Design and fabrication of anisotropic SiO2 gyroid bioscaffolds with tunable properties
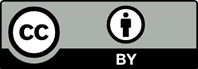
This paper introduces a mathematical approach and additive manufacturing process to customize the mechanical properties of sheet gyroid bioscaffolds and mimicking the intricate architecture of natural bone. By defining the parameters of the level-set equation, scaffolds with spatially controlled porosity and anisotropic properties can be fabricated though digital light processing and microwave heating. A new susceptor-assisted hybrid pyrolysis-sintering process was developed, resulting in a significant enhancement in quality and mechanical properties of the three-dimensional (3D)-printed ceramic compared to conventional methods. The enhancements are originated from the improved densification, accelerated sintering kinetics, promotion of cristobalite phase transformation, and reduced defect volume under microwave heating. Sheet gyroid scaffolds with radially graded porosity and anisotropic properties were fabricated. Despite the porosity distribution, an increase in the unit cell’s aspect ratio amplified the anisotropic mechanical properties. This was also accompanied by a slight decrease in cell proliferation efficiency possibly due to variations in Gaussian curvatures.

- Vijayavenkataraman S, Kuan LY, Lu WF. 3D-printed ceramic triply periodic minimal surface structures for design of functionally graded bone implants. Mater Design. 2020;191:108602. doi: 10.1016/j.matdes.2020.108602
- Yan C, Hao L, Hussein A, Young P. Ti–6Al–4V triply periodic minimal surface structures for bone implants fabricated via selective laser melting. J Mech Behav Biomed Mater. 2015;51:61-73. doi: 10.1016/j.jmbbm.2015.06.024
- Dong Z, Zhao X. Application of TPMS structure in bone regeneration. Eng Regen. 2021;2(8):154-162. doi: 10.1016/j.engreg.2021.09.004
- Shan Y, Bai Y, Yang S, et al. 3D-printed strontium-incorporated β-TCP bioceramic triply periodic minimal surface scaffolds with simultaneous high porosity, enhanced strength, and excellent bioactivity. J Adv Ceram. 2023;12(9):1671-1684. doi: 10.26599/JAC.2023.9220787
- Al‐Ketan O, Abu Al‐Rub RK. MSLattice: a free software for generating uniform and graded lattices based on triply periodic minimal surfaces. Mater Des Process Commun. 2021;3(6):e205. doi: 10.1002/mdp2.205
- Ma S, Song K, Lan J, Ma L. Biological and mechanical property analysis for designed heterogeneous porous scaffolds based on the refined TPMS. J Mech Behav Biomed Mater. 2020;107:103727. doi: 10.1016/j.jmbbm.2020.103727
- Yang Y, Xu T, Bei H-P, et al. Gaussian curvature–driven direction of cell fate toward osteogenesis with triply periodic minimal surface scaffolds. Proc Natl Acad Sci U S A. 2022;119(41):e2206684119. doi: 10.1073/pnas.2206684119
- Deering J, Dowling KI, DiCecco L-A, McLean GD, Yu B, Grandfield K. Selective Voronoi tessellation as a method to design anisotropic and biomimetic implants. J Mech Behav Biomed Mater. 2021;116:104361. doi: 10.1016/j.jmbbm.2021.104361
- Yao Y, Qin W, Xing B, Sha N, Jiao T, Zhao Z. High performance hydroxyapatite ceramics and a triply periodic minimum surface structure fabricated by digital light processing 3D printing. J Adv Ceram. 2021;10(1):39-48. doi: 10.1007/s40145-020-0415-4
- Li G, Li Z, Min Y, Chen S, Han R, Zhao Z. 3D‐printed piezoelectric scaffolds with shape memory polymer for bone regeneration. Small. 2023;19(40):e2302927. doi: 10.1002/smll.202302927
- Chen A, Su J, Li Y, et al. 3D/4D printed bio-piezoelectric smart scaffolds for next-generation bone tissue engineering. Int J Extrem Manuf. 2023;5(3):032007. doi: 10.1088/2631-7990/acd88f
- Zhou Q, Su X, Wu J, et al. Additive manufacturing of bioceramic implants for restoration bone engineering: technologies, advances, and future perspectives. ACS Biomater Sci Eng. 2023;9(3):1164-1189. doi: 10.1021/acsbiomaterials.2c01164
- Ravi M, Paramesh V, Kaviya S, Anuradha E, Solomon FP. 3D cell culture systems: advantages and applications. J Cell Physiol. 2015;230(1):16-26. doi: 10.1002/jcp.24683
- Ma J, Qin C, Wu J, et al. 3D printing of strontium silicate microcylinder‐containing multicellular biomaterial inks for vascularized skin regeneration. Adv Healthc Mater. 2021;10(16):e2100523. doi: 10.1002/adhm.202100523
- Feng C, Zhang K, He R, et al. Additive manufacturing of hydroxyapatite bioceramic scaffolds: dispersion, digital light processing, sintering, mechanical properties, and biocompatibility. J Adv Ceram. 2020;9:360-373. doi: 10.1007/s40145-020-0375-8
- Chen Z, Li Z, Li J, et al. 3D printing of ceramics: a review. J Eur Ceram Soc. 2019;39(4):661-687. doi: 10.1016/j.jeurceramsoc.2018.11.013
- Ren X, Wang J, Wu Y, et al. One-pot synthesis of hydroxyapatite hybrid bioinks for digital light processing 3D printing in bone regeneration. J Mater Sci Technol. 2024;188:84-97. doi: 10.1016/j.jmst.2024.01.001
- Li Y, Su J, Chen A, et al. Strontium-doped calcium silicate scaffolds with enhanced mechanical properties and tunable biodegradability fabricated by vat photopolymerization. Int J Bioprint. 2023;9(6):1233. doi: 10.36922/ijb.1233
- Akinwekomi AD, Yeung K-W, Tang C-Y, Law W-C, Tsui GC-P. Finite element simulation of hybrid microwave sintering based on power approach. Int J Adv Manuf Technol. 2020;110:2503-2515. doi: 10.1007/s00170-020-05952-0
- Zuo F, Badev A, Saunier S, Goeuriot D, Heuguet R, Marinel S. Microwave versus conventional sintering: estimate of the apparent activation energy for densification of α-alumina and zinc oxide. J Eur Ceram Soc. 2014;34(12):3103-3110. doi: 10.1016/j.jeurceramsoc.2014.04.006
- Tang J, Xu J, Ye Z, Li X, Luo J. Microwave sintered porous CoCrFeNiMo high entropy alloy as an efficient electrocatalyst for alkaline oxygen evolution reaction. J Mater Sci Technol. 2021;79:171-177. doi: 10.1016/j.jmst.2020.10.079
- Yeung K-W, Tang C-Y, Hu R, et al. Fabrication of ceramic bioscaffolds from fly ash cenosphere by susceptor-assisted microwave sintering. J Eur Ceram Soc. 2022;42(2): 4410-4419. doi: 10.1016/j.jeurceramsoc.2022.03.046
- Garnault T, Bouvard D, Chaix J-M, Marinel S, Harnois C. Is direct microwave heating well suited for sintering ceramics? Ceram Int. 2021;47(12):16716-16729. doi: 10.1016/j.ceramint.2021.02.242
- Zhou M, Liu W, Wu H, et al. Preparation of a defect-free alumina cutting tool via additive manufacturing based on stereolithography–Optimization of the drying and debinding processes. Ceram Int. 2016;42(10):11598-11602. doi: 10.1016/j.ceramint.2016.04.050
- Cui H, Hensleigh R, Yao D, et al. Three-dimensional printing of piezoelectric materials with designed anisotropy and directional response. Nature Mater. 2019;18(3):234-241. doi: 10.1038/s41563-018-0268-1
- Zhianmanesh M, Varmazyar M, Montazerian H. Fluid permeability of graded porosity scaffolds architectured with minimal surfaces. ACS Biomater Sci Eng. 2019;5(3): 1228-1237. doi: 10.1021/acsbiomaterials.8b01400
- Song K, Wang Z, Lan J, Ma S. Porous structure design and mechanical behavior analysis based on TPMS for customized root analogue implant. J Mech Behav Biomed Mater. 2021;115:104222. doi: 10.1016/j.jmbbm.2020.104222
- Yeung K-W, Huang Z, Mang C-Y, et al. Fabrication of predesigned 3D carbon based microstructures via two-photon vat photopolymerization and susceptor-assisted microwave post-processing. Addit Manuf. 2023;79(16):103934. doi: 10.1016/j.addma.2023.103934
- Arita R, Iijima M, Fujishiro Y, et al. Rapid three-dimensional structuring of transparent SiO2 glass using interparticle photo-cross-linkable suspensions. Commun Mater. 2020;1(1):30. doi: 10.1038/s43246-020-0029-y
- Zhao D, Su H, Hu K, et al. Formation mechanism and controlling strategy of lamellar structure in 3D printed alumina ceramics by digital light processing. Addit Manuf. 2022;52:102650. doi: 10.1016/j.addma.2022.102650
- Wan W, Huang C-e, Yang J, Zeng J, Qiu T. Effect of sintering temperature on the properties of fused silica ceramics prepared by gelcasting. J Electron Mater. 2014;43(7):2566-2572. doi: 10.1007/s11664-014-3112-7
- Yeung K-W, Chen L, Tang C-Y, et al. Rapid hybrid microwave cladding of SiO 2/TiO 2 sol–gel derived composite coatings. J Sol-Gel Sci Technol. 2021;98(1):35-44. doi: 10.1007/s10971-021-05498-x
- Bhattacharya M, Basak T. A review on the susceptor assisted microwave processing of materials. Energy. 2016;97:306-338. doi: 10.1016/j.energy.2015.11.034
- Liu Z, Ma C, Chang Z, Yan P, Li F. Advances in crack formation mechanism and inhibition strategy for ceramic additive manufacturing. J Eur Ceram Soc. 2023;43(12): 5078-5098. doi: 10.1016/j.jeurceramsoc.2023.05.008
- Luongo A, Falster V, Doest MB, et al. Microstructure control in 3D printing with digital light processing. Comp Graph Forum. 2020;39(1):347-359. doi: 10.1111/cgf.13807
- Schamberger B, Ziege R, Anselme K, et al. Curvature in biological systems: its quantification, emergence, and implications across the scales. Adv Mater. 2023;35(13):2206110. doi: 10.1002/adma.202206110
- Karayannis VG. Microwave sintering of ceramic materials. IOP Conf Ser Mater Sci Eng. 2016;161(1):012068. doi: 10.1088/1757-899X/161/1/012068
- Chorsi MT, Curry EJ, Chorsi HT, et al. Piezoelectric biomaterials for sensors and actuators. Adv Mater. 2019;31(1):e1802084. doi: 10.1002/adma.201802084