta Ti-Zr-Nb Alloy Processed by Laser Powder Bed Fusion: Process Optimization. J Mater Process Technol, 252:821–9. https://doi.org/10.1016/j.jmatprotec.2017.10.052
65. Xu ZF, Liang P, Yang W, et al., 2014, Effects of Laser Energy Density on Forming Accuracy and Tensile Strength of Selective Laser Sintering Resin Coated Sands. China Foundry, 11:151–6.
66. Shuai CJ, Yang ML, Deng F, et al., 2020, Forming Quality, Mechanical Properties, and Anti-Inflammatory Activity of Additive Manufactured Zn-Nd Alloy. J Zhejiang Univ Sci A, 21:876–91. https://doi.org/10.1631/jzus.A2000186
67. Wang Q, Lu Y, Zeng X, et al., 1999, Study on the Fluidity of AZ91+xRE Magnesium Alloy. Mater Sci Eng A, 271:109–15.
68. Dong L, Correia J, Barth N, et al., 2017, Finite Element Simulations of Temperature Distribution and of Densification of a Titanium Powder During Metal Laser Sintering. Addit Manuf, 13:37–48.
69. Foteinopoulos P, Papacharalampopoulos A, Angelopoulos K, et al., 2020, Development of a Simulation Approach for Laser Powder bed Fusion Based on Scanning Strategy Selection. Int J Adv Manuf Technol, 108:3085–100.
70. Liu C, Tong J, Jiang M, et al., 2019, Effect of Scanning Strategy on Microstructure and Mechanical Properties of Selective Laser Melted Reduced Activation Ferritic/Martensitic Steel. Mater Sci Eng A, 766:138364.
71. Cheng B, Shrestha S, Chou K, 2016, Stress and Deformation Evaluations of Scanning Strategy Effect in Selective Laser Melting. Addit Manuf, 12:240–51.
72. Kabir H, Munir K, Wen C, et al., 2021, Recent Research and Progress of Biodegradable Zinc Alloys and Composites for Biomedical Applications: Biomechanical and Biocorrosion Perspectives. Bioact Mater, 6:836–79.
73. Lee H, Lim CH, Low MJ, et al., 2017, Lasers in Additive Manufacturing: A Review. Int J Precision Eng Manuf Green Technol, 4:307–22. https://doi.org/10.1007/s40684-017-0037-7
74. Chen YZ, Wen P, Voshage M, et al., 2019, Laser Additive Manufacturing of Zn Metal Parts for Biodegradable Implants: Effect of Gas Flow on Evaporation and Formation Quality. J Laser Appl, 31:1003. https://doi.org/10.2351/1.5096118
75. Lu FG, Li XB, Li ZG, et al., 2015, Formation and influence mechanism of keyhole-induced porosity in deep-penetration laser welding based on 3D transient modeling. Int J Heat Mass Transfer, 90:1143–52. https://doi.org/10.1016/j.ijheatmasstransfer.2015.07.041
76. Young ZA, Guo Q, Parab ND, et al., 2020, Types of Spatter and their Features and Formation Mechanisms in Laser Powder Bed Fusion Additive Manufacturing Process. Addit Manuf, 36:101438. https://doi.org/10.1016/j.addma.2020.101438
77. Wen P, Qin Y, Chen Y, et al., 2019, Laser Additive Manufacturing of Zn Porous Scaffolds: Shielding Gas Flow, Surface Quality and Densification. J Mater Sci Technol, 35:368–76.
78. Jauer L, Jülich B, Voshage M, et al., 2015, Selective Laser Melting of Magnesium Alloys.
79. Yang Y, Yang M, He C, et al., 2021, Rare Earth Improves Strength and Creep Resistance of Additively Manufactured Zn Implants. Compos B Eng, 216:108882. https://doi.org/10.1016/j.compositesb.2021.108882
80. Elmer JW, Allen S M, Eagar TW, 1989, Microstructural Development during Solidification of Stainless Steel Alloys. Metall Trans A, 20:2117–31.
81. Shuai C, Xue L, Gao C, et al., 2018, Selective Laser Melting of Zn-Ag Alloys for Bone Repair: Microstructure, Mechanical Properties and Degradation Behaviour. Virtual Phys Prototyp, 13:146–54.
82. Qin Y, Wen P, Xia D, et al., 2020, Effect of Grain Structure on the Mechanical Properties and In Vitro Corrosion Behavior of Additively Manufactured Pure Zn. Addit Manuf, 33:101134. https://doi.org/10.1016/j.addma.2020.101134
83. Gandin R, 1993, Probabilistic modelling of microstructure formation in solidification processes. Acta Metall Mater, 41:345–60.
84. Wei HL, Elmer JW, de Broy T, 2017, Three-Dimensional Modeling of Grain Structure Evolution during Welding of an Aluminum Alloy. Acta Mater, 126:413–25.
85. de Rosa C, Park C, Thomas EL, et al., 2000, Microdomain Patterns from Directional Eutectic Solidification and Epitaxy. Nature, 405:433–7.
86. Zheng W, He Y, Yang J, et al., 2019, Influence of Crystallographic Orientation of Epitaxial Solidification on the Initial Instability during the Solidification of Welding Pool. J Manuf Proc, 38:298–307.
87. Sullivan EM, 2021, Influence of Reaction Synthesis Feedstocks on Solidification Defect Formation and Microstructure-Property Relationships in Electron Beam Freeform Fabrication of Aluminum Metal Matrix Composites. Illinois: Colorado School of Mines.
88. Zhu YY, Tang HB, Li Z, et al., 2019, Solidification Behavior and Grain Morphology of Laser Additive Manufacturing Titanium Alloys. J Alloys Compd, 777:712–6.
89. Wang X, Zhang C, Cui X, et al., 2021, Novel Gradient Alloy Steel with Quasi-Continuous Ratios Fabricated by SLM: Material Microstructure and Wear Mechanism. Mater Charact, 174:111020.
90. Rappaz M, David SA, Vitek JM, et al., 1989, Development of Microstructures in Fe15Ni15Cr Single Crystal Electron Beam Welds. Metall Trans A, 20:1125–38.
91. Soler R, Evirgen A, Yao M, et al., 2018, Microstructural and Mechanical Characterization of an Equiatomic YGdTbDyHo High Entropy Alloy with Hexagonal Close-Packed Structure. Acta Mater, 156:86–96.
92. Paidar V, Capek J, Ostapovets A, 2018, Secondary Twinning in Zinc. Philos Mag Lett, 98:437–45. https://doi.org/10.1080/09500839.2019.1566799
93. Li Y, Shi J, Jahr H, et al., 2021, Improving the Mechanical Properties of Additively Manufactured Micro-Architected Biodegradable Metals. JOM J Miner Metals Mater Soc, 73:1–11.
94. Liu S, Yang W, Shi X, et al., 2019, Influence of Laser Process Parameters on the Densification, Microstructure, and Mechanical Properties of a Selective Laser Melted AZ61 Magnesium Alloy. J Alloys Compd, 808:151160.
95. Auer S, Frenkel D, 2001, Suppression of Crystal Nucleation in Polydisperse Colloids due to Increase of the Surface Free Energy. Nature, 413:711–3.
96. Wei K, Gao M, Zemin W, et al., 2014, Effect of Energy Input on Formability, Microstructure and Mechanical Properties of Selective Laser Melted AZ91D Magnesium Alloy. Mater Sci Eng A Struct Mater Properties Misrostruct Process, 611:212–22.
97. Azizand MJ, 1982, Model for Solute Redistribution during Rapid Solidification. J Appl Phys, 53:1158–68.
98. Xu C, Liu Y, Liu Y, et al., 2020, New Inorganic Coating- Based Triboelectric Nanogenerators with Anti-Wear and Self-Healing Properties for Efficient Wave Energy Harvesting. Appl Mater Today, 20:100645.
99. Chen Y, Zhang K, Huang J, et al., 2016, Characterization of Heat Affected Zone Liquation Cracking in Laser Additive Manufacturing of Inconel 718. Mater Des, 90:586–94.
100. Ding WW, Zhao XY, Chen TL, et al., 2020, Effect of Rare Earth Y and Al-Ti-B Master Alloy on the Microstructure and Mechanical Properties of 6063 Aluminum Alloy. J Alloys Compd, 830:154685. https://doi.org/10.1016/j.jallcom.2020.154685
101. Wei K, Wang Z, Zeng X, 2015, Influence of Element Vaporization on Formability, Composition, Microstructure, and Mechanical Performance of the Selective Laser Melted Mg-Zn-Zr Components. Mater Lett, 156:187–90.
102. Li J, Qin L, Yang K, et al., 2020, Materials Evolution of Bone Plates for Internal Fixation of Bone Fractures: A Review. J Mater Sci Technol, 36:190–208.
103. Tong X, Zhang D, Zhang X, et al., 2018, Microstructure, Mechanical Properties, Biocompatibility, and In Vitro Corrosion and Degradation Behavior of a New Zn-5Ge Alloy for Biodegradable Implant Materials. Acta Biomater, 82:197–204. https://doi.org/10.1016/j.actbio.2018.10.015
104. Wang P, Goh MH, Li Q, et al., 2020, Effect of Defects and Specimen Size with Rectangular Cross-Section on the Tensile Properties of Additively Manufactured Components. Virtual Phys Prototyp, 15:251–64.
105. Pougis A, Toth LS, Fundenberger JJ, et al., 2014, Extension of the Derby Relation to Metals Severely Deformed to Their Steady-State Ultrafine-Grain Size. Scr Mater, 72–73:59–62. https://doi.org/10.1016/j.scriptamat.2013.10.020
106. Qin Y, Wen P, Voshage M, et al., 2019, Additive Manufacturing of Biodegradable Zn-xWE43 porous Scaffolds: Formation Quality, Microstructure and Mechanical Properties. Mater Des, 181:107937. https://doi.org/10.1016/j.matdes.2019.107937
107. Yang YW, Cheng Y, Peng SP, et al., 2021, Microstructure Evolution and Texture Tailoring of Reduced Graphene Oxide Reinforced Zn Scaffold. Bioact Mater, 6:1230–41. https://doi.org/10.1016/j.bioactmat.2020.10.017
108. Fu Q, Saiz E, Tomsia AP, 2011, Direct Ink Writing of Highly Porous and Strong Glass Scaffolds for Load-Bearing Bone Defects Repair and Regeneration. Acta Biomater, 7:3547–54.
109. Wu S, Liu X, Yeung KW, et al., 2014, Biomimetic Porous Scaffolds for Bone Tissue Engineering. Mater Sci Eng R Rep, 80:1–36.
110. Carluccio D, Xu C, Venezuela J, et al., 2020, Additively Manufactured Iron-Manganese for Biodegradable Porous Load-Bearing Bone Scaffold Applications. Acta Biomater, 103:346–60.
111. Zhu S, Wu C, Li G, et al., 2020, Microstructure, Mechanical Properties and Creep Behaviour of Extruded Zn-xLi (x=0.1, 0.3 and 0.4) Alloys for Biodegradable Vascular stent Applications. Mater Sci Eng A, 777:139082.
112. Liu S, Kent D, Doan N, et al., 2019, Effects of Deformation Twinning on the Mechanical Properties of Biodegradable Zn-Mg Alloys. Bioact Mater, 4:8–16.
113. Shi ZZ, Gao XX, Zhang HJ, et al., 2020, Design Biodegradable Zn Alloys: Second Phases and their Significant Influences on Alloy Properties. Bioact Mater, 5:210–8. https://doi.org/10.1016/j.bioactmat.2020.02.010
114. Odusote JK, Ajayi PA, 2016, Mechanical Properties and Microstructure of Recycled Aluminum Cast with Zinc and Copper Additions. Int J Metalcast, 10:483–90. https://doi.org/10.1007/s40962-016-0060-4
115. Yang HT, Jia B, Zhang ZC, et al., 2020, Alloying design of Biodegradable Zinc as Promising Bone Implants for Load-Bearing Applications. Nat Commun, 11:401. https://doi.org/10.1038/s41467-019-14153-7
116. Shuai C, Xue L, Gao C, et al., 2020, Rod-Like Eutectic Structure in Biodegradable Zn-Al-Sn Alloy Exhibiting Enhanced Mechanical Strength. ACS Biomater Sci Eng, 6:3821–31.
117. Zhao S, McNamara CT, Bowen PK, et al., 2017, Structural Characteristics and In Vitro Biodegradation of a Novel Zn-Li alloy Prepared by Induction Melting and Hot Rolling. Metall Mater Trans A, 48:1204–15.
118. Singh A, Osawa Y, Somekawa H, et al., 2011, Ultra-Fine Grain Size and Isotropic Very High Strength by Direct Extrusion of Chill-Cast Mg-Zn-Y Alloys Containing Quasicrystal Phase. Scr Mater, 64:661–4.
119. Zhang Q, Fan TW, Fu L, et al., 2012, Ab-Initio Study of the Effect of Rare-Earth Elements on the Stacking Faults of Mg Solid Solutions. Intermetallics, 29:21–6. https://doi.org/10.1016/j.intermet.2012.04.015
120. Smola B, StuliKová I, Pelcová J, et al., 2004, Significance of Stable and Metastable Phases in High Temperature Creep Resistant Magnesium-Rare Earth Base Alloys. J Alloys Compd, 378:196–201.
121. Prasad CV, Reddy MS, Reddy VR, et al., 2018, Effect of Annealing on Chemical, Structural and Electrical Properties of Au/Gd2O3/n-GaN Heterostructure with a High-K Rare-Earth Oxide Interlayer. Appl Surf Sci, 427:670–7. https://doi.org/10.1016/j.apsusc.2017.09.016
122. Tehranchi A, Yin B, Curtin WA, 2018, Solute Strengthening of Basal Slip in Mg Alloys. Acta Mater, 151:56–66. https://doi.org/10.1016/j.actamat.2018.02.056
123. Gayathri J, Elansezhian R, 2020, Influence of Dual Reinforcement (Nano CuO Plus Reused Spent Alumina Catalyst) on Microstructure and Mechanical Properties of Aluminium Metal Matrix Composite. J Alloys Compd, 829:154538. https://doi.org/10.1016/j.jallcom.2020.154538
124. Sahu R, Anup S, 2016, Molecular Dynamics Study of Toughening Mechanisms in Nano-Composites as a Function of Structural Arrangement of Reinforcements. Mater Des, 100:132–40. https://doi.org/10.1016/j.matdes.2016.03.076
125. Li YL, Wang SJ, Wang Q, 2017, A molecular Dynamics Simulation Study on Enhancement of Mechanical and Tribological Properties of Polymer Composites by Introduction of Graphene. Carbon, 111:538–45. https://doi.org/10.1016/j.carbon.2016.10.039
126. Yang Y, Cheng Y, Yang M, et al., 2021, Semi-Coherent Interface Strengthens Graphene/Zinc Scaffolds. Mater Today Nano, 17:100163.
127. Chu K, Wang F, Li Y B, et al., 2018, Interface and Mechanical/Thermal Properties of Graphene/Copper Composite with Mo2C Nanoparticles Grown on Graphene. Composites A Appl Sci Manuf, 109:267–79.
128. Zhang X, Li S, Pan B, et al., 2019, Regulation of Interface between Carbon Nanotubes-Aluminum and its Strengthening Effect in CNTs Reinforced Aluminum Matrix Nanocomposites. Carbon, 155:686–96.
129. Yang Y, Cheng Y, Peng S, et al., 2021, Microstructure Evolution and Texture Tailoring of Reduced Graphene Oxide Reinforced Zn Scaffold. Bioact Mater, 6:1230–41.
130. Chengde G, Yao M, Shuai C., et al., 2019, Nano-SiC Reinforced Zn Biocomposites Prepared Via Laser Melting: Microstructure, Mechanical Properties and Biodegradability. J Mater Sci Technol, 35:2608–17.
131. Yang Y, He C, Dianyu E, et al., 2020, Mg Bone Implant: Features, Developments and Perspectives. Mater Des, 185:108259.
132. Sureshbabu AR, Kurapati R, Russier J, et al., 2015, Degradation-by-Design: Surface Modification with Functional Substrates that Enhance the Enzymatic Degradation of Carbon Nanotubes. Biomaterials, 72:20–8.
133. Nasir S, Hussein MZ, Zainal Z, et al., 2018, Carbon-Based Nanomaterials/Allotropes: A Glimpse of Their Synthesis, Properties and Some Applications. Materials, 11:295.
134. Li Y, Li W, Bobbert F, et al., 2020, Corrosion Fatigue Behavior of Additively Manufactured Biodegradable Porous Zinc. Acta Biomater, 106:439–49.
135. Li Y, Jahr H, Zhang X, et al., 2019, Biodegradation-Affected Fatigue Behavior of Additively Manufactured Porous Magnesium. Addit Manuf, 28:299–311.
136. Li HF, Xie XH, Zheng YF, et al., 2015, Development of Biodegradable Zn-1X Binary Alloys with Nutrient Alloying Elements Mg, Ca and Sr. Sci Rep, 5:10719. https://doi.org/10.1038/srep12190
137. Qian G, Zhang L, Wang G, et al., 2021, 3D Printed Zn-Doped Mesoporous Silica-Incorporated Poly-L-Lactic Acid Scaffolds for Bone Repair. Int J Bioprint, 7:346.
138. Qian G, Lu T, Zhang J, et al., 2020, Promoting Bone Regeneration of Calcium Phosphate Cement by Addition of PLGA Microspheres and Zinc Silicate Via Synergistic Effect of In Situ Pore Generation, Bioactive Ion Stimulation and Macrophage Immunomodulation. Appl Mater Today, 19:100615.
139. Li Y, Pavanram P, Zhou J, et al., 2020, Additively Manufactured Biodegradable Porous Zinc. Acta Biomater, 101:609–23.
140. Ralston K, Birbilis N, Davies C, 2010, Revealing the Relationship between Grain Size and Corrosion Rate of Metals. Scr Mater, 63:1201–4.
141. Schultze JW, Davepon B, Karman F, et al., 2013, Corrosion and Passivation in Nanoscopic and Microscopic Dimensions: The Influence of Grains and Grain Boundaries. Br Corros J, 39:45–52.
142. Pu Z., Song GL, Yang S, et al., 2012, Grain Refined and Basal Textured Surface Produced by Burnishing for Improved Corrosion Performance of AZ31B Mg Alloy. Corros Sci, 57:192–201.
143. Jiang B, Xiang Q, Atrens A, et al., 2017, Influence of Crystallographic Texture and Grain Size on the Corrosion Behaviour of As-Extruded Mg Alloy AZ31 Sheets. Corros Sci, 126:374–80.
144. Liu X, Sun J, Qiu K, et al., 2016, Effects of Alloying Elements (Ca and Sr) on Microstructure, Mechanical Property and In Vitro Corrosion Behavior of Biodegradable Zn-1.5 Mg Alloy. J Alloys Compd, 664:444–52.
145. Yue R, Huang H, Ke G, et al., 2017, Microstructure, Mechanical Properties and In Vitro Degradation Behavior of Novel Zn-Cu-Fe Alloys. Mater Charact, 134:114–22.
146. Qin Y, Wen P, Guo H, et al., 2019, Additive Manufacturing of Biodegradable Metals: Current research status and Future Perspectives. Acta Biomater, 98:3–22.
147. Duchoslav J, Arndt M, Steinberger R, et al., 2014, Nanoscopic View on the Initial Stages of Corrosion of Hot Dip Galvanized Zn-Mg-Al Coatings. Corros Sci, 83:327–34. https://doi.org/10.1016/j.corsci.2014.02.027
148. Rosalbino F, Angelini E, Maccio D, et al., 2009, Application of EIS to Assess the Effect of Rare Earths Small Addition on the Corrosion Behaviour of Zn-5% Al (Galfan) Alloy in Neutral Aerated Sodium Chloride Solution. Electrochim Acta, 54:1204–9. https://doi.org/10.1016/j.electacta.2008.08.063
149. Bowen PK, Seitz JM, Guillory RJ 2nd, et al., 2018, Evaluation of Wrought Zn-Al Alloys (1, 3, and 5 wt % Al) through Mechanical and In Vivo Testing for Stent Applications. J Biomed Mater Res B Appl Biomater, 106:245–58. https://doi.org/10.1002/jbm.b.33850
150. Wang Y, Fu P, Wang N, et al., 2020, Challenges and Solutions for the Additive Manufacturing of Biodegradable Magnesium Implants. Engineering, 6:1267–75.
151. Li Y, Zhou J, Pavanram P, et al., 2018, Additively Manufactured Biodegradable Porous Magnesium. Acta Biomater, 67:378–92.
152. Li Y, Jahr H, Lietaert K, et al., 2018, Additively Manufactured Biodegradable Porous iron. Acta Biomater, 77:380–93.
153. Kambe T, Tsuji T, Hashimoto A, et al., 2015, The Physiological, Biochemical, and Molecular Roles of Zinc Transporters in Zinc Homeostasis and Metabolism. Physiol Rev, 95:749.
154. Trumbo P, Schlicker S, Yates AA, et al., 2002, Dietary Reference Intakes for Energy, Carbohydrate, Fiber, Fat, Fatty Acids, Cholesterol, Protein and Amino Acids. J Am Diet Assoc, 102:1621–30.
155. Liu Y, Zheng Y, Chen XH, et al., 2019, Fundamental Theory of Biodegradable Metals-Definition, Criteria, and Design. Adv Funct Mater, 29:1805402.
156. Nie F, Zheng Y, Wei S, et al., 2010, In Vitro Corrosion, Cytotoxicity and Hemocompatibility of Bulk Nanocrystalline Pure Iron. Biomed Mater, 5:065015.
157. Sunil BR, Kumar AA, Kumar TS, et al., 2013, Role of Biomineralization on the Degradation of Fine Grained AZ31 Magnesium Alloy Processed by Groove Pressing. Mater Sci Eng C, 33:1607–15.
158. Wang P, Li X, Luo S, et al., 2021, Additively Manufactured Heterogeneously Porous Metallic Bone with Biostructural Functions and Bone-Like Mechanical Properties. J Mater Sci Technol, 62:173–9.
159. Wang P, Li X, Jiang Y, et al., 2020, Electron beam melted heterogeneously porous microlattices for metallic bone applications: Design and investigations of boundary and edge effects. Addit Manuf, 36:101566.
160. Li Y, Pavanram P, Zhou J, et al., 2020, Additively Manufactured Functionally Graded Biodegradable Porous Zinc. Biomater Sci, 8:2404–19.
161. Zadpoor AA, 2015, Bone Tissue Regeneration: The Role of Scaffold Geometry. Biomater Sci, 3:231–45.
162. Benn F, Kröger N, Zinser M, et al., 2021, Influence of Surface Condition on the Degradation Behaviour and Biocompatibility of Additively Manufactured WE43. Mater Sci Eng C, 124:112016.
163. Walter R, Kannan MB, He Y, et al., 2013, Effect of Surface Roughness on the In Vitro Degradation Behaviour of a Biodegradable Magnesium-Based Alloy. Appl Surf Sci, 279:343–8.
164. Cox SC, Jamshidi P, Eisenstein NM, et al., 2017, Surface Finish has a Critical Influence on Biofilm Formation and Mammalian Cell Attachment to Additively Manufactured Prosthetics. ACS Biomat Sci Eng, 3:1616–26.
165. McMurray RJ, Gadegaard N, Tsimbouri PM, et al., 2011, Nanoscale Surfaces for the Long-Term Maintenance of Mesenchymal Stem Cell Phenotype and Multipotency. Nat Mater, 10:637–44.
166. Li Y, Lietaert K, Li W, et al., 2019, Corrosion Fatigue Behavior of Additively Manufactured Biodegradable Porous Iron. Corros Sci, 156:106–16.
167. Liu L, Huang B, Liu X, et al., 2021, Photo-Controlled Degradation of PLGA/Ti3C2 Hybrid Coating on Mg-Sr Alloy Using Near Infrared Light. Bioact Mater, 6: 568–78.
168. Huang L, Li J, Yuan W, et al., 2020, Near-Infrared Light Controlled Fast Self-Healing Protective Coating on Magnesium Alloy. Corros Sci, 163:108257.
169. Zhuang Y, Liu Q, Jia G, et al., 2020, A Biomimetic Zinc Alloy Scaffold Coated with Brushite for Enhanced Cranial Bone Regeneration. ACS Biomat Sci Eng, 7:893–903.
170. Mao CP, Zhang B, Tang XN, et al., 2014, Optimized Preparation of Zinc-Inorganic Antibacterial Material Containing Samarium using Response Surface Methodology. J Rare Earths, 32:900–6. https://doi.org/10.1016/s1002-0721(14)60161-7
171. Xu Y, Gao H, Shen Y, et al., 2017, Application of Gemini Quaternary Ammonium with Ester Groups in Cationic P(Stco-BA) Nanolatex and Study on its Antibacterial Properties. Mater Sci Eng C Mater Biol Appl, 80:417–24. https://doi.org/10.1016/j.msec.2017.06.010
172. Lakshminarayanan R, Ye E, Young DJ, et al., 2018, Recent Advances in the Development of Antimicrobial Nanoparticles for Combating Resistant Pathogens. Adv Healthc Mater, 7:1701400.
173. Liu R, Memarzadeh K, Chang B, et al., 2016, Antibacterial Effect of Copper-Bearing Titanium Alloy (Ti-Cu) Against Streptococcus mutans and Porphyromonas gingivalis. Sci Rep, 6:1–10.
174. Li P, Schille C, Schweizer E, et al., 2018, Mechanical Characteristics, In Vitro Degradation, Cytotoxicity, and Antibacterial Evaluation of Zn-4.0 Ag Alloy as a Biodegradable Material. Int J Mol Sci, 19:755.