Patient-specific 3D-printed Splint for Mallet Finger Injury
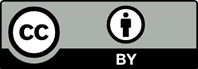
Despite the frequency of mallet finger injuries, treatment options can often be costly, time-consuming, and ill-fitted. Three-dimensional (3D) printing allows for the production of highly customized and inexpensive splints, which suggests potential efficacy in the prescription of casts for musculoskeletal injuries. This study explores how the use of engineering concepts such as 3D printing and topology optimization (TO) can improve outcomes for patients. 3D printing enables the direct fabrication of the patient-specific complex shapes while utilizing finite element analysis and TO in the design of the splint allowed for the most efficient distribution of material to achieve mechanical requirements while reducing the amount of material used. The reduction in used material leads to significant improvements in weight reduction and heat dissipation, which would improve breathability and less sweating for the patient, greatly increasing comfort for the duration of their recovery.
1. Pegoli L, Pivato G, 2019, Mallet finger injuries. In: Sports Injuries of the Hand and Wrist. Springer, Berlin. pp. 1–13. DOI: 10.1007/978-3-030-02134-4_1.
2. Engdahl SM, Christie BP, Kelly B, et al., 2015, Surveying the Interest of Individuals with Upper Limb Loss in Novel Prosthetic Control Techniques. J Neuroeng Rehabil, 12:53. DOI: 10.1186/s12984-015-0044-2.
3. O’Brien L, 2010, Adherence to Therapeutic Splint Wear in Adults with Acute Upper Limb Injuries: A Systematic Review. Hand Ther, 15:3–12. DOI: 10.1258/ht.2009.009025.
4. Young KJ, Pierce JE, Zuniga JM, Assessment of Body-powered 3D Printed Partial Finger Prostheses: A Case Study. 3D Print Med, 5:7. DOI: 10.1186/s41205-019-0044-0.
5. Choi H, Seo A, Lee J, 2019, Mallet Finger Lattice Casts Using 3D Printing. J Healthc Eng, 2019:4765043.
6. Koo DS, Lee JR, 2017, The Development of a Wrist Brace using 3D Scanner and 3D Printer. Fashion Text Res J, 19:312–9. DOI: 10.5805/sfti.2017.19.3.312.
7. Żyluk A, Piotuch B, 2010, Treatment of Mallet Finger a Review. Pol J Surg, 82:243–50.
8. Bazavar M, Rouhani A, Tabrizi A, 2014, Simultaneous Dorsal Base Fracture and FDP Avulsion of Distal Phalanx of the Little Finger. Arch Bone Joint Surg, 2:63.
9. Tuttle HG, Olvey SP, Stern PJ, 2006, Tendon Avulsion Injuries of the Distal Phalanx. Clin Orthop Relat Res, 445:157–68.
10. Robinson LS, Sarkies M, Brown T, et al., 2016, Direct, Indirect and Intangible Costs of Acute Hand and Wrist Injuries: A Systematic Review. Injury, 47:2614–26. DOI: 10.1016/j.injury.2016.09.041
11. Brunet M, Haddad RJ, Sanchez J, et al., 1984, How i Manage Sprained Finger in Athletes. Phys Sportsmed, 12:99–108. DOI: 10.1080/00913847.1984.11701926.
12. Imoto FS, Leão TA, Imoto RS, et al., 2016, Osteosynthesis of Mallet Finger Using Plate and Screws: Evaluation of 25 Patients. Rev Bras Ortop, 51:268–73. DOI: 10.1016/j. rboe.2015.09.013.
13. O’Brien LJ, Bailey MJ, 2011, Single Blind, Prospective, Randomized Controlled Trial Comparing Dorsal Aluminum and Custom Thermoplastic Splints to Stack Splint for Acute Mallet Finger. Arch Phys Med Rehabil, 92:191–8. DOI: 10.1016/j.apmr.2010.10.035.
14. Berman B, 2013, 3D Printing: The New Industrial Revolution. IEEE Eng Manag Rev, 41:72–80. DOI: 10.1109/ emr.2013.6693869.
15. Goh G, Yap YL, Tan HK, et al., 2019, Process-structure properties in Polymer Additive Manufacturing Via Material Extrusion: A Review. Crit Rev Solid State Mater Sci, 45:1–21. DOI: 10.1080/10408436.2018.1549977.
16. Brenken B, Barocio E, Favaloro A, et al., 2018, Fused Filament Fabrication of Fiber-reinforced Polymers: A Review. Addit Manuf, 21:1–16. DOI: 10.1016/j.addma.2018.01.002.
17. Blaya F, Pedro PS, Silva JL, et al., 2018, Design of an Orthopedic Product by Using Additive Manufacturing Technology: The Arm Splint. J Med Syst, 42:54.
18. Yu C, Jiang J, 2020, A Perspective on Using Machine Learning in 3D Bioprinting. Int J Bioprinting, 6:95. DOI: 10.18063/ijb.v6i1.253.
19. Durgun I, Ertan R, 2014, Experimental Investigation of FDM Process for Improvement of Mechanical Properties and Production Cost. Rapid Prototyp J, 20:228–35. DOI: 10.1108/rpj-10-2012-0091.
20. Bodaghi M, Noroozi R, Zolfagharian A, et al., 2019, 4D Printing Self-morphing Structures. Materials, 12:1353. DOI: 10.3390/ma12081353.
21. Rahim TN, Abdullah AM, Akil HM, 2019, Recent Developments in Fused Deposition Modeling-based 3D Printing of Polymers and their Composites. Polym Rev, 59(4):589-624. DOI: 10.1080/15583724.2019.1597883.
22. Jiang J, Xu X, Stringer J, 2019, Optimisation of Multipart Production in Additive Manufacturing for Reducing Support Waste. Virtual Phys Prototyp, 14:219–28. DOI: 10.1080/17452759.2019.1585555.
23. Bodaghi M, Serjouei A, Zolfagharian A, et al., 2020, Reversible Energy Absorbing Meta-Sandwiches by 4D FDM Printing. Int J Mech Sci, 173:105451. DOI: 10.1016/j.ijmecsci.2020.105451.
24. Zolfagharian A, Kouzani A, Khoo SY, et al., 2018, 3D Printed Soft Parallel Actuator. Smart Mater Struct, 27:45019. DOI: 10.1088/1361-665x/aaab29.
25. Zolfagharian A, Kaynak A, Kouzani A, 2019, Closed-loop 4D-printed Soft Robots. Mater Des, 188:108411. DOI: 10.1016/j.matdes.2019.108411.
26. Jiang J, Xu X, Stringer J, 2018, Support Structures for Additive Manufacturing: A Review. J Manuf Mater Process, 2:64.
27. Gordelier TJ, Thies PR, Turner L, et al., 2019, Optimising the FDM Additive Manufacturing Process to Achieve Maximum Tensile Strength: A State-of-the-art Review. Rapid Prototyp J, 25:953-971. DOI: 10.1108/rpj-07-2018-0183.
28. Mohamed OA, Masood SH, Bhowmik JL, 2015, Optimization of Fused Deposition Modeling Process Parameters: A Review of Current Research and Future Prospects. Adv Manuf, 3:42– 53. DOI: 10.1007/s40436-014-0097-7.
29. Wong JY, 2015, On-site 3D Printing of Functional Custom Mallet Splints for Mars Analogue Crewmembers. Aerosp Med Hum Perform, 86:911–4. DOI: 10.3357/amhp.4259.2015.
30. Cazon A, Kelly S, Paterson AM, et al., 2017, Analysis and Comparison of Wrist Splint Designs Using the Finite Element Method: Multi-material Three-dimensional Printing Compared to Typical Existing Practice with Thermoplastics. Proc Inst Mech Eng H, 231:881–97. DOI: 10.1177/0954411917718221.
31. Dhanwal DK, Dennison EM, Harvey NC, et al., 2011, Epidemiology of Hip Fracture: Worldwide Geographic Variation. Indian J Orthop, 45:15–22. DOI: 10.4103/0019- 5413.73656.
32. Lee RJ, Mears SC, 2012, Greening of Orthopedic Surgery. Orthopedics, 35:e940–4. DOI: 10.3928/01477447-20120525-39.
33. Teo AJ, Mishra A, Park I, et al., 2016, Polymeric Biomaterials for Medical Implants and Devices. ACS Biomater Sci Eng,2:454–72.
34. Jiang J, Xu X, Stringer J, 2019, Optimization of Process Planning for Reducing Material Waste in Extrusion Based Additive Manufacturing. Robot Comput Integr Manuf,59:317–25. DOI: 10.1016/j.rcim.2019.05.007.
35. Liu X, Song R, Zhang W, et al., 2017, Development of Ecofriendly Soy Protein Isolate Films with High Mechanical Properties Through HNTs, PVA, and PTGE Synergism Effect. Sci Rep, 7:1–9. DOI: 10.1038/srep44289.
36. Yang R, Chen C, 1996, Stress-based Topology Optimization. Struct Optim, 12:98–105.
37. Zolfagharian, A., Denk, M., Bodaghi, M, et al., 2019, Topology-optimized 4D Printing of a Soft Actuator. Acta Mech Solid Sin, 1:1-13. DOI:10.1007/s10338-019-00137-z.
38. Labanda, S.R, 2015, Mathematical Programming Methods for Large-scale Topology Optimization Problems. PhD Thesis, DTU.
39. Bendsøe MP, 2009, Topology Optimization. Springer, Berlin.
40. Price MJ, Trbovich M, 2018, Thermoregulation following spinal cord injury. In: Handbook of Clinical Neurology. Elsevier, Amsterdam. pp. 799–820. DOI: 10.1016/b978-0-444-64074-1.00050-1.
41. Stevens M, 2016, Human Body Heat as a Source for Thermoelectric Energy Generation, Submitted as Coursework for PH240. Stanford University, United States.