Fabrication of Microstructured Calcium Phosphate Ceramics Scaffolds by Material Extrusion-Based 3D Printing Approach
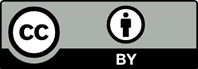
Natural materials such as bone and enamel have intricate microstructures with inorganic minerals oriented to perform multiple mechanical and biological functions. Current additive manufacturing methods for biominerals from the calcium phosphate (CaP) family enable fabrication of custom-shaped bioactive scaffolds with controlled pore structures for patient-specific bone repair. Yet, these scaffolds do not feature intricate microstructures similar to those found in natural materials. In this work, we used direct material extrusion to 3D print water-based inks containing CaP microplatelets, and obtained microstructured scaffolds with various designs. To be shear-thinning and printable, the ink incorporated a concentration of 21 – 24 vol% CaP microplatelets of high aspect ratio. Good shape retention, print fidelity and overhanging layers were achieved by simultaneous printing and drying. Combined with the 3D design, versatile CaP microstructured objects can be built, from porous scaffolds to bulk parts. Extruded filaments featured a core-shell microstructure with graded microplatelet orientations, which was not affected by the printing parameters and the print design. A simple model is proposed to predict the core-shell microstructure according to the ink rheology. Given the remaining open porosity after calcination, microstructured scaffolds could be infiltrated with an organic phase in future to yield CaP biocomposites for hard tissue engineering.
1. Reznikov N, Bilton M, Lari L, et al., 2018, Fractal-like Hierarchical Organization of Bone Begins at the Nanoscale. Science, 360:eaao2189. https://doi.org/10.1126/science.aao2189
2. Beniash E, Stifler CA, Sun CY, et al., 2019, The Hidden Structure of Human Enamel. Nat Commun, 10:1–13. https://doi.org/10.1038/s41467-019-12185-7
3. Gao H, 2006, Application of fracture mechanics concepts to hierarchical biomechanics of bone and bone-like materials. Int J Fract, 138:101–137. https://doi.org/10.1007/s10704-006-7156-4
4. Wegst UG, Bai H, Saiz E, et al., 2015, Bioinspired Structural Materials. Nat Mater, 14:23–36. https://doi.org/10.1038/nmat4089
5. Yousefi AM, 2019, A Review of Calcium Phosphate Cements and Acrylic Bone Cements as Injectable Materials for Bone Repair and Implant Fixation. J Appl Biomater Funct Mater, 17:2280800019872594. https://doi.org/10.1177/2280800019872594
6. Jia W, Lau GY, Huang W, et al., 2015, Bioactive Glass for Large Bone Repair. Adv Healthc Mater, 4:2842–2848. https://doi.org/10.1002/adhm.201500447
7. Marques A, Miranda G, Silva F, et al., 2021, Review on Current Limits and Potentialities of Technologies for Biomedical Ceramic Scaffolds Production. J Biomed Mater Res Part B Appl Biomater, 109B:1–17. https://doi.org/10.1002/jbm.b.34706
8. Li T, Chang J, Zhu Y, et al., 2020, 3D Printing of Bioinspired Biomaterials for Tissue Regeneration. Adv Healthc Mater, 9:1–17. https://doi.org/10.1002/adhm.202000208
9. Wen Y, Xun S, Haoye M, et al., 2017, 3D Printed Porous Ceramic Scaffolds for Bone Tissue Engineering: A Review. Biomater Sci, 5:1690–8. https://doi.org/10.1039/C7BM00315C
10. Lin K, Sheikh R, Romanazzo S, et al., 2019, 3D Printing of Bioceramic Scaffolds Barriers to the Clinical Translation: From Promise to Reality, and Future Perspectives. Materials, 12:2660. https://doi.org/10.3390/ma12172660
11. Le Ferrand H, Athanasiou CE, 2020, A Materials Perspective on the Design of Damage-Resilient Bone Implants Through Additive/Advanced Manufacturing. JOM, 72(3):1195–210. https://doi.org/10.1007/s11837-019-03999-3
12. Rogina A, Antunović M, Milovac D, 2019, Biomimetic Design of Bone Substitutes Based on Cuttlefish Bone-derived Hydroxyapatite and Biodegradable Polymers. J Biomed Mater Res Part B Appl Biomater, 107B:197–204. https://doi.org/10.1002/jbm.b.34111
13. Bigoni D, Cavuoto R, Misseroni D, et al., 2020, Ceramics with the Signature of Wood: A Mechanical Insight. Mater Today Bio, 5:100032. https://doi.org/10.1016/j.mtbio.2019.100032
14. Sprio S, Panseri S, Montesi M, et al., 2020, Hierarchical porosity inherited by natural sources affects the mechanical and biological behaviour of bone scaffolds. Journal of the European Ceramic Society, 40: 1717-1727. https://doi.org/10.1016/j.jeurceramsoc.2019.11.015
15. Tampieri A, Sprio S, Sandri M, et al., 2011, Mimicking Natural Bio-mineralization Processes: A New Tool for Osteochondral Scaffold Development. Trends Biotechnol, 29:526–35. https://doi.org/10.1016/j.tibtech.2011.04.011
16. Ruffini A, Sprio S, Tampieri A, 2013, Study of the Hydrothermal Transformation of Wood-derived Calcium Carbonate into 3D Hierarchically Organized Hydroxyapatite. Chem Eng J, 217:150–8. https://doi.org/10.1016/j.cej.2012.11.107
17. Cheng Q, Huang C, Tomsia AP, 2017, Freeze Casting for Assembling Bioinspired Structural Materials. Adv Mater, 29:1703155. https://doi.org/10.1002/adma.201703155
18. Nelson I, Naleway SE, 2019, Intrinsic and Extrinsic Control of Freeze Casting. J Mater Res Technol, 8:2372–85. https://doi.org/10.1016/j.jmrt.2018.11.011
19. Deville S, Saiz E, Tomsia AP, 2006, Freeze Casting of Hydroxyapatite Scaffolds for Bone Tissue Engineering. Biomaterials, 27:5480–9. https://doi.org/10.1016/j.biomaterials.2006.06.028
20. Bouville F, Portuguez E, Chang Y, et al., 2014, Templated Grain Growth in Macroporous Materials. J Am Ceram Soc, 97:1736–42. https://doi.org/10.1111/jace.12976
21. Bai H, Walsh F, Gludovatz B, et al., 2016, Bioinspired Hydroxyapatite/Poly(methyl methacrylate) Composite with a Nacre-Mimetic Architecture by a Bidirectional Freezing Method. Adv Mater, 28:50–6. https://doi.org/10.1002/adma.201504313
22. Gao HL, Chen SM, Mao LB, et al., 2017, Mass Production of Bulk Artificial Nacre with Excellent Mechanical Properties. Nat Commun, 8:287. https://doi.org/10.1038/s41467-017-00392-z
23. Chen SM, Gao HL, Zhu YB, et al., 2018, Biomimetic Twisted Plywood Structural Materials. Natl Sci Rev, 5:703–14. https://doi.org/10.1093/nsr/nwy080
24. Kumar A, Kargozar S, Baino F, et al., 2019, Additive Manufacturing Methods for Producing Hydroxyapatite and Hydroxyapatite-Based Composite Scaffolds: A Review. Front Mater, 6:1–20. https://doi.org/10.3389/fmats.2019.00313
25. Chen S, Jang TS, Pan HM, et al., 2020, 3D Freeform Printing of Nanocomposite Hydrogels through in situ Precipitation in Reactive Viscous Fluid. Int J Bioprint, 6:29–49. https://doi.org/10.18063/ijb.v6i2.258
26. Martin JJ, Fiore BE, Erb RM, 2015, Designing Bioinspired Composite Reinforcement Architectures via 3D Magnetic Printing. Nat Commun, 6:1–7. https://doi.org/10.1038/ncomms9641
27. Feilden E, Ferraro C, Zhang Q, et al., 2017, 3D Printing Bioinspired Ceramic Composites. Sci Rep, 7:1–9. https://doi.org/10.1038/s41598-017-14236-9
28. Fu Z, Freihart M, Wahl L, et al., 2017, Micro-and Macroscopic Design of Alumina Ceramics by Robocasting. J Eur Ceram Soc, 37:3115–24. https://doi.org/10.1016/j.jeurceramsoc.2017.03.052
29. Le Ferrand H, 2020, Pressure-Less Processing of Ceramics with Deliberate Elongated Grain Orientation and Size. In: Minerals, Metals and Materials Series. Berlin/Heidelberg: Springer. p45–56. https://doi.org/10.1007/978-3-030-36552-3_5
30. Zocca A, Colombo P, Gomes CM, et al., 2015, Additive Manufacturing of Ceramics: Issues, Potentialities, and Opportunities. J Ame Ceram Soc, 98:1983–2001. https://doi.org/10.1111/jace.13700
31. Mandel S, Tas AC, 2010, Brushite (CaHPO4·2H2O) to Octacalcium Phosphate (Ca8(HPO4)2(PO4)4·5H2O) Transformation in DMEM Solutions at 36.5 °C. Mater Sci Eng C, 30:245–54. https://doi.org/10.1016/j.msec.2009.10.009
32. Anastasiou AD, Thomson CL, Hussain SA, et al., 2016, Sintering of calcium phosphates with a femtosecond pulsed laser for hard tissue engineering. Mater Des, 101:346–54. https://doi.org/10.1016/j.matdes.2016.03.159
33. M’Barki A, Bocquet L, Stevenson A, 2017, Linking Rheology and Printability for Dense and Strong Ceramics by Direct Ink Writing. Sci Rep, 7:1–10. https://doi.org/10.1038/s41598-017-06115-0
34. del-Mazo-Barbara L, Ginebra MP, 2021, Rheological Characterisation of Ceramic Inks for 3D Direct Ink Writing: A Review. J Eur Ceram Soc, 41:18–33. https://doi.org/10.1016/j.jeurceramsoc.2021.08.031
35. Adcock D, McDowall I, 1957, The Mechanism of Filter Pressing and Slip Casting. J Am Ceram Soc, 40:355–60. https://doi.org/10.1111/j.1151-2916.1957.tb12552.x
36. Hu F, Mikolajczyk T, Pimenov DY, et al., 2021, Extrusion based 3d Printing of Ceramic Pastes: Mathematical Modeling and In Situ Shaping Retention Approach. Materials, 14:1–22. https://doi.org/10.3390/ma14051137
37. Hausmann MK, Rühs PA, Siqueira G, et al., 2018, Dynamics of Cellulose Nanocrystal Alignment during 3D Printing. ACS Nano, 12:6926–37. https://doi.org/10.1021/acsnano.8b02366
38. Windarti T, Taslimah, Haris A, et al., 2017, Synthesis of β-Calcium Pyrophosphate by sol-gel method. IOP Conf Ser Mater Sci Eng, 172:012058. https://doi.org/10.1088/1757-899X/172/1/012058
39. Pujari-Palmer M, Pujari-Palmer S, Lu X, et al., 2016, Pyrophosphate Stimulates Differentiation, Matrix Gene Expression and Alkaline Phosphatase Activity in Osteoblasts. PLoS One, 11:e0163530. https://doi.org/10.1371/journal.pone.0163530
40. Grover LM, Wright AJ, Gbureck U, et al., 2013, The Effect of Amorphous Pyrophosphate on Calcium Phosphate Cement Resorption and Bone Generation. Biomaterials, 34:6631–7. https://doi.org/10.1016/j.biomaterials.2013.05.001
41. Ribeiro A, Blokzijl MM, Levato R, et al., 2018, Assessing Bioink Shape Fidelity to Aid Material Development in 3D Bioprinting. Biofabrication, 10:14102. https://doi.org/10.1088/1758-5090/aa90e2
42. Schwab A, Levato R, D’Este M, et al., 2020, Printability and Shape Fidelity of Bioinks in 3D Bioprinting. Chem Rev, 120:11028–55. https://doi.org/10.1021/acs.chemrev.0c00084
43. Smay JE, Cesarano J, Lewis JA, 2002, Colloidal Inks for Directed Assembly of 3-D Periodic Structures. Langmuir, 18:5429–37. https://doi.org/10.1021/la0257135
44. Li Z, Hojati M, Wu Z, et al., 2020, Fresh and Hardened Properties of Extrusion-based 3D-printed Cementitious Materials: A Review. Sustainability (Switzerland), 12:1–33. https://doi.org/10.3390/su12145628
45. Liu Q, Lu WF, Zhai W, 2021, Toward Stronger Robocast Calcium Phosphate Scaffolds for Bone Tissue Engineering: A Mini-review and Meta-analysis. Mater Sci Eng C, 107:2411–502. https://doi.org/10.1016/j.msec.2021.112578
46. Behera RP, Le Ferrand H, 2021, Impact-resistant Materials Inspired by the Mantis Shrimp’s Dactyl Club. Matter, 4:2831–49. https://doi.org/10.1016/j.matt.2021.07.012
47. Houmard M, Fu Q, Saiz E, et al., 2012, Sol-gel Method to Fabricate CaP Scaffolds by Robocasting for Tissue Engineering. J Mater Sci Mater Med, 23:921–30. https://doi.org/10.1007/s10856-012-4561-2
48. Huang H, Lu X, 2017, An Ellipsoidal Particle in Tube Poiseuille Flow. J Fluid Mech, 822:664–88. https://doi.org/10.1017/jfm.2017.298