Roles of support materials in 3D bioprinting – Present and future
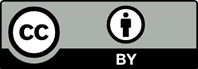
Bioprinting has been introduced as a new technique in tissue engineering for more than a decade. However, characteristics of bioprinted part are still distinct from native human tissue and organ in terms of both shape fidelity and functionality. Recently, the combination of at least two hydrogels or “multi-materials/multi-nozzles” bioprinting enables simultaneous deposition of both model and support materials, thus advancing the complexity of bioprinted shapes from 2.5D lattice into micro-channeled 3D structure. In this article, a perspective on the roles of second bioinks or support materials is presented and future outlook of sacrificial materials is discussed.
1.Murphy S V, Atala A, 2014, 3D bioprinting of tissues and organs. Nature Biotechnology, vol.32: 779–785.
https://dx.doi.org/10.1038/nbt.2958
2. Suntornnond R, An J, Chua C K, 2016, Bioprinting of thermoresponsive hydrogels for next generation tissue engineering: A review. Macromolecular Materials and Engineering. https://doi.org/10.1002/mame.201600266
3. Lee J M and Yeong W Y, 2016, Design and printing strategies in 3D bioprinting of cell-hydrogels: A review. Advanced Healthcare Material.
https://doi.org/10.1002/adhm.201600435
4. Schuurman W, Khristov V, Pot M W, et al., 2011, Bioprinting of h ybrid tissue constructs with tailorable mechanical properties. Biofabrication, vol.3: 021001. https://doi.org/10.1088/1758-5082/3/2/021001
5. Cheah C M, Leong K F, Chua C K, et al., 2002, Characterization of microfeatures in selective laser sintered drug delivery devices. Proceedings of the Institution of Mechanical Engineers, Part H: Journal of Engineering in Medicine, vol.216: 369 –383. https://doi.org/10.1243/095441102321032166
6. Yeong W Y, Chua C K, Leong K F, et al., 2007, Comparison of drying methods in the fabrication of collagen scaffold via indirect rapid prototyping. Journal of Biomedical Materials Research — Part B Applied Biomaterials, vol.82: 260–266. https://doi.org/10.1002/jbm.b.30729
7. Kok Y H, Tan X P, Loh N H, et al., 2016, Geometry dependence of microstructure and microhardness for selective electron beam-melted Ti–6Al–4V parts. Virtual and Physical Prototyping, vol.11: 183–191. https://doi.org/10.1080/17452759.2016.1210483
8. Ozbolat I T and Hospodiuk M, 2016, Current advances and future perspectives in extrusion-based bioprinting. Biomaterials, vol.76: 321–343.
https://dx.doi.org/10.1016/j.biomaterials.2015.10.076
9. Murphy S V, Skardal A and Atala A, 2013, Evaluation of hydrogels for bio-printing applications. Journal of Biomedical Materials Research Part A, vol.101A: 272–284. https://doi.org/10.1002/jbm.a.34326
10. Kucukgul C, Ozler S B, Inci I, et al., 2015, 3D bioprinting of bi omimetic aortic vascular constructs with self‐supporting cells. Biotechnology and Bioengineering,vol.112: 811–821.https://doi.org/10.1002/bit.25493
11. Kolesky D B, Truby R L, Gladman A S, et al., 2014,3D bioprinting of vascularized, heterogeneous cell-laden tissue constructs. Advanced Materials, vol.26: 3124–3130.https://doi.org/10.1002/adma.201305506
12. Hoch E, Tovar G E M and Borchers K, 2014, Bioprinting of a rtificial blood vessels: Current approaches towards a demanding goal. European Journal of Cardio-Thoracic Surgery, vol.46: 767–778.https://doi.org/10.1093/ejcts/ezu242
13. Hinton T J, Jallerat Q, Palchesko R N , et al., 2015,Three-dimensional printing of complex biological structures by freeform reversible embedding of suspended hydrogels. Science Advances, vol.1. https://doi.org/10.1126/sciadv.1500758
14. Bertassoni L E, Cecconi M, Manoharan V, et al., 2014, Hydrogel bioprinted microchannel networks for vascularization of tissue engineering constructs. Lab on a Chip, vol.14: 2202–2211. https://doi.org/10.1039/C4LC00030G
15. Müller M, Becher J, Schnabelrauch M, et al., 2013, Printing thermoresponsive reverse molds for t he creation of patterned two-component hydrogels for 3D cell culture. Journal of Visualized Experiments:H± e50632.
16. Boparai K, Singh R, Singh H, 2015, Comparison of tribological behaviour for Nylon6-Al-Al2O3 and ABS parts fabricated by fused deposition modelling. Virtual and Physical Prototyping, vol.10: 59–66. https://doi.org/10.1080/17452759.2015.1037402