Perspectives on Additive Manufacturing Enabled BetaTitanium Alloys for Biomedical Applications
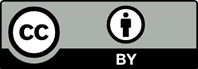
“Stress shielding” caused by the mismatch of modulus between the implant and natural bones, is one of the major problems faced by current commercially used biomedical materials. Beta-titanium (β-Ti) alloys are a class of materials that have received increased interest in the biomedical field due to their relatively low elastic modulus and excellent biocompatibility. Due to their lower modulus, β-Ti alloys have the potential to reduce “stress shielding.” Powder bed fusion (PBF), a category of additive manufacturing, or more commonly known as 3D printing techniques, has been used to process β-Ti alloys. In this perspective article, the emerging research of PBF of β-Ti alloys is covered. The potential and limitations of using PBF for these materials in biomedical applications are also elucidated with focus on the perspectives from processes, materials, and designs. Finally, future trends and potential research topics are highlighted.
1. Liu ZH, Zhang DQ, Chua CK, et al., 2013. Crystal Structure Analysis of M2 High Speed Steel Parts Produced by Selective Laser Melting. Mater Characterization, 84:72–80. https://doi.org/10.1016/j.matchar.2013.07.010
2. Sing SL, Yeong WY, Wiria FE, et al., 2016. Characterization of Titanium Lattice Structures Fabricated by Selective Laser Melting Using an Adapted Compressive Test Method. Exp Mech, 56:735–48. https://doi.org/10.1007/s11340-015-0117-y
3. Herzog D, Seyda V, Wycisk E, et al., 2016. Additive Manufacturing of Metals. Acta Mater, 117:371–92. https://doi.org/10.1016/j.actamat.2016.07.019
4. Sing SL, Yeong WY, Wiria FE, et al., 2017. Direct Selective Laser Sintering and Melting of Ceramics: A Review. Rapid Prototyp J, 23:611–23. https://doi.org/10.1108/rpj-11-2015-0178
5. Yap CY, Chua CK, Dong ZL, et al., 2015. Review of Selective Laser Melting: Materials and Applications. Appl Phys Rev, 2:041101. https://doi.org/10.1063/1.4935926
6. Bogue R, 2011. Nanocomposites: A Review of Technology and Applications. Assembly Autom, 31:106–12.
7. Colombo-Pulgarin JC, Biffi CA, Vedani M, et al., 2021. Beta Titanium Alloys Processed By Laser Powder Bed Fusion: A Review. J Mater Eng Perform, 30:6365–88. https://doi.org/10.1007/s11665-021-05800-6
8. DebRoy T, Wei HL, Zuback JS, et al., 2018. Additive Manufacturing of Metallic Components Process, Structure and Properties. Prog Mater Sci, 92:112–224. https://doi.org/10.1016/j.pmatsci.2017.10.001
9. Gu DD, Meiners W, Wissenbach K, et al., 2013. Laser Additive Manufacturing of Metallic Components: Materials, Processes and Mechanisms. Int Mater Rev, 57:133–64. https://doi.org/10.1179/1743280411y.0000000014
10. Olakanmi EO, Cochrane RF, Dalgarno KW, 2015. A Review on Selective Laser Sintering/Melting (SLS/SLM) of Aluminium Alloy Powders: Processing, Microstructure, and Properties. Prog Mater Sci, 74:401–77. https://doi.org/10.1016/j.pmatsci.2015.03.002
11. Sercombe TB, Li X, 2016. Selective laser melting of aluminium and aluminium metal matrix composites: A review. Mater Technol 2016;31:77-85. https://doi.org/10.1179/1753555715y.0000000078
12. Li Y, Yang C, Zhao H, et al., 2014. New Developments of Ti-based Alloys for Biomedical Applications. Materials, 7:1709–800. https://doi.org/10.3390/ma7031709
13. Niinomi M. Recent Metallic Materials for Biomedical Applications. Metallurgical Mater Trans A, 2002;33:477. https://doi.org/10.1007/s11661-002-0109-2
14. Yang CL, Zhang ZJ, Li SJ, et al., 2018. Simultaneous Improvement in Strength and Plasticity of Ti-24Nb-4Zr-8Sn Manufactured by Selective Laser Melting. Mater Des, 157:52–9. https://doi.org/10.1016/j.matdes.2018.07.036
15. Kuroda D, Niinomi M, Morinaga M, et al., 1998. Design and Mechanical Properties of New β Type Titanium Alloys for Implant Materials. Mater Sci Eng A, 243:244–9. https://doi.org/10.1016/S0921-5093(97)00808-3
16. Ummethala R, Karamched PS, Rathinavelu S, et al., 2020. Selective Laser Melting of High-strength, Low-modulus Ti-35Nb-7Zr-5Ta alloy. Materialia, 14:100941. https://doi.org/10.1016/j.mtla.2020.100941
17. Yadroitsev I, Gusarov AV, Yadroitsava I, et al., 2010. Single Track Formation in Selective Laser Melting of Metal Powders. J Mater Proc Technol, 210:1624–31. https://doi.org/10.1016/j.jmatprotec.2010.05.010
18. Markl M, Körner C, 2016, Multiscale Modeling of Powder Bed-Based Additive Manufacturing. Ann Rev Mater Res, 46:93–123. https://doi.org/10.1146/annurev-matsci-070115-032158
19. Aleixo GT, Afonso C, Coelho A, et al., 2008. Effects of Omega Phase on Elastic Modulus of Ti-Nb Alloys as a Function of Composition and Cooling Rate. Solid State Phenomena, 138:393–8. https://doi.org/10.4028/www.scientific.net/SSP.138.393
20. Mantri SA, Nartu MS, Dasari S, et al., 2021. Suppression and Reactivation of Transformation and Twinning Induced Plasticity in Laser Powder Bed Fusion Additively Manufactured Ti-10V-2Fe-3Al. Addit Manuf, 48:102406.
21. Sing SL, Huang S, Goh GD, et al., 2021. Emerging Metallic Systems for Additive Manufacturing: In-Situ Alloying and Multi-metal Processing in Laser Powder Bed Fusion. Prog Mater Sci, 119:100795. https://doi.org/10.1016/j.pmatsci.2021.100795
22. Yu WH, Sing SL, Chua CK, et al., 2019. Particle-Reinforced Metal Matrix Nanocomposites Fabricated by Selective Laser Melting: A State of the Art Review. Prog Mater Sci, 104:330–79. https://doi.org/10.1016/j.pmatsci.2019.04.006
23. Saedi S, Moghaddam NS, Amerinatanzi A, et al., 2018. On the Effects of Selective Laser Melting Process Parameters on Microstructure and Thermomechanical Response of Ni-rich NiTi. Acta Mater, 144:552–60. https://doi.org/10.1016/j.actamat.2017.10.072
24. Guzmán J, de Moura Nobre R, Nunes ER, et al., 2021. Laser Powder Bed Fusion Parameters to Produce High-density Ti-53%Nb Alloy Using Irregularly Shaped Powder from Hydridedehydride (HDH) Process. J Mater Res Technol, 10:1372–81. https://doi.org/10.1016/j.jmrt.2020.12.084
25. Silvestri AT, Foglia S, Borrelli R, et al., 2020. Electron Beam Melting of Ti6Al4V: Role of the Process Parameters under the Same Energy Density. J Manuf Processes, 60:162–79. https://doi.org/10.1016/j.jmapro.2020.10.065
26. Pobel CR, Osmanlic F, Lodes MA, et al., 2019. Processing Windows for Ti-6Al-4V Fabricated by Selective Electron Beam Melting with Improved Beam Focus and Different Scan Line Spacings. Rapid Prototyp J, 25:665–71. https://doi.org/10.1108/RPJ-04-2018-0084
27. Sabzi HE, 2019. Powder Bed Fusion Additive Layer Manufacturing of Titanium Alloys. Mater Sci Technol, 35:875–90. https://doi.org/10.1080/02670836.2019.1602974
28. Sun SH, Hagihara K, Ishimoto T, et al., 2021. Comparison of Microstructure, Crystallographic Texture, and Mechanical Properties in Ti-15Mo-5Zr-3Al Alloys Fabricated Via Electron and Laser Beam Powder Bed Fusion Technologies. Addit Manuf, 47:102329. https://doi.org/10.1016/j.addma.2021.102329
29. Guzmán J, de Moura Nobre R, Rodrigues Júnior DL, et al., 2021. Comparing Spherical and Irregularly Shaped Powders in Laser Powder Bed Fusion of Nb47Ti Alloy. J Mater Eng Perf, 30:6557–67. https://doi.org/10.1007/s11665-021-05916-9
30. De Moura Nobre R, Ank de Morais W, Vasques MT, et al., 2021. Role of Laser Powder Bed Fusion Process Parameters in Crystallographic Texture of Additive Manufactured Nb-48Ti Alloy. J Mater Res Technol, 14:484–95. https://doi.org/10.1016/j.jmrt.2021.06.054
31. Hafeez N, Wei D, Xie L, et al., 2021. Evolution of Microstructural Complex Transitions in Low-modulus β-type Ti-35Nb-2Ta-3Zr Alloy Manufactured by Laser Powder Bed Fusion. Addit Manuf, 48:102376. https://doi.org/10.1016/j.addma.2021.102376
32. Schwab H, Prashanth K, Löber L, et al., 2015. Selective Laser Melting of Ti-45Nb Alloy. Metals, 5:686–94. https://doi.org/10.3390/met5020686
33. Schulze C, Weinmann M, Schweigel C, et al., 2018. Mechanical Properties of a Newly Additive Manufactured Implant Material Based on Ti-42Nb. Materials, 11:124. https://doi.org/10.3390/ma11010124
34. Macias-Sifuentes MA, Xu C, Sanchez-Mata O, et al., 2021. Microstructure and Mechanical Properties of β-21S Ti Alloy Fabricated through Laser Powder Bed Fusion. Prog Addit Manuf, 6:417–30. https://doi.org/10.1007/s40964-021-00181-7
35. Schwab H, Palm F, Kuhn U, et al., 2016. Microstructure and Mechanical Properties of the Near-beta Titanium Alloy Ti-5553 Processed by Selective Laser Melting. Mater Des, 105:75–80. https://doi.org/10.1016/j.matdes.2016.04.103
36. Liu YJ, Zhang YS, Zhang LC, 2019. Transformation induced Plasticity and High Strength in Beta Titanium Alloy Manufactured by Selective Laser Melting. Materialia, 6:100299. https://doi.org/10.1016/j.mtla.2019.100299
37. Zhang LC, Klemm D, Eckert J, et al., 2011. Manufacture by Selective Laser Melting and Mechanical Behavior of a Biomedical Ti-24Nb-4Zr-8Sn Alloy. Script Mater, 65:21–4. https://doi.org/10.1016/j.scriptamat.2011.03.024
38. Surmeneva M, Grubova I, Glukhova N, et al., 2021. New Ti-35Nb-7Zr-5Ta Alloy Manufacturing by Electron Beam Melting for Medical Application Followed by High Current Pulsed Electron Beam Treatment. Metals, 11:1066. https://doi.org/10.3390/met11071066
39. Wang Q, Zhang W, Li S, et al., 2021. Material Characterisation and Computational Thermal Modelling of Electron Beam Powder Bed Fusion Additive Manufacturing of Ti2448 Titanium Alloy. Materials, 14:7359. https://doi.org/10.3390/ma14237359
40. Poozov I, Sufiiarov V, Popovich A, et al., 2018. Synthesis of Ti-5Al, Ti-6Al-7Nb, and Ti-22Al-25Nb Alloys from Elemental Powders Using Powder-bed Fusion Additive Manufacturing. J Alloys Comp, 763:436–45. https://doi.org/10.1016/j.jallcom.2018.05.325
41. Kang N, Lu Y, Lin X, et al., 2019. Microstructure and Tensile Properties of Ti-Mo Alloys Manufactured via Using Laser Powder Bed Fusion. J Alloys Comp, 771:877–84.
https://doi.org/10.3390/cryst11091064
42. Wang Q, Han C, Choma T, et al., 2017. Effect of Nb Content on Microstructure, Property and In Vitro Apatite-forming Capability of Ti-Nb Alloys Fabricated via Selective Laser Melting. Mater Des, 126:268–77. https://doi.org/10.1016/j.matdes.2017.04.026
43. Zhao D, Han C, Li J, et al., 2020. In Situ Fabrication of a Titanium-niobium Alloy with Tailored Microstructures, Enhanced Mechanical Properties and Biocompatibility by Using Selective Laser Melting. Mater Sci Eng C, 2020:110784. https://doi.org/10.1016/j.msec.2020.110784
44. Surmeneva MA, Koptyug A, Khrapov D, et al., 2020. In Situ Synthesis of a Binary Ti-10at% Nb Alloy by Electron Beam Melting Using a Mixture of Elemental Niobium and Titanium Powders. J Mater Proc Technol, 282:116646. https://doi.org/10.1016/j.jmatprotec.2020.116646
45. Mosallanejad MH, Niroumand B, Aversa A, et al., 2021. In-Situ Alloying in Laser-based Additive Manufacturing Processes: A Critical Review. J Alloys Comp, 872:159567. https://doi.org/10.1016/j.jallcom.2021.159567
46. Sing SL, Wiria FE, Yeong WY, 2018. Selective Laser Melting of Lattice Structures: A Statistical Approach to Manufacturability and Mechanical Behavior. Robot Comput Integr Manuf, 49:170–80. https://doi.org/10.1016/j.rcim.2017.06.006
47. Sing SL, Wiria FE, Yeong WY, 2018. Selective Laser Melting of Titanium Alloy with 50 wt% Tantalum: Effect of Laser Process Parameters on Part Quality. Int J Refract Metals Hard Mater, 77:120–7. https://doi.org/10.1016/j.ijrmhm.2018.08.006
48. Yang Y, Wang G, Liang H, et al., 2019. Additive Manufacturing of Bone Scaffolds. Int J Bioprint, 5:148. https://doi.org/10.18063/IJB.v5i1.148
49. Hafeez N, Liu J, Wang L, et al., 2020. Superelastic Response of Low-modulus Porous Beta-type Ti-35Nb-2Ta-3Zr Alloy Fabricated by Laser Powder Bed Fusion. Addit Manuf, 34:101264. https://doi.org/10.1016/j.addma.2020.101264
50. Liu YJ, Li SJ, Wang HL, et al., 2016. Microstructure, Defects and Mechanical Behavior of Beta-type Titanium Porous Structures Manufactured by Electron Beam Melting and Selective Laser Melting. Acta Mater, 113:56–67. https://doi.org/10.1016/j.actamat.2016.04.029
51. Liu YJ, Li SJ, Zhang LC, et al., 2018. Early Plastic Deformation Behaviour and Energy Absorption in Porous β-type Biomedical Titanium Produced by Selective Laser Melting. Script Mater, 153:99–103. https://doi.org/10.1016/j.scriptamat.2018.05.010
52. Li Y, Ding Y, Munir K, et al., 2019. Novel β-Ti35Zr28Nb Alloy Scaffolds Manufactured Using Selective Laser Melting for Bone Implant Applications. Acta Biomater, 87:273–84. https://doi.org/10.1016/j.actbio.2019.01.051
53. Liu YJ, Zhang JS, Liu XC, et al., 2021. Non-layer-wise Fracture and Deformation Mechanism in Beta Titanium Cubic Lattice Structure Manufactured by Selective Laser Melting. Mater Sci Eng A, 822:141696. https://doi.org/10.1016/j.msea.2021.141696
54. Qiu C, Liu Q, Ding R, 2021. Significant Enhancement in Yield Strength for a Metastable Beta Titanium Alloy by Selective Laser Melting. Mater Sci Eng A, 816:141291. https://doi.org/10.1016/j.msea.2021.141291
55. Liu YJ, Wang HL, Li SJ, et al., 2017. Compressive and Fatigue Behavior of Beta-type Titanium Porous Structures Fabricated by Electron Beam Melting. Acta Mater, 126:58–66. https://doi.org/10.1016/j.actamat.2016.12.052
56. Goh GD, Sing SL, Yeong WY, 2020. A Review on Machine Learning in 3D Printing: Applications, Potential, and Challenges. Artif Intell Rev, 54:63–94. https://doi.org/10.1007/s10462-020-09876-9
57. Özel T, Altay A, Kaftanoğlu B, et al., 2020. Focus Variation Measurement and Prediction of Surface Texture Parameters Using Machine Learning in Laser Powder Bed Fusion. J Manuf Sci Eng, 12:011008. https://doi.org/10.1115/1.4045415
58. Kwon O, Kim HG, Ham MJ, et al., 2020. A Deep Neural Network for Classification of Melt-pool Images in Metal Additive Manufacturing. J Intell Manuf, 31:375–86. https://doi.org/10.1007/s10845-018-1451-6
59. Kunkel MH, Gebhardt A, Mpofu K, et al., 2019. Quality Assurance in Metal Powder Bed Fusion Via Deep-learning-Based Image Classification. Rapid Prototyp J, 26:259–66. https://doi.org/10.1108/RPJ-03-2019-0066
60. Shin DS, Lee CH, Kuhn U, et al., 2021. Optimizing Laser Powder Bed Fusion of Ti-5Al-5V-5Mo-3Cr by Artificial Intelligence. J Alloys Comp, 862:158018. https://doi.org/10.1016/j.jallcom.2020.158018
61. Meng L, McWilliams B, Jarosinski W, et al., 2020. Machine Learning in Additive Manufacturing: A Review. JOM, 72:2363–77. https://doi.org/10.1007/s11837-020-04155-y
62. Qi X, Chen G, Li Y, et al., 2019. Applying Neural-Network-Based Machine Learning to Additive Manufacturing: Current Applications, Challenges, and Future Perspectives. Engineering. 5:721–9. https://doi.org/10.1016/j.eng.2019.04.012
63. Sing SL, Kuo CN, Shih CT, et al., 2021. Perspectives of Using Machine Learning in Laser Powder Bed Fusion for Metal Additive Manufacturing. Virtual Phys Prototyp, 2021;16:372–86. https://doi.org/10.1080/17452759.2021.1944229
64. Rudolph JP, Emmelmann C, 2018. Self-learning Calculation for Selective Laser Melting. Proc CIRP, 67:185–90. https://doi.org/10.1016/j.procir.2017.12.197
65. Renken V, Albinger S, Goch G, et al., 2017. Development of an Adaptive, Self-learning Control Concept for an Additive Manufacturing Process. CIRP J Manuf Sci Technol, 19:57–61. https://doi.org/10.1016/j.cirpj.2017.05.002
66. Baturynska I, Semeniuta O, Martinsen K, 2018. Optimization of Process Parameters for Powder Bed Fusion Additive Manufacturing by Combination of Machine Learning and Finite Element Method: A Conceptual Framework. Proc CIRP, 67:227–32. https://doi.org/10.1016/j.procir.2017.12.204