A continuous net-like eutectic structure enhances the corrosion resistance of Mg alloys
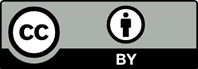
Mg alloys degrade rather rapidly in a physiological environment, although they have good biocompatibility and favorable mechanical properties. In this study, Ti was introduced into AZ61 alloy fabricated by selective laser melting, aiming to improve the corrosion resistance. Results indicated that Ti promoted the formation of Al-enriched eutectic α phase and reduced the formation of β-Mg17Al12 phase. With Ti content reaching to 0.5 wt.%, the Al-enriched eutectic α phase constructed a continuous net-like structure along the grain boundaries, which could act as a barrier to prevent the Mg matrix from corrosion progression. On the other hand, the Al-enriched eutectic α phase was less cathodic than β-Mg17Al12 phase in AZ61, thus alleviating the corrosion progress due to the decreased potential difference. As a consequence, the degradation rate dramatically decreased from 0.74 to 0.24 mg·cm-2·d-1. Meanwhile, the compressive strength and microhardness were increased by 59.4% and 15.6%, respectively. Moreover, the Ti-contained AZ61 alloy exhibited improved cytocompatibility. It was suggested that Ti-contained AZ61 alloy was a promising material for bone implants application.
1. Staiger M, Pietak A, Huadmai J, et al., 2006, Magnesium and its Alloys as Orthopedic Biomaterials: A Review. Biomaterials, 27:1728-34. DOI 10.1016/j.biomaterials.2005.10.003.
2. Zhao D, Witte F, Lu F, et al., 2017, Current Status on Clinical Applications of Magnesium-based Orthopaedic Implants: A Review from Clinical Translational Perspective. Biomaterials, 112:287-302. DOI 10.1016/j. biomaterials.2016.10.017.
3. Gao C, Feng P, Peng S, et al., 2017, Carbon Nanotube, Graphene and Boron Nitride Nanotube Reinforced Bioactive Ceramics for Bone Repair. Acta Biomater, 61:1-20. DOI 10.1016/j.actbio.2017.05.020.
4. Abidin NIZ, Da Forno A, Bestetti M, et al., 2015, Evaluation of Coatings for Mg Alloys for Biomedical Applications. Adv Eng Mater, 17(1):58-67. DOI 10.1002/adem.201300516.
5. Shuai C, Li S, Peng S, et al., 2019, Biodegradable Metallic Bone Implants. Mater Chem Front, 3:544-62.
6. Chai Y, Jiang B, Song J, et al., 2018, Role of Al content on the Microstructure, Texture and Mechanical Properties of Mg-3.5 Ca Based Alloys. Mater Sci Eng A, 730:303-16.
7. Zheng YF, Gu XN, Witte F, 2014, Biodegradable Metals. Mater Sci Eng R, 77:1-34.
8. Cheng W, Bai Y, Wang L, et al., 2018, Strengthening Effect of Extruded Mg-8Sn-2Zn-2Al Alloy: Influence of Micro and Nano-Size Mg-Sn Precipitates. Materials, 10(7):822. DOI 10.3390/ma10070822.
9. Witte F, Kaese V, Haferkamp H, et al., 2005, In vivo Corrosion of Four Magnesium Alloys and the Associated Bone Response. Biomaterials, 26(17):3557-63. DOI 10.1016/j. biomaterials.2004.09.049.
10. Wen Z, Wu C, Dai C, et al., 2009, Corrosion Behaviors of Mg and its Alloys with Different Al contents in a Modified Simulated Body Fluid. J Alloys Compd, 488(1):392-9. DOI 10.1016/j.jallcom.2009.08.147.
11. Baek SM, Kang JS, Shin HJ, et al., 2017, Role of Alloyed Y in Improving the Corrosion Resistance of Extruded Mg– Al–Ca-based Alloy. Corros Sci, 118:227-32. DOI 10.1016/j. corsci.2017.01.022.
12. Liu W, Cao F, Chang L, et al., 2009, Effect of Rare Earth Element Ce and La on Corrosion Behavior of AM60 Magnesium Alloy. Corros Sci, 51:1334-43. DOI 10.1016/j. corsci.2009.03.018.
13. Wu PP, Xu FJ, Deng KK, et al., 2017, Effect of Extrusion on Corrosion Properties of Mg-2Ca-χAl (χ = 0, 2, 3, 5) Alloys. Corros Sci, 127:280-90. DOI 10.1016/j.corsci.2017.08.014.
14. Shuai C, Yang Y, Peng S, et al., 2017, Nd-induced Honeycomb Structure of Intermetallic Phase Enhances the Corrosion Resistance of Mg Alloys for Bone Implants. J Mater Sci Mater Med, 28(9):130. DOI 10.1007/s10856-017-5945-0.
15. Ai X, Quan G, 2012, Effect of Ti on the Mechanical Properties and Corrosion of Cast AZ91 Magnesium Alloy. Open Mater Sci J, 6:6-13.
16. Feng P, Wu P, Gao C, et al., 2018, A Multimaterial Scaffold with Tunable Properties: Toward Bone Tissue Repair. Adv Sci, 5(6):1700817. DOI 10.1002/advs.201700817.
17. Li Z, Gu X, Lou S, et al., 2008, The Development of Binary Mg–Ca Alloys for Use as Biodegradable Materials within Bone. Biomaterials, 29:1329-44. DOI 10.1016/j. biomaterials.2007.12.021.
18. Shuai C, Wang B, Yang Y, et al., 2019, 3D Honeycomb Nanostructure-encapsulated Magnesium Alloys with Superior Corrosion Resistance and Mechanical Properties. Compos B, 162:611-20. DOI 10.1016/j.compositesb.2019.01.031.
19. Lothe J, Pound GM, 1962, Reconsiderations of Nucleation Theory. J Chem Phys, 36:2080-5.
20. Bian D, Deng J, Li N, et al., 2018, In Vitro and In Vivo Studies on Biomedical Magnesium Low-alloying with Elements Gadolinium and Zinc for Orthopedic Implant Applications. ACS Appl Mater Interfaces, 10:4394-408. DOI 10.1021/ acsami.7b15498.
21. Mochizuki A, Yahata C, Takai H, 2016, Cytocompatibility of Magnesium and AZ31 Alloy with Three Types of Cell Lines using a Direct In Vitro Method. J Mater Sci Mater Med, 27:145. DOI 10.1007/s10856-016-5762-x.
22. Shuai C, Guo W, Wu P, et al., 2018, A Graphene Oxide- Ag co-dispersing Nanosystem: Dual Synergistic Effects on Antibacterial Activities and Mechanical Properties of Polymer Scaffolds. Chem Eng J, 347:322-33. DOI 10.1016/j. cej.2018.04.092.
23. International Organization for Standardization, 2009, ISO 10993-5:2009(E). Biological Evaluation of Medical Devices- Part 5: Tests for In Vitro Cytotoxicity. Geneva: International Organization for Standardization.
24. Shuai C, Li Y, Wang G, et al., 2019, Surface Modification of Nanodiamond: Toward the Dispersion of Reinforced Phase in Poly-l-lactic Acid Scaffolds. Int J Biol Macromol, 126:1116- 24. DOI 10.1016/j.ijbiomac.2019.01.004.
25. Shuai C, Xu Y, Feng P, et al., 2019, Antibacterial Polymer Scaffold Based on Mesoporous Bioactive Glass Loaded with In Situ Grown Silver. Chem Eng J, 374:304-15. DOI 10.1016/j.cej.2019.03.273.
26. Shuai C, Cheng Y, Yang Y, et al., 2019, Laser Additive Manufacturing of Zn-2Al Part for Bone Repair: Formability, Microstructure and Properties. J Alloys Compd, 798:606-15. DOI 10.1016/j.jallcom.2019.05.278.
27. Feng P, He J, Peng S, et al., 2019, Characterizations and Interfacial Reinforcement Mechanisms of Multicomponent Biopolymer Based Scaffold. Mater Sci Eng C, 100:809-25.
28. Monas A, Shchyglo O, Kim SJ, et al., 2015, Divorced Eutectic Solidification of Mg-Al Alloys. JOM, 67:1805-11. DOI 10.1007/s11837-015-1418-4.
29. Liang G, Schulz R, 2003, Synthesis of Mg-Ti Alloy by Mechanical Alloying. J Mater Sci, 38:1179-84.
30. Xie D, Zhao J, Qi Y, et al., 2013, Decreasing Pores in a Laser Cladding Layer with Pulsed Current. Chin Opt Lett, 11:111401. DOI 10.3788/col201311.111401.
31. Choi HY, Kim WJ, 2017, The Improvement of Corrosion Resistance of AZ91 Magnesium Alloy through Development of Dense and Tight Network Structure of Al-rich α Phase by Addition of a Trace amount of Ti. J Alloys Compd, 696:736- 45. DOI 10.1016/j.jallcom.2016.11.215.
32. Mathieu S, Rapin C, Steinmetz J, et al., 2003, A Corrosion Study of the Main Constituent Phases of AZ91 Magnesium Alloys. Corros Sci, 45:2741-55. DOI 10.1016/s0010- 938x(03)00109-4.
33. Prabhu DB, Dhamotharan S, Sathishkumar G, et al., 2018, Stress Corrosion Cracking of Biodegradable Mg-4Zn Alloy in Simulated Body Fluid at Different Strain Rates–a Fractographic Investigation. Mater Sci Eng A, 730:223-31. DOI 10.1016/j.msea.2018.06.002.
34. Wang F, Hu T, Zhang Y, et al., 2017, Effects of Al and Zn Contents on the Microstructure and Mechanical Properties of Mg-Al-Zn-Ca Magnesium Alloys. Mater Sci Eng A, 704:57- 65. DOI 10.1016/j.msea.2017.07.060.
35. Fu K, Wang J, Qiu M, et al., 2018, Effects of Cold Rolling on Microstructural Evolution and Mechanical Properties of Mg– 14Li–1Zn Alloy. Adv Eng Mater, 21:1801344. DOI 10.1002/ adem.201801344.
36. Shuai C, Zan J, Qi F, et al., 2019, nMgO-incorporated PLLA Bone Scaffolds: Enhanced Crystallinity and Neutralized Acidic Products. Mater Des, 174:107801. DOI 10.1016/j. matdes.2019.107801.